1. 引言
采用硅氧烷偶联剂对丙烯酸酯改性,一方面可通过硅氧基的水解缩合反应形成交联结构,提高共聚物的强度;另外共聚物中未反应完的Si-OH基可与无机基材表面的羟基等基团作用,形成氢键或化学键,提高其与被粘附表面的粘接强度。但缺点是在乳液聚合过程中,有机硅氧烷单体易于水解而发生自缩聚反应,影响乳液的聚合稳定性和贮存稳定性 [1] [2] 。已有研究者 [3] - [7] 考察了有机硅单体的加入对体系凝聚物析出的影响以及提出了一些控制措施,也有研究者 [8] [9] 对乳液的粒径分布进行分析,制备出了有机硅改性丙烯酸酯纳米乳液,但要从根本上抑制有机硅的水解仍有很多有待解决的问题。本文通过对乳液外观观察以及对反应体系凝聚率的测定,定性和定量表征乳液聚合过程的反应稳定性,考察多种因素对反应体系稳定性的影响,确定稳定有机硅改性聚丙烯酸酯纳米乳液的合成条件,简单分析反应过程中凝聚物的析出机理,可对稳定的有机硅改性丙烯酸酯乳液体系的制备提供一定的理论指导。
2. 实验部分
2.1. 主要原料
甲基丙烯酸甲酯(MMA),丙烯酸丁酯(BA),α-甲基丙烯酸(MAA)(国药集团化学试剂有限公司);甲基丙烯酸-2-羟基乙基酯(HEMA) (日本进口瓶装);乙烯基三乙氧基硅烷(A151) (中国蓝星化学清洗总公司);过硫酸铵(APS) (爱建德固赛上海化学试剂公司);十二烷基硫酸钠(SDS) (Farco);辛基酚聚氧乙烯醚(OP-10) (淄博天德精细化工研究所);去离子水(自制)。其中MMA、BA、HEMA均经过减压蒸馏除去阻聚剂,其它试剂未经处理直接使用。
2.2. 共聚乳液的合成
1) 单体半连续滴加法:先将去离子水、乳化剂、缓冲剂和部分引发剂加入到反应器中进行预乳化10 min,通氮气10 min,然后在4 h内连续滴加单体,待单体滴加一半时再加入部分引发剂水溶液,待滴加完成后补加剩余引发剂熟化1 h后出料。
2) 种子预乳液法:先将去离子水、乳化剂、缓冲剂、全部反应单体及功能性助剂加到容器中进行超声预乳化10 min制得预乳液。取约1/3的预乳液及大部分计量的引发剂于反应器中,通氮气10 min,在设定温度下反应30 min得淡蓝色种子乳液,然后在180 min内连续滴加剩余2/3单体预乳液,补加剩余引发剂熟化1 h后出料。
3) 间歇法:将所有的反应物料一次加入到反应器中,充分乳化10 min,通氮气10 min,然后加入引发剂水溶液进行反应,反应进行5.5小时后出料。
2.3. 性能表征
2.3.1. 重量法测定乳液固含量和单体总转化率
准确称取适量乳液(约2 g左右),放入装有1 mL 0.1%对苯二酚阻聚剂溶液的铝箔中,在120℃烘箱内烘干至恒重,按下式计算实际固含量s。

其中m0、m1、m2分别为阻聚剂、烘干前乳液和阻聚剂、烘干后干胶和阻聚剂的质量。
聚合反应的转化率x定义如下:
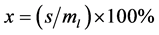
其中ml为理论固含量,其值由假设体系中单体全部反应计算所得。
2.3.2. 凝聚率表征反应稳定性
乳液聚合完成后,将乳液过滤,收集滤纸上以及釜壁和搅拌器上的凝聚物,然后将其用蒸馏水洗涤后在120℃烘箱中干燥至恒重,表征反应稳定性的凝聚率σ按下式计算。
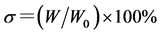
其中,W为烘干后凝聚物的质量,W0为单体的总质量。
2.3.3. 粒径测定
将乳液稀释到0.2 wt%,用Zetasizer3000 ZETA电位-粒度分析仪分析粒径分布。
3. 结果与讨论
3.1. 聚合工艺对反应稳定性的影响
探讨了单体半连续滴加法、种子预乳液法、间歇法等合成工艺对反应稳定性的影响,结果见表1。
从表1看出,采用单体半连续滴加法,可使乳胶粒处于“饥饿”状态,乳液中单体珠滴稳定占用的乳化剂少,更多乳化剂用来产生胶束,因此乳胶粒子多,粒径小,乳液呈现蓝光。但反应体系中单体浓度低,单体向乳胶粒的扩散速度相对较慢,导致反应速度慢,乳胶粒子反应平稳。由于粒子在反应体系中停留时间不同,在反应成核阶段会生成粒径不一的乳胶粒,致使粒径分布较宽。而种子预乳液法会使更多单体预乳化产生单体珠滴,需要的乳化剂较多,使得体系胶束较少,制得的种子乳液聚合反应较平稳,但乳胶粒粒径较大,难以得到纳米(100 nm左右)乳胶粒子。对间歇法来说,反应体系单体浓度较单体半连续滴加法和种子预乳液法高,反应速度较快,反应放热显著(体系温度升高2℃~3℃),胶粒粒径较大但粒径分布均匀,40%单体固含量时粒径在200 nm左右(粒径测量部分本文没有给出)。所以采用单体半连续滴加工艺,可制得聚合反应稳定的100 nm左右的有机硅改性聚丙烯酸酯纳米乳液。
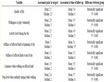
Table 1. The effects of different polymerization methods on reaction stability
表1. 不同聚合工艺对反应稳定性的影响
注:搅拌速率 = 200 rpm,m(A151) = 4%,m(HEMA) = m(MAA) = 2%,T = 80℃,m(S) = 3%,m(I) = 0.3%,初始pH = 7
3.2. 聚合温度对反应稳定性的影响
我们考察了聚合温度在60℃~90℃时乳液聚合的稳定性及反应转化率,如表2所示。
从表2可看出,随着温度的升高,反应转化率增大,凝聚率提高,反应稳定性降低。这主要是因为热引发剂APS的过硫酸酸根离子的热分解半衰期受温度影响大,升高温度,引发剂热分解半衰期缩短,反应速度快,转化率提高。更为关键的是有机硅的水解、缩和反应对温度敏感,随着温度的升高,有机硅水解生成的醇羟基缩合导致凝聚物析出,同时,温度过高(大于85℃),反应过于激烈,聚合反应产生的热量无法及时排出,会出现“飞温”现象,乳液易失稳,导致凝聚物的析出。综合考虑,温度在80℃左右时反应体系稳定,凝聚率小于0.5%,可制备粒径较小的纳米乳液。
3.3. 搅拌强度对反应稳定性的影响
由图1可看出,在乳液聚合时,搅拌对乳液反应过程的稳定性起重要的作用。因此,根据乳液聚合体系的特点,结合搅拌器形式及搅拌强度的影响,实验确定乳液聚合过程中搅拌器的转速。结果表明当搅拌速率大于600 rpm时,易于产生大量的泡沫,从而导致聚合反应失稳。当搅拌速率低于150 rpm时,聚合反应后期易于产生大量的粗粒子,有大块凝胶出现。本实验搅拌器的转速大致在200 rpm为最佳,但乳液聚合不同阶段的搅拌速度在此值上下波动,前期的搅拌速度高于200 rpm,加快单体的分散,而后期应低于200 rpm,防止乳液因搅拌剪切而失稳,导致凝聚物的析出,从而提高乳液聚合产品的产率和质量。
3.4. 乳化剂用量对反应稳定性的影响
由表3可知,随着乳化剂用量的增加,乳液聚合时产生的凝聚物减少,聚合稳定性提高,但是,随着乳化剂用量的升高,乳液胶膜耐水性变差,影响其使用性能,同时也会使生产成本增加,所以,选乳化剂用量3%为佳。
3.5. 引发剂用量对反应稳定性的影响
由表4可知,引发剂用量较低时,产生的凝聚物少,反应不完全,转化率低;而引发剂用量增大时,反应速度过快,容易产生暴聚,导致凝聚物的析出。引发剂用量为0.3%,反应的转化率较高且聚合体系凝聚物少,反应体系较为稳定。
3.6. pH值对反应稳定性的影响
在酸性条件下有机硅易发生水解、缩合反应,因此反应体系的pH值对体系聚合稳定性影响显著,结果如表5所示。
从表5看出,为抑制有机硅的水解、缩合反应,体系的pH值应控制在5.8~6.6为宜。实验表明当反应体系中加入一定量NaHCO3时,反应过程中体系的pH可以维持在5.8~6.6之间。
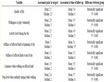
Table 2. The effects of reaction temperatures on reaction stability
表2. 温度对反应稳定性的影响
注:搅拌速率 = 200 rpm,m(A151) = 4%,m(HEMA) = m(MAA) = 2%,m(S) = 3%,m(I) = 0.3%,初始pH = 7
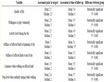
Table 3. The effects of emulsifier contents on reaction stability
表3. 乳化剂用量对反应稳定性的影响
注:搅拌速率 = 200 rpm,m(A151) = 4%,m(HEMA0 = m(MAA) = 2%,T = 80℃,m(I) = 0.3%,初始pH = 7
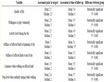
Table 4. The effects of initiator contents on stability
表4. 引发剂的量对反应稳定性的影响
注:搅拌速率 = 200 rpm,m(A151) = 4%,m(HEMA) = m(MAA) = 2%,T = 80℃,m(S) = 3%,初始pH = 7
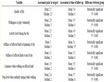
Table 5. The effects of pH on reaction stability
表5. pH值对反应稳定性的影响
注:搅拌速率 = 200 rpm,m(A151) = 4%,m(HEMA0 = m(MAA) = 2%,T = 80℃,m(I) = 0.3%,m(S) = 3%
m(A151) = 4%,m(HEMA) = m(MAA) = 2%,T = 80℃,m(S) = 3%,m(I) = 0.3%,初始pH = 7
Figure 1. The effects of stirring speeds on reaction stability
图1. 搅拌速度对聚合反应稳定性的影响
3.7. HEMA用量对反应稳定性的影响
甲基丙烯酸羟基乙基酯(HEMA)为含-OH基的官能单体,在聚合反应中提供接枝的-OH,可有效的改善乳液耐水和附着性能,选择合适的官能性单体的用量,可获得性能优良的共聚物乳液。
由表6可见,聚合反应体系中不加HEMA,合成的乳液为乳白色,粒径较大;HEMA用量加大,交联现象出现,乳液体系不稳定程度增加。当其用量增至一定程度时,乳液中出现大量凝聚物,甚至无法搅拌。当HEMA用量为2%时,凝聚率最小为0.281%,反应过程稳定,乳液呈现蓝色乳光,乳液粒径小。
3.8. MAA用量对反应稳定性的影响
由表7可知,随着MAA用量的增加,乳液逐渐由乳白色变成呈现蓝色乳光,说明乳液颗粒的平均粒径变小。聚合体系中的羧酸单体以形成共聚物为主,这是因为MAA在MMA与BA中的分配系数较大的缘故。水溶性单体用量增大,不可避免生成部分粒径较小的无核新粒子,导致乳液的平均粒径变小,粒径分布变宽。此外,当MAA的用量增大时,体系的酸度增大,有机硅的水解、缩合反应程度加剧,导致聚合物乳液中的凝聚物含量增加;另外羧基含量增大时,乳液粒子表面上的羧基相互间作用加强,使得乳液的粘度增大。所以,MAA的用量以2%~3%为宜。
3.9. 有机硅用量对反应稳定性的影响
由表8可知,随着A151用量的增加,硅氧烷基发生水解和缩合反应的程度加强,乳液聚合物的支链化程度和相对分子质量也迅速增加,导致乳胶粒径增大;体系原有的乳化剂不能起到稳定作用,凝胶率增加,聚合稳定性降低,甚至出现胶凝现象。
4. 结论
1) 采用单体半连续滴加工艺,当温度在80℃~85℃,引发剂、复合乳化剂、有机硅A-151、HEMA以及MAA的质量百分含量分别为0.5%、4%、4%、2%、2%时,可得到固含量40%、粒径为80 nm左右的乳液,其凝聚率低于0.5%,反应过程稳定。
2) 体系反应温度、pH值、搅拌速率、乳化剂及引发剂用量等是乳液聚合稳定性的关键因素。升高反应温度,反应稳定性降低;搅拌速率及pH过高或过低均不利于乳液聚合过程的稳定,适宜的搅拌速
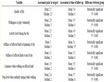
Table 6. The effects of HEMA contents on reaction stability
表6. HEMA用量对反应稳定性的影响
注:搅拌速率 = 200 rpm,m(A151) = 4%,m(MAA) = 2%,T = 80℃,m(S) = 3%,m(I) = 0.3%,初始pH = 7
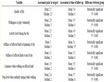
Table 7. The effects of MAA contents on reaction stability
表7. MAA用量对反应稳定性的影响
注:搅拌速率 = 200 rpm,m(A151) = 4%,m(HEMA) = 2%,T = 80℃,m(S) = 3%,m(I) = 0.3%,初始pH = 7
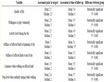
Table 8. The effects of A151 contents on reaction stability
表8. A151用量对反应稳定性的影响
注:搅拌速率 = 200 rpm,m(HEMA) = m(MAA) = 2%,T = 80℃,m(S) = 3%,m(I) = 0.3%,初始pH = 7
率为200 rpm,合适的pH范围为5.8~6.6;乳化剂增加有利于乳液稳定,而引发剂含量高则对乳液聚合过程的稳定不利。
3) 有机硅单体是影响乳液稳定的最重要因素。随A151用量增加,乳液的稳定性降低,当其含量超过6%时,凝聚率迅速增加,聚合稳定性快速下降。