1. 引言
本文研究的复合腔体材料是一种用于地铁隧道结构加固使用的矩形截面新型加固材料,其由空心钢管构成基本形状,内部灌注混凝土,钢管外部包裹碳纤维。近些年来纤维增强复合材料作为轻质、高比强度、高比模量材料在军事、航空、工业方面得到了广泛的运用[1] 。关于圆筒形碳纤维增强钢管混凝土的抗压试验以及抗弯等力学性能试验之前已有过一些研究[1] [2] ,目前国内还没有本文矩形试件结构材性的研究。由于近些年地铁隧道的快速发展出现的一些问题,本文对提供的两种不同碳纤维加固工艺和粘结胶水材料的复合腔体试件进行轴向抗压性能试验,比较两种不同加工工艺试件的抗压承载力。A、B两组试件所用的钢材及混凝土相同,所用的粘结胶水和碳纤维加工工艺不同。试验表明,复合腔体的抗压性能比单一种材料的抗压性能提高很多,其外层纤维材料的厚度及加工工艺对复合腔体的整体抗压性能影响较大。相比较而言,B组试件的碳纤维使用方式和粘结胶水比A组试件的轴压强度高。
2. 试验设计
2.1. 试件设计
复合腔体是由混凝土、钢管、碳纤维三种材料复合而成。其截面形式为4个40 mm × 40 mm × 2 mm (截面长 × 宽 × 厚度)的钢管焊接而成,钢管空腔内部灌注混凝土,钢管外部包裹碳纤维,厚度为t,截面尺寸如图1所示。试验采用的复合腔体试件尺寸为160 mm × 40 mm × 100 mm (截面长 × 宽 × 长度)。
2.2. 加载方案
本试验以加载力的大小控制速度,试验机最大试验力2000 kN,测量精度 ≤ ±1%;调试好试验设备后,进入正常加载状态,第一个试件加载时根据初步计算,第二个试件的加载方案根据第一个试件加载
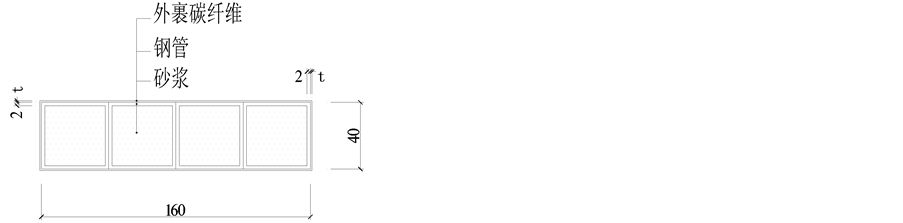
Figure 1. Sectional dimensions of the specimen
图1. 试件截面尺寸
得到的极限值对加载方案做调整,采集加载过程中的荷载、位移、应变。加载临近最终破坏的极限承载力时以位移值控制,当试件轴向压缩位移达到变形率的35%~39%时认为轴压试件达到破坏状态,终止试验。
2.3. 测量内容及测点布置
试验测试内容包括轴向位移和轴向应变。具体的测点布置如图2所示。本试验由200 t万能试验机设备自动采集轴向位移。轴向应变采用应变采集仪采集。本试验共布置了四个应变测点,试件正反面每侧各两个,每侧位置为长度方向中线位置的三等分点。
3. 试验分析
3.1. 材料性能指标、试件数量及编号
本试验所用的三种材料混凝土、钢管、碳纤维的各项材料性能指标如表1所示。本试验分别有A、B两组试件,其中A、B两组试件的碳纤维厚度取值根据实际测量确定。每组试件数量为3个。A、B两组试件的编号以及试验所测值如表2所示。

Figure 2. Diagram: position of the strain gauges
图2. 应变片测点布置图
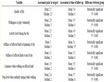
Table 1. Mechanical properties of the specimen
表1. 试件所用材料性能指标
表2. 试件编号及试验结果
3.2. 试验过程及现象
本试验中定义的平均应力
。试件上测点1、2同侧,测点3、4同侧,在
试件轴心受压过程中,当轴力增大到一定值后,混凝土受到钢管及外包碳纤维的约束,钢管混凝土向外鼓出,最终使外裹的碳纤维受拉破坏。
3.2.1. A组试验结果
选取其中一个试件分析,如图3为A组试件c-1的平均应力应变曲线图,由图中可以看出,当平均应力依次达到72 N/mm2、105 N/mm2时,测点3、4处应变先后出现突变,表明该处碳纤维先出现破坏。最后测点1、2处的应变发生突变,表明测点1、2处的碳纤维基本上同时出现受拉破坏,此时对应的应力为110.0 N/mm2左右,对应的外荷载值为704.0 kN。图4、图5分别为另外两个试件加载过程中的试验现象。
由A组复合腔体试件轴心抗压试验结果可以看出,在轴压试验过程中,在荷载值达到700.0 kN左右时,外部碳纤维由于钢管混凝土的压鼓环向受拉逐步破坏。
图6为A组3个试件的轴向荷载位移曲线图,A组复合腔体试件在轴向压力770 kN~830 kN时开始屈服,进入弹塑性阶段,此时位移为5.8 mm左右。由图中可以看出该复合试件本身具有很好的延性。
图7中8张图片分别为A组试件在试验前的构件尺寸及外观,以及试验后试件的破坏形态、截面尺寸,碳纤维的破坏形态以及钢材的破坏形态。
3.2.2. B组试验结果
选取B组其中一个试件分析,图8为B组试件c-11的平均应力应变曲线图,由图中可以看出,当平均应力达到63.0 N/mm2,测点2处应变发生突变,表明该处碳纤维先出现破坏,其后当平均应力达到119.0 N/mm2时,测点3、4处应变发生突变,表明该测点处的碳纤维出现受拉破坏,最后测点1处应变发生突变,表明该处碳纤维受拉破坏,此时的平均应力为130.0 N/mm2左右,对应外荷载值为832.0 kN。由图上可以看出测点1、3、4处碳纤维开始破坏的时间相差不大。图9、图10分别为另外两个试件加载过程中的试验现象。
图11为B组3个试件的轴向荷载位移曲线图,从图中可以看出,B组复合腔体试件在轴向压力达到1000.0 kN~1100.0 kN时开始屈服,进入弹塑性阶段,此时位移为5.81 mm。由图中还可以看出该复合试件具有很好的延性。图12为A、B两组试件的荷载位移曲线关系对比图。
图13中8张图片分别为B组试件试验前的构件尺寸及外观,试验后试件的破坏形态、截面形状,碳纤维的破坏形态以及钢材的破坏形态。
在试验过程中首先出现碳纤维开始拉坏时,同时可听到碳纤维拉坏断裂的声音,此后碳纤维逐渐破坏失去承载力,复合腔体试件的承载力出现短暂的下降趋势,随后荷载基本维持不变,位移不断增加。此阶段为屈服阶段。当位移达到30 mm左右时,复合腔体的承载能力又有所增强。从破坏形态来看,A、B组试件钢板均被压缩,破坏形态基本一致,但是外裹碳纤维的破坏形态是不相同的。A组试件的碳纤维在试验过程中断裂,与钢板表面脱离,而B组试件的碳纤维拉坏,还未与钢板完全脱离。
3.3. 试验结果分析
图14、图15分别为本试验中采用的复合腔体试件钢材和混凝土在轴压试验中采用的截面计算面积示意图。
根据材料性能指标,可计算得到混凝土在轴压力作用下的截面设计承载力[3] [4] :
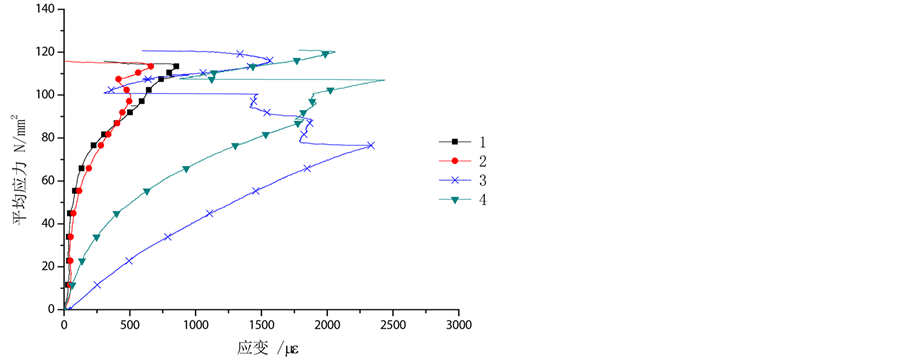
Figure 3. Curve:stress-strain of C-1
图3. C-1应力-应变曲线
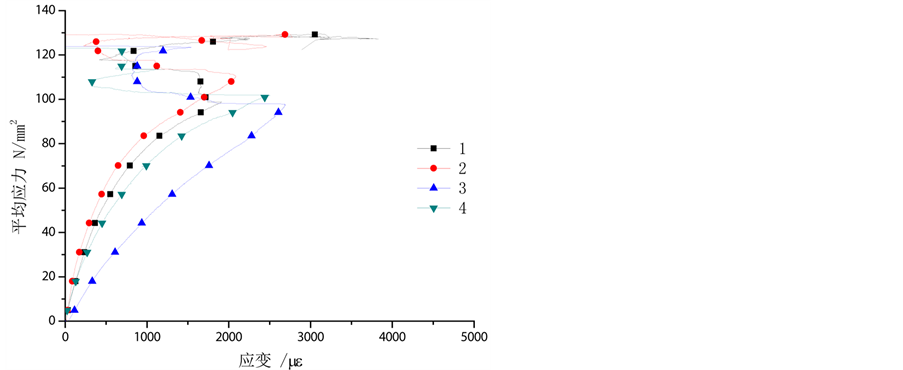
Figure 4. Curve:stress-strain of C-2
图4. C-2应力-应变曲线
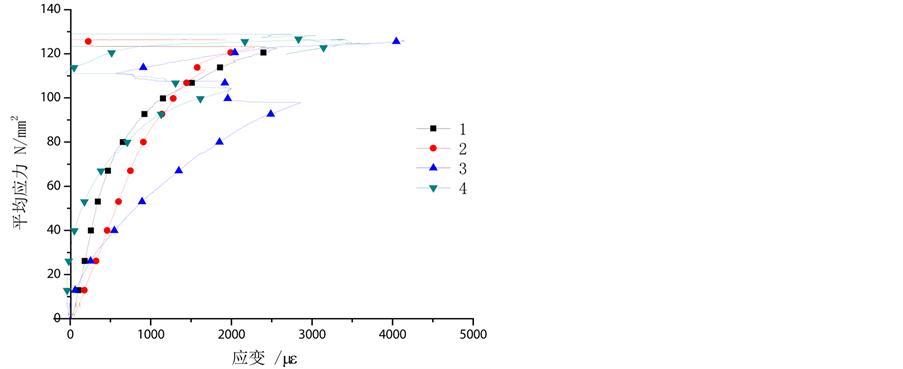
Figure 5. Curve:stress-strain of C-3
图5. C-3应力-应变曲线
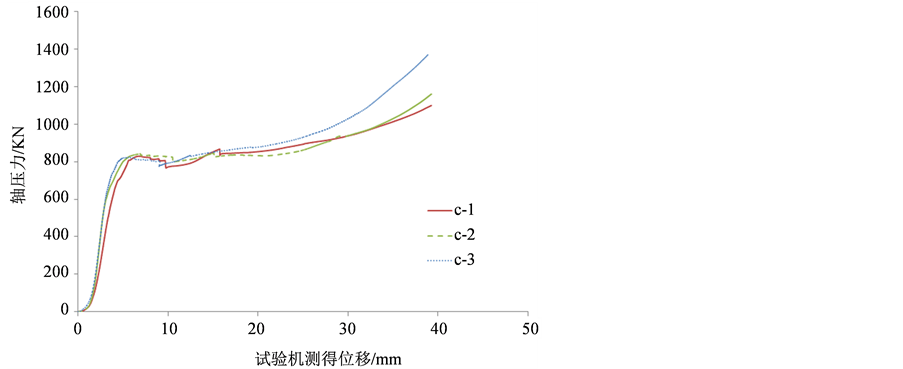
Figure 6. Curve:load-displacement of sets A
图6. A组试件荷载-位移曲线
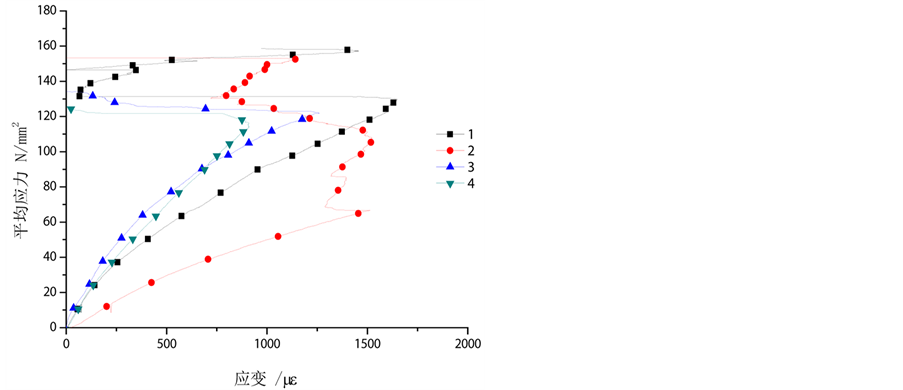
Figure 8. Curve:stress-strain of C-11
图8. C-11应力应变曲线
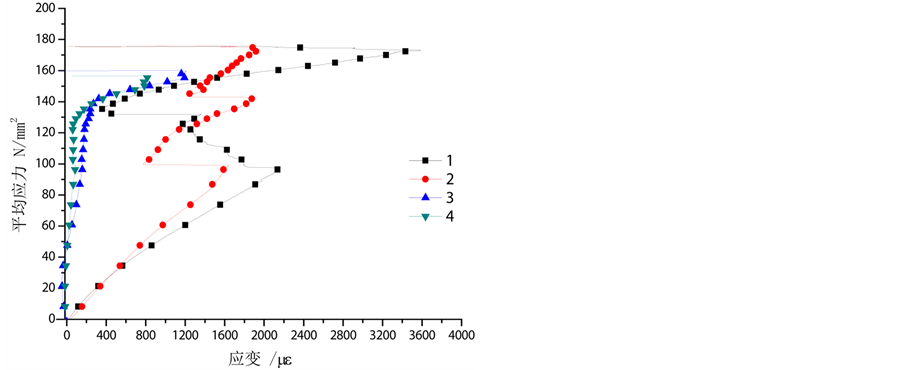
Figure 9. Curve:stress-strain of C-22
图9. C-22应力应变曲线
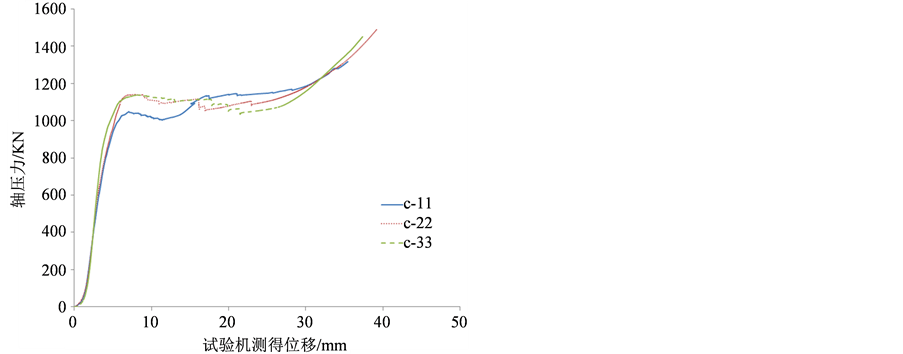
Figure 11. Curve:load-displacement of sets B
图11. B组试件荷载-位移曲线
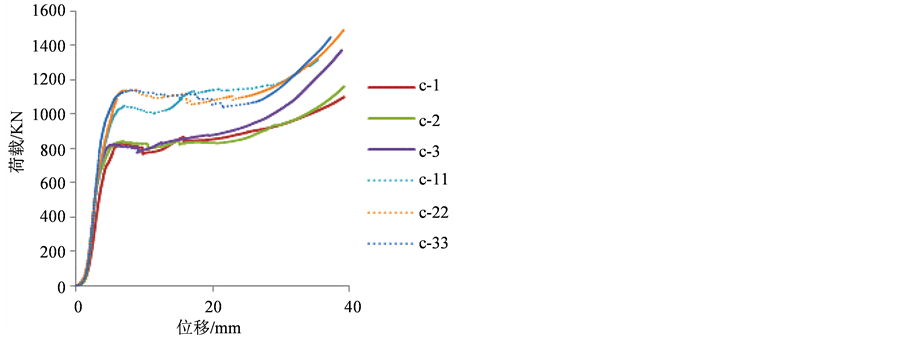
Figure 12. Curve:load-displacement of sets A and B
图12. A、B组试件荷载-位移曲线对比

钢材在轴压力作用下的截面设计承载力:

混凝土和钢材截面承载力之和N为404 kN。
表3所示为试验所得复合腔体试件的屈服荷载、极限荷载以及试验所测值与理论计算值的一些比较。表4为试验过程中,试件表面碳纤维最初开始破坏时的荷载、碳纤维被拉坏逐渐退出工作时荷载、试件开始屈服的荷载、试验所测极限荷载的汇总表。表5中数据为A组、B组试件分别取3个试件各项荷载的平均值。
由表5A、B两组数据处理结果来看,A组和B组试件碳纤维开始出现破坏时的荷载很接近,均为529.0~550.0 kN。但B组试件的其他承载力均比A组试件大。由表中可知,碳纤维开始退出工作时的荷载A组为725.3 kN左右,B组为893.87 kN,B组试件的碳纤维开始退出工作时荷载比A组高23.2%。A组的屈服荷载均值为827.56 kN,B组的屈服荷载均值为1112.43 kN,B组试件的屈服荷载比A组试件高34.4%。试验所得的极限荷载承载力A组均值为1207.57 kN,B组为1420.37 kN,B组试件的极限承载力比A组高17.6%左右。从承载力方面来看B组试件比A组试件的承载力大。表5中还列出A组试件的强屈比均值为1.46,而B组为1.28,均比设计所要求的1.25大,说明二组试件均满足延性要求。但A组试件的延性要比B组试件好,高14%左右。
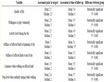
Table 3. Analysis of the experimental results
表3. 试件试验结果分析
表4. 试验结果汇总列表
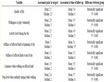
Table 5. Comparision of experimental results between sets A and sets B
表5. A、B组试验结果对比列表
4. 结论
通过对两种不同复合腔体试件的轴心抗压试验可以得到如下结论:
1) 复合腔体试件的这种材料结构相较于三种材料抗压强度直接组合得到的抗压强度提高很多。
2) 复合腔体试件在轴向压力作用下的失效模式主要体现在外层碳纤维剥离钢材表面,碳纤维被拉断,钢管被压鼓屈曲。
3) 通过两组复合腔体试件的轴心受压试验,可知复合腔体的A、B组试件承载力均比单一材料提高很多,而且都具有很好的延性。
4) B组试件的承载性能更好,B组试件的承载力比A组高30%左右。这主要是由于B组试件提供的粘结胶水和外层包裹碳纤维的加工工艺与A组不同。