1. 引言
企业竞争和经营环境的日益变化 [1] ,促使国内很多自主品牌不断展开国内市场的角逐,同时在海外也不断进行战略部署和推进海外汽车工厂建设。以G公司为例,G公司是我国汽车自主品牌,旗下拥有汽车、轿车等产品,是中国汽车行业十强,公司除了国内制造产品进行内销及出口,也在海外建立汽车工厂以半散装件Semi Knock Down即SKD和全散装件Completely Knock Down即CKD (SKD半散装件:在国际贸易中,特别是在国际汽车贸易中,整车出口国的汽车公司把成品予以拆散,而以半成品或零部件的方式出口,再由进口厂商在所在国以自行装配方式完成整车成品并进行销售。CKD全散装件:CKD是以全散件形式作为进口整车车型的一种专有名词术语,在当地生产的零部件以较低的关税和较低的工资,利用当地劳动力组装成整车,并以较低零售价出售。)的模式等进行组装并销售。在这一前提下,批量的零部件订单将发往海外汽车工厂,由于制造、包装、物流、供货清单等多方面的原因造成了或多或少的零部件需要进行索赔。为保障海外汽车工厂生产并提高客户满意度,这就要求索赔件必须快速送达,考虑到索赔成本问题又必须选择合理发运方式和追溯方式,所以企业间除了质量、种类的竞争外,时间和成本也成了最有力的竞争优势资源。在索赔业务中,索赔周期与索赔成本既相关又矛盾,那么如何打破索赔周期与索赔成本的博弈状态,使得多个追逐竞争的要素成为可能,是目前需要探讨的问题。而G公司从事海外汽车生产多年,在索赔方面积累了较为完善的数据,下面就以G公司的索赔业务实例来探讨海外工厂索赔件的周期及成本问题。
2. 零部件索赔
当发往海外工厂的零部件在开箱、拆箱过程中或在装配过程中发现存在缺陷异常情况,缺陷异常主要有以下几类:
错发,实际所发运的零部件在颜色、尺寸、状态、规格型号上与实际需求不相符。
漏发,实际所发运的零部件有遗漏的情况。一是发现某种物料在包装清单上的数量少于所对应供货清单中的数量,二是发现某种物料在包装箱内的数量少于包装清单上的数量。
装配质量问题,国内分装在总成零部件上的物料存在错、漏装违背工艺及质量缺陷。
功能性质量问题,实际所发运的零部件虽满足装配工艺但在国外装配过程中却出现功能缺陷或功能丧失的问题。
包装类问题,实际所发运的零部件因包装材料、包装工艺及包装过程中出现的缺陷导致零部件在国外开箱现场出现凹坑、划伤、变形、磨损、损坏等问题。
零部件质量问题,非包装原因的零部件本身质量缺陷问题。
当该缺陷异常经判定确实为供货方造成,此时海外工厂方向国内供货方提出物料索赔及返修索赔我们称之为零部件索赔,本文中的零部件索赔仅指物料方面的索赔。处理索赔业务的周期称之为索赔周期,而因索赔产生的相关费用则称为零部件索赔成本。
当该缺陷异常经判定确实为供货方造成,此时海外工厂方向国内供货方提出物料索赔及返修索赔我们称之为零部件索赔,本文中的零部件索赔仅指物料方面的索赔。处理索赔业务的周期称之为索赔周期,而因索赔产生的相关费用则称为零部件索赔成本。
零部件索赔成本主要包括国内段成本和国外段成本,国内段索赔成本包含零部件采购货值、运杂费(包括运输费、装卸费、拖车费、仓储费等),国外段索赔成本主要包含清关关税费、仓储费、报关管理费。索赔成本的多少主要受索赔件货值、索赔运输方式、索赔件体积重量等因素的影响。
G公司海外的零部件索赔基本上为应急型需求,即当海外发生索赔就补发,这种应急形式导致对索赔周期和索赔成本的考虑也相当匆忙,根据G公司海外各驻厂办反馈信息及往期索赔成本追溯数据得知,存在索赔周期较长及索赔亏损问题,而合理的索赔周期和索赔成本是索赔业务要达到的效益目标,因此缩短索赔周期和控制索赔成本十分有必要。
3. 缩短索赔周期和控制索赔成本的方法
以G公司各海外汽车工厂615条索赔样本数为例,对索赔周期进行均值过程分析(见表1),不同发运
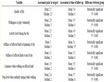
Table 1. Resulting data of variable grouping—Claim cycle report
表1. 变量分组统计结果数据—索赔周期报告
方式其周期长短不同,国际快递最短、其次空运、海运最长。根据标准差,各发运方式下的周期模块实际需要的周期存在一定波动,波动越小越接近于周期均值,波动越大则离均值越远同时也说明其制约因素越多,所以根据零部件紧急程度和工厂生产实际需要,可以选择合适的发运方式。
由于需要索赔的零部件不固定,在缩短索赔周期和控制索赔成本方面,除了正常的分紧急和非紧急情况下用压缩业务操作时间及应急型补发外,还可通过以下方法进行。
3.1. 最优发运方式法
在发运前,应根据索赔件的重量、数量、体积等选择最优发运方式以提高发运方案的安全性、经济性和迅速性,这有利于缩短索赔周期和控制索赔成本。根据G公司索赔业务操作实际来看,当索赔件重量小于30 kg,体积小于1 m3时采用国际快递进行发运优于走空运或是海运,若走空运或是海运,一是定制的舱位空间利用率不高;二是易丢失且费用较高。当需要索赔的零部件比较笨重(如钣金件、发动机)或体积庞大(如顶盖内饰)时,根据物料属性选择空运或者海运优于走国际快递。
3.2. 提高空间利用率法
空间利用率等于箱内最大容积除以箱内所有子箱所占空间所得的数值,这对小包装来说较为有利些 [2] 。空间利用率主要包括集装箱空间利用率,包装成品空间利用率及最小包装单元空间利用率。它直接决定着包装体积,从而直接影响包装运输成本。空间利用率可以通过空间体积分割法及汽车散件形状、尺寸搭配设计方法提高。空间利用率只有达到最大,才能充分的利于运输空间,减少运输包装成本 [3] 。如空间利用率达85%甚至90%以上。
3.3. 建立海外安全库存法
通过建立海外安全备件库来缩短索赔周期的方法,即将零部件中易损坏及质量不稳定的零部件提前准备一些在海外汽车工厂,把零星的领料转变为有目的性的备货。采用安全库存法,索赔周期几乎为零,索赔成本等于零部件采购货值和运杂费,当准备的零部件随订单拼箱发运时,索赔成本基本等于零部件采购货值。
易损件或是质量不稳定的件的数量可以通过需求进行预测。首先收集分析当前生产量及其在一定时间的索赔变化率,按问题类别对索赔数据进行分类,确定以往索赔需求的决定因素及其对以后索赔需求的影响,同时预测这些因素的发展趋势及对新需求的影响,最终综合分析进行需求预测 [4] 。因此对TOP问题前10位且反复发生的故障,建议根据问题发生概率及订单数量,可适当准备一些在海外的安全备件库存中。这样,可避免因国内月底、节假日原因无法领料以及供应厂家无物料库存而导致海外发生问题急需零部件却只能等待的情况及因缺件导致停产、整车无法出运的情况发生。而对于体积大的总成提前通过海运拼箱,可避免因紧急需求而采用发空运和国际快递,一定程度上节省了运输成本。
3.4. 固定舱额体积发运法
在每月持续生产订单量的情况下,累计每天产生的索赔件数量并定期(如一周一趟)将固定舱额体积X m3的索赔件发往国外以满足海外生产的方法叫做固定舱额体积发运法。当累计的索赔件的体积大于固定舱额体积时,根据实际需求,可将其中的部分索赔件累计到下一批次的固定舱额体积中去发运也可走国际快递或空运;当累计的索赔件体积小于固定舱额体积时,可直接发运或通过掏箱方式去补海外安全库存将固定舱额体积填满后再发运。当长期所累积的索赔件体积都低于固定舱额体积,那么该固定舱额体积可适当进行调整。
固定舱额体积发运法的船期船舱固定,当索赔件包装好后即可拉至码头安排进仓,省去了物流询价预定舱位的时间。随着零部件质量不断提升、包装方案不断优化以后,需要索赔的零部件减少,此时该固定舱额体积也可根据实际需要进行缩减,这样舱位运费也将减少。
对G公司2016年海外零部件海运索赔订单数据进行分析,由报告可知(见表2),在每月平均生产订单数为322.56台情况下,其所需的月度索赔件固定舱额平均体积为1.6906 m3,据此可推出,周度索赔件固定舱额平均体积 = 1.6906 m3 ÷ 4 = 0.42265 m3,单台订单索赔件固定舱额平均体积 = 1.6906 m3 ÷ 322.56 = 0.00524 m3,根据前文最优发运方式法,当海外索赔件重量小于30 kg,体积小于1 m3时建议走国际快递。
假设G公司海外某汽车工厂年产值60000台,平均每月订单数为5000台,那么该汽车工厂的索赔件周度固定舱额的值 = 5000 × 0.00524 ÷ 4 = 6.55 m3。
综上,当海外工厂所需索赔件体积大于1 m3且KD工厂为月持续一定量订单时可采用固定舱额体积进行发运。按本案例情况,若要采用固定舱额体积发运,其海外汽车工厂月持续生产订单应不小于800台。
4. 索赔成本追溯方案的提出
当发生零部件索赔时,对外致力于做到索赔成本低、索赔周期短;对内则希望对责任单位尽快追溯保障索赔盈亏。但在索赔成本追溯过程中由于索赔责任单位众多,追溯扣款速度缓慢,导致索赔成本追溯存在考核不明以及亏损情况。以G公司2016年索赔成本追溯为例,其索赔成本追溯主要扣回了部分国内段索赔成本,或只扣索赔件货值或只扣运杂费用或扣零部件货值和运杂费,而国外段的索赔成本由于包装外包和外方国外段成本反馈周期长等原因基本无法及时追溯造成了亏损,为扭转这一局面,可参考以下方案。
4.1. K系数方案追溯
即按照索赔成本用零部件采购货值与系数K的方式来追溯索赔成本的方案,该系数K计算公式如下:
根据,索赔成本 = 国内段费用 + 国外段费用
= (零部件采购货值 + 运杂费)+ 国外段费用
= 零部件采购货值 × (1 + K)
得知,系数K = (运杂费 + 国外段费用) ÷ 零部件采购货值。
这种追溯方式的优势在于操作简单且快捷只要知道零部件的采购货值乘以系数K就可以向责任方进行成本追溯,但这种方式存在盈亏不可控的问题,由于运杂费和国外段费用主要影响因素是索赔件重量和索赔件体积,从G公司各发运方式下索赔件重量、体积与成本的关系(见图1、图2和图3,为了更直观展示其趋势我们将索赔成本缩小了10倍或100倍,在国际快递发运方式下也对索赔件体积由立方米扩
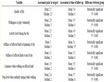
Table 2. The data analysis report of claim orders and volume
表2. 索赔订单与体积数据分析报告
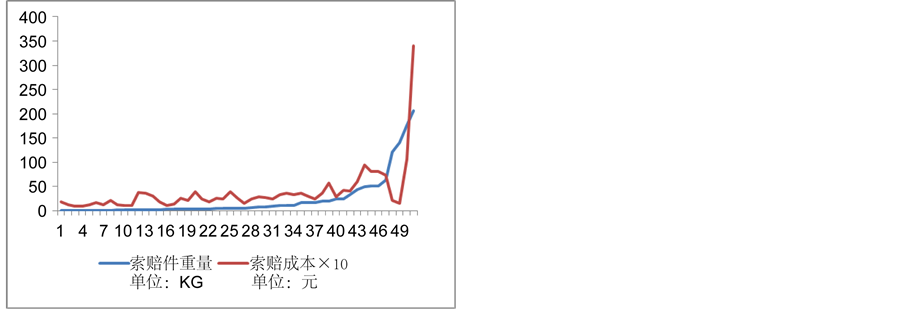
Figure 1. Relationship between weight & volume of claim parts and cost delivered by International Express
图1. 国际快递发运方式下索赔件重量、体积与成本的关系
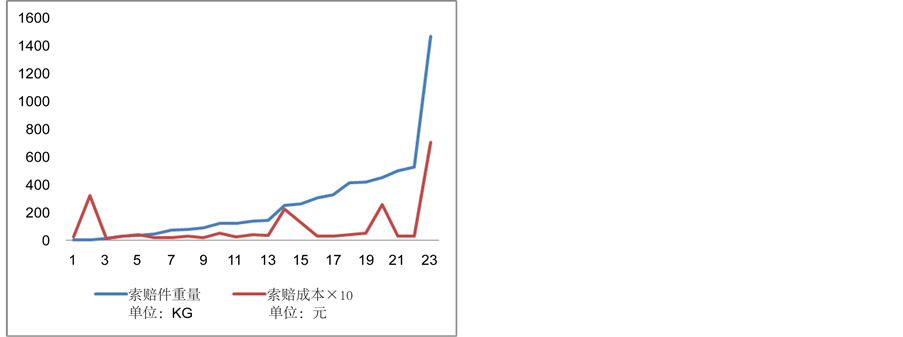
Figure 2. Relationship between weight & volume of claim parts and cost delivered by Air
图2. 空运发运方式下索赔件重量、体积与成本的关系
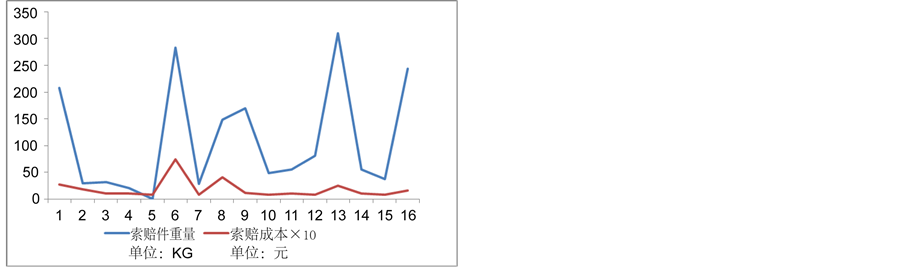
Figure 3. Relationship between weight & volume of claim parts and cost delivered by Sea
图3. 海运发运方式下索赔件重量、体积与成本的关系
大到立方分米)可知当索赔的零部件以国际快递和空运发运方式占多数时其索赔成本的波动较大,即追溯的成本盈亏波动也大,而海运发运方式下索赔件重量、体积与成本为正相关,基本可以保证不亏。
4.2. 按实际产生费用混合追溯
该追溯方法即向责任方追溯扣款索赔实际产生的费用。这种索赔追溯的方案基本可以保证索赔成本不亏,而一票索赔订单往往存在多方责任单位,这时按照单个责任方的索赔件体积或重量占所有索赔件包装总体积/总重量百分比来进行追溯扣款,方案的分配规则并非十分精确,索赔成本追溯的速度也比较慢。总体上说这种方案取决于企业愿意承担索赔追溯成本结算滞后的风险程度。
4.3. 单独追溯
当发生的多个索赔件或是批量索赔件的责任方唯一时,采用单独发运,所产生的索赔成本也进行单独追溯。单独追溯可以保证索赔成本不亏损,但该种追溯方式由于相关费用的单据反馈迟缓同样具有滞后风险。
5. 总结
在激烈的市场竞争中为了提高竞争优势 [5] ,企业在面对海外索赔时,一方面需尽可能地控制索赔成本和缩短周期,另一方面为了应对索赔需求的不确定性以满足海外生产并提高客户满意度,不仅需要选择最优的发运方式、提高空间利用率,同时还需要设置合适的海外安全库存以及采用固定舱额体积的方法来发运一定量的索赔件,为保障索赔盈亏,在追溯零部件索赔成本时可用K系数追溯、实际产生费用混合追溯或单独追溯。当然,如何缩短索赔周期和选择何种索赔成本追溯方案,企业还应根据自身海外汽车工厂产量及实际需求来确定。