1. 引言
7N01铝合金为Al-Zn-Mg可热处理强化型高强铝合金,具有优良的焊接性能、挤压性能等综合性能。因此,7N01铝合金被广泛应用于高速列车生产制造中以满足高速列车轻量化和高速的要求 [1] [2] [3] 。铝合金车体主要采用焊接的加工工艺制造,焊接完成后,焊接接头表面会形成一定的余高,而焊后焊缝余高的存在将影响铝合金焊接接头的使用性能 [4] [5] 。铝合金焊缝打磨主要针对焊缝余高和焊缝接头的打磨,利用良好的打磨工艺除去余高以及焊接残留物,使焊缝具有良好的表面光滑度且具有金属光泽。目前铝合金焊接工艺方面法国、德国、日本等国都做了许多研究。而焊后打磨工艺研究正处于起步阶段,相关方面需要更加深入的研究。
本文针对不同打磨粒度(40目,80目和120目)打磨后的焊接接头进行金相组织观察、硬度试验、拉伸试验和疲劳试验,对打磨粒度对焊接接头疲劳性能的影响进行研究。
2. 试验材料及方法
2.1. 试验材料
本试验采用12 mm厚A7N01P-T4 (淬火 + 自然时效)铝合金板材进行焊接,试验用板材均满足JIS H4100相关要求。焊接材料选用直径1.2 mm的ER5356铝镁合金焊丝。7N01铝合金和ER5356焊丝的化学成分如表1所示。
2.2. 试验方法
铝合金试板采用半自动MIG焊进行焊接,坡口形式为双面V形对接坡口(如图1),焊接参数如表2所示。焊后依次对试板进行渗透探伤和射线探伤。渗透探伤试验方法按EN 571-1:1997《无损检验·渗透检验·第1部分:通用原理》进行,焊接缺欠等级按ISO 10042-B执行;射线探伤按ISO17636:2003《焊缝的无损检测-熔化焊接头的射线检测》进行,焊接缺欠等级按ISO 10042-B执行。焊接试板起弧与收弧处25 mm内的缺陷不计入。探伤后对符合要求的试板分别用40、80、120三种不同粒度砂轮进行焊缝余高打磨。打磨方向与焊缝方向平行,打磨后的纹路与焊缝垂直。打磨后的焊缝与母材等高。
2.3. 测试方法
打磨完成后对焊接接头分别进行显微组织观察,硬度、拉伸和疲劳试验。微观组织观察参照GBT 3246.2-2000变形铝及铝合金制品组织检验方法进行。硬度试验根据标准GB/T2654-2008/ISO9015:1-2000及HB5173-96,采用HV-30数显维氏硬度计进行试验,载荷3 KN,加载时间10 S。拉伸试验根据GB/T228-2010标准,在CMT5305电子万能试验机上进行试验,试验速度5 mm/min。疲劳试验使用GPS200高频疲劳试验机进行,应力比R = 0,加载频率为85~140 Hz。
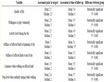
Table 1. Main chemical compositions of A7N01P-T4 alloy and solder wire ER5356
表1. A7N01P-T4铝合金及ER5356焊丝主要化学成分(wt%)
表2. 焊接工艺参数
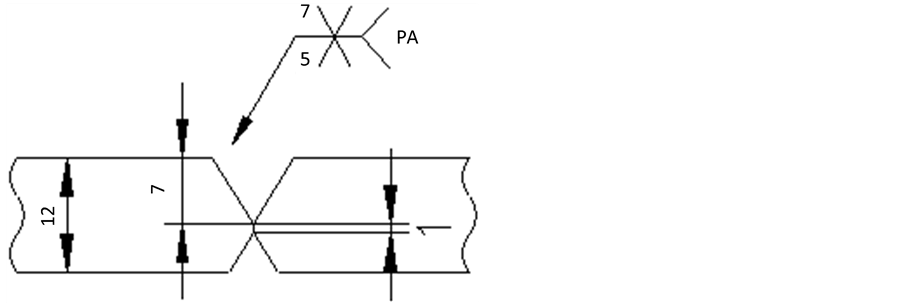
Figure 1. Diagram of welding groove of butt joint
图1. 对接接头焊接坡口示意图
3. 试验结果与讨论
3.1. 显微组织分析
图2(a)为焊缝区显微组织,主要为α-Al基体和其上分布着的部分析出的β (MgZn2),焊缝晶粒形态多为等轴树枝晶,图2(b)为熔合区显微组织,左侧为焊缝,右侧为热影响区,在靠熔合线的焊缝一边,晶粒沿散热方向呈十分明显的柱状晶,在熔合线处柱状晶较为粗大,这是因为铝合金焊接过程中,由于铝的热导率很大且结晶温度区间较宽,热量很快就传导开,使得热影响区晶粒生长过程中产生很大的过冷度,导致柱状晶组织的出现,过冷度越大,柱状晶越粗大,图2(c)为热影响区显微组织,可以看出热影响区组织与母材相似但由于热影响区靠近焊缝,受到焊接热循环的影响比母材大,温度高且冷却速度快,导致晶粒比母材处粗大,且析出相也比母材要多,图2(d)为A7N01P-T4铝合金焊接接头母材的显微组,为沿轧制方向延长呈纤维状的晶粒在α-Al基体上分布着时效过程中析出的MgZn2强化相。
3.2. 焊接接头硬度分布
图3为7N01铝合金对接接头硬度曲线。焊接接头显微硬度的变化表明焊接热循环作用下,焊接接头组织发生了复杂的相和组织变化。焊缝中心的硬度最低,约在80 HV左右,在距离焊缝中心6~10 mm
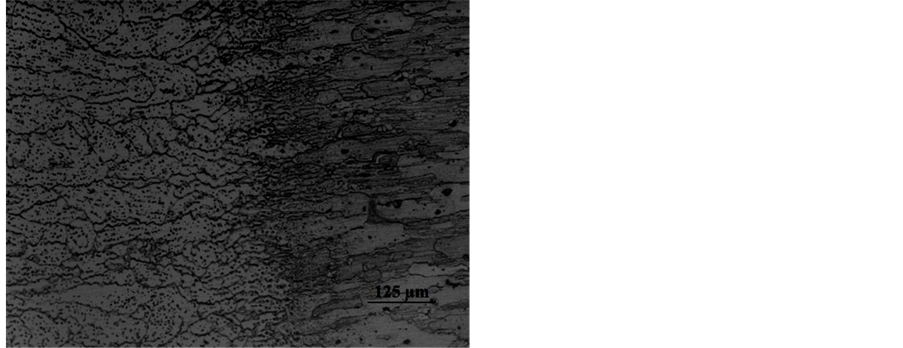
(a) 焊缝(b) 熔合区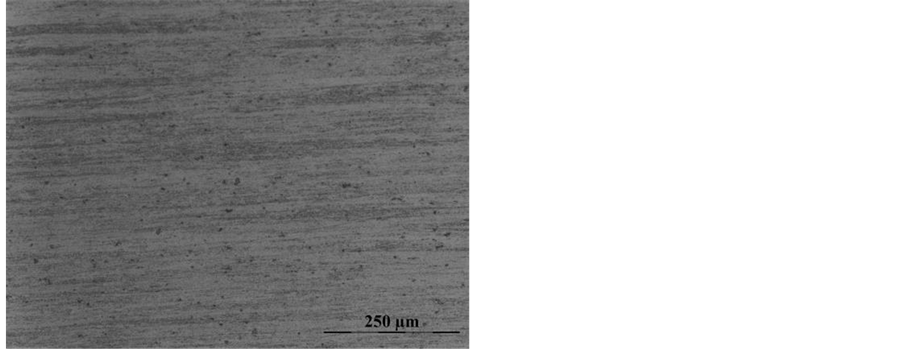
(c) 热影响区(d) 母材
Figure 2. Microstructure of A7N01P-T4 aluminum alloy butt joint
图2. A7N01P-T4铝合金对接接头显微组织
左右为淬火区,硬度约为145 HV,在距离焊缝中心±15 mm为软化区,在此区域硬度值显著下降,为热影响区硬度的最低点,约为110 HV。软化区由于焊接热循环温度过高使其组织发生再结晶而发生软化;在距离焊缝中心22 mm左右为母材,此区域硬度最高,为155 HV。对比三条曲线,可以发现打磨粒度对A7N01P-T4铝合金焊接接头硬度影响并不明显。
3.3. 拉伸试验结果及分析
从表3可看出,A7N01P-T4铝合金对接接头拉伸断裂位置都在焊缝,这与硬度试验得到的结论一致,说明焊缝是整个接头最薄弱的环节。其中试样7-40、7-80的抗拉强度相同,为303 MPa,试样7-120抗拉强度略有下降为288 MPa;经过打磨的焊接接头屈服强度和抗拉强度具有相同的规律,在打磨粒度为80目时取得最优的屈服强度为276 MPa,在打磨粒度为120目时,屈服强度最低,为257 MPa。焊接接头的延伸率亦在打磨粒度为80目时取得最大,在打磨粒度为40目时最小。
3.4. 疲劳试验结果及分析
通过表4和图4为经过不同粒度打磨后焊接接头疲劳试验结果和S-N曲线,可以看出7-40和7-120
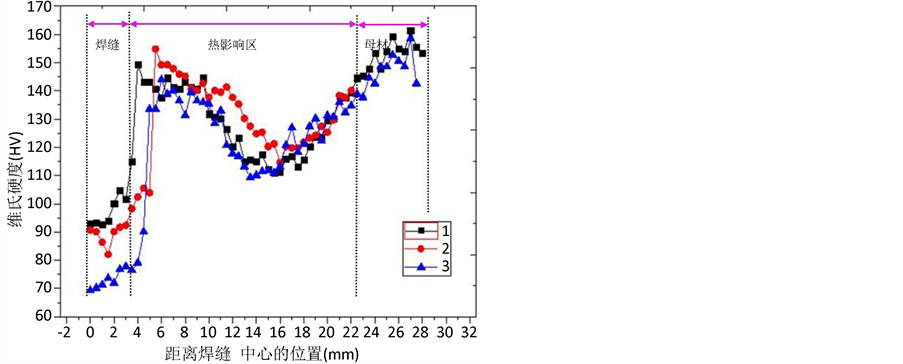
Figure 3. Hardness curve of A7N01P-T4 aluminum alloy butt joint
图3. A7N01P-T4铝合金对接接头硬度值曲线
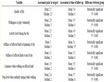
Table 3. Tensile test data of A7N01P-T4 aluminum alloy butt joint
表3. A7N01P-T4铝合金对接接头拉伸试验数据
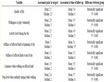
Table 4. Fatigue data of A7N01P-T4 aluminum alloy butt joint
表4. A7N01P-T4铝合金对接接头疲劳数据

(a) (b)
(c)
Figure 4. Fatigue S-N curves of A7N01P-T4 aluminum alloy butt joint after being polished by different particle sizes ((a) 40 mesh, (b) 80 mesh, (c) 120 mesh))
图4. 经不同粒度打磨后A7N01P-T4铝合金对接接头疲劳S-N曲线((a) 40目,(b) 80目,(c) 120目)
试样的疲劳极限为110 MPa,7-80试样的疲劳极限为100 MPa。
图5是经40目砂轮打磨7N01-T4铝合金对接接头疲劳断口形貌。图5(a)为疲劳源部,可以看到有放射状纹路汇聚于此,并且可以看出是由于气孔导致疲劳开裂。铝合金焊接时最容易产生的缺陷就是气孔和夹杂,尤其是厚板多层多道焊接时,气体来不及溢出因而会产生大量的气孔。由于气孔的存在导致试样内部几何条件不连续,孔边出现应力集中现象,使孔边应力远高于外部加载应力,滑移带更容易在孔边出现,萌生疲劳裂纹。疲劳裂纹自孔边萌生以后,将沿着与加载应力方向垂直的平面扩展,气孔的存在将影响到裂纹尖端应力强度因子的大小,从而影响到疲劳裂纹扩展速率 [6] 。图(b)为疲劳裂纹稳定扩展区,辉纹较浅,其扩展的切向方向指向疲劳源,图(c)是断口瞬断区的韧窝形貌,并伴随着气孔。
图6为经80目砂轮打磨A7N01P-T4-T4铝合金对接接头的疲劳断口,可以看出疲劳源位于试样近表面,有放射状纹路收敛于此。稳定扩展区由十分细密的疲劳辉纹组成,并且有二次裂纹穿插其中,瞬断区由大小深浅不一的韧窝组成,韧窝中有第二相粒子分布其中,为韧性断裂的特征。
图7为经120目砂轮打磨A7N01P-T4-T4铝合金对接接头的疲劳断口,可以看出疲劳源位于试样近表面,有放射状纹路收敛于此。稳定扩展区由十分细密的疲劳辉纹组成,瞬断区由大小深浅不一的韧窝组成,韧窝中有第二相粒子分布其中,为韧性断裂的特征。
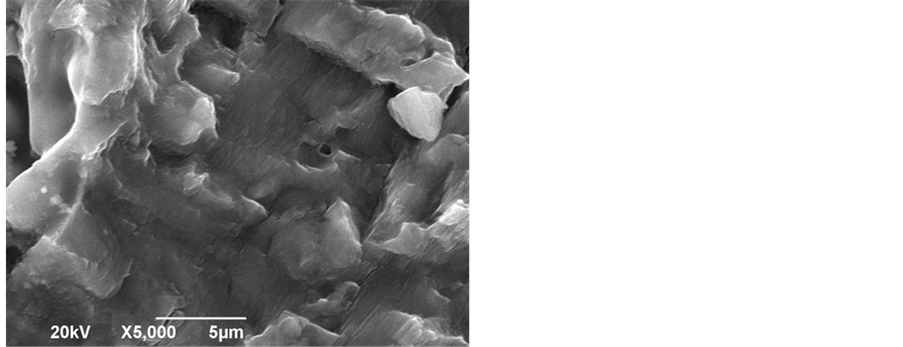
(a) 疲劳源 (b) 稳定扩展区
(c) 瞬断区
Figure 5. SEM diagram Fatigue fracture of A7N01P-T4 aluminum alloy butt joint after being polished by 40 mesh
图5. 经40目砂轮打磨A7N01P-T4铝合金对接接头的疲劳断口SEM图
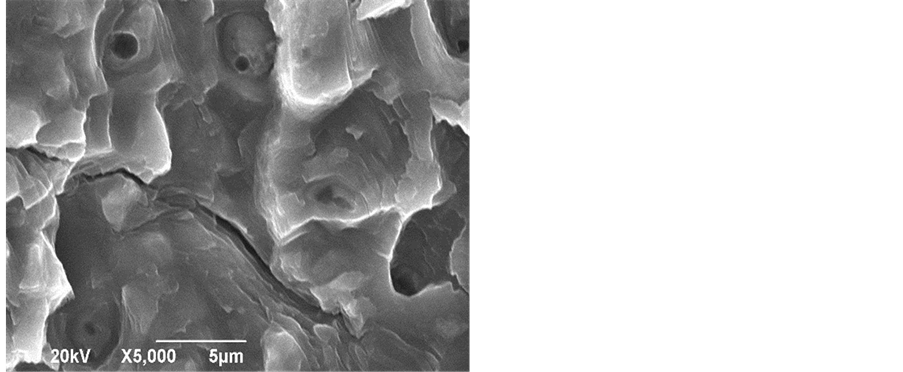
(a) 疲劳源 (b) 稳定扩展区
(c) 瞬断区
Figure 6. SEM diagram Fatigue fracture of A7N01P-T4 aluminum alloy butt joint after being polished by 80 mesh
图6. 经80目砂轮打磨A7N01P-T4铝合金对接接头的疲劳断口SEM图

(a) 疲劳源 (b) 稳定扩展区
(c) 瞬断区
Figure 7. SEM diagram Fatigue fracture of A7N01P-T4 aluminum alloy butt joint after being polished by 120 mesh
图7. 经120目砂轮打磨A7N01P-T4铝合金对接接头的疲劳断口SEM图
4. 结论
(1) 利用MIG焊可获得焊接质量比较好的铝合金焊接接头,拉伸试验结果表明A7N01P-T4铝合金焊接接头的抗拉强度低于母材的抗拉强度,拉伸断口部位位于焊缝中心位置,可见A7N01P-T4铝合金焊接接头的焊缝强度最低,成为焊接接头的薄弱环节。随着打磨粒度的升高,焊接接头的拉伸强度和屈服强度均有所下降,但下降幅度很小。
(2) 焊接接头的显微硬度在焊缝处较低,且整体上随着远离焊缝显微硬度会慢慢升高,但是在距离焊缝中心16 mm左右处存在软化区。焊接接头显微硬度的变化表明焊接接头在热循环作用下,其组织发生了一系列复杂的变化。
(3) 在焊接热循环的作用下,铝合金A7N01P-T4焊接接头分为热影响区、焊缝区以及母材区,在热影响区存在软化区,在不同的区域有着不同的显微组织结构、第二相分布,焊缝中心为等轴晶组织,焊缝边缘形成了柱状晶。熔合区形成柱状晶粒,熔合区存在严重的化学不均匀性和物理不均匀性。
(4) 不同打磨粒度下铝合金A7N01P-T4焊接接头的S-N曲线整体变化趋势相同,随着应力幅值的降低其疲劳寿命升高;且打磨粒度对其并无明显影响。
(5) 焊接接头疲劳断裂均发生在焊缝处,焊接接头的疲劳断口包括三部分,即疲劳裂纹萌生区、疲劳扩展区和瞬断区,并且各个区域有着不同的断口性貌;由于焊缝边缘微观组织的不均匀性,且焊缝中存在气孔等缺陷,焊接接头疲劳裂纹易于在此处产生,进而向焊缝处扩展,最终断裂。
(6) 虽然焊接热循环作用在焊接接头的热影响区形成软化区,此区域的硬度值较低,力学性能也有所下降,但是疲劳断裂仍然没有在此处发生,说明软化区对A7N01P-T4铝合金整体疲劳寿命影响不大,在进行疲劳性能的改善上应该主要考虑焊接接头。