1. 试验材料及方法
1.1. 试验材料
本试验采用12 mm厚A6061-T6 (固溶处理 + 人工时效)铝合金板材为试验对象,试验用板材满足JIS H4100相关要求。焊接材料选用直径1.2 mm的ER5356铝镁合金焊丝。A6061-T6铝合金和ER5356焊丝的化学成分如表1所示。
焊接采用半自动焊接设备,操作人员为从事现车焊接焊工,具有相应的资质。焊机型号PHOENIX 421 EXPERT forceArc MIG焊机。保护气体为高纯氩(Ar纯度不小于99.999%)。焊接工艺参数及环境要求按照现车执行,为防止焊接变形,采用刚性固定。焊接工艺参数如表2。
焊后对焊接试板进行外观检查(VT)、渗透探伤(PT)和射线探伤(RT),对检测合格的试板取样进行不同粒度(40目、80目和120目)的焊缝余高打磨。
1.2. 试验方法
打磨完成后对焊接接头分别进行显微组织观察,硬度、拉伸和疲劳试验。微观组织观察参照GBT 3246.2-2000变形铝及铝合金制品组织检验方法进行。硬度试验根据标准GB/T2654-2008/ISO9015:1-2000及HB5173-96,采用HV-30数显维氏硬度计进行试验,载荷30 N,加载时间10 S。拉伸试验根据GB/T228-2010标准,在CMT5305电子万能试验机上进行试验,试验速度为5 mm/min。疲劳试验使用GPS200高频疲劳试验机进行,应力比R = 0,加载频率为85~140 Hz。
2. 试验结果与讨论
2.1. 显微组织分析
6061-T6铝合金焊接接头显微组织如图1,由显微组织可以看出,焊缝为焊接时高温产生铸态组织。
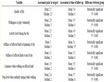
Table 1. Main chemical compositions of A6061 alloy and solder wire ER5356
表1. A6061铝合金、ER5356焊丝主要化学成分(wt%)
表2. 焊接工艺参数
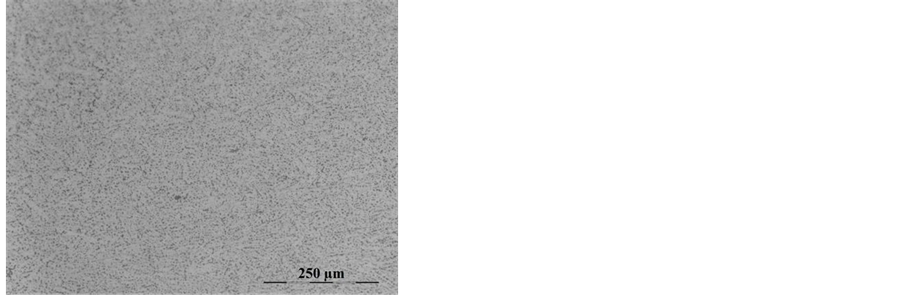
(a) 热影响区 (b) 焊缝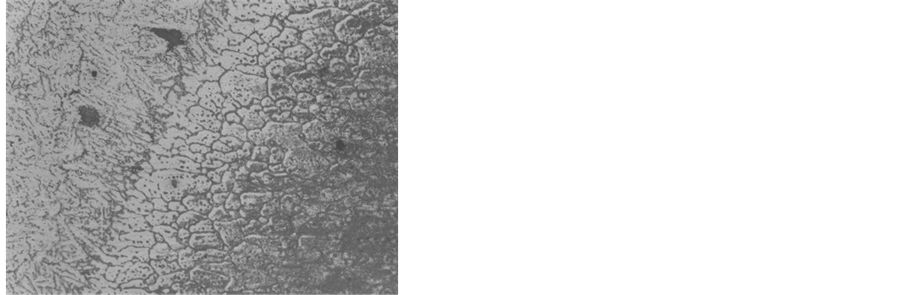
(c) 熔合区 (d) 焊缝
Figure 1. Microstructure of A6061-T6 aluminum alloy butt joint
图1. A6061-T6铝合金对接接头显微组织
在熔合区靠近热影响区一端为粗大的晶粒,靠近焊缝一端晶粒较小。热影响区由淬火区和过时效区(软化区)组成,淬火区的组织主要为过饱和α固溶体,淬火区由于靠近焊缝,受到焊接过程中较高温度热循环的影响,多发生固溶强化,第二相析出物较少;而过时效区(软化区)距离焊缝较远,焊接过程中,受热温度较低,但是又高于铝合金时效温度,处于一种过时效的状态,在这个温度下脱溶相互相聚集,形成稳定的β (Mg2Si)第二相,第二相的析出聚集长大,造成软化区的性能有所下降 [1] [2] [3] 。
2.2. 硬度试验分析
6061铝合金对接接头硬度曲线如图2所示。从硬度曲线上可以看出三条焊缝硬度曲线相差不大。走势也很相近。焊缝硬度值较高,硬度值大约为60 HV,所有接头硬度随着与焊缝中心距离的增加先上升,再下降,在距离焊缝4~10 mm间存在一明显的软化区,硬度最低,约为40 HV,过了软化区硬度继续上升,直至与母材相同,母材的硬度值低于焊缝,约为53 HV。
2.3. 拉伸性能
表3为A6061-T6铝合金对接接头拉伸试验数据。可看出A6061-T6铝合金12 mm对接接头拉伸断裂位置都在热影响区,进一步印证了软化区是整个焊接接头最薄弱的区域。经不同粒度砂轮打磨后,焊接接头的抗拉强度、屈服强度相差不大,抗拉强度都分布在150~160 MPa之间,屈服强度在125~135 MPa之间,在打磨粒度为80目时取得最优的抗拉强度和屈服强度,分别为159 MPa和127 MPa。打磨粒度为120目时,延伸率略有降低,为9.49%,经40目和80目打磨后的接头的延伸率相差不大。
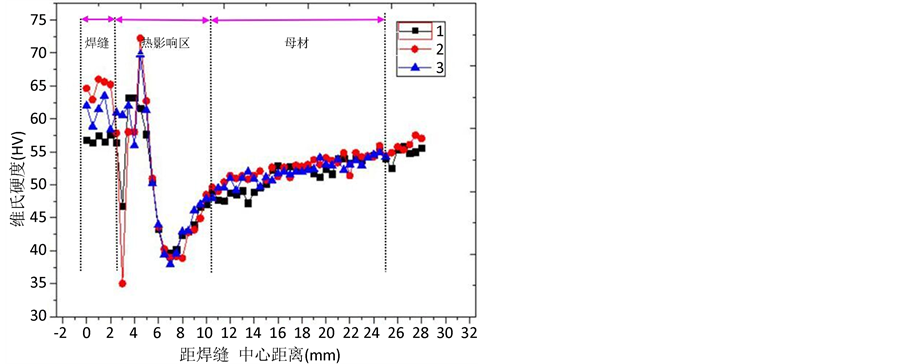
Figure 2. Hardness curve of 12 mm thick A6061-T6 aluminum alloy butt joint
图2. A6061-T6铝合金12 mm对接接头硬度值曲线
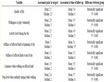
Table 3. Tensile test data of 12 mm thick A6061-T6aluminum alloy butt joint
表3. A6061-T6铝合金12 mm对接接头拉伸试验数据
2.4. 疲劳性能
通过表4和图3我们可以观察到6-120试样的疲劳极限为100 MPa,6-40和6-80试样的疲劳极限为90 MPa。断裂的疲劳试样均断于焊缝处,说明在疲劳试验中焊缝是整个接头最薄弱的区域,这与硬度、拉伸试验得到的结论并不相符,然而通过对疲劳断口的分析可以发现,焊缝由于焊接工艺与过程的影响,存在数量不等的气孔和夹杂等缺陷,这些焊接缺陷往往是疲劳裂纹最容易萌生的区域,因此造成了焊缝在疲劳试验中成为整个接头最薄弱的区域 [4] 。
图4(b)显示断口起裂源在试样表面,可以看出焊缝中存在大量大小不一的气孔,气孔的存在,极易成为再服役过程中发生疲劳断裂的起裂源。从图4中可见,在试件中有较多的气孔,这就可能导致较大的应力集中,加速疲劳裂纹的扩展,加快试件的断裂。(b)是裂纹扩展区的疲劳辉纹,(c)是瞬断区韧窝形貌。
图5是80目打磨12 mm厚A6061-T6铝合金对接接头疲劳断口的形貌。图(a)显示断口的裂纹源位于试件的表面的一处夹渣,这可能是厚板多层多道焊时清渣未彻底造成的。图(b)是裂纹扩展区的疲劳辉纹,辉纹较深,形貌清晰。图(c)是瞬断区韧窝形貌,还能观察到气孔的存在。
图6是120目打磨12 mm厚A6061-T6铝合金对接接头疲劳断口的形貌。断裂面上有明显的疲劳辉纹,这是疲劳裂纹扩展时留下的,并存在二次裂纹。瞬断区断口呈明显的韧窝图样,这说明该疲劳试件在断裂时也是以塑性断裂的方式断裂的,说明该试件在疲劳加载过程中发生了塑性变形。由裂纹源区的疲劳断口可以发现一处聚集分布的气孔,引起疲劳断裂主要原因可能是这些缺陷综合作用的结果。这些缺陷一方面造成应力集中,另一方面造成截面积的减少。多个缺陷的出现增加了裂纹产生的概率,从而引起疲劳强度的下降。
3. 结论
(1) 利用MIG焊可获得焊接质量比较好的6061铝合金焊接接头,拉伸试验结果表明软化区是整个6061铝合金焊接接头最薄弱的区域,因此不同粒度对焊缝余高的打磨未对接头的抗拉强度和屈服强度造成明显影响。
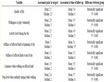
Table 4. Fatigue data of 12 mm thick A6061-T6aluminum alloy butt joint
表4. 12 mm厚A6061-T6铝合金对接接头疲劳数据
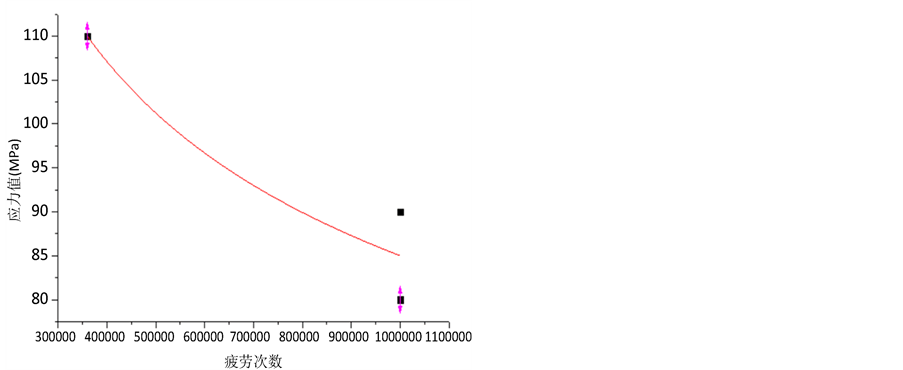
(a) (b)
(c)
Figure 3. Fatigue S-N curves of 12 mm thick A6061-T6 aluminum alloy butt joint after being polished by different particle sizes ((a) 40 mesh, (b) 80 mesh, (c) 120 mesh)
图3. 不同粒度打磨后的12 mm厚A6061-T6铝合金对接接头疲劳S-N曲线((a) 40目,(b) 80目,(c) 120目)
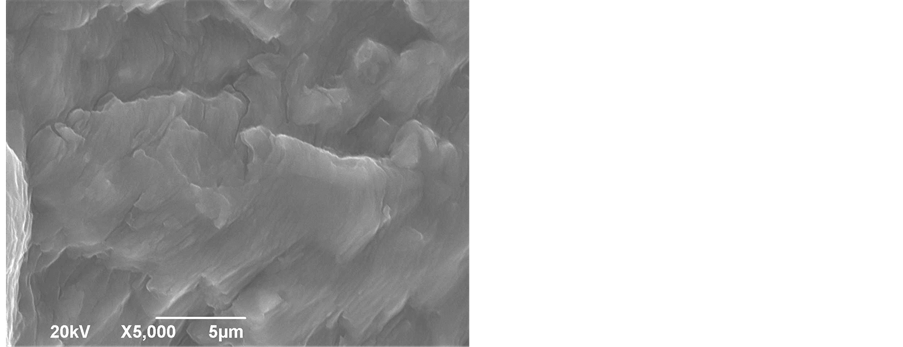
(a) 疲劳源 (b) 裂纹扩展区
(c) 瞬断区
Figure 4. Fatigue S-N curves of 12 mm thick A6061-T6 aluminum alloy butt joint after being polished by different particle sizes ((a) 40 mesh, (b) 80 mesh, (c) 120 mesh)
图4. 不同粒度打磨后的12 mm厚A6061-T6铝合金对接接头疲劳S-N曲线((a) 40目,(b) 80目,(c) 120目)
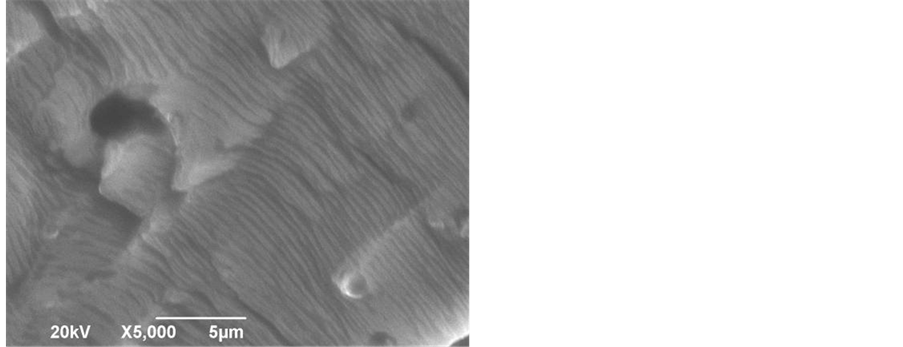
(a) 疲劳源 (b) 裂纹扩展区
(c) 瞬断区
Figure 5. Fatigue fracture of 12 mm thick A6061-T6 aluminum alloy butt joint after being polished by 80 mesh
图5. 经80目砂轮打磨后12 mm厚A6061-T6铝合金对接接头的疲劳断口图
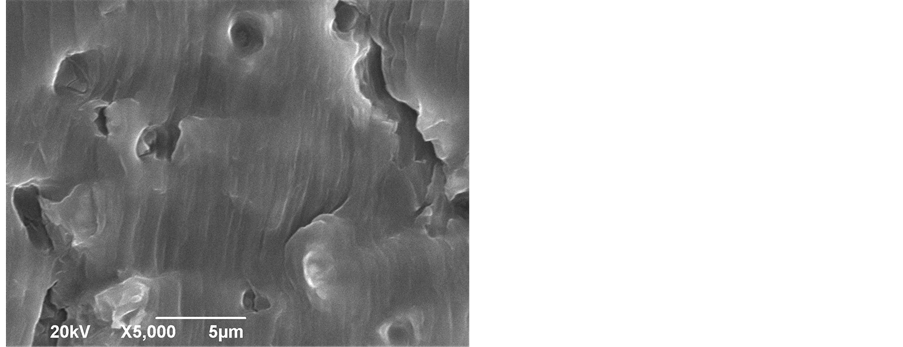
(a) 疲劳源 (b) 裂纹扩展区
(c) 瞬断区
Figure 6. Fatigue fracture of 12 mm thick A6061-T6 aluminum alloy butt joint after being polished by 120 mesh
图6. 经120目砂轮打磨后12 mm厚A6061-T6铝合金对接接头的疲劳断口图
(2) 焊接接头的显微硬度在焊缝处最高,在热影响区中存在一软化区,是整个接头硬度值最低的区域,也是力学性能最差的区域。
(3) 不同打磨粒度下铝合金6061焊接接头的S-N曲线整体变化趋势相同,随着应力幅值的降低其疲劳寿命升高;且随着打磨粒度的增加,焊接接头的疲劳极限有所降低。
(4) 焊接接头疲劳断裂发生在焊缝处,焊接接头的疲劳断口包括三部分,即疲劳裂纹萌生区、疲劳扩展区和瞬断区,并且各个区域有着不同的断口性貌;由于焊缝中组织的不均匀性,且焊缝中存在气孔等缺陷,焊接接头疲劳裂纹易于在此处产生,进而向焊缝处扩展,最终断裂。