1. 引言
据统计,2014年我国的粗钢总产量达8.2亿多吨,约占全球总产量的50%。钢渣作为钢铁生产过程的副产品,产量约为粗钢的15%~20%,目前累计堆放尚未利用的钢渣达3亿吨以上 [1] [2] ,利用率却不足30% [3] ,大量钢渣的堆积不仅污染环境而且还会造成资源的浪费,因而,应积极开展冶金废渣资源化利用的研究。转炉冶炼结束后,熔融态钢渣温度在1600℃以上,其内蕴含大量的显热 [4] ,是钢铁企业可以回收利用的重要热资源之一。目前国内外钢铁企业大部分先将钢渣冷却处理,之后通过简单的磁选回收金属铁,尾渣堆砌于渣场或用于筑路,但这些处理工艺一方面未对熔融态钢渣的显热加以利用,另一方面未对钢渣中的铁氧化物等进行回收,造成钢渣资源的巨大浪费。因此,积极开展对熔融态钢渣的综合回收利用,实现“渣”的零排放和“热”的高效回收利用具有重要意义。
本文从熔融态钢渣的传统处理工艺、铁磷等有价元素的回收、直接合成有价材料以及显热回收等方面全面综述了熔融态钢渣利用的现状,并对未来的发展方向进行了展望,可为更好地实现钢渣的循环利用提供依据。
2. 熔融钢渣的传统处理工艺
目前,对于钢渣综合利用比较成熟的处理工艺主要是先将钢渣冷却、破碎,然后通过磁选回收钢渣中的铁,之后再将尾渣用于筑路或生产水泥。为了使钢渣在冷却过程中更好的破碎和粒化,需对熔融态的钢渣进行加工预处理。钢铁企业根据实际情况决定钢渣处理的工艺,经查阅相关文献 [5] - [9] ,如表1所示。
钢渣处理工艺为后续的钢渣资源化利用创造条件,目前国内转炉钢渣预处理工艺较多,主要有热焖法、水淬法、风淬法、热泼或浅盘热泼法以及滚筒法,各有其优缺点。风淬法、水淬法和滚筒法处理工艺对钢渣的流动性要求较高,需要配备其它处理工艺,方能100%处理热态钢渣;热泼法、浅盘法处理工艺简单、处理能力大,但是在环保和钢渣处理效果方面还需要改进;热焖法易于机械化,钢渣处理效果好,兼顾了钢渣性能和环保要求,但处理周期较长,在投资和处理能力方面还有待改进。从近年来的生产实际看,以滚筒法工艺为主,配以热泼法或者浅盘法工艺对转炉钢渣进行预处理,在大型炼钢厂的应用越来越普遍,逐渐成为发展趋势之一。
对熔融态钢渣采用冷却处理,再进行磁选回收金属的工业流程,便于机械化、工艺流程简单、成本较低。但易产生废水、粉尘而污染环境,而且也造成钢渣高温资源和铁氧化物等资源的浪费,属于附加值较低的处理工艺。
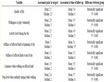
Table 1. Common of slag treatment process, the process flow and representatives of steel plant
表1. 常见的钢渣处理工艺、处理流程及代表钢厂
3. 熔融态钢渣热还原回收有价元素的研究
3.1. 熔融态钢渣热还原单独回收铁的研究
研究表明 [10] ,转炉渣中TFe含量在17%~30%之间,其中金属铁约占7%~10%,表2示出了部分钢铁厂钢渣的成分组成,其中铁氧化物的含量都在20%以上,针对铁氧化物的回收利用,部分学者利用碳硅等还原剂在高温下对钢渣进行了还原提铁的研究。
项长祥 [11] 等人在实验室使用碳管炉,在氩气保护气氛下,进行了还原法处理转炉渣的实验研究,结果如图1所示,在1600℃时,纯Si的还原效果最好,加入硅粉5 min后渣中的铁基本被还原出来,煤粉及煤矸石的还原效果比硅粉差,加入30 min后铁的还原率达到80%以上,而且煤粉密度小、易燃,高温下不易加入。
另外,在提铁实验过程中发现,碱度对铁的还原及回收有着重要的影响,杨志杰 [12] 等人研究了碱度对转炉钢渣熔融还原提铁的影响,实验将破碎过的渣和改质剂SiO2混匀后放入马弗炉内升温,结果表明:在1550℃下,随着SiO2加入量增大,铁的回收率及金属化率呈先升后降的趋势,在碱度1.1时铁的回收率和金属化率达到最大,分别为95.8%和99.2%。但存在渣铁分离困难,大铁块回收量少等问题。
总之,利用还原剂还原处理熔融态钢渣,可以有效的还原回收钢渣中的铁。但若想得到很高的还原回收率,还要考虑还原剂种类、温度条件以及适宜的渣碱度和粘度。
3.2. 熔融态钢渣热还原同时回收铁和磷的研究
目前,人们已开发出了多种钢渣在冶金流程内的循环利用方式,如,用作烧结矿熔剂、炼钢返回料等,这些利用方式在一定程度上减少了钢渣的排放量。但钢渣返回冶金流程继续使用的方式都存在一个关键问题未解决,即有害物质磷的循环累积,这一问题严重制约了钢渣的循环利用量。同时,磷矿为不可再生资源,随着不断的开采,磷矿资源也已接近枯竭。转炉渣中含有2%~5%的P2O5,是一种廉价的磷资源,所以若能将钢渣中的磷回收再利用,不仅可节约磷矿的开采量而且也可以更加容易的进行钢渣的后续利用 [13] 。因此,还原回收钢渣中的磷资源也具有重大的现实意义。
为了能够使熔融态钢渣可以在冶金流程中循环使用,避免磷的累积,早在1975年,日本就进行了对熔融态钢渣的还原脱铁和磷的研究,宫下芳雄 [14] 等人直接在转炉出钢后钢渣中添加碳材、萤石,在吹氧5 min后的检测结果中发现,渣中FeO和P2O5的还原率都能达到90%。但是,其中只有60%的磷进入铁相,40%被气化。
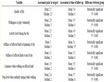
Table 2. Chemical composition of BOF slags
表2. 部分钢铁厂转炉渣的化学成分

Figure 1. Reduction rate curves of different reductants
图1. 不同还原剂的还原率曲线
李光强等人[15] 进行了高温碳热还原进行转炉渣资源化的研究。研究结果表明,温度在1923 K时,渣中部分FeO和P2O5可以被还原,还原出的磷大部分进入铁碳合金中形成Fe-C-P合金。在2073 K下,渣中的磷可以完全被还原出来,其中60%以上可以进入铁碳合金中,但是进入金属中的磷随着保温时间的延长而逐渐减少。
吕岩等[16] 利用微波加热方式对1100℃~1400℃下转炉钢渣的碳热还原行为进行了研究,试验结果表明,使用微波手段脱除钢渣中磷具有较好的效果,但是钢渣中磷主要以气体形式脱除,留在还原铁相中的磷极少。
王德永等人[10] 在钢渣中同时回收铁和磷的资源化利用新思路的研究中发现,在先对转炉渣进行改制处理,使得渣碱度调整在1.2左右,然后再用碳饱和铁水与固体碳共同还原,可以使得还原出的磷有效的迁移至铁水相,减少磷的挥发,多次富集后得到的高磷铁水可作为低品位磷铁合金应用于炼钢生产。
综上所述,为了实现钢渣的综合利用,避免钢渣中有价元素的浪费,对熔融态钢渣进行还原处理,可以实现有价元素的高效回收。而且转炉钢渣出渣温度也较高,倘若能够在实际生产中应用,势必节省大量的能耗,而且还原后的钢渣中主要含有氧化钙、二氧化硅和氧化镁,对钢渣的后续利用也提供了便利。考虑到目前转炉炼钢工艺流程的连续性,必须考虑如何实现还原处理后的渣铁分离,以及对分离后的余渣进一步的处理利用,避免渣资源的浪费。
4. 熔融钢渣直接合成有价材料的研究
为了充分发挥钢渣作为二次资源的利用价值,从根本上减少钢渣的产生量,将熔融态钢渣合成有价材料如陶瓷、微晶玻璃等也具有极大的意义。国外对钢渣微晶玻璃的研究较早,美国的Agarwal G等人[17] 利用钢渣制造的微晶玻璃,具有比普通玻璃高2倍的耐磨性及较好的耐化学腐蚀性。西欧的Goktas A A用钢渣制造出的透明玻璃和彩色玻璃陶瓷,可以用作墙面装饰及地面瓷砖[18] 。2010年,Sarkar R等人[19] 开展了热态电炉渣配30%~40%的辅料制备陶瓷砖的研究。
虽然国内开展这方面的研究较晚,但是近年来也取得了一些成就。姚强等[20] 人利用宝钢钢渣制备出了微晶玻璃材料,其各项性能都优于花岗岩、大理石和瓷质砖。张乐军,封鉴秋等[21] [22] 人证实了利用钢渣和粉煤灰制备微晶玻璃的可行性,并且可以满足建筑材料的性能要求。杨志杰[23] 等人通过对熔融态钢渣进行直接改质并制备微晶玻璃的研究,认为该处理方法不仅可以高效利用熔态钢渣的显热,而且制得了以透辉石为主晶相且性能优越的微晶玻璃,如表3所示。
综上所述,国内外的研究表明了通过改质熔融态钢渣来制取微晶玻璃的可行性,若此工艺能够实现工业化生产,将给钢铁企业带来巨大的经济和环境效益,一方面解决了钢渣的排放问题;另一方面通过将熔融态钢渣制成价格较高的有价材料,微晶玻璃等,也为如今钢铁企业不景气的现状,去除了处理钢渣的费用并带来一定的经济效益,实现“双赢”。虽然国内外的研究表明了制备钢渣微晶玻璃的可行性,但是也存在着许多问题制约着产业化的发展,如:钢渣的成分复杂多变;对熔融钢渣热态调质实际施行方案较难实现等。
5. 熔融态钢渣显热回收的研究
转炉冶炼结束后,熔融态钢渣温度在1600℃以上,其内蕴含的热能高达68 kgce/t,是高品质的余热资源,极具开发利用价值。在当前节能减排、环境保护的大背景下,积极开发利用熔融态钢渣的热资源,不仅可以节约能源、降低生产成本、提高钢铁企业的竞争力,还可以避免资源浪费,具有较好的经济和环境效益。目前,对于熔融态钢渣显热回收的利用可分为物理手段和化学手段两种。
5.1. 物理手段
显热回收的物理手段主要是通过介质的热传导、对流换热和热辐射。目前钢铁企业主要采用风淬法,滚筒法,连铸连轧法和粒化轮法等[24] -[26] 对钢渣进行预处理的同时进行热回收,但是采用这几种物理手段进行热回收存在着很多的问题。首先,大部分的处理工艺对钢渣的流动性都有很高的要求,这就导致钢渣的处理率较低,对于流动性不好的钢渣只能采用其他工艺进行处理,造成热能浪费。其次,在采用物理法进行热量回收时,传热的介质主要是水、空气等,不仅造成热回收率低而且会产生污水、粉尘等环境问题。
5.2. 化学手段
化学手段就是通过化学反应将熔融钢渣的显热转化为化学能进行利用。通过向钢渣中添加其他物料,利用熔融态钢渣的物理显热,直接合成有价材料如陶瓷,微晶玻璃,建筑材料等的方式[27] [28] 最具经济和环境效益。从热量的回收效率看,利用化学手段回收熔融钢渣显热的效率较高,比物理手段更有前途。
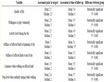
Table 3. Slag glass ceramics compared with the other physical properties of building materials
表3. 钢渣微晶玻璃与其它建材物理性能对比
6. 熔融态钢渣回收利用存在的问题及未来发展的方向
从以上的分析可得知,在对熔融态钢渣的综合回收方面的研究已经取得了许多成果。但是,仍然存在着一些问题没有解决,主要有以下几个方面:
1) 目前大部分钢铁企业对熔融态钢渣采用的冷却–破碎–磁选工艺,虽然便于机械化、工艺流程简单、成本较低,但这种工艺流程不能有效的回收渣中的有价元素,热回收率也较低。
2) 在对熔融态钢渣还原回收有价元素的研究中,我们可以发现对熔融态钢渣进行还原处理时,还原温度和渣的粘度是制约有价元素还原回收铁合金的两大制约条件。所以,在对出渣后的熔融态钢渣进行还原时,应着重解决温度的补偿和渣的粘度两大问题。
3) 将熔融态钢渣直接制备成有价材料(陶瓷材料等)方面,钢渣的成分复杂多变也制约着对熔融态钢渣热态调质的实际施行。
在解决熔融态钢渣综合回收利用上存在的问题时,一方面要对有价元素进行回收,另一方面要提高余渣的利用价值。本文提出回收有价元素后将余渣直接制成高附加值的有价材料的工艺流程,来解决熔融态钢渣回收利用。但是,这种工艺必须要解决的主要是整个工艺流程的钢渣改质以及温度补偿问题。
1) 不论是渣中有价元素还是余渣都有很高的利用价值,在对熔融态钢渣还原处理后,钢渣的改质将成为渣金有效分离与制备有价材料的关键环节。所以,根据目前对钢渣直接制备成有价材料的研究基础,分析有价材料的成分以及高温下的粘度,找出高温下既适合渣金分离的粘度又符合成分要求的有价材料。这样既可以高效的回收有价元素,又能进一步的提高余渣的利用价值,从根本上解决钢渣的排放问题。
2) 熔融态钢渣的“热”资源是其本身的一大优势,但仅靠熔融态钢渣自身的物理显热,显然满足不了整个回收工艺流程的热量需求。因此,有必要在整个工艺流程中增加一个电加热装置,来解决还原的温度条件、添加改质剂后的温度补偿以及空冷散热等问题。
7. 结语
实现熔融态钢渣的综合回收利用,不仅可以降低钢渣的排放量,还可以降低生产成本、避免资源浪费,具有较好的经济和环境效益。目前对于熔融态钢渣回收利用的研究中,存在着有价元素的回收利用率低、热资源的浪费以及余渣利用的附加值较低等问题。对于熔融态钢渣,要充分发挥其自身“渣”和“热”的双重优势,在添加合适的改质剂以及增加电加热装置的基础上,使用回收有价元素后将余渣直接制成高附加值的有价材料的工艺流程,来进行熔融态钢渣的全面回收利用,将实现熔融态钢渣资源利用的最大化。