1. 引言
环保与节能是当前汽车设计的焦点,轻量化设计可以显著减少能源消耗,降低环境污染,同时提高汽车操纵性能和安全性能 [1] [2] [3] 。采用多元材料混用策略可以达到良好的汽车轻量化效果 [4] 。通过在低成本全钢汽车车身中引入铝合金等轻金属材料,可以充分发挥不同材料各自的性能优势。因此多元材料车身已成为现阶段汽车车身轻量化的必然选择。
铝合金–高强钢的复合焊接结构强度高、耐腐蚀、质量轻。在汽车车身中采用铝合金代替钢材,是实现汽车轻量化设计最直接有效的途径 [5] 。由于铝–钢物理性能差异显著,且Fe在Al中的固溶度极低,导致铝–钢异种金属的焊接性极差,焊接接头中容易产生缩孔、裂纹等缺陷及硬脆的金属间化合物,大幅度降低了接头的力学性能 [6] ,限制了铝–钢焊接结构在汽车领域的应用。
磁脉冲焊接是一种高速固相焊接技术,能够有效地避免上述铝–钢的焊接问题 [7] 。与爆炸焊接类似,磁脉冲焊接接头结合区存在和压力焊类似的金属塑性变形、和熔化焊类似的金属融化以及和扩散焊类似的金属原子的互相扩散。因此,磁脉冲焊接工艺可以看作为压力焊、熔化焊和扩散焊三位一体的金属焊接新工艺 [8] 。焊接过程中,金属无熔化过程,避免或减少了金属化合物的产生;碰撞点处产生高速射流清理焊接表面氧化层,利于不同金属原子互相扩散、结合,可形成性能良好的接头。
本文对不同焊接工艺参数下的5052铝合金和HC420LA高强钢磁脉冲焊接接头进行了性能测试,通过OM、SEM和EDS等微观分析方法对铝–钢焊接界面微观组织进行研究,进一步阐释了失效机理,为铝–钢磁脉冲焊接技术在汽车上的应用提供参考。
2. 实验
2.1. 磁脉冲焊接原理
磁脉冲焊接(Magnetic Pulse Welding)是一种较新的固态焊接工艺,其原理是利用电磁力驱动焊接结构中动件与静件高速碰撞而实现冶金焊接效果。板件磁脉冲焊接的原理如图1所示,首先将动件与静件以一定间距放置、固定好,通过电容器对线圈放电,线圈中通入变化的高强度电流,由于涡流效应,动件内会产生变化的感应电流,两种变化的电流方向相反,两者之间会产生巨大的洛伦兹力。动件在洛伦兹力的作用下获得较高的速度向静件运动,并与静件发生高速碰撞而产生焊接效果,通常碰撞速度能达到数百米每秒。
在本文焊接试验中,放电电流通过放电能量控制,因此主要工艺参数为放电能量与焊接间距。对5052铝合金板材和HC420LA高强钢板材进行磁脉冲搭接焊,分别进行了30 kJ能量−1.4 mm间距和30 kJ能量−1.6 mm间距两种工艺参数下的工艺试验。
2.2. 试验材料
动件材料为5052铝合金,是应用最广的一种防锈铝,具有强度高、疲劳寿命久、塑性与耐腐蚀性好等优点;静件材料为HC420LA高强钢,是一种常见的冷成型高强钢。这两种材料在交通车辆中广泛应用。动件和静件尺寸一致,其长宽厚为90 × 40 × 1.5 mm。两种材料化学成分如表1、表2所示。
3. 结果与讨论
3.1. 焊接接头力学性能
对两种焊接工艺参数下的铝–钢焊接接头进行强度测试,通过剪切试验对铝–钢焊接件进行性能评估,从而考察不同工艺参数对焊接接头强度的影响。30 kJ放电能量为例,选取焊接间距分别为1.4 mm和1.6 mm的焊接件,考察不同焊接参数下的焊接失效模式。剪切试验所用设备为Instron5184电子拉伸机,最大拉伸力为150 kN。设定拉伸速率为2 mm/min,进行室温下的准静态测试。由于焊接件为搭接形式,其形状不是平直的,为避免搭接接头在厚度方向上的偏距对测试产生影响,因此夹持的时候添加一定厚度的夹片,尽量削减额外扭矩。如图2所示,基体的板材受到单向的拉伸,而焊缝受载可简化为纯剪切状态。为了确保所测焊接机头抗剪切力的准确,每种工艺参数下的焊接接头进行三次重复性剪切试验。
如图3所示,图3(a)为30 kJ −1.4 mm参数下焊接接头的失效形式,最终表现为铝合金母材的断裂;图3(b)为30 kJ −1.6 mm参数下焊接接头的失效形式,最终表现为焊接接头断裂。
对于第一种失效模式,即铝合金母材断裂失效,其最终断裂形式为韧性断裂。在该参数下,铝–钢焊接接头获得了合适的碰撞速度与碰撞角度,获得了良好的冶金焊接效果,形成了稳定牢固的焊接接头。该参数下的焊接接头强度较高,高于铝合金母材强度,因此在外加载荷作用下,铝合金母材作为较弱区发生了断裂失效。

Figure 1. The schematic of magnetic pulse welding for sheet metal
图1. 板件磁脉冲焊接原理图
表1. 5052铝合金板材化学成分(wt. %)
表2. HC420LA高强钢板材化学成分(wt. %)
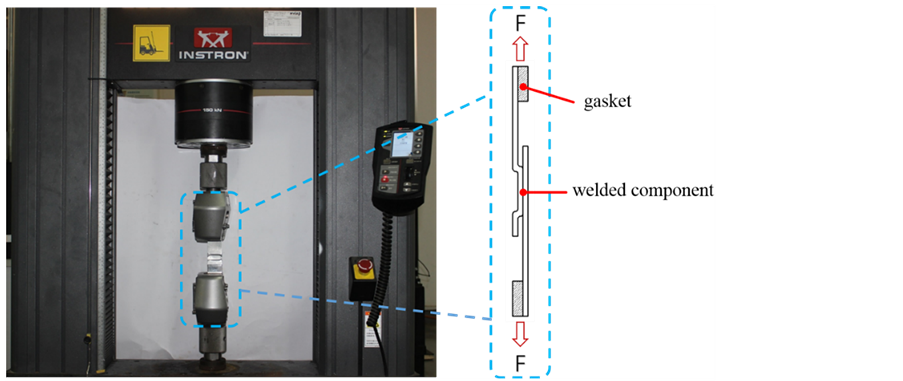
Figure 2. Shear test of aluminum-steel magnetic pulse welded joint
图2. 铝–钢磁脉冲焊接接头剪切测试
(a) 30 kJ −1.4 mm焊接接头失效形式 (b) 30 kJ −1.6 mm焊接接头失效形式
Figure 3. Failure form of welded joint
图3. 焊接接头失效形式
对于第二种失效模式,即焊接接头断裂失效,最终断裂形式为脆性断裂。在该焊接参数下,由于焊接间距的增大,导致了碰撞速度和碰撞角度均增大,此时的焊接接头质量一般,其强度低于铝合金母材,在外加载荷所用下断裂发生在焊接接头。对于这种失效模式,原因是较为复杂的,主要是由于焊接工艺参数不合适导致了焊接界面失稳。
3.2. 焊接界面形貌分析
为了对不同焊接参数下导致的焊接接头性能差异进行进一步探索,对两种工艺参数下的焊接接头界面进行微观形貌分析。根据图4所示金相图片,发现两种参数下的焊接接头的有效焊缝长度是不一样的。其中图4(a)为30 kJ −1.4 mm的焊接界面,其抗剪切载荷均值为10219 N,断裂失效发生在母材;图4(b)为30 kJ −1.6 mm的焊接界面,其抗剪切载荷均值为7856 N,断裂失效发生在焊接接头;虽然失效形式不一样,但是焊接接头强度均属于焊接良好的状况。这与图中出现了明显的波形结合界面特征相符。
两种参数下的焊接接头强度存在的差异可以从图中成波长度得到解释。可以发现,焊接质量好的接头界面,即30 kJ −1.4 mm,其成波长度较长,约1000 μm;焊接质量较差的接头界面,即30 kJ −1.6 mm,
(a)30 kJ −1.4 mm接头波形界面
(b)30 k J −1.6 mm接头波形界面
Figure 4. Wave interface of welded joint
图4. 焊接接头波形界面
其成波长度较短,约500 μm。对于焊接区域两侧无波部分,也发现焊接质量较好的界面无波部分贴合依然很紧密,而焊接质量较差的界面无波部分贴合较为疏松。由于成波长度以及结合紧密程度的不同,两个焊接参数下的有效焊缝长度和面积相差较大,因而表现出不同的强度特征。
3.3. 焊接界面缺陷分析
图5为不同失效模式所对应焊接件的焊接界面SEM扫描图像和EDS元素分析。其中图5(a)为30 kJ −1.4 mm的焊接界面;图5(b)为30 kJ −1.6 mm的焊接界面。
首先对铝–钢焊接界面微观形貌观察,图中黑色区域为铝基体,白色区域为钢基体。通过形貌观察发现结合区主要包括波形界面和灰色过渡区。波形界面的出现是冲击应力波和材料互相作用的结果,反映了金属塑性变形形成焊接的过程 [9] 。波形界面形状为剪切波,即铝母材和钢母材以互相嵌入的形式结合,嵌入程度越深,说明连接效果越好。而随着焊接间距变大,碰撞速度变大,碰撞角度变大,金属塑性变形也变得更为剧烈,因此界面波形尺寸从图5(a)中较为平坦的剪切波逐渐变为图5(b)中起伏较大的波形。
通过EDS对铝–钢焊接界面过渡区进行元素分析,发现在1.4 mm间距的接头过渡区内没有发现原子分布平台的出现,说明没有出现Al原子和Fe原子固定质量比的第二相,过渡区仅仅发生了元素扩散,因此其性能较好。而在1.6 mm间距的接头过渡区内,则发现两母材元素的质量分数在一定范围内呈现近似平台状分布,说明此区域内元素发生了扩散并形成了金属固溶体或者金属间化合物的第二相,而这些硬脆的第二相对于焊接质量具有削弱作用。
对于焊接界面中的缺陷,可以发现图5(a)中焊接质量良好,未出现明显的缺陷;而图5(b)中则出现了明显的孔洞与裂纹。因此,虽然1.6 mm间距下的碰撞速度和碰撞角度较大,金属塑性变形较明显,可是过高的碰撞速度和过大的碰撞角度导致了母材剧烈的变形,从而发生了焊接区微观缺陷。这个现象也解释了两种参数下焊接接头性能差异的原因。
(a)30 kJ −1.4 mm焊接接头波形与元素分布
(b)30 k J −1.6 mm焊接接头波形与元素分布
Figure 5. Wave shape and elements analysis of welded joint
图5. 焊接接头波形形貌与元素分析
4. 结论
1) 焊接工艺参数对铝–钢焊接接头强度影响较大,过大的碰撞速度和碰撞角度导致焊接接头强度的明显差异,从而表现为不同的失效形式。
2) 随着焊接间距的增大,碰撞速度和碰撞角度随之增大,焊接界面发生剧烈的塑性变形,但是有效结合长度缩短。
3) 碰撞速度和碰撞角度的增大导致焊接界面的失稳,表现为微观裂纹和空洞的增加,同时生成了异种金属间的第二相生成物体,削弱了接头强度。