1. 引言
Mg-Gd-Y系列合金由于具有优异的室温及高温性能而在航空航天工业中具有广阔的应用前景 [1] - [3] 。该合金是典型的时效强化型合金,时效强化是其主要的强化机制,前期研究表明 [4] - [8] ,该系合金的时效析出序列通常为:s.s.s.s→β→β'→β1→β。β相在时效初期形成,其晶体结构为DO19,晶格常数为:
,
,由于其与基体完全共格,强化效果较弱。随着时效时间的延长,将形成β'相,该相为底心正交结构(bco),其晶格常数为:
,
,
,与基体呈半共格关系,能够有效阻碍位错的滑移,是该
合金的主要强化相,常常存在于峰时效状态的样品中,随着时效时间的进一步延长,β'相将逐步演变为β1相,β1相与基体不共格,对位错的阻碍作用降低,同时开始出现合金硬度和强度的下降。最后,该相演变为平衡相β,标志着合金完全进入过时效状态,强度和硬度进一步下降。近年来的研究也表明 [9] ,在一些合金中,并未观察到过渡相β1的存在,而是直接由亚稳相β'演变为平衡相β。由合金析出相演变规律及合金的强化机制可以看出,为获得高强度的Mg-Gd-Y合金材料,形成高体积分数的β'相是可能的途径。但是,研究表明 [10] [11] ,Mg-Gd-Y合金在塑性变形过程中,通常容易发生动态析出,直接形成平衡相β,降低基体中溶质原子的浓度,从而降低时效时形成的β'相的体积分数以及合金的时效强化效果。因此,在时效之前,可参考铝合金的处理方式,进行固溶处理 [12] [13] ,将析出的平衡相β重新溶入基体,但需要注意的是,镁合金晶界迁移容易,在高温固溶时容易发生晶粒长大,从而降低晶界强化效果及晶粒之间变形的协调性。针对这一难题,本文研究了固溶温度及时间对Mg-Gd-Y合金挤压板材组织与织构演变的影响规律,研究结果可为高性能镁合金制备提供参考。
2. 实验
本文所用实验材料为Mg-8Gd-4Y-Nd-Zr合金挤压板。锭坯采用差压铸造的方式进行制备,尺寸为Φ 250 × 500 mm,挤压前,铸锭预热温度为
400 ℃
,挤压时挤压杆的移动速度为1 mm/s,挤压比为11.3。采用电火花线切割机从挤压板上切取尺寸为15 × 15 × 3 mm的样品进行固溶,固溶处理在电阻加热炉内进行,固溶处理过程中采用氩气进行保护以减少合金的氧化,固溶温度分别为
450 ℃
、
475 ℃
、
500 ℃
和
520 ℃
。用于金相组织观察及扫描电镜观察的样品采用机械预磨及抛光的方式制备,腐蚀液采用4 vol.%硝酸酒精溶液,市购硝酸的纯度为65%,腐蚀采用浸蚀的方式,腐蚀时间为20~30 s,合金晶粒尺寸的测试采用截线法进行。挤压态及固溶处理后样品中第二相粒子的观察在Quanta 200型扫描电镜上进行,并采用能谱仪对第二相的化学成分进行分析。织构测试在荷兰帕纳科高分辨衍射仪X’pert Pro MRD内进行,织构测试样品的尺寸为18 × 15 × 3 mm,测试面为ED (Rolling direction,轧向)-TD (Transverse direction,横向)面,测试前,为去掉表面应力层,试样表面采用浓度为4%的硝酸酒精混合溶液进行腐蚀,腐蚀时间大约为25~30 s。
3. 结果与讨论
3.1. 挤压态显微组织
图1所示为挤压板材的金相显微组织。从图中可以看出,挤压板的晶粒组织非常细小,其平均晶粒尺寸为3.2 μm。除此之外,在合金中还可观察到大量弥散分布的细小黑色的第二相粒子,该类黑色第二相粒子在扫描电镜下为白色,如图2所示。由图可知,合金中主要有三种类型的第二相粒子:细小且形状不规则的第二相粒子(粒子A)、方块状第二相粒子(粒子B)和团聚成块状的第二相粒子(粒子C)。其中,体积分数最高的是尺寸较细小、形状不规则的第二相粒子,能谱分析表明,该粒子中Gd元素含量为13.42 wt.%,Y元素含量为6.41 wt.%,Nd元素含量为4.21 wt.%。对第二类方块状粒子的分析表明,Gd元素含量为42.83 wt.%,Y元素含量为45.32 wt.%,Nd元素含量为3.29 wt.%。此外,对团聚块状粒子的能谱分析表明,Gd元素含量为34.81 wt.%,Y元素含量为44.95 wt.%,Nd元素含量为2.35 wt.%。由上述分析结果可知,三类第二相粒子中均富含稀土元素。对比几种类型粒子的能谱分析结果,可知方块状粒子和团聚的块状粒子中Gd、Y元素的含量更高,远远超过Nd元素的含量,也超过细小不规则第二相粒子中Gd元素及Y元素的含量。结合其它研究成果可知 [11] [14] ,细小且形状不规则的第二相粒子为挤压过程中动态析出的平衡相β,方块状粒子则为铸锭均匀化处理后残留的富稀土粒子,团聚的块状粒子与此相似,可能是均匀化处理后团聚的富稀土粒子在挤压过程中被破碎,从而团聚在挤压板材中。
3.2. 固溶过程中的组织演变
上述分析表明,合金在挤压过程中形成了大量的析出相,消耗了基体中的溶质原子,降低了基体中的过饱和固溶度,将降低合金在时效过程中产生的时效析出相的体积分数,降低合金的时效强化效果。另外,合金挤压过程中形成的平衡相,由于尺寸为微米级,强化效果有限,且该相还可能引起应力集中,成为裂纹源。因此,须通过固溶处理,将动态析出的第二相溶入基体,再在时效过程中析出,增加时效强化效果,使合金具有更高的强度。
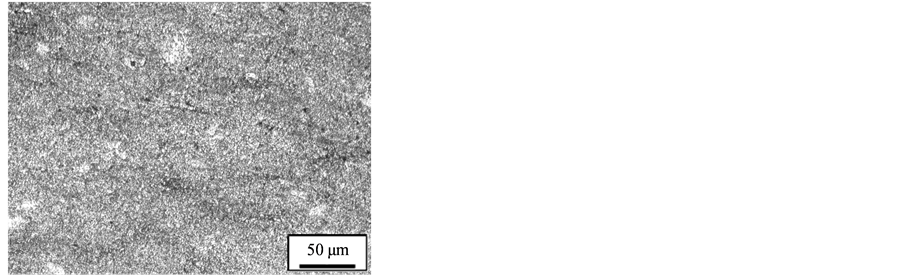
Figure 1. Optical microstructure of the extruded plate
图1. 挤压板材金相显微组织
(a)(b)
(c) (d)
Figure 2. SEM image and EDS results of the extruded plate: (a) SEM image, (b) EDS results of particle A, (c) EDS results of particle B, (d) EDS results of particle C
图2. 挤压板材的扫描电镜组织及能谱分析结果:(a) SEM照片,(b) A点能谱,(c) B点能谱,(d) C点能谱
本文研究了合金在
450 ℃
、
475 ℃
、
500 ℃
和
520 ℃
条件下固溶处理过程中的微观组织演变,在上述温度下固溶不同时间的金相显微组织如图3所示,由图可知,当合金在
450 ℃
条件下固溶时,合金中晶粒的长大速度非常缓慢,经
450 ℃
/4h固溶后,合金的晶粒尺寸为9.6 μm,仅较挤压态合金的晶粒尺寸增加6.4 μm,当在
475 ℃
条件下固溶时,合金中晶粒长大速度稍快,但仍维持在较低的水平。但是,当在
500 ℃
及更高的条件下进行固溶时,合金的晶粒尺寸迅速增长,经
520 ℃
/0.5 h固溶后,合金的晶粒尺寸即长大到34.1 μm。从固溶处理后合金的扫描电镜照片(图4)可以看出,当在
450 ℃
及
475 ℃
条件下固溶0.5 h后,合金中仍然有大量动态析出的第二相粒子,但当合金在
500 ℃
条件下固溶0.5 h后,合金中的第二相粒子迅速减少;当温度升高到
520 ℃
后,仅固溶半小时后,合金中的第二相粒子均已溶入基体,仅残留下少量均匀化处理后剩下的富稀土粒子,该粒子在均匀化处理过程中形成,熔点较高,难以在固溶温度下溶入基体。
挤压过程中析出的第二相粒子,在固溶处理过程中对晶界迁移有显著的阻碍作用,当在
450 ℃
和
475 ℃
条件下固溶时,晶界上动态析出的第二相粒子溶解进入基体的速度较慢,还能有效阻碍晶粒的长大,当固溶温度升高到
500 ℃
及更高的温度时,第二相粒子溶入基体的速度大大增加,从而也失去了对晶界迁移的阻碍作用,导致合金中的晶粒迅速长大。
(a)(b)
(c) (d)
Figure 4. SEM images of the extruded plate after solution treatment: (a) 450˚C/0.5h; (b) 475˚C/0.5h; (c) 500˚C/ 0.5h; (d) 520˚C/0.5h
图4. 挤压板材固溶处理后的扫描电镜照片:(a) 450˚C/0.5h;(b) 475˚C/0.5h;(c) 500˚C/0.5h;(d) 520˚C/0.5h
3.3. 固溶过程中的织构演变
为进一步分析合金固溶处理过程中的组织结构演变,本文对挤压态样品及固溶处理后的样品进行了织构分析,其结果如图5所示。由图可知,合金挤压态的织构主要由两种织构组分构成,即基面平行于挤压板面的基面织构和基面垂直于板材横向的棱柱面织构组态。经过
475 ℃
/0.5h固溶处理后,基面织构的极密度由挤压态的4.96降低为4.59,棱柱面织构的极密度则有所增强;经过
520 ℃
/0.5h固溶处理后,合金中的主要织构组态则由以基面织构为主变为以棱柱面织构为主。亦即,随着固溶过程的进行,合金中基面织构的强度减弱,而棱柱面织构的强度上升,可能是由于棱柱面织构组分在固溶过程中择优生长造成。
4. 结论
通过研究挤压板材在固溶处理过程中合金微观组织与织构的演变规律,得到了如下结论:
1) 挤压板材固溶处理过程中,晶粒长大和动态析出相的溶解同时进行,固溶温度低于
500 ℃
时,晶粒长大速度较慢,固溶温度高于
500 ℃
时,晶粒长大速度显著提高,其原因在于高温固溶时动态析出相迅速溶入基体,降低了对合金晶粒长大的阻碍作用,导致晶粒长大速度快速增长。
2) 挤压板材中基面织构是主要的织构组态,经固溶处理后,基面织构强度降低,棱柱面织构增加,主要归因于该类晶粒的择优生长。
基金项目
湖南省自然科学基金(2016JJ5042)。