1. CFM56发动机及其风扇简介
CFM56发动机是由美国通用电气公司(GE)和法国国营航空发动机研究制造公司(SNECMA)共同组成的CFM国际公司(CFMI),在F101核心机技术的基础上,为适应20世纪80年代后国际军、民用飞机市场的需要而研制的100 kN级高涵道比涡扇发动机。从它的第1个型号CFM56-2于1979年11月取得适航证后,到2005年已发展了CFM56-3,CFM56-5A、CFM56-5B、CFM56-5c、CFM56-7等6个系列,共有28个型号,其推力覆盖了71~151 kN,已成为22个型号飞机的动力。
航空发动机是飞机的动力装置,为其提供飞行推力,被誉为飞机的“心脏”,而风扇是涡轮风扇发动机的重要部件之一。风扇后面的空气分为两路,一路是外涵道,一路是内涵道。风扇一般为一级,结构简单。风扇设计技术主要包括气动设计技术、全三元计算技术、间隙控制技术、旋转失速和喘振控制技术、结构设计技术、材料与工艺技术等方面。风扇是航空发动机的重要压缩部件,它的性能的好坏直接影响整个发动机的性能。
2. 风扇叶片的线弹性有限元应力分析计算
由于风扇叶片的结构、受载及约束条件都是空间的,所以要计算风扇叶片在离心载荷下的应力,就需对风扇叶片进行有限元分析。叶片线弹性应力分析的前提条件为 [1] [2] 。
1) 叶片工作时的变形为小量。一般来说,变形量的大小事先并不能确定,只能凭经验估计。从现有的发动机来看,风扇叶片的变形比较小,可以认为它满足小变形的要求。
2) 工作时叶片材料尚未屈服,即处于弹性范围之内。目前绝大多数发动机叶片均采用弹性设计,都能满足这一要求。
3) 叶片相互之间或与其他零件不接触。所以,本文讨论的叶片不包括榫头部分,且不考虑其相邻叶冠和减振凸肩间的接触。
对叶片进行离散化时,在应力变化大的区域如叶根附近,网格应分的比较密,而在应力变化小的区域如叶尖附近,网格可分得疏一些,还应注意的是,划分单元时应使单元各方向的尺寸大致相近,并尽量使各单元的各夹角相差不大,这样才能保证所划分的单元具有良好的特性。
2.1. 风扇强度分析模型
2.1.1. 风扇三维模型
根据CFM56发动机在三维设计软件CATIA中建立了风扇的模型如图1示。
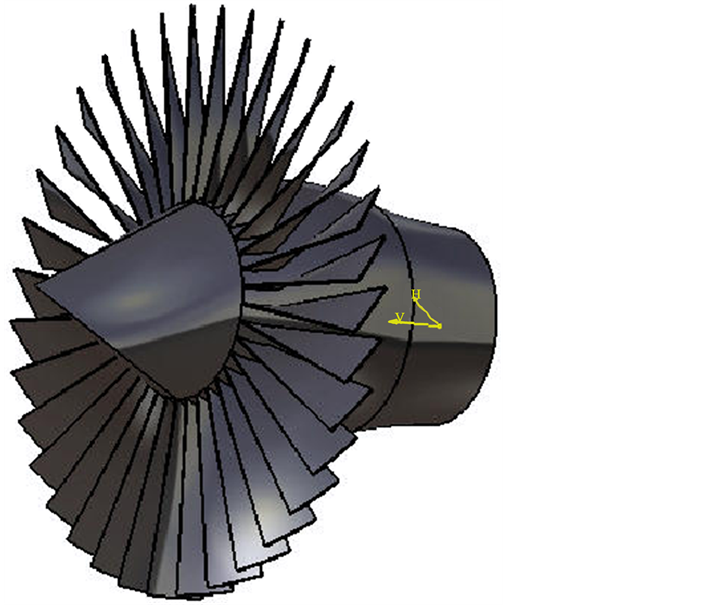
Figure 1. Fan model of CFM56 engine
图1. CFM56发动机风扇模型
2.1.2. 风扇的材料的应用
计算中模型所采用的材料为钢材,材料参数如表1示。
2.2. 风扇的有限元网格
单元全部采用的是六面体单元,风扇的单元尺寸为50 mm,由于需要对风扇叶片进行强度计算,所以叶片的网格风扇叶片的单元尺寸为20 mm。网格采用CATIA软件中的网格划分工具,对三维实体生成有限元网格,得到57,403个单元、18,459个节点。
2.3. 计算载荷与边界条件
2.3.1. 叶片受载特点
风扇叶片在工作时绕发动机轴线旋转,所受载荷包括离心力、气动力和热载荷。
气动力是一种表面分布压力,它作用在叶片的各个表面,但它不是均匀分布力,它沿叶高方向和叶宽方向的分布都不是均匀的 ,较为准确的气动力场可由叶栅通道和三维流场计算得到,但工作量较大。一般来说,对叶片进行应力分析时应该考虑气动力,但有时可能因得不到有关数据而无法予以考虑。风扇叶片上离心应力比气动应力大得多,所以忽略气动力对分析结果的影响不大。
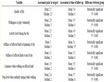
Table 1. Physical parameters of steel
表1. 钢材的物理参数
离心力是一种体积力,它与质量及其所处的半径成正比,与其转速的平方成正比,离心力主要使叶片产生径向的拉应力,对于扭转叶片,同时会产生扭转应力。热载荷是由于叶片受热时各部分的变形相互制约而产生的,热载荷所产生的热应力不仅与叶片的温度梯度有关,而且与叶片所受的几何约束有关,叶片的温度梯度越大,几何约束越紧,则热应力越大,所以,热载荷通常以温度场的形式来描述,并且与几何边界条件密切相关,严格地讲,所有叶片上都有热载荷作用,但对于风扇叶片来说,由于温度较低且温度分布均匀,所产生的热应力不大,所以应力分析时常常予以忽略。
2.3.2. 离心力的分析计算
由2.3.1可知,叶片的应力分析只需考虑离心力的影响。本文只对风扇叶片在离心载荷下进行强度计算与分析。用CATIA计算风扇叶片的变形和应力,风扇的额定转速为14,460 r/min,为分析风扇在不同转速下的应力分布,这里取三个不同的转速8000 r/min、14,460 r/min和20,000 r/min进行分析。用CATIA自带有限元进行分析不同的转速下的应力如图2和图3所示。
由图2和图3可知,风扇在8000 r/min时应力集中在风扇叶片的根部,叶片所受的最大应力为74.4 MPa,变形位移出现在风扇叶片的叶尖,叶尖的最大径向位移约为0.208 mm。
同理可知,风扇在14,460 r/min时应力集中在风扇叶片的根部,所受的最大应力为398.2 MPa,变形位移出现在风扇叶片的叶尖,其中叶尖的最大径向位移约为0.713 mm。风扇在20,000 r/min时应力集中在风扇叶片的根部,叶片所受的最大应力为614.1 MPa,变形位移出现在风扇叶片的叶尖,叶片的最大径向位移约为1.0948 mm。
由上可知,在不同转速下风扇的受力情况基本相同,应力集中点都在叶片的根部,最大变形位移均在叶片的尖端,转速越大,叶片受力也越大,叶片的径向位移越大。在额定转速下风扇的最大离心应力为398 MPa。
2.3.3. 扭矩的影响
风扇叶片在离心力场的作用下,叶片除了拉伸外,还要承受扭转恢复扭矩,产生扭矩恢复变形。叶片扭转的越大,其产生的恢复扭矩也越大,叶片的扭转恢复变形,将在叶片的横截面上产生扭转切应力,并使叶片截面上的拉应力重新分布。在2.3.2中考虑了只离心力的影响,没有考虑扭矩的影响,在此单独分析扭矩对风扇叶片的影响,在风扇叶片添加一个扭矩。根据风扇的额定转速计算扭矩的具体方法如下:
式中,T (N∙m)为扭矩;P (kW)为功率,本文中的功率为1800 kW;n (r/min)为转速,这里采用额定转速14,460 r/min。风扇在额定转速下的扭矩的大小是1189 N∙m,在此对风扇分别施加三个不同的扭矩进行分析,其应力如图4和图5所示。
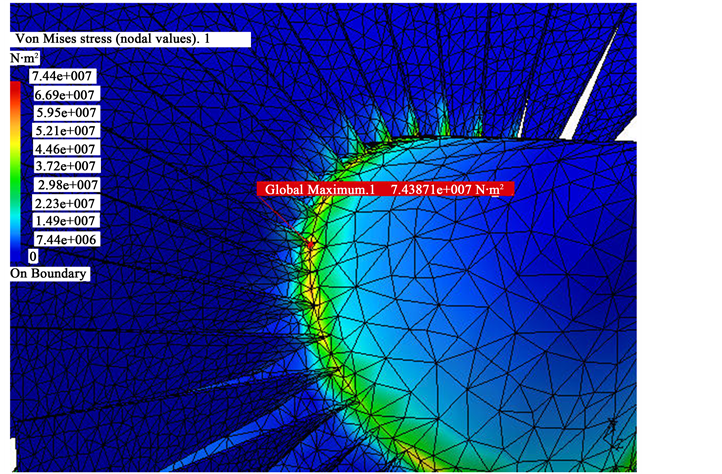
Figure 2. The stress distribution of fan at 8000 r/min
图2. 风扇在8000 r/min的Von Mises应力分布
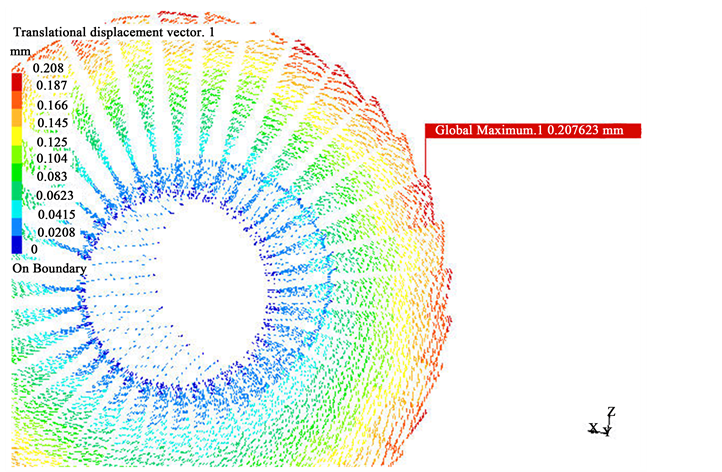
Figure 3. The stress deformation of fan at 8000 r/min
图3. 风扇在8000 r/min的Von Mises应力变形图
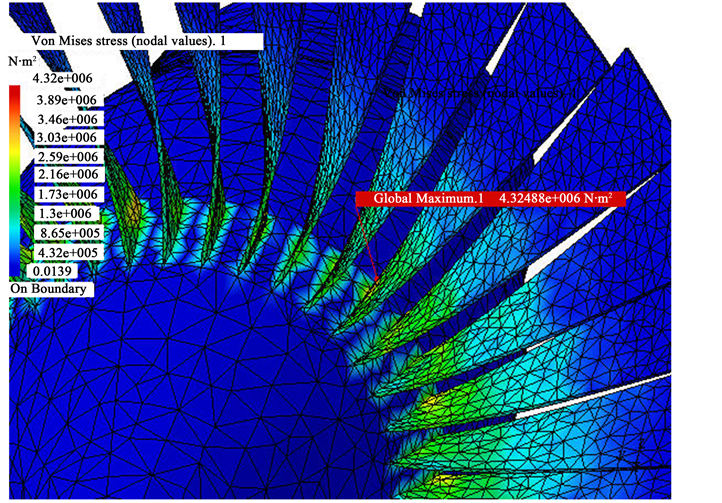
Figure 4. The stress distribution of fan at 800 N∙m
图4. 扭矩为800 N∙m时风扇的Von Mises应力分布
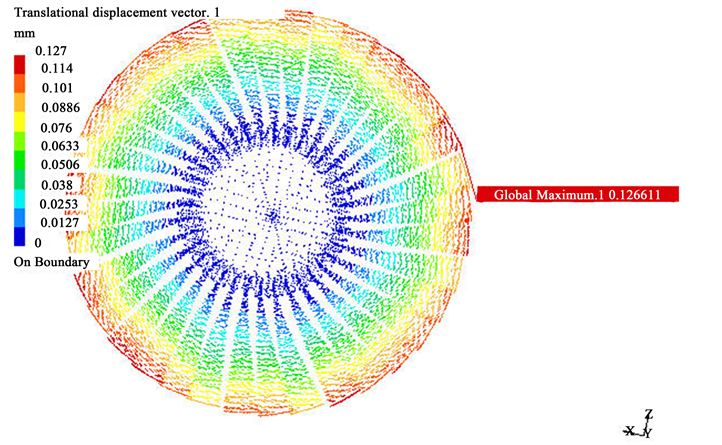
Figure 5. The stress deformation of fan at 800 N∙m
图5. 扭矩为800 N∙m时风扇的Von Mises应力变形
由图4和图5可知,风扇在扭矩为800 N∙m时应力集中在风扇叶片的根部,叶片所受的最大应力为4.32 MPa;变形位移出现在风扇叶片的叶尖,叶片的最大径向位移约为0.127 mm。
同理可知,风扇在扭矩为1189 N∙m时应力集中在风扇叶片的根部,叶片所受的最大应力为6.4 MPa;变形位移出现在风扇叶片的叶尖,叶片最大径向位移约为0.327 mm。风扇在扭矩为1500 N∙m时应力集中在风扇叶片的根部,叶片所受的最大应力为8.11 MPa;变形位移出现在风扇叶片的叶尖,叶片的最大径向位移约为0.237 mm。
综上可得,不同扭矩下风扇的受力情况基本相同,最大应力位置在叶片根部,最大位移变形在叶尖处,额定转速下叶尖的最大径向位移为0.327 mm。扭矩越大,应力越大,受力位置基本不变,额定转速下由扭矩作用引起的应力为6.4 Mpa。
由2.3.2和2.3.3的计算结果可知,风扇在工作时最大应力集中在叶片根部,风扇在额定转速下工作时的最大当量应力为404 MPa,按斯贝发动机应力标准(EGD-3) [3] [4] ,风扇作为航空发动机的关键部件,为防止其发生各种失效故障,首先必须进行叶片的静强度校核。斯贝发动机应力标准规定为在所有正常工作条件下涡轮轮盘的平均周向应力不超过σ0.1的75%,在离心载荷及热载荷作用下内径处的周向应力不超过σ0.1的95% [5] 。本文中,风扇在设计转速状态下的屈服强度是750 MPa,而风扇在额定转速下的最大应力为404 MPa,小于95%的σ0.1,因此在此计算工况下该涡轮盘满足EGD-3的静强度设计要求。
3. 小结
本章利用CATIA自带有限元对CFM56发动机风扇叶片进行了离心载荷下的应力分析,由分析结果可以看出,变形位移最大点位于风扇的叶尖,高应力区在于叶身根部区域。在额定功率下,由旋转离心力所引起的最大Von Mises应力为398 Mpa,由旋转传递的扭矩引起的应力为6.4 MPa,最大应力叠加后为404 MPa。由扭矩作用所引起的应力相对于由离心力所引起的应力而言非常低,风扇在正常工作情况下的应力主要是由离心载荷所引起的。
风扇是民用大涵道比涡扇发动机的关键技术,今后研究的方向有弯掠叶片、带箍叶片和分隔式叶片。降噪、抗外物损伤和叶片包容能力也是大风扇设计中的关键问题 [6] 。关键技术:非定常有粘全三维气动设计技术;大小叶片设计技术;弯掠风扇叶片设计及制造技术;整体叶盘设计及制造技术;二次流控制技术;刷式密封设计及制造技术;金属基复合材料设计。
未来风扇设计是继续提高流通能力、叶尖切线速度和平均级负荷。提高流通能力可以减少发动机进口直径,从而有效地减小发动机重量,提高推重比。其办法是减小轮毂比(d)和提高气流轴向马赫数(Ma)。目前,风扇设计中采用的d为0.34,Ma为0.631。提高叶尖切线速度和扩散因子可以提高级压比,从而减少给定总压比条件下所需的级数并由此减少整个发动机的长度和重量。目前试验研究中的发动机风扇进口叶尖切线速度已达550~600 m/s。通过三维气动设计又可使扩散因子提高0.07。目前,已验证的风扇级压比已达2.0~2.5。
近年来随着计算机技术的普及和计算速度的不断提高,有限元分析在工程设计和分析中得到了越来越广泛的重视,己经成为解决复杂的工程分析计算问题的有效途径,几乎所有的设计制造都己离不开有限元分析计算,主要表现在以下几个方面:
l) 增加产品和工程的可靠性和在产品的设计阶段发现潜在的问题;
2) 经过分析计算,采用优化设计方案,降低原材料成本;
3) 模拟试验方案,减少试验次数,从而减少试验经费。
资助信息
国家自然科学基金(51465047);航空科学基金(2014ZD56009);江西省自然科学基金资助项目(2015BAB207011)。