1. 引言
木质素具有可再生、可降解、无毒等优点,因而被视为优良的绿色环保型化工原料。自19世纪,人们开始便开发利用木质素,最开始利用的是木质素磺酸盐,来自于亚硫酸钙制浆废液中,其主要用作皮革鞣剂和燃料添加剂方面 [1] ,在19世纪中末期,关于该种木质素磺酸盐木质素作胶粘剂的专利首次见刊,大约20世纪50年代后,随着对木质素胶粘剂的不断研发,利用木质素改性酚醛树脂、脲醛树脂作为胶粘剂的专利层出不穷,80年代以后,木质素的分离纯化,改性等方面受到了木质素研究者的广泛关注。到了90年代以后,随着现代分析仪器技术的发展与更新,木质素作为胶粘剂的化学反应机理和反应特性成为研究的焦点研究,从而木质素胶粘剂制备的理论和技术不断成熟。近年来,随着人们对绿色生态环保理念的理解与深入,新型的环保类木质素胶粘剂问世 [2] 。木质素的化学反应活性主要与结构单元中酚羟基、醇羟基和酚羟基邻、对位活泼氢的含量成正比。树脂合成过程中利用可再生无毒的木质素替代苯酚制备木质素酚醛树脂,既能减少苯酚的使用量,又达到废物利用,实现资源化治理的目的。
本文综述了木质素在胶粘剂中的应用,重点介绍了木质素酚醛树脂研究进展与发展趋势木质素在酚醛树脂中的应用,评述了木质素酚醛树脂的最新进展,以及木质素酚醛树脂存在的问题,旨在全面评价木质素在胶粘剂应用特点,进而指导木质素及其改性衍生物在高分子胶粘剂领域的应用。
2. 木质素胶粘剂概述
木质素结构分子中含有酚羟基和醛基等活性官能团,因而,用木质素改性胶粘剂可节约苯酚和减少甲醛的残余量 [3] 。木质素在胶粘剂中的应用主要有两种方式:第一,将木质素与酚醛树脂和聚氨酯等混合,然后进行改性反应,从而制备出胶粘剂;第二,以木质素自身为胶粘剂,工艺操作过程需要复杂的反应条件,如较高的热压温度、很长的热压时间等。比如常见的木质素磺酸盐和碱木质素等通过添加反应助剂,按照一定的反应条件,从而制备出木材用胶粘剂。
2.1. 木质素胶粘剂发展史
自19世纪,人们开始便开发利用木质素,最开始利用的是木质素磺酸盐,来自于亚硫酸钙制浆废液中,其主要用作皮革鞣剂和燃料添加剂方面,在19世纪中末期,关于该种木质素磺酸盐木质素作胶粘剂的专利首次见刊,大约20世纪50年代后,随着对木质素胶粘剂的不断研发,利用木质素改性酚醛树脂、脲醛树脂作为胶粘剂的专利层出不穷,80年代以后,木质素的分离纯化,改性等方面受到了木质素研究者的广泛关注。到了90年代以后,随着现代分析仪器技术的发展与更新,木质素作为胶粘剂的化学反应机理和反应特性成为研究的焦点研究,从而木质素胶粘剂制备的理论和技术不断成熟。却并没有实现工业化生产,主要是由于生产条件苛刻、能耗高和设备易腐蚀等。近年来,随着人们对绿色生态环保理念的理解与深入,新型的环保类木质素胶粘剂问世,但其仍未实现工业化生产,主要是由于木质素结构组成不均一、反应活性较低、产物性能不稳定等多种原因,严重的限制了木质素胶粘剂的应用。
2.1.1. 木质素本身作为胶粘剂
尹子康等 [3] 对木质素磺酸盐进行改性反应后,作为胶粘剂,并对其热压生产过程和胶合性能进行研究,结果表明木质素磺酸盐自身作为胶粘剂,其良好的胶合性能可直接用于胶合板的生产。Li等 [4] 通过碱木质素与聚乙烯亚胺、聚酰胺多胺–环氧氯丙烷共混,从而制备出了两种无醛型环保类木材胶粘剂。Li等 [4] 通过木质素(小分子质量)、单宁与乙二醛混合,制备出环保型木材胶粘剂,其天然材料约含80%,该种环保型胶粘剂具有较好的结合强度,可达到室外级相关标准与要求。
2.1.2. 木质素–脲醛树脂胶粘剂
脲醛树脂无色黏度低,水溶性好,固化速度快,吸附力强,性能稳定,但其耐水性能不好,热压过程释放甲醛有害气体。因此,采用木质素改性脲醛树脂,大大降低了游离甲醛释放量,同时使其生产成本下降。
木质素–脲醛树脂的生产工艺经历了不同的发展阶段。最早阶段,研究者通过采用不同的催化剂,将木质素与脲醛树脂共混,得到木质素脲醛树脂胶粘剂产物。但存在胶粘剂产物力学强度较差;而后,研究者首先将木质素进行化学改性,主要包括羟甲基化、氧化、磺化改性等,然后再与脲醛树脂混合制备木质素脲醛树脂胶粘剂,该种方法制备的产物性能均得到提高。
之后,Raskin等 [5] 发明了一种新型的木质素–脲醛树脂胶粘剂,采用该种胶粘剂进行人造板加工生产,板材的机械性能稳定。该种胶粘剂生产工艺过程大致如下:以FeC13等催化剂,木质素磺酸盐首先与丙烯醛等一些不饱和醛类发生反应,然后再与脲醛树脂混合制备胶粘剂产物,其接枝共聚物可以高达80%。
2.1.3. 木质素改性聚氨酯胶粘剂
聚氨酯是反应型胶粘剂,可以分为两类:聚氨酯与多异氰酸酯,具有较好的胶合性能,但存在难降解、生产成本较高等缺点。然而,当聚氨酯中添加木质素后,有效的避免了上述问题,即产物易降解、生产成本得下降。
提高木质素与聚氨酯的反应程度是木质素改性聚氨酯胶粘剂关键所在,而提高其反应程度主要在于提高木质素中醇羟基的含量。刘全校等 [6] 采用溶液流延法,以木质素和甲苯二异氰酸酯或六亚甲基二异氰酸酯为原料,得到木质素–聚氨酯塑料。
2.1.4. 木材液化制备胶粘剂
早在20世纪20年代,人们发明出了木材液化技术,使其成为燃料或化工原料 [7] ,工艺原理大致如下:木材中的大分子化合物通过液化方法降解小分子化合物,即固态木材转化为具有特定活性官能团的液态化合物,反应活性增强。早期木材液化的方法主要是采用高温高压法,随后木材液化的方法不断发展与增多。从而增大了木材的应用空间,可用于生产胶粘剂、塑料、碳纤维、易生物降解类高分子化合物等 [8] 。
木材的苯酚液化产物常用于制备胶粘剂。苯酚的活性空位与降解的木材小分子组分的活性点反应,反应后的这些小分子具备了酚类物质所具有的化学特性,可以用来替代苯酚,从而制取共聚树脂 [9] 。白石信夫等研究表明,将木材进行羧甲基化改性后,与苯酚、间苯二酚反应分别得到木材-苯酚胶粘剂,木材-间苯二酚胶粘剂,这两种胶粘剂的胶黏强度显著高于酚醛树脂胶粘剂 [10] 。
由于催化剂酸性不同,苯酚液化产物性能不同。林兰珍等 [11] 研究结果证实,当采用硫酸、磷酸和草酸两类催化剂,苯酚液化产物结构和性能截然不同,后者与天然木材化学结构大致相同,具有较高的结合酚量,当与甲醛发生反应时,完全将没有与木材反应的苯酚全部转化为树脂。
水高度离子化也可以作为酸性催化剂。木材在近临界条件下,即高度离子化的水为酸性催化剂,可迅速液化,相对于普通酸催化剂,其总反应速率提高10~100倍。Li等 [4] 采用超临界状态的苯酚,在30 s内使木材迅速液化,液化率可达90%以上。超临界流体液化实现了低温快速液化的目的,但对反应设备和反应条件要求较高。
3. 酚醛树脂
19世纪中期,A. Bayer(西德化学家)首先发现,当PH < 7,有酸性物质时,醛和酚发生缩合反应,得到一种树脂状产物,该产物为棕红色、无定型、不能进行再处理,当时研究者不太关注这种树脂状产物。19世纪末,化学家史密斯(A. Smith)和化学家克莱堡(W. Kleeberg)再次对甲醛和苯酚的缩合反应进行了系统的研究,通过反应介质、改变催化剂等条件来实现对反应的控制,使反应速度平缓,制备出较硬的呈块状或片状的产物,然后将其切削,制得不同形状的工艺品。
1901年以后,研究者对苯酚–甲醛缩合反应较为关注。世界上第一个商业化苯酚–甲醛酚醛树脂(Laccain)在20世界初由L. Blulner推出。继而,A. Lugt也制备出了该种树脂。当时研究者无法克服酚醛树脂容易破碎的缺点。而后,L. H. Backeland发明了不易破碎的酚醛塑料,增强了其实用价值,其特别之处在于,在高压的生产过程下,将木粉或填料加入反应过程中,并指出甲醛和苯酚的用量比和所用催化剂类型影响酚醛树脂的热塑性。
乙阶酚醛树脂作为绝缘材料,可应用于电器、涂料和清漆等方面,这种树脂是由艾尔斯活思(Aylesworth) 1911年发现的,当乙阶酚醛树脂被六次甲基四胺作用前后,将由可溶可熔性转变为不溶不熔性。20世纪中期,苏联塔拉索夫、彼得夫等发明卡尔波里特铸塑体,就是将石油磺酸和芳磺酸加入酚醛制备工艺中。而后,K. Albert研究将松香加入酚醛制备工艺中,制备出松香改性的酚醛树脂,此外,他又发明了漆膜,即把桐油和树脂混合的产物(油漆)涂刷到物体的表面,干燥4小时后,物体表面形成了膜,这种膜具有良好的防腐等性质,为酚醛树脂应用于涂料工业开辟了新途径和新领域。
20世纪80年代,新型酚醛制品层出不穷,其广泛应用于建筑、军事、交通各个领域 [12] 。如何在低温下固化酚醛树脂是研究者的当时关注的焦点,尤其是Chemical和Wallay total等企业。目前,开发新型的复合材料及酚醛树脂已经成为重要的研究方向。一种新型的开环聚合酚醛树脂由谢美丽和顾宜等 [13] 开发成功。北美的Mudde [14] 成功制备了以玉米淀粉为原料的酚醛树脂,不断开发出来的新型酚醛树脂和传统酚醛树脂相比,前者具有价格低廉、性能相当、无污染或污染少等优势。
3.1. 酚醛树脂分类
目前,根据所制备的酚醛树脂的性质和用途不同,醛和酚配比、催化剂的类型及反应条件也不同。在酚醛树脂生产中,以酚类和醛类为原料,前者以苯酚、间苯二酚甲酚等酚类物质为主,后者以甲醛、丙烯醛等醛类物质为主;根绝pH值,反应催化剂分为两类:酸性催化剂、碱性催化剂 [15] - [17] 。当采用酸作催化剂,在其加工成型时需要加入固化剂的热塑性酚醛树脂(Novolak型),又称为二步法酚醛树脂(PF2),常见表观为固体状 [18] ;当采用碱催化剂,在其加工成型时不需要添加固化剂的热固性酚醛树脂(Resol型)也常称为一步法酚醛树脂(PF1),常见表观为液体状;图1 为酚醛树脂分类示意图。
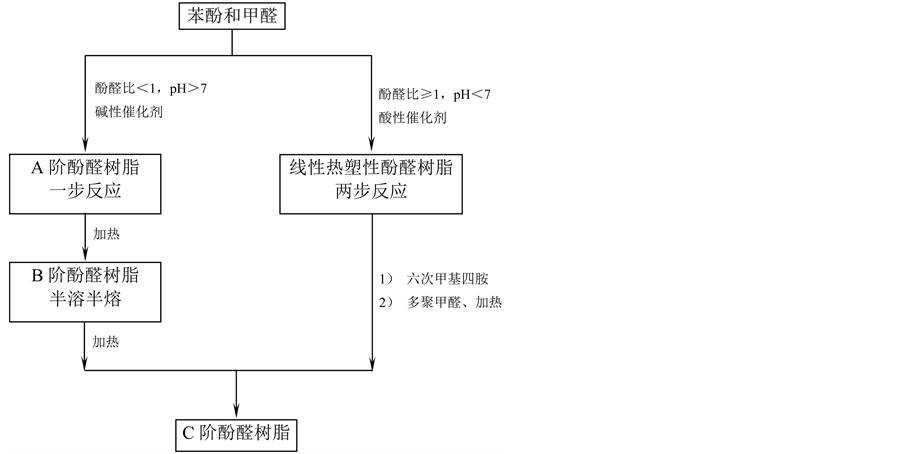
Figure 1. The classification diagram of phenol-formaldehyde resin
图1. 酚醛树脂分类图
3.2. 酚醛树脂的研究进展
1) 丁腈橡胶改性酚醛树脂 [19] - [24]
酚醛树脂的韧性主要由丁腈橡胶决定的。由于丁腈橡胶粒子均匀分散在酚醛树脂的连续相中,明显增加酚醛树脂的韧性和抗冲击强度,同时起到延缓应力裂缝的发展和阻止断裂破坏过程的作用。李新明等 [25] 深入的研究丁睛橡胶共聚反应,研究结果表明在酚醛树脂制备工艺中,当丁睛橡胶加入量为2%时,便可显著提高酚醛树脂的抗冲击强度。
2) 聚对苯二甲酸丁二醇醋改性酚醛树脂
酚醛树脂聚和对苯二甲酸丁二醇醋两者具有良好相容性,后者本身是热塑性树脂,具有较高热稳定性和韧性的特点,当与前者混熔时,四个相连的亚甲基碳链结构被引入到产物中,使其韧性和机械强度得到进一步增强,而产物的热稳定性没有发生改变 [26] 。
3) 聚酰胺及其衍生物改性酚醛树脂
较高的机械强度和韧性是聚酰胺所具性能优势,利用这个优势将其与酚醛树脂共同化,以便形成互穿网络的稳定结构,从而酚醛树脂的机械强度的得到提高 [27] [28] 。酚醛树脂结构中酚羟基与聚酰胺结构中酰胺基之间通过氢键促进酚醛树脂和聚酰胺的相溶 [29] 。在一定温度下,用适量的甲醛处理聚酰胺,可获得羟甲基聚酰胺,能与酚醛树脂的羟甲基化基团发生固化反应,从而获得良好的胶接强度。
4) 梓(桐)油改性酚醛树脂
梓(桐)油改性酚醛树脂制备分两个反应阶段实现的,第一阶段是在酸性条件下,植物油和过量的苯酚发生化学反应,反应结束后进入第二阶段,碱性条件下第一阶段的产物与甲醛发生反应,生成梓(桐)油改性酚醛树脂。杨进元等 [30] 研究结果表明梓(桐)油改善了酚醛树脂的韧性,同时也提高了树脂的耐热性。
5) 钼改性酚醛树脂 [31]
在催化条件下,苯酚、甲醛、钼酸为主要原料,反应生成一种新型的耐烧蚀树脂,即钼酚醛树脂。由于通过钼酸改性,使得酚醛树脂的耐热性得到很大提高。当树脂中钼含量达到12%时,得到的固化酚醛树脂热分解温度高达522℃。其耐热性能比钡、氨酚醛等其它类型树脂显著增强。
6) 硼改性酚醛树脂
由于缩聚物中,硼原子是以B-O酯键存在(键能较高,773.3 KJ/mol),这赋予了硼酚醛树脂较高的耐热性,即在高温条件下变成坚硬且高熔点的碳化硼,所以当温度升高至900℃时,硼酚醛树脂残碳率达到70% [32] 。同时,由于硼酚醛树脂中引入B-O酯键结构存在,有效的增强了树脂的韧性以及机械性能。目前主要该种树脂主要应用于空间技术方面(如空间飞行器和导弹等) [33] 。
7) 有机硅改性酚醛树脂
为了提高酚醛树脂的耐热和耐水能力,采取有机硅与羟甲基或酚羟基发生反应方式来实现。有机硅改性的酚醛树脂复合材料可在200℃~260℃温度下长时间工作,主要应用于耐高温材料方面(如火箭等耐烧蚀材料) [34] [35] 。
8) 双马来酰亚胺改性酚醛树脂
该种树脂可在低压条件下成型、固化反应过程中不会释放低分子化合物、绝缘性能优异、阻燃性能较强、力学性能良好 [36] 。双马来酰亚胺主要通过与酚醛树脂酚羟基上的活泼氢发生加成反应 [37] ,使改性树脂的热分解温度显著提高,从而有力的增强了产物的耐高温性能。
9) 氰酸酯改性酚醛树脂
氰酸酯改性酚醛树脂(酚三嗪树脂)反应过程如下:一定量的三烷基胺和热塑性酚醛树脂在二氯甲烷溶剂中反应,生成树脂季胺盐,在零下30℃温度条件下,再与二氯甲烷溶液发生化学反应。经过滤分离、溶剂回收等工艺后,制备出产物酚醛树脂的氰酸酯。所得到的氰酸酯酚醛树脂的热氧化稳定性相对于酚醛树脂有了较大改善。这归因于稳定的氰基及其所生成的三嗪环取代了酚醛树脂的羟基,并形成交联结构,同时有韧性的氧醚键存在于固化物交联密度大的三嗪环网状结构中,即使在400℃温度高条件下,在三个方向上氧醚键仍存在 [38] 。从而增强了该种固化树脂具有良好的韧性强度 [39] 。
10) 芳烷基改性酚醛树脂 [40] [41]
苯酚与甲醛反应生成酚醛树脂的反应中,最主要的是引入芳烷基作为保护基团,从而有效的保护酚羟基结构,之后再进行后续反应。所得到这类树脂产物在高温环境下可长期使用,并具有优异的耐氧化性和耐热性,用其制作的玻璃钢在高温下有较高的弯曲强度保持率,此类树脂主要应用于火箭壳体材料等领域。
11) 烷基磷酸酯改性酚醛树脂
为了改善酚醛树脂的阻燃性,在酚醛树脂合成过程中通过引入烷基磷酸酯来提高酚醛树脂阻燃效果。由于烷基磷酸酯基团可以有效的抑制火焰,因此烷基磷酸酯改性酚醛树脂阻燃机理为凝聚相阻燃,由于燃烧时会有磷酸或磷酸酐等物质产生,导致聚合物发生脱水并炭化,防止产生更多可燃性气体,从而阻断燃料向火焰供给 [42] 。
12) 氮改性酚醛树脂(苯并噁嗪树脂、开环聚合酚醛树脂) [43]
该种树脂反应过程大致如下:以胺类化合物、甲醛和酚类化合物作为起始原料,生成苯并噁嗪类化合物中间体,随后在催化剂或加热条件下,该化合物中间体通过开环反应重新聚合成含氮的交联网状结构,此结构与酚醛树脂交联网状结构相似。该种酚醛树脂产物收缩率小、没有低分子挥发物 [44] 、具有高含氮量的结构和杂环,耐高温摩擦性能和阻燃性能优良,主要应用于高性能的增强纤维复合材料。
13) 高分子量酚醛树脂 [45]
高分子量的线型酚醛树脂主要是在酸或碱水溶液作催化剂作用下,而邻甲酚或对甲酚与甲醛在强酸和强极性溶液条件下发生醛类和酚类缩合反应从而制备。近期,一种新型酚醛树脂高分子量成型材料在日本研究成功,此种高分子量树脂起始失重温度较高,约为340℃,耐冲击强度和弯曲强度也较高,分别达到11 kJ/m2和31.9 MPa。
4. 木质素酚醛树脂研究进展与发展趋势
天然木质素分子结构中含有一定量的醛基官能团和酚羟基官能团。在酸存在的条件下,木质素可以酚发生缩合反应;在碱存在的条件下,木质素又可以和醛发生缩合反应。因而,酚醛树脂在碱性条件下合成过程中,木质素可以替代部分苯酚参与酚醛树脂合成,这不仅可以改善酚醛树脂的性能,还可以使生产酚醛树脂成本大大减少 [46] [47] 。
为了进一步提高木质素反应活性,常常需要对木质素进行改性处理,目前较常用的方法包括羟磺化、酚化、甲基化、脱甲基化以及氧化反应等 [48] 。木质素经活化改性后,有利于提高木质素在酚醛树脂中使用量,从而进一步提高和改善酚醛树脂的性能。
1) 木质素磺酸盐
磺化木质素也称木质素磺酸盐,是制浆生产过程中亚硫酸盐法产生的副产品,是一种线性高分子化合物,反应活性也较低。需要在高温酸性条件下木质素磺酸盐与苯酚进行酚化改性。酚化可以有效的减小木质素的分子质量和甲氧基含量,增大木质素的酚羟基含量,从而可以取代苯酚(毒性较高)的工业化应用(如合成树脂等),该种改性的木质素磺酸盐可以保护环境,实现资源有效利用的目的 [49] 。
2) 碱木素
碱木素又称木糖粉,来自于传统碱法制浆“黑液”,其经过过滤加工后,采用喷雾干燥所得到的固形物。由于碱木素在制浆过程中经过高温高碱处理,碱木素分子上的活性官能团消耗殆尽,通常需要对碱木素进行改性,才能用于酚醛树脂合成,常用的改性法有甲基化、酚化、脱甲基化等。
甲基化改性是指在碱木质素苯环或苯环侧链引入羟甲基官能团,从而实现通过增加羟甲基官能团含量增强碱木质素反应活性。
脱甲基化改性是将木质素苯环上的甲氧基官能团脱除,并增加酚羟基官能团的反应。安鑫南等人利用碱木质素黑液与硫在温度为220℃~240℃条件下反应0.5 h,然后冷却,进行酸处理后,用乙酸乙酯萃取分离得到脱甲基化改性木质素,其甲氧基含量为5%,因而,脱甲基化改性木质素可作为苯酚的替代,用来制成良好性能的胶粘剂 [50] 。碱木素脱甲基化改性在一定程度上提高碱木质素反应活性点的数目,该种改性方法具有高成本、工艺操作过程繁琐等缺点。
酚化改性是将苯酚和碱木质素在碱性高温条件下进行反应。碱木质素酚化改性有效的增加碱木质素活性官能团数目,且工艺操作过程比较简单。Sudan [51] 在碱性条件下将“黑液”酚化进行改性后制备成LPF树脂,其具备良好性能,产物中苯酚被木质素取代率约60%。刘纲勇等[52] 在碱性条件下,将麦草碱木质素进行酚化改性后制备成LPF胶粘剂(为国标I类板),苯酚被木质素取代率约70%。
3) 植物酶解木质素
植物酶解木质素通常是以秸秆发酵制乙醇过程中产生的残渣为原料,从中提取分离得到的木质素,由于提取分离条件温和,使得木质素上化学活性官能团较好地被保留下来。郑钻斌等[53] 以秸秆发酵制备乙醇所残留的渣子为原料,从中进行酶解木质素,经过后续处理后,生成改性酚醛树脂胶,通过热压工艺制成胶合板。此方法木质素无需预处理,只是木质素替代苯酚率较低,目前还没实现工业化应用。
4) 有机溶剂(高沸醇)木质素
高沸醇法木质素通常使用高沸点的有机醇作为木质素提取液,在催化剂作用下从木质植物原料中提取木质素,加入适当比例的水使得溶解在高沸醇中的木质素沉淀析出,高沸醇法木质素具有纯度高、化学活性强等优点。如在松香酚醛树脂生产过程中加入高沸醇木质素,叔丁基苯酚可以被高沸醇木质素部分取代,从而大大降低了苯酚和甲醛用量,有力的保护了生态环境。
5. 木质素酚醛树脂胶粘剂中存在的问题
木质素酚醛树脂通常采用工业木质素对酚醛树脂进行修饰改性,由于工业木质素自身结构与性质缺陷决定了其在树脂应用研究过程中,存在以下几方面主要问题:
1) 在纤维原料蒸煮制浆过程中,脱木质素是在较高反应温度和强碱作用下完成的,木质素会发生大量的降解和无序缩合反应,改变了木质素的基本分子结构,降低了分子量,且分布变宽,成分组成更为复杂,均一性差;
2) 另外,脱出的木质素也易发生氧化反应,造成工业木质素甲氧基含量高,特别是羟基含量相对较低,直接导致工业木质素化学反应活性降低,其分子结构中有大量的紫丁香基结构单元,少量的愈创木基结构单元;
3) 碱木质素在制浆过程中发生了缩合反应和氧化反应等,导致木质素分子上缺乏活性官能团,特别是缺乏双亲性的官能团,因此工业木质素较难溶解于有机相和水相中;
4) 此外,纤维原料种类、采伐时间以及存放条件的不同,使得工业木质素含量和组成都不尽相同。
6. 展望
综上所述,有机溶剂法提取分离木质素具有化学结构破坏较小,木质素能保持原有天然高分子化学活性。有机溶剂法提取木质素具有无污染、节能等特点,属于清洁生产工艺,与传统制浆法有本质区别,其应用前景将更为广阔。与传统工业木质素相比具有灰分含量低、含糖少等特点,在结构上较好地保留了各种活性基团,特别是酚羟基和醇羟基,这对于合成胶粘剂尤其有利。因而,高反应活性的有机溶剂法木质素制备方法和产业化应用仍需进一步完善。
基金项目
林业公益性行业科研专项(201304601);青年教师自主创新基金项目(DL12BA37)。