1. 引言
随着我国铁路事业的发展,列车的运行速度不断提高,对其中各零部件的质量提出了更高的要求。轮对和联轴节作为列车的关键部件,不仅有使列车在轨运行和转向的作用,同时能承受列车的静、动载荷,并完成卸荷实现列车平稳运行。因此,对轮对的日常检查是非常重要的 [1] 。
轮对和联轴节的主要故障有裂纹、磨伤、车轴弯曲和车轮的踏面磨耗等,其中磨伤主要指车轴、轮毂、防尘板座上的纵、横向划痕、凹痕等。而划痕是产生应力集中,造成车轴裂纹的主要原因。因此,对轮对的划痕及时而准确的测量,淘汰不合格的轮对,对保证列车安全、可靠的运行具有重要意义 [2] - [4] 。
轮对的和联轴节检测方法主要有接触式测量方法和非接触式测量方法 [5] [6] 。接触式测量是探头与被测表面直接接触,通过探头的移动将被测表面的情况通过位移变化量的形式进行反馈。非接触式测量是以光、电、电磁等技术为基础,在不接触物体表面的情况下,得到物体表面参数信息的测量方法。非接触测量虽然具有自动化程度高、反应快、数据率高等优点,但其在使用时对操作人员的技术水平要求较高、测量精度受到所配置PSD (Position Sensitive Detector)元器件性能的限制、对被测表面的光洁平整度也有一定的要求。因此,同一款非接触测量仪不能满足广泛适用性的要求。且受划痕测量空间和被测表面形状的限制,目前没有合适的非接触测量设备,对轮对划痕进行测量,仍主要依靠人工检测的方式进行测量,测量误差率较大。
本文将介绍一款新型动车轮对及联轴节轴孔划痕测量仪,不仅集成了机械接触式测量方法定位可靠、反应真实的特点,而且融入了CCD (Charge Coupled Device)技术和数字处理技术反应快、数据率高的优点。
2. 划痕测量仪的测量原理
2.1. 测量要求
测量对象:联轴节轮毂内锥孔、轮轴外圆锥表面、轮对轴、孔圆柱表面划痕深度。
测量技术要求:如表1所示,给出了零件的结构参数与划痕的测量参数及要求。
工件结构特征:材料为钢或合金钢,表面粗糙度Ra0.4~Ra0.8;最小孔为圆锥孔,锥度1:50,大端直径Φ68 mm,深度75 mm;圆柱轴直径范围Φ60~Φ200 mm,圆锥轴锥度1:50,大端直径Φ68 mm。
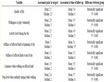
Table 1. Nick measurement technology index
表1. 划痕测量技术指标
划痕特征:工件材料为钢,划痕为细长轻微形状,方向不定,划痕截面宽度最小值0.04 mm,深度最小值0.01 mm。
作业环境与作业模式:在生产现场作业,人工手提测量仪,现场安装测量,并直接给出测量结果。
自动化程度:手动测量。
2.2. 测量工艺分析及工艺方案确定
测量工艺方法选择:测量方法的选择,不仅取决于被测工件的材料、划痕的形状、尺度及测量精度特征,还取决于工件形状、测量作业环境和作业模式。
特征分析
测量基准与定位方式确定
工件结构特征表明,最小圆锥孔的测量空间狭小,考虑到测量仪的定位装置还需要占据一定空间,传感器结构尺寸受到限制严格限制,因此需要首先设计定位装置,原则是在保证定位精度及操作要求前提下,尽可能减少体积和占据的空间,为传感器的选择和设计提供准确空间尺寸参数。
测量方式类型选择
综合考虑各种传感器的测量精度、测量尺度、结构尺寸、抗干扰能力、使用条件和成本等因素,进行各项指标对比,均需满足特征要求。分析以上各个方面的因素,传感器的精度与结构尺寸限制较为严格,因此选择测量方式主要从这两项指标考虑。
非接触式测量可选的传感器类型:
激光测距激光测距(脉冲法、相位法、三角法和干涉法)、超声波、电磁感应、电容测距、CCD传感器等。以上传感器结构尺寸过大,测量空间容纳不下,因此均被排除(特殊的能满足结构尺寸和测量精度传感器成本太高)。
接触式测量可选的传感器:由于接触式测量方法是由测头直接接触被测量表面,只要求测头触点半径小于被测划痕最小曲率半径,即可实现测量,因此传感器选择只需要考虑其结构尺寸、测量精度、抗干扰能力和成本即可。
基于以上要求,国内外现有的技术和产品均能实现,因此确定选择这种测量方式。
接触式测量尚需要解决的问题:1. 为了保证探针能够接触到划痕底部,接触式测量探针针尖圆弧半径要小于划痕最小曲率半径;2. 为了保证找到最低点,在观察无法判断的情况下,需要多点测量比较的方法求取深度最大值得到;3. 由于划痕过于微细,人眼无法分辨划痕较深位置,也难于清晰判断探针是否测量到划痕底部,需要通过放大图像观察判断,实现可视化定位;4. 为了保证探针达到划痕底部,手动调节的位移分辨尺度必须小于划痕的尺度(微米级),需要具有微位移调整功能实现手动精细调整。
测量操作工艺方案
综合以上因素,确定测量工艺方案:采用接触式测量仪,依靠可视化方法实现探针对划痕的准确定位,手动测量方法,利用多点测量并通过对测量值比较求取最大值方法达到测量目的。
3. 测量仪研发
3.1. 测量仪组成
划痕测量仪用于测量轴外锥面和轮毂的内锥孔,被测件如图1所示。
3.2. 测量仪工作原理与结构
工作原理:CCD摄像头采集视觉信息经处理后显示在图像显示屏上,人工观察探针的位置,手动调节仪器位置使对正测量部位,位移传感器测量探针的位移,经信号传输、信号采集、A/D转换、数据处理,输出到显示屏或存储。仪器采用接触式测量方法,选择精密位移传感器(英国基恩斯),由探针直接接触测量表面,测量圆锥表面的位移值,将基准表面的测量值作为标定值,测量并求取划痕的深度差,即得到划痕的实际深度。为了准确将探针置于划痕的测量位置,利用摄像头经过放大3倍的镜头,通过显示屏可观察划痕和探针的测量位置,达到可视化测量的效果,从而实现可视化手动测量的目的。
精度指标:联轴节内外圆锥表面划痕测量仪和梯形槽侧面划痕测量仪采用英国基恩斯AML/EU-±0.5 mm—S2型位移传感器,其分辨率0.001 mm,非线性度小于0.5%,重复精度小于0.001 mm。
划痕测量仪组成,如图2所示,各部分功能见表2。
组成:如图2所示,测量仪由联轴节轮毂与车轴圆锥表面测量附件、测量装置和配电箱组成。测量附件安装在测量装置上,其功能是将测量装置定位并安装到轮毂或车轴圆锥表面;测量装置实施测量;电控箱内装有供电、控制元器件,其表面安装有数据显示屏和图像显示屏,提供可视化测量截面,同时显示测量结果。
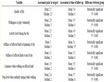
Table 2. Nick measuring instrument parts function
表2. 划痕测量仪各部分功能
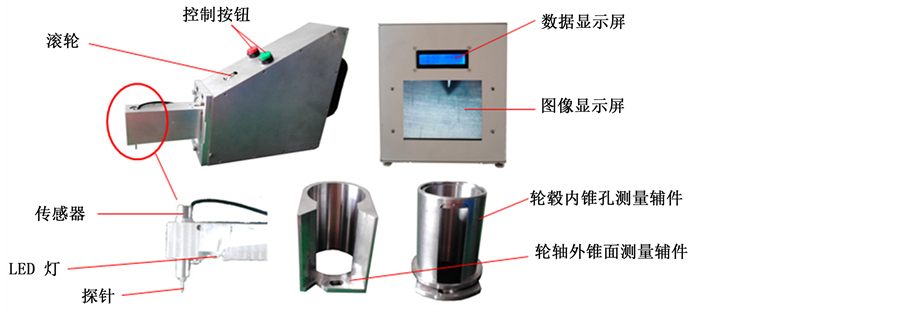
Figure 2. The scratch of measuring instrument
图2. 划痕测量仪组成
测量附件原理结构
测量附件分为轮毂测量附件和车轴测量附件。附件通过定位止口定位,通过三个螺钉固定安装到测量装置上。轮毂测量附件:如图3所示,由两部分组成,即与轮毂内锥孔定位的定位套(定位元件)和安装于测量附件的支撑套组成。定位套将圆锥面转化为圆柱面,即可以利用两套之间的孔轴配合,既可实现定位,又能使测量装置相对测量表面实现轴向移动和转动。
车轴测量附件
如图4所示,附件作为定位元件,其端面与测量装置由定位止口定位通过螺钉安装在测量装置上,由此保证测量装置的探针与附件的位置精度。附件上具有与定位端面垂直布置的V形槽作为与车轴圆锥表面的定位基准。
测量装置原理结构
测量装置如图5所示,由测量头与操控盒组成。测量头由位移传感器和安装其上的探针组成;工作时探针接触被测表面,接触力由压缩弹簧施加恒定力;探针提起由拨轮绳索牵引手动完成。测量时,分为基准测量和划痕测量,差值为划痕深度值,可以通过显示屏读取。摄像头与水平30度安装,焦距中心在探针头部附近,用以采集视频信号,供显示屏输出。
测量仪与工件安装结构如图6所示,图6(a)为测量仪安装到被测轴上图片,图6(b)为测量仪安装到轮毂上图片。
3.3. 划痕测量仪的特点
3.3.1. 测量精度
划痕测量仪的测量精度主要由以下两方面进行保证:
(1)测量仪定位精度
轮对的车轴外表面和轮毂内表面均是具有一定锥度的锥面,而划痕测量仪的测量辅件在设计时也预留了与之配合的锥度,且经过精密的磨削处理。因此当进行测量时,测量辅件将与被测面形成精密的机械配合,实现被测面与操作箱体的完全定位,从而排除操作人员因抖动带来的测量误差。
(2)探针单点接触式测量
探针经过精密的磨削处理,使探针端部极其尖锐,从而使探针与被测件之间形成单点接触,保证测量值反应被测点的值,而不是探针接触点所在区域的测量值;又因为探针与被测件之间直接接触,所以能真实、准确的反应被测量的信息,而不受外部环境因素的影响。
(a) (b)
Figure 6. Fixture and measuring devices
图6. 夹具与测量装置图
3.3.2. 测量点定位
当启动划痕测量仪时,CCD摄像头将把探针与被测面的画面,放大3倍地显示在图像显示屏上,可方便操作人员实时把握探针与被测表面的位置状态。只有当探针对准被测点时,才放下探针与被测面接触,这样就避免了以往探针一直与被测面接触,探针滑动时磨损过快,造成测量不准确的弊端。
3.3.3. 操作方便
(1)当需要测量时,只需拨动操作箱体上的滚轮,带动探针上下移动,即可实现测量。
(2)测量车轴外锥面和轮毂内锥孔时,只需更换操作箱体头部的测量辅件,且更换极为方便。其中,轮毂内锥孔的安装拆卸过程,如图7所示。首先,旋松操作箱体上的测量辅件更换螺钉;其次,将螺钉头部从测量辅件固定孔的大端穿过;再次,旋转测量辅件使螺钉头部与测量辅件固定孔的小端配合;最后,拧紧螺钉。当需要更换时,只需旋松螺钉,执行相反的操作即可。
3.3.4. 读值方便
当进行测量时,PLC将保存记录在基准里的数值,以后每次测量均以它为基准,进行代数运算,并将基准值、实时测量值和它们之间的差值直接反应在一块数字显示屏上,方便操作人员观察和做出判断。当需要重新选定基准时,只需配合控制按钮的操作即可完成。
4. 结论
依据动车轮对及联轴节轴孔划痕特征,进行了测量工艺的研究,提出了可视化接触式测量的工艺方案。
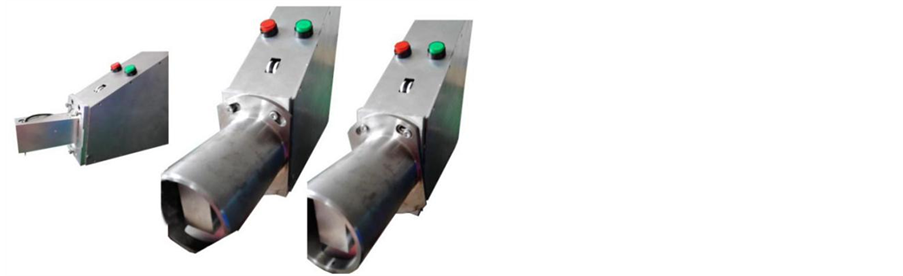
Figure 7. Auxiliary measuring parts replacement process
图7. 测量辅件更换过程
研发了一款新型适于动车轮对及联轴节轴、孔表面划痕测量的测量仪;介绍了测量仪的工作原理与基本组成;并对其精度与可靠性进行了理论分析。
制作了功能样机和适于轴、孔定位的夹具,并对实际工件进行了测量试验,证明了样机原理方案的可行性,结构方案的合理性与可行性。
本文研发的动车轮对划痕测量仪,不仅具有接触式测量定位准确、测量精度高的特点;同时具有非接触式测量图像处理、数据分析处理的反应快、数据率高的特点。经实际测量验证,该划痕测量仪可达到微米级的测量精度,完全满足动车轮对划痕的测量精度要求。