1. 引言
随着现代粉末冶金技术的发展和相关新兴产品的产业化,高性能的合金粉末被越来越广泛地应用于金属注射成形、热喷涂、电子表面贴装等领域 [1] ,这就要求金属粉末必须向着具备微细、高纯度、球形度高、粉末粒度可控、低成本等方面发展 [2] 。当代材料科学和工程技术研究领域高度关注粉末冶金技术的研究和发展。
雾化法制备粉末适用于多种金属及合金粉末,是制备金属粉末最主要的方法,据统计,当今世界粉末总量的80%是雾化法生产的,其中30%~50%是气雾法制取的 [3] 。气雾法的过程是用高速气流冲击金属或合金液体,使其破碎成小液滴,随后冷却冷凝成粉末 [3] 。其关键技术是设计合理的气体喷嘴结构,研究气体和金属液体的耦合作用,使气流的动能更充分地作用于液体表面,以提高雾化效率和金属粉末的质量。
国内外学者对雾化器进行了大量的研究,开发了多种新型雾化器结构 [4] ,如层流雾化技术、超声紧耦合雾化技术、热气体雾化技术等 [5] 。主要分为限制式和非限制式。非限制式的雾化器工作时,金属或合金溶液从漏包流出后靠重力自由下落到雾化介质相遇点 [6] ,制取高质量的微细金属粉末是现阶段雾化工艺的主要目标和发展方向,对于某种旋涡环缝式雾化器,现有技术和实际生产需要之间形成了一定的差距, 因此本文基于此种结构的雾化器,计算模拟了气流流动过程,总结其内部流动和环缝出口射流的流动特点,可以为提高该雾化器雾化性能提供依据。
2. 计算模型和方法
本文采用某种典型结构的旋涡环缝式雾化器,其结构透视图如图1所示,内部气流管道用红色高亮显示,从图1截面A处切割雾化器模型,得到截面图如图2。雾化器由四部分拼合而成,空腔是由上中心锥体和下中心锥体组成。雾化器工作状态时,气流的大致流动过程为:气体从两个直管道入口流入雾化器,先后流经一个圆环形管道,四个相对于空腔对称切向布置的斜管道,进入由上下中心椎体构成的环形空腔,在空腔的收缩段被压缩,最后从环状缝隙喷嘴高速喷出。当有高温金属溶液从引流管流出,立即被从喷嘴喷出的高速射流冲击雾化成粉末。雾化器的环状出口缝隙为0.4 mm,气体出口的喷射顶角为30°,入口直管道直径12 mm,流经斜管道直径10 mm。
模型截面A处的网格如图3所示,计算域选择圆柱形,计算域上边界距离模型的环缝喷口上方31 mm,下边界距离模型的环缝喷口下方62 mm,计算域的底面半径为210 mm。气体以25 L/min的总流量从两个直管入口流入雾化器,入口边界条件为质量流量入口,计算域上下边界均为压力出口条件,压强为

Figure 1. Perspective of atomizer structure
图1 雾化器结构透视图
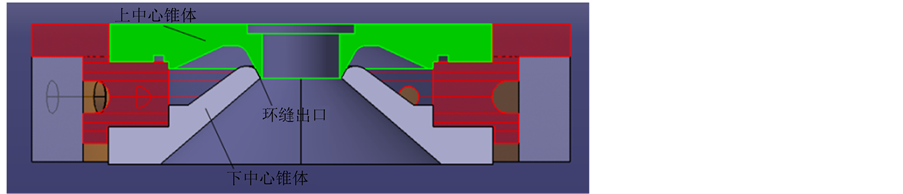
Figure 2. Sectional drawing of section A
图2. 截面A截面图
96,700 Pa,计算域侧面为壁面边界条件。用ICEM软件划分三维非结构网格,网格数量为2,087,361,雾化器内部网格加密,为了研究雾化器喷嘴处的射流特性,因此进一步加密雾化器喷嘴附近的网格。
本文暂不考虑金属溶液的加入,研究只充入气体时,雾化器内外的气流流场特点,模拟只有气体的单相流动,而且暂不考虑热传导作用,温度恒定为300 K。本文用定常方法求解雾化器的气流流场,数值计算采用流体力学软件Fluent。气体采用Fluent数据库的理想气体,由于气体密度较小,质量较轻,求解过程中不考虑气体的重力。方程中压力速度耦合方法采用基于SIMPLE的隐式算法,迭代步数为25,000步,本文选用的湍流模型为k-omega两方程的SST格式,其方程为:
(1)
(2)
其中,
和
分别是k和ω的有效扩散项,
和
分别是由层流速度梯度和ω方程而产生的湍动能,
和
分别是k和ω的发散项,
和
由用户自定义。
3. 数值计算结果与分析
3.1. 内部管路流场
计算三维模型所得结果,截取雾化器内管道剖面,即图1所示剖面B处,此剖面处的内部气流流场流线局部放大图(从下往上视角)如图4所示,截面A处气流流场流线及压强局部放大图如图5所示,压力单位为Pa。对比两幅图,观察气流流动过程。
气流从一个直管入口进入后分两股气流,分别沿着环形管道流入最近的两个斜管道。其中,一股气流几乎全部流入与直管平行的斜管道,另一股气流大部分流入与直管垂直的斜管道,一小部分沿着环形管道继续向下流动,最终与另一个入口的气流一起流入下一个斜管道。另一个入口的气流流动特点相同。管道内局部气流拐弯处有漩涡存在,会产生气流能量损失。直管入口处的气流平均速度约为39.4 m/s,斜管出口将要流入空腔处即图4中C截面处的气流平均速度约为23.6 m/s。随后,斜管道中流出的四股气流都大致从切向汇入环形空腔,由于空腔内壁的约束作用,气流先沿空腔内壁做圆周运动,然后在空腔内做逆时针漩涡流动,内部有少量漩涡,最后气流经过空腔的收缩段逐渐加速从环缝喷嘴加速喷出形成射流。
雾化器是将高压气体的动能转化为金属的表面能的换能装置 [7] ,撞击金属液流的射流动能越大,能
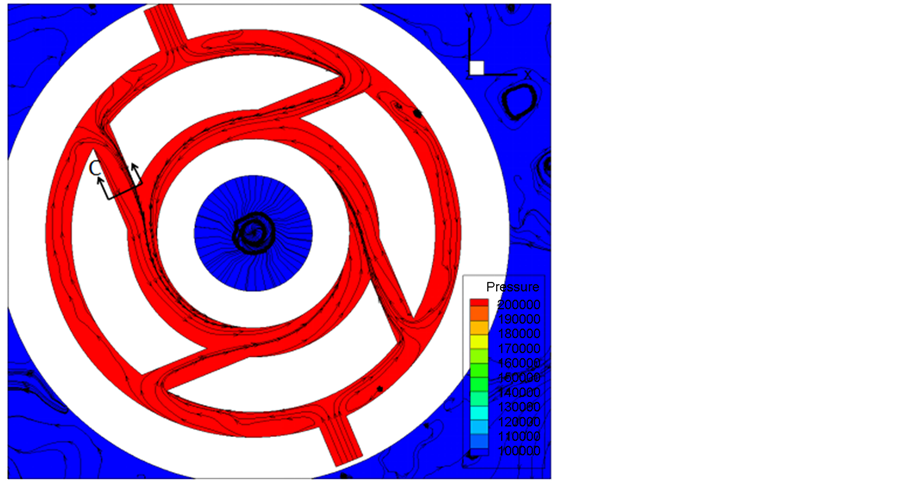
Figure 4. The internal airflow stream at the cross-section of the atomizer
图4. 雾化器内管道剖面处的内部气流流线局部放大图
增加金属液流的破碎程度,雾化后能获得较细的金属粉末 [8] 。所以要尽可能减小气流在雾化器内部流动时的流动损失。内部管道越多,拐弯越急,能量损失越大 [9] 。管道内壁的加工粗糙度越大,摩擦阻力越大。因此,可以在环状管道和斜管道连接处通过加工使之平缓过渡或倒角,来减少气流拐弯时漩涡的产生,从而更充分利用气流的动能,保证雾化效果。雾化器加工时尽量使内管道表面光滑。
3.2. 喷嘴外流场
气流从雾化器环缝喷嘴喷出后,呈一空心的对顶气锥 [10] ,见图6,且存在从下往上看逆时针的旋度,流体介质任意一个微团的运动轨迹是一条空间锥螺旋线,这个旋转强度越高,越有利于雾化 [11] 。在颈缩处存在一个负压区,颈缩区域即为有效雾化区,颈缩处直径为11 mm。取颈缩处的截面,该处射流流场流线图如图7,可以清晰地看到一个逆时针的漩涡。喷嘴处气流流速较大,静压较小,对周围的空气产生
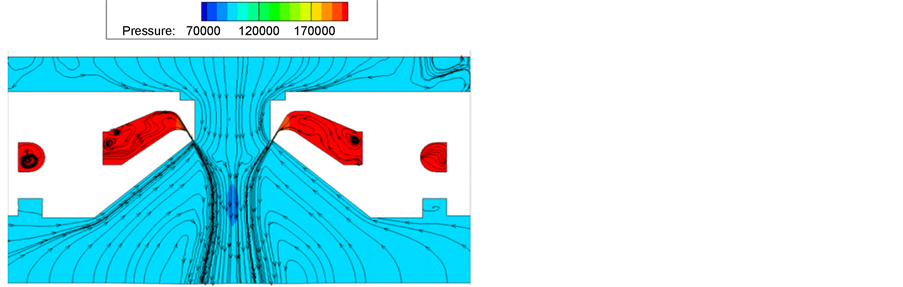
Figure 5. The airflow stream and pressure at section A
图5. 截面A处气流流场流线及压强局部放大图
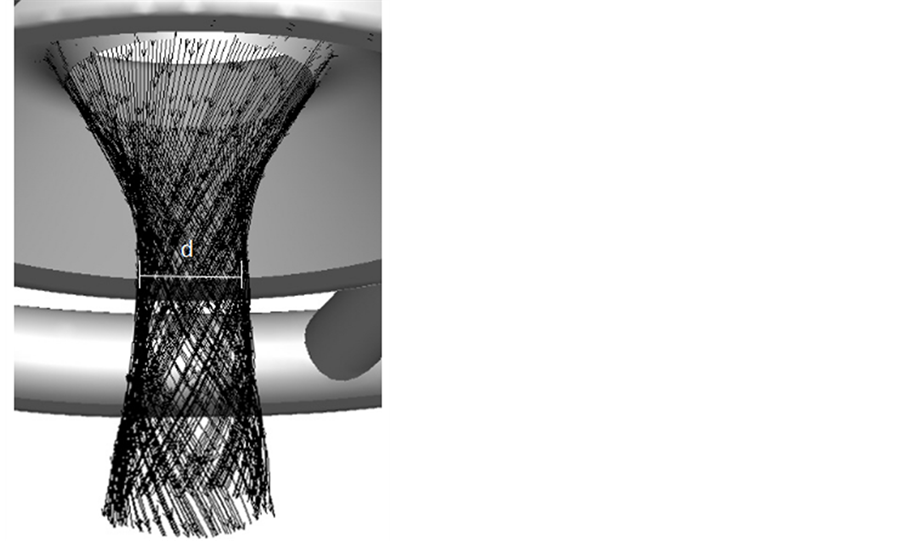
Figure 6. The morphological diagram of the hollow double cone
图6. 空心对顶气锥形态示意图
卷吸作用 [12] ,雾化器上方与下方气流均趋向于与速度高的喷嘴附近的射流汇聚 [13] ,射流微团与周围气流微团进行质量和动量交换,使射流质量和宽度增加,射流速度沿喷射方向逐渐减小,喷嘴处气流最大流速为247 m∙s−1,颈缩处最大流速约为150 m∙s−1,到计算边界出口处射流最大速度约为96 m∙s−1,射流形态呈向周围扩张的流动场 [14] [15] 。
4. 结论
经过对雾化器流场的数值模拟与分析,可以得出如下结论:
1) 气流在雾化器内部的流动存在漩涡,使气流的动能损失,可以通过加工平缓过渡或倒角的方法更充分地利用气流的动能。
2) 气流从雾化器环缝喷嘴喷出后,呈空心的对顶气锥形态,且存在从下往上看逆时针的旋度。
3) 射流流速沿喷射方向逐渐减小,形成向周围扩张的流动场。
通过本文对某型号雾化器流场的计算模拟分析,可以为改进该雾化器雾化性能提供依据。
致谢
这篇论文得以顺利完成,并不是我一个人的努力,离不开我的指导老师的亲切关怀和悉心指导。从研究开始到结束,期间碰到了不少困难,都是指导老师及时给我指明方向,给我鼓励,从中我学到了很多新的知识和看问题的方式方法。
感谢我的朋友、室友、父母给予我的帮助和鼓励,感谢南京航空航天大学给我一个良好的科研环境,谢谢!