1. 引言
在钻具生产车间,频繁运送钻具,80 dB以上高分贝噪声不绝于耳,工作人员长期置身于此种环境中,极易导致身体健康问题,如肾上腺素分泌增多、心跳加快、血压升高、烦躁易怒、甚至神经衰弱、耳聋、色觉、视野异常等[1] -[7] 。噪音危害已被世界公认为继空气污染之后的人类公共健康的第二个杀手[8] 。然而,在钻具生产车间,噪音随处可闻,尤其钻具间碰撞产生的噪声最为突出,降噪问题亟待解决。目前,国内外还未见专门针对钻具车间噪声问题提出有效解决方案的报道[9] -[11] 。
为此,本文拟查找钻具生产车间噪声主要来源,通过在钻具管排架上设计防碰机构,来降低钻具间接触力,使钻具生产车间主要噪声源的噪音强度降低或消弱,从而减小噪音对工人健康的伤害。
2. 钻具生产车间噪声来源
通过观察和检测整个钻具生产过程,发现钻具车间噪声主要来源有钻具碰撞噪声、修订焊缝残余飞边噪声、气缸排气噪声、摩擦焊机工作噪声及车床噪声等。
2.1. 钻具碰撞噪声
钻具碰撞噪声是钻具车间的主声源,检测数据如表1所示。这种噪音具有突发性和连续性特点,对人体产生很大伤害。
2.2. 修磨噪声
钻具焊接后会在焊缝处留有残余飞边,必须通过修磨清除,在修磨过程中砂轮与管体摩擦会产生巨大的噪声(表2)。此种噪声持续时间长。
2.3. 气缸排气湍流噪声
摩擦焊车间气缸使用多,动作频繁,气缸排气湍流引发强烈啸叫(表3),属气体动力性非稳态噪声。此种噪声属于间息性,但间隔时间较短。
2.4. 摩擦焊机产生的噪声
摩擦焊机工作时管体和接头摩擦焊接时摩擦面产生的摩擦噪声(表4)。此种噪声也属于间息性,噪声值较高。
2.5. 管螺纹车床噪声
管螺纹车床运转时产生的噪声(表5)。此种噪声持续时间长,对人体某些器官伤害较大。
3. 降噪控制措施
3.1. 钻具碰撞缓冲降噪
通过在钻具架上增加缓冲装置,降低钻具滚动过程中的速度,减小冲击力,降低噪声,解决钻具在运送过程中自由滚动相互碰撞而发生的巨大噪声问题。
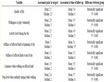
Table 1. Monitoring data of drill impact noise
表1. 钻具碰撞噪声监测数据(单位:dB)
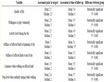
Table 2. Monitoring data of drill grinding noise
表2. 钻具修磨噪声监测数据(单位:dB)
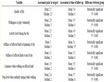
Table 3. Monitoring data of cylinder exhaust turbulence noise
表3. 气缸排气湍流噪声监测数据(单位:dB)
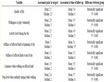
Table 4. Monitoring data of friction welding machine noise
表4. 摩擦焊机噪声监测数据(单位:dB)
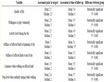
Table 5. Monitoring data of lathe noise
表5. 车床噪声监测数据(单位:dB)
3.2. 空压机隔离降噪
通过建立独立的具有隔音效果的空压机房,减少空压机运转噪声对人体的危害。
3.3. 修磨隔离降噪、工人倒班
通过建立独立的具有隔音效果的修磨工序房,同时为工作人员配备良好的防噪工具,采用轮班制,减少、降低噪声。
4. 无动力降噪防碰钻具输送装置
钻具输送流水线设计原理是利用钻具趋低滚动原理,设计一组倾斜的钻具排放架,当钻具放在管排架的高位时,钻具存有较高重力势能,依靠自身重力沿斜坡向低位端滚动,转化为动能,直到运动到最低位,与已经处于低位的钻具接触碰撞,产生巨大的金属碰撞噪声。为了解决此问题,通过在常规钻具管排架上增设无动力防碰机构来降低噪声分贝值。
4.1. 方案设计
降噪防碰钻具输送装置是由管排架和管排架上添加的一系列无动力防碰机构组成,如图1所示。
无动力防碰机构依靠自身重力实现自动回弹和通过前一根钻具的重力实现无动力防碰机构对后一根钻具的有效阻挡(图2)。无钻具通过时,因无动力防碰机构挡块头部较重,尾部处于翘起状态。当前一根钻具滚过,利用钻具的重力压起无动力防碰机构的尾部使机构前段翘起,在后一根钻具撞向前一根钻具之前,无动力防碰机构型机构翘起的头部阻挡着后一根钻具前进并使之与前一根钻具保持一定距离,等前一根钻具起走以后,后一根钻具将沿着倾斜的管排架继续前进,同时压着前一个无动力防碰机构的尾部,使头部翘起,阻挡相邻后面钻具的继续前进。以此类推,将在管排架上形成一个标准有序的排列,同时阻挡了钻具间的相互碰撞,从而实现降低噪音的目的。
4.2. 无动力防碰机构制备
(1) 结构设计与装配
该机构以销轴为轴心,旋转角度0˚~35˚,要求头部重量要大于尾部重量。设计如图3所示,装配如图4所示。
(2) 材质选择
本体:20号钢;
吸能片:硫化塑料;
销轴:40Cr;
限位柱:45号钢。
(3) 组装(图5)
5. 降噪防碰测试
5.1. 噪音测试
测试对象:中原油田钻井管具工程处钻具生产车间。
车间生产现状:该车间有固定设备40余台套,其中C-125-J型钻具摩擦对焊设备1台套、电动单梁吊3台套、管螺纹车床8台套、热处理设备20台套,主要对钻具进行焊接和热处理,生产钻具能力17,200根/年,平均每天要对150~300根钻具进行流水线处理。
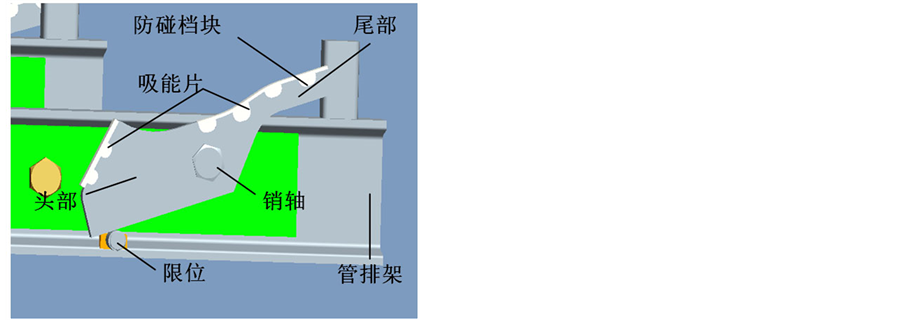
Figure 1. Unpowered anti-collision mechanism
图1. 无动力防碰机构
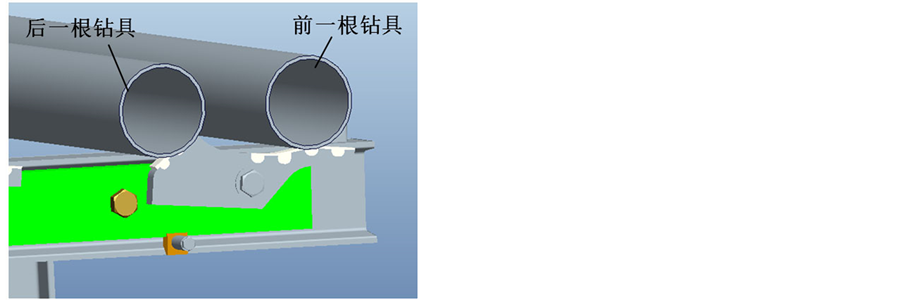
Figure 2. Unpowered anti-collision mechanism
图2. 无动力防碰机构

Figure 3. The design of unpowered anti-collision mechanism
图3. 无动力防碰机构设计图

Figure 4. Assemble of unpowered anti-collision mechanism
图4. 无动力防碰机构装配
噪声测试:在车间内分别对降噪防碰钻具管排装置和常规钻具管排机进行噪音对比测试。生产状态和未生产状态各五组,表6为降噪防碰钻具管排装置噪音监测数据,表7为常规钻具管排机噪音监测数据。图6为降噪防碰钻具管排装置噪声监测过程,图7常规钻具管排机噪声监测过程。
5.2.分析
由表1、表2监测数据可知,降噪防碰钻具管排装置低位端噪音平均值为66.32 dB,峰值为76.04 dB。高位端噪音平均值为51.36 dB,峰值为74.88 dB。监测值均达到工业企业噪音四类标准(55-70 dB),也低于80 dB,故不会对人体造成伤害。而常规钻具管排机低位端噪音平均值为88.06 dB,峰值为109.6 dB。高位端噪音平均值为76.52 dB,峰值为108.74 dB,严重超标,工人工作环境十分恶劣。对比两种管排装
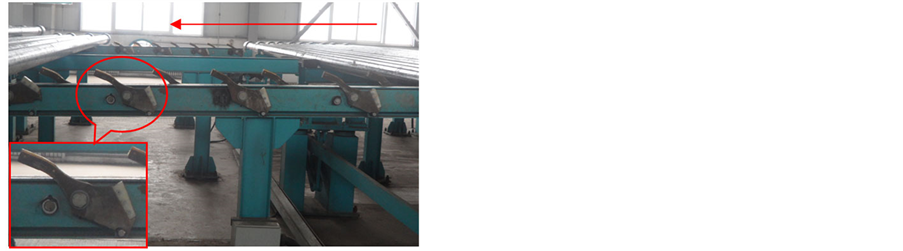
Figure 5. Put together of unpowered anti-collision mechanism
图5. 无动力防碰机构组装
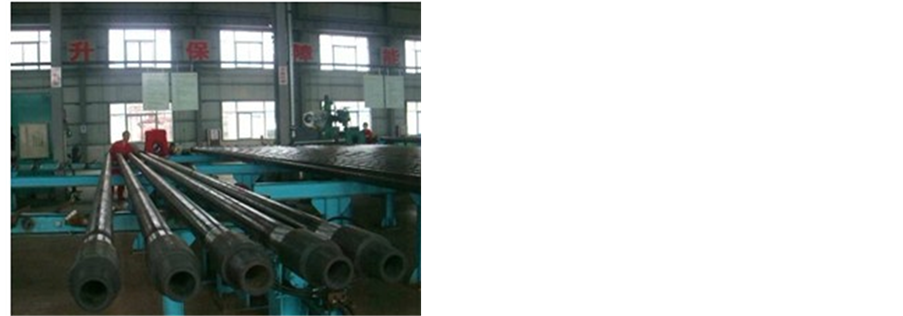
Figure 6. Device of noise reduction drill pipe row
图6. 降噪防碰钻具管排装置
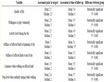
Table 6. Monitoring data of anti collision drill pipe
表6. 降噪防碰钻具管排装置噪音监测数据(单位:dB)
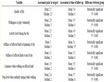
Table 7. Monitoring data of conventional drill pipe
表7. 常规钻具管排机噪音监测数据(单位:dB)
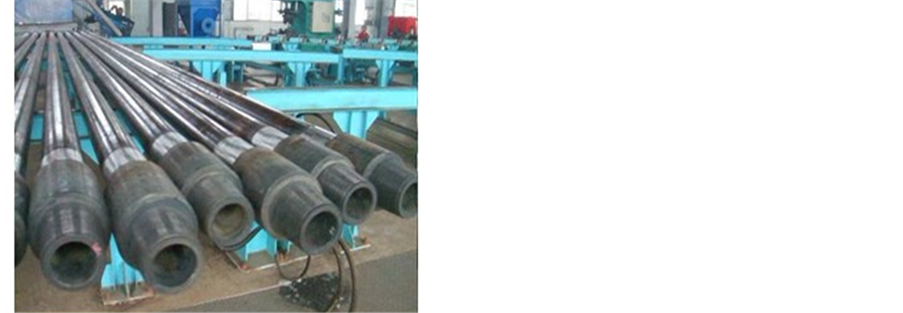
Figure 7. Device of conventional drill pipe
图7. 常规钻具管排机
置的监测数据,降噪防碰钻具管排装置较常规钻具管排机钻具碰撞产生的噪音低位端峰值下降30.6%,噪音平均值下降24.7%,高位端峰值下降31.1%,噪音平均值下降32.9%,机构降噪效果明显。该机构设计巧妙、结构简单、使用方便,具有很高的应用价值。
6. 结论
(1) 通过巧妙设计,无动力防碰机构实现了依靠自身重力自动回弹和通过前一根钻具的重力实现对后一根钻具的阻挡目的,有效降低钻具碰撞产生的巨大噪音,减小对工人身体的直接伤害。
(2) 通过现场监测,降噪防碰钻具管排装置产生的噪音达到工业企业噪音四类标准,有效改善了工人的工作环境。