1. 引言
我国镁电解技术起步较晚,至目前共经历了三个重要历史时期,一是1957~1993年期间,引进并使用的是有隔板镁电解槽技术。二是1993~2010年期间,引进并使用的是大型无隔板镁电解槽技术 [1] 。三是2010年至今,引进并使用的是镁电解多极槽技术。每次技术的引进都使我国镁电解技术实现了跨越式的进步与装备的提升,使得镁电解效率、产品质量以及节能、环保指标得到显著改善。我国海绵钛工业发展起步于上世纪60年代末,至2004年我国仅有2家海绵钛生产企业,即遵义钛厂和抚顺铝厂的钛分厂,年产量总计约2000吨。2004年末国内海绵钛需求逐步增加,2005年价格已从5~6万元/吨,涨到20~30万元/吨,产能翻了60倍以上。2005~2008年,国内由原两家扩张到三四十家,海绵钛企业遍地开花、产能突飞猛进,形成年产15~20万吨规模。在这近10年的期间内,海绵钛行业经历了两次扩张和一次洗牌,至2013年末国内海绵钛企业只剩约20家,均处于产能严重过剩、市场与成本倒挂状态。如何及时、有效、合理地消耗掉海绵钛生产过程中产出的大量副产品氯化镁并降低海绵钛生产成本,已引起了海绵钛生产企业的高度重视,一些企业纷纷寻求引进镁电解技术或盲目的实施镁电解技术。由于很多企业对镁电解工艺技术的缺乏了解,因此,不同的镁电解技术在国内不同企业得到了引进和实施。本文首先论述了镁电解在海绵钛生产工艺中的重要性,进而以国内引进的几种镁电解槽技术在相关企业的实际应用情况为依据,结合每种槽型技术的设计指标进行了详细的对比和分析,着重阐述了多极槽技术原理及其先进性,总结归纳了多极槽取得良好经济技术指标的主要影响因素并对其进行了经济分析,为我国今后镁电解技术的选择明确了方向。
2. 镁电解在海绵钛生产工艺中的重要性
我国镁电解技术的开发与工业应用起步较晚,技术来源和技术依托为前苏联。由前苏联援建中国的156个项目之一的原有隔板镁电解槽技术之后,于80年代末抚顺铝厂花巨资引进了前苏联的105 KA大型无隔板镁电解槽技术并进行了推广,至今国内有的企业仍采用该技术配套海绵钛生产。当前,全球海绵钛生产工艺均采用克劳尔法即镁热还原法(见图1),镁电解工序是实现海绵钛全流程中氯-镁循环的关键(吨海绵钛消耗金属镁1.05~1.15吨、氯气4.6~5.2吨),且电解金属镁经济技术指标与电解氯气浓度对海绵钛生产中的氯化工序及海绵钛的最终成本和环保治理影响极大 [2] 。
3. 我国海绵钛生产工艺中几种镁电解槽技术的对比分析
我国海绵钛生产工艺中的镁电解工序是将还蒸过程产出的MgCl2电解生产金属镁和氯气,实现了海绵钛生产的镁氯循环,降低了海绵钛生产成本。自2007年以来,各种镁电解技术在我国得到了引进和实
施,至目前我国海绵钛生产工艺中配套的镁电解技术基本涵盖了世界各种镁电解槽型技术,有110 KA无隔板电解槽、200 KA流水线电解槽、90~165 KA多极槽。
3.1. 几种镁电解槽型技术设计指标的对比分析
近十年来海绵钛产业在我国得到了迅猛发展,全流程海绵钛生产工艺中必配的镁电解工序也得到了广泛的应用,因此,几种镁电解槽型技术在相关海绵钛企业不同时期进行了引进、推广应用和实施,其设计指标如表1所示。
由表1可以看出,90~165 KA多极槽各项指标最优,具体体现在:
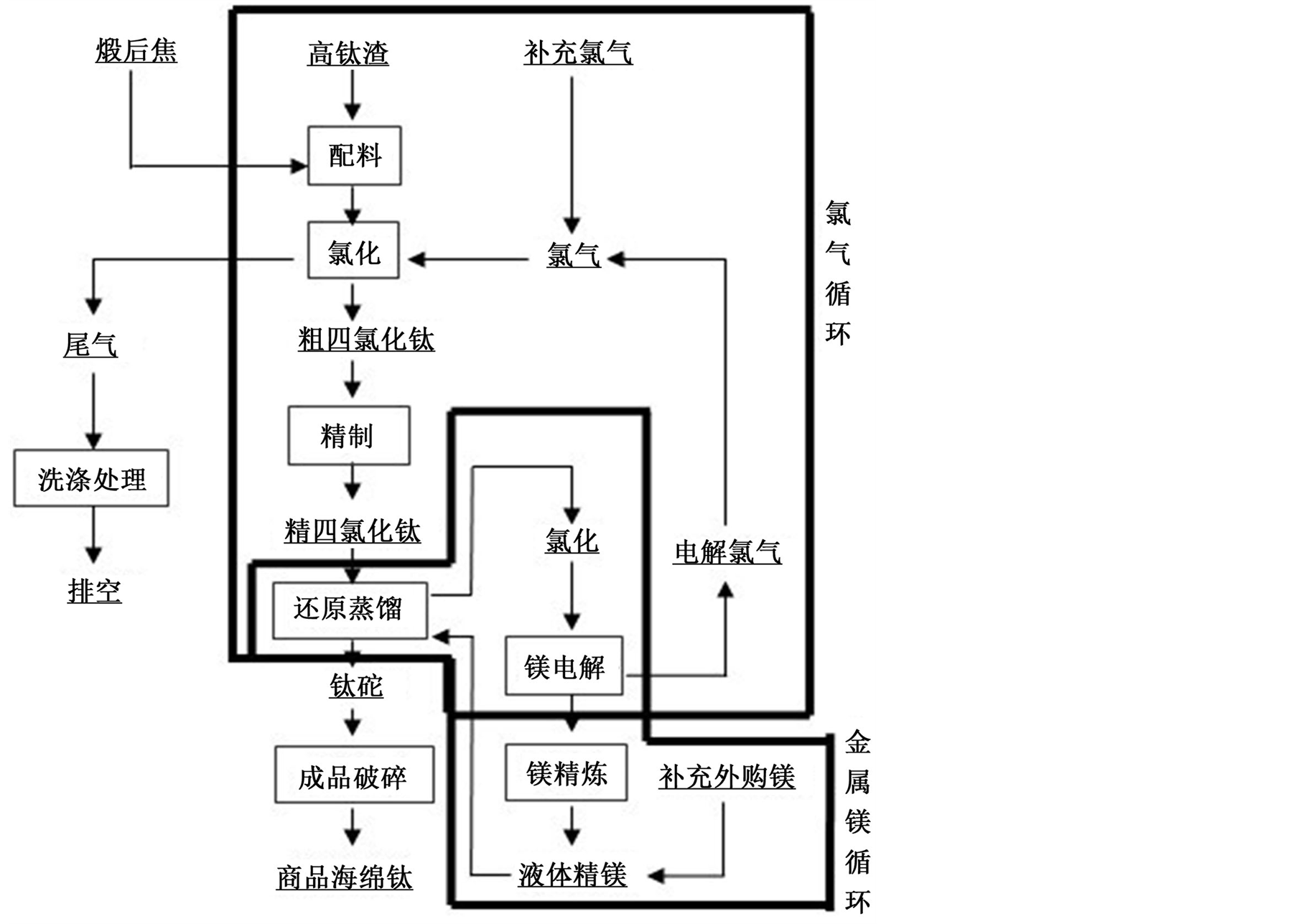
Figure 1. Flow diagram of titanium sponge production process
图1. 海绵钛生产工艺流程图
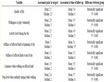
Table 1. Comparison of technical and economic indicators of different magnesium cells
表1. 各种镁电解槽型生产技术经济指标对比[3]
单槽产能大
各槽型的体积基本相似,尺寸范围大约都在(长)5/7 m × (宽)4 m × (高)4 m左右。
电耗低
90~165 KA多极槽不仅直流电耗低,且电解槽产出的镁纯度高,可以直接作为钛还原剂,无需精炼,可节约精炼电耗约1000 kwh/tMg。其他三种槽型电解槽产出的是粗镁,需要进行精炼过程。
氯气回收率高
随着镁电解生产的进行,电解槽中将不断地产出金属镁和氯气。理论上讲,每生产1 t镁,将产出2.958 t的氯气,但实际生产仅能回收2.75~2.9 t,主要的损失途径为被卫生排气带走后被碱液中和或散入空气中这两部分。电解槽中产生的氯气需及时地被氯压机所产生的负压抽走,否则将严重影响环境。
氯气回收浓度高
90~165 KA多极槽在槽盖与槽体、阳极与槽体之间采用了严格的密封技术,以防止液镁氧化和氯气外溢,并由此减除了其它三种槽型必配的卫生排气系统。
电解镁纯度高
90~165 KA多极槽不仅密封性能好,而且电解温度低,因此产出的金属镁杂质含量低。
3.2. 几种镁电解槽型技术在我国海绵钛企业的实际应用情况 [4]
自2007年1月起,遵义钛业万吨海绵钛扩建工程指挥部成立,标志着全流程海绵钛企业对镁电解技术引进的开始。随后河南双瑞万基钛业、攀钢钛业、金川钛业等企业陆续开始引进、实施镁电解技术。下面对各种镁电解槽型技术在我国全流程海绵钛企业的实际应用情况简介如下。
3.2.1. 110 KA无隔板电解槽
该槽型技术来源于原抚顺铝厂引进的前苏联105 KA无隔板电解槽技术,经贵阳铝镁设计院略做改进设计而成。该槽型技术自2001年起应用于遵义钛业配套海绵钛生产至2014年上半年,虽未完全达到设计指标,主要表现在能耗和氯气回收浓度指标上,但该技术仍具有成熟性、完整性、操作粗放、对氯化镁原料质量要求不高、电解槽材料无需进口等优点。
3.2.2. 175 KA无隔板电解槽
遵义钛业万吨海绵钛扩建工程指挥部成立之初,对具有合法引进途径的乌克兰镁电解技术“175 KA无隔板电解槽”和“200 KA流水线电解槽”进行了论证和选择,确定了引进175 KA无隔板镁电解槽技术,并与乌克兰国立钛研究设计院进行了一系列的技术交流,正意欲实施之际,找到了更为先进的多极槽技术引进途径,因此,175 KA无隔板镁电解槽技术在我国没有得到应用。该槽型技术是前苏联上世纪80年代开发应用的电解法制镁技术,目前仍配套应用于乌克兰、独联体海绵钛生产企业。该技术是在原105KA无隔板镁电解槽技术的基础上大型化创新的具体体现,其各项指标略优于原技术以及我国的110 KA无隔板镁电解槽技术。
3.2.3. 200 KA流水线电解槽
攀钢钛业和金川钛业引进的是乌克兰200 KA流水线电解槽技术。该项技术经过两家企业几年的建设与试生产,效果极不理想。金川钛业现已将其改为90~165 KA多极槽,正在实施中。攀钢钛业运行槽台数较少,实际指标与设计指标差距较大,尚在攻关中,未实现成功应用。
3.2.4. 90~165 KA多极槽
在上世纪80年代,90~165 KA多极槽即已广泛应用于美国、日本等海绵钛企业。由于西方发达国家对我国长期的技术封锁,该项技术时至2007年才得以引进。我国全流程海绵钛企业配套该项技术的最多,如:遵宝钛业、双瑞万基钛业、新宇化工、云南新立、唐山天赫、抚顺钛业等。该项技术在我国已经实现了消化、吸收、提高与再创新,目前遵宝钛业、双瑞万基钛业的镁电解仍满负荷配套其海绵钛生产,唐山天赫也在加速启动电解槽台数。在当今激烈的海绵钛市场竞争中,采用该技术配套生产的全流程海绵钛企业是市场竞争的主体,也是今后能否生存与发展的关键,采用该项技术的重要性得以突显。
4. 多极槽技术原理及其先进性
多极槽技术已成为配套海绵钛生产电解金属镁的主流槽型技术,除个别企业采用的是乌克兰的流水线电解槽技术。
4.1. 多极槽技术原理
目前国际上具有代表性的镁电解槽按照阴、阳极的结构分为单极槽与多极槽 [5] 。按照电极的极性分为单极性电解槽和双极性电解槽。我国曾使用过的有隔板槽和无隔板槽均为单极槽(单极性电解槽)。如图2、图3所示。多极槽是指在电解槽每组阳极和阴极之间还设有数个导电极,以增加导电面积,提高电解能力和电能效率。增加的数个导电极曾双极性,即:靠近阳极的一侧呈阴极极性,靠近阴极的一侧呈阳极极性。
4.2. 多极槽技术的先进性
自上世纪90年代中末期以来,具有中国特色的皮江法(热法)炼镁技术在我国得到了迅猛发展,我国一跃成为世界上原生镁锭的生产与出口大国,曾雄踞世界镁电解行业的海德鲁公司、死海镁厂以及国内技术力量雄厚的抚顺铝厂在随后的几年间相继关停其镁电解厂。目前,世界上电解法制镁技术仅应用于海绵钛生产企业,采用的电解槽型有:多极槽、200 KA流水线电解槽、175 KA无隔板电解槽,我国曾使用的110 KA无隔板电解槽已于2014年结束了其历史使命。其中美国、日本均采用的是多极镁电解槽技术。
在镁电解工艺过程中,电解槽是核心设备。镁电解的技术水平主要取决于镁电解槽的技术水平。体现镁电解槽技术水平的主要技术指标是单位产品能耗低、单槽产能大、产品回收率高、产品质量好及环
保指标好。国际上镁电解槽的设计都是朝着电解槽大型化、大电流方向发展,并在结构上不断优化改进。与单极槽相比,多极槽具有更高的电解效率、单槽(同等大小)产出率、设备利用率和产品质量高等优点。我国使用的110 KA无隔板电解槽和200 KA流水线电解槽均属单极槽。
从上述指标对比分析和实际应用情况得到证明,多极槽明显具有单槽产能大、能耗低、镁和氯气纯度高、回收率高、电流强度可调节幅度大等优点,是当今世界上最为先进的镁电解技术。
5. 多极槽取得良好经济技术指标的主要影响因素
多极槽能否取得良好的经济技术指标,取决于以下主要因素的控制。
5.1. 电解槽的烘烤与启动
砌筑、安装完好的电解槽需经过10~15天的烘烤后方可投料启动。
5.1.1. 烤槽
烤槽的目的就是排除电解槽内衬中的水分。在烘烤过程中应严格遵循烤槽升温制度,尽力避免因烤槽加热器、烤槽变压器等出现故障而中途停电问题的发生,从而造成处于高温状态的电解槽再度降温至常温。在对电解槽烘烤过程中,要按期排出烤槽水汽收集器(刺猬包)中的水,烤槽最终温度不应超过空气与石墨阳极发生剧烈氧化反应时的临界温度。
5.1.2. 投料启动
烘烤完成的电解槽应及时投料启动。在投料即向电解槽中加入第一批电解质之前,需断开烤槽加热器电源,快速拆除烤槽变压器、吊出烤槽加热器以及相关连接部件,快速清理干净电解槽内残存杂物后盖好集镁室盖,以使烘烤后的电解槽热损失最小。特别需要强调的是启动电解质要配制合理且不易温度过高,否则将后患无穷,在此不加以详述。启动一台多极槽共需要电解质约65吨,是分批加入电解槽中的。当加入第二批料后,即电解质的加入量至枕砖位置,需对枕砖、阴、阳极和隔墙充分预热数小时后方可加入第三批电解质,否则会对电解槽使用寿命造成严重影响。待电解质加至标准液位后,仍需保持交流加热至700℃恒温2~3天方可接通直流电。
5.2. 电解质的液位
电解质液位的控制是多极槽运行过程中能否取得良好经济技术指标的关键。偏离液位控制区间都会使电解室中的镁导入集镁室困难,增加镁氯二次反应几率,造成镁与氯气的损失以及电流空耗,破坏电解槽的热平衡。液位偏低又会使电解出的金属镁停留在阴阳极、双极之间,引起极间短路,使槽电压降低,同时又将导致阴极暴露在氯气气氛中产生强烈的腐蚀。如短路现象严重,会严重恶化电解质标。
多极槽对电解质液位的控制采用的是DCS智能控制系统,从而实现了对电解质液位的自动控制与调整。其控制原理是依靠惰性气体的压力变化来控制与调整浸没在电解质中液下罐内电解质的量,从而实现对电解质液位升降的控制。
在多极槽的实际生产中应确定科学合理的液位控制参数并定期检测液位测量仪器、仪表的准确度。
5.3. 电解质的温度
电解质温度的控制是多极槽运行过程中能否取得良好经济技术指标的重要影响因素。多年生产实践经验证明,低温高效率是无隔板镁电解槽的特点,同时也适用于多极槽。电解质温度每升高10℃,电流效率降低1.67% [6] 。因此,在较低的电解质温度即略高于金属镁熔点时运行电解槽,可保证其取得良好的经济技术指标。
多极槽配备有智能化的电解质温度控制系统,较无隔板电解槽易于操控。多极槽对电解质温度的控制同电解质液位控制一样,采用的是DCS智能控制系统,从而实现了对电解质温度的自动控制与调整。其控制原理是依靠交流电加热系统来实现对电解质的升温,依靠热交换系统来实现对电解质的降温。
在多极槽的实际生产中通常将电解质温度控制在655℃。虽然这一控制温度通过DCS智能控制系统较易实现,但应尽量避免交流电加热系统和热交换系统的频繁运行,应依靠建立完好的电解槽热平衡来实现,以确保电解槽实现较好的综合交流电耗指标。
5.4. 电解质的成分
为保证多极槽正常稳定的运行,电解质成分必须控制合理,以满足多极槽工艺及其特点要求,这样,多极槽才会取得良好的经济技术指标与质量指标。多极槽采用的电解质成分主要由MgCl2、NaCl、CaCl2和CaF2组成,由于多极槽具有良好的密封性能这一其他槽型技术所不具备的显著特点,加之其采用的物料质量优良,因此,电解槽渣产出率极低,在日常的生产操作过程中基本无需对电解质成分中的NaCl和CaCl2作调整,其损失量甚微,仅需对电解质成分中的MgCl2含量每天每班作调整,对电解质成分中的CaF2含量进行周期性的分析与调整即可。
MgCl2是镁电解的原料,电解槽的加料过程就是调整电解质中MgCl2含量的过程。由于MgCl2在生产过程中不断被消耗,为了保证镁电解的正常生产能够取得良好的经济技术指标,应定期的向电解槽中添加MgCl2,以使电解质中的MgCl2含量保持在规定的范围内,如其含量偏离科学的控制范围,都会对电解过程产生恶劣影响,本文作者曾做过相关论述。
在多极槽的实际生产中只要做好生产的组织与管理,使海绵钛生产的还蒸与电解工序之间建立起“镁钛平衡”,电解质成分的合理控制是很容易实现的。
6. 结语
以上从四个方面对镁电解多极槽技术在海绵钛生产中的应用做了详细的分析,生产实践证明:采用90~165 KA多极槽技术,可以高效、节能、安全、环保地生产优质电解金属镁供还蒸工序使用。该项技术在我国的成功应用,极大地提高了我国海绵钛尤其是镁电解工艺技术及装备水平,同时也为我国海绵钛企业今后选择配套镁电解技术明确了方向。如何实现多极槽技术的进一步提高与再创新,还需要我们每一名镁电解工作者去努力研究和探索,以获得更好的电解指标,实现经济价值和技术进步。
基金项目
科技部国际科技合作项目(2010DFB50290)。