1. 引言
报废弹药销毁车间在弹丸倾倒、熔融、制片的过程中会产生大量TNT粉尘及热量,即危害工人的身体健康,又影响生产工艺,并且造成很大的安全隐患。此外,报废弹药销毁车间对防火防爆的要求级别较高,需迅速排除弹药销毁过程中产生的大量TNT粉尘和热量,防止事故发生。目前,研究室内气流组织的方法主要有四种[1] :射流理论方法、模型实验方法、区域模型(Zonal Model)方法以及计算流体力学(Computational Fluid Dynamics,简称CFD)方法。其中,后三种方法均属数值计算方法。
室内气流组织模拟方面的研究多针对于采用空调通风系统的典型建筑,如礼堂、剧院、候车厅等。到目前为止,专门针对报废弹药销毁车间的室内流场进行数值模拟和实验研究的文章还鲜有报道。
本文利用FLUENT软件对报废弹药销毁车间车间内的通风流场、颗粒物分布进行了数值模拟,并根据数值模拟结果分析了气流组织存在的问题。模拟结果可为通风系统优化设计提供参考。
2. 工程概况
报废弹药销毁车间分保温车间、制片车间、包装车间等三个车间,弹丸的倾倒、熔融、制片等主要工作都是在制片车间完成,因此,制片车间含有大量TNT粉尘及热量,通风系统设计主要针对制片车间。
制片车间的尺寸为5.5 m (y轴) × 宽3.8 m (x轴) × 高3.9 m (z轴),外窗均为宽2.05 m × 高1.7 m,排气罩水平断面尺寸为制片机的外轮廓尺寸,即长1.0 m × 宽0.9 m,制片机高度为0.84 m。各物体具体放置情况见图1所示。
3. 流速数值模拟求解过程
3.1. 物理模型的简化设定
在对空气流场进行数值模拟之前,对所建模型进行适当合理简化和假设是必要的。并且,经过简化和假设后的计算精度,可以满足实际工程的需要 [1] 。因而,本文对物理模型做如下简化和假设[1] [2] :1) 室内空气是粘性不可压缩的常物性连续介质,且满足斯克涅斯克(Boussinesq)假设;2) 空气在室内的流动状态是稳态湍流流动;3) 不考虑透过玻璃的太阳辐射以及内部各传热表面的辐射影响;4) 不考虑运
动过程中颗粒由于碰撞、凝聚引起的变化,即不存在质量损失;5) 车间内各墙壁均为等温壁面;6) 门窗密闭性很好,不考虑漏风的影响。
3.2. 模型构建及网格划分
运用FLUENT前置模块GAMBIT按制片间实际尺寸建立模型,并进行结构化网格划分,网格划分间距为10 cm,网格形式为正四面体网格,进行了网格无关性检验。总共划分网格数为487,598个。
网格划分完成后,定义边界条件,将送风口定义为速度入口1 (velocity-inlet),将排风罩断面定义为速度入口2 (velocity-inlet) (注:速度设定为负值,即速度方向指向房间外)。
3.3. 求解计算
本文采用标准
两方程湍流模型和SIMPLEC的压力–速度耦合算法,采用有限容积法离散计算区域,分别对0.5 m/s、1 m/s、2 m/s等三种不同送风速度的流场进行了数值模拟,计算过程如下:
1) 运行FLUENT程序,选择3D FLUENT求解器,读入GAMBIT导出的物理模型*.msh文件;
2) 检查网格,设定模型长度单位;
3) 定义隐式(Implicit)非耦合(Segregated)的三维(3D)稳态(Steady)求解器;
4) 选择标准k-e双方程湍流模型,采用标准壁面函数;
5) 设定操作环境及空气物性;
6) 设定边界条件,设定送风口和排风罩回风口的气流速度;
7) 设置求解方法,速度和压力耦合采用SIMPLEC算法;
8) 对计算流场赋初值,初始化计算区域,并进行迭代计算;
9) 对计算结果进行后处理。
3.4. 数值模拟结果及分析
分别对0.5 m/s、1 m/s、2 m/s等三种不同送风速度下的流速场进行了数值模拟。为更好的分析数值模拟结果,本文选取三个典型的断面:距出口300 cm、距右侧墙120 cm、距地面90 cm来对模拟结果进行分析(图2~4)。
(a) 距出口300 cm断面的速度分布 (b) 距右侧墙120 cm断面的速度分布
(c) 距地面90 cm断面的速度分布 (d) 距出口300 cm,距地面150 cm处速度沿程分布
Figure 2. Simulation results: velocity distribution in difference actions when blowing velocity is 0.5 m/s
图2. 送风速度为0.5 m/s的典型断面的模拟结果
(a) 距出口300 cm断面的速度分布 (b) 距右侧墙120 cm断面的速度分布
(c) 距地面90 cm断面的速度分布 (d) 距出口300 cm,距地面150 cm处速度沿程分布
Figure 3. Simulation results: velocity distribution in difference actions when blowing velocity is1.0 m/s
图3. 送风速度为1.0 m/s的典型断面的模拟结果
(a) 距出口300 cm断面的速度分布 (b) 距右侧墙120 cm断面的速度分布
(c) 距地面90 cm断面的速度分布 (d) 距出口300 cm,距地面150 cm处速度沿程分布
Figure 4. Simulation results: velocity distribution in difference actions when blowing velocity is 2.0 m/s
图4. 送风速度为2.0 m/s的典型断面的模拟结果
1) 送风速度为0.5 m/s:
2) 送风速度为1 m/s:
3) 送风速度为2 m/s:
1) 由不同送风速度的数值模拟结果可以看出,当送风速度发生改变时,车间内的气流组织情况并未发生显著变化,即:在现有的送回风形式下,改变送风速度,对车间的气流组织状况影响较小。送回风形式是影响气流组织情况的关键性因素,因此,欲改善车间内的通风状况,须制定和选择正确合理的送回风形式,使车间内的空气品质得到优化改善。
2) 由于送回风口的高度设置较低,并且送风速度及湍流度较小,所以,模拟结果显示,车间顶部的气流运动速度相对较慢,尤其是在车间东南角顶部,由于此角落高度较高,且离送回风口较远,容易形成气流运动的“死区”。
3) 由于送回风口不在同一平面上,在水平面内,气流从送风口以近乎射流的状态送出并到达对面墙面时,开始围绕制片机和排风罩运动并且形成涡流,最终经排风罩排至车间外。由于台阶的阻碍作用,且气流流动速度较小,气流在车间西北角底部形成涡流。
4. 粉尘浓度场数值模拟
在连续相计算收敛前提下[3] ,分别对0.1 μm、1 μm、5 μm、10 μm等四种不同粒径的TNT颗粒的浓度分布进行了数值模拟,计算步骤如下:
1) 待连续相完全收敛后,定义DPM模型 [4] ;
2) 定义离散相射流源:选择面射流源(距地面0.9 m的水平面),颗粒密度r = 1654 kg/m3,颗粒质量流量为0.1 g/s,颗粒垂直向上的初速度为0.1 m/s;
3) 设置随机游走模型 [1] [4] (DRW);
4) 设置颗粒的受力 [4] [5] :重力、萨夫曼(Saffman Lift Force)、热泳力(Thermophoretic Force)、布朗运动(Brownian Motion),流体拽力选择斯托克斯–坎宁安(Stokes-Cunningham)定律;
5) 设定离散相边界条件:送风口和回风口设为逃逸边界(Escape),固壁设为捕集边界(Trap);
6) 对计算流场赋初值,初始化计算区域,并进行计算;
7) 对计算结果进行后处理。
离散相数值模拟结果及分析
分别对0.5 m/s、1 m/s、2 m/s等三种不同送风速度下的流场和0.1 μm、1 μm、5 μm、10 μm等四种不同粒径的颗粒相进行了数值模拟。为节约篇幅,选取三个典型的断面,仅列出0.5 m/s送风速度,不同粒径颗粒物的浓度分布图(图5,图6)。
模拟结果表明:
1) 由于气流组织是影响颗粒物浓度分布的决定性因素,因此,在送回风形式一定的情况下,不同粒径的颗粒物浓度的分布规律具有相似或相同之处,例如,在气流的涡流区或死循环区颗粒物的浓度较高,容易形成积聚等。
2) 对比不同粒径的颗粒物的数值模拟结果可知,在相同条件下,粒径小的颗粒物易扩散到车间顶部或高度较高的水平面,而大粒径的颗粒物则不易向上扩散,进口(距地面90 cm)以下空间的颗粒物浓度明显高于发射面以上的浓度。
(a) 距出口300 cm断面的颗粒物浓度分布 (b) 距右侧墙120 cm断面的颗粒物浓度分布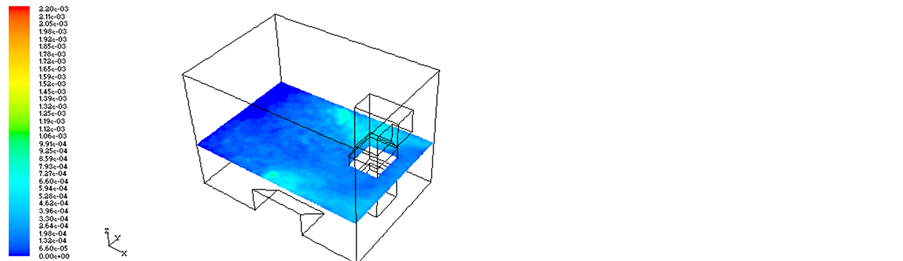
(c) 距地面90 cm断面的颗粒物浓度 (d) 距出口300 cm,地面150 cm处颗粒物浓度沿程分布
Figure 5. Simulation Results: concentration distribution in difference actions when blowing velocity is 0.5 m/s & particle size is 0.1 μm
图5. 0.5 m/s送风速度,粒径为0.1 μm颗粒物浓度分布模拟结果
(a) 颗粒物粒径为1 μm (b) 颗粒物粒径为5 μm
(c) 颗粒物粒径为10 μm
Figure 6. Simulation results: concentration distribution in the position (hight is150 cm, distance is 300 cm) when blowing velocity is 0.5 m/s
图6. 0.5 m/s送风速度,距出口300 cm、离地150 cm处不同粒径颗粒物浓度分布
3) 车间内距右侧墙200 cm的空间下部,易积聚大量颗粒物,尤其是在车间东南角的台阶处,颗粒物积聚情况更为严重。
4) 在人员呼吸区高度范围内(距地面150 cm左右),颗粒物浓度较低,分布较均匀。
5) 颗粒物的浓度曲线图显示,粒径为0.1 μm的颗粒在墙壁处浓度较高,射流状的送风气流使车间中间部位的颗粒物浓度远低于车间两侧的颗粒物浓度;然而大粒径的颗粒物曲线分布图规律不明显,表明颗粒物分布云团不均匀。
通过对报废弹药销毁车间空气流场和颗粒物分布的数值模拟结果可以看出,在现有送回风形式下,车间内某些区域的气流组织和颗粒物分布不理想,通过对数值模拟结果的深入分析,对车间通风系统设计提出以下几点建议:
1) 送风口形式应改为长条形,且在送风侧均匀布置,以消除空气流动的某些死区或死循环区域,使气流组织更加合理;
2) 送风速度不宜过大,以免造成颗粒物向车间顶部扬起或二次扬尘的产生;
3) 建议在弹丸倾倒、熔融、制片等工作区域均加设局部排风系统,使产生的TNT粉尘迅速排除,避免其向其他区域扩散。
5. 结论
1) 相同条件下,粒径小的颗粒物易扩散到车间顶部或高度较高的水平面,而大粒径的颗粒物则不易向上扩散,发射面以下空间的颗粒物浓度明显高于发射面以上的浓度。
2) 车间内距送风口 ≥ 200 cm断面的空间下部,易积聚大量颗粒物,尤其是在车间东南角的台阶处,颗粒物积聚情况更为严重。
3) 在人员呼吸区高度范围内,颗粒物浓度较低,分布较均匀。
4) 在现有的送回风形式下,改变送风速度对车间内气流组织影响较小,而且车间内某些区域的气流流动易形成死区;在相同条件下,粒径小的颗粒物易扩散到车间顶部或高度较高的水平面,而大粒径的颗粒物则不易向上扩散,车间内某些区域颗粒物的浓度较高。