1. 引言
燃气–蒸汽联合循环由于发电效率高,排放低,启动灵活快速,逐步受到世界各国的重视 [1] 。随着我国联合循环机组装机容量及所占比率的逐步攀升,如何充分发挥其优势,保持机组在最佳状态下运行,成为亟需研究分析的重要课题。性能监测与诊断系统现已广泛应用于燃煤机组,并在实际应用中得到了普遍认可。因此,将燃煤机组的性能监测诊断系统的技术移植到联合循环机组上,必然会对联合循环机组的运行起到重要作用。
由于联合循环机组的控制系统是由燃气轮机的Mark VIe [2] 、蒸汽轮机的DCS和辅助设备的PLC控制系统组成,性能监测诊断系统与它们的数据交互方式较为复杂,同时,这些系统的数据还将和SIS系统、MIS系统共享,因此如何构建一个完整、可靠、有效的数据信息体系极为重要。
2. 联合循环机组的控制系统
2.1. 联合循环控制系统方式
所开发的性能监测诊断系统所针对的“E级燃气–蒸汽联合循环供热机组主要包括两台125 MW的PG9171E型燃气轮机,两台181.4 t/h的双压余热锅炉,一台125 MW的LCZ125型双压,双缸抽凝式汽轮机及一台20 MW的LB19型背压式蒸汽轮机。
该机组控制模式采用“DCS (Distributed Control System,分布式控制系统) + Mark VIe” [3] 模式,相对于GE公司为一整套联合循环机组定制的“一体化ICS (Integrated Control System,集成控制系统)”模式,具有相对灵活方便的特点,并且可以利用煤电机组DCS系统的成熟技术。
2.2. 联合循环控制总体架构
如图1所示,联合循环控制系统构架可分为三层:
最底层是PAS (Process Automation System,过程自动化系统)层,对全厂实时监控,所监测、搜集的数据要传往中间层。PAS层分为两层:底层是现场控制层,该层是全厂自动化控制的基础,负责测量、读取设备各参数并将信息上传;顶层是过程控制层,包括DCS、Mark VIe等系统,负责收集现场控制层上传的数据,并进行计算、分析、显示。
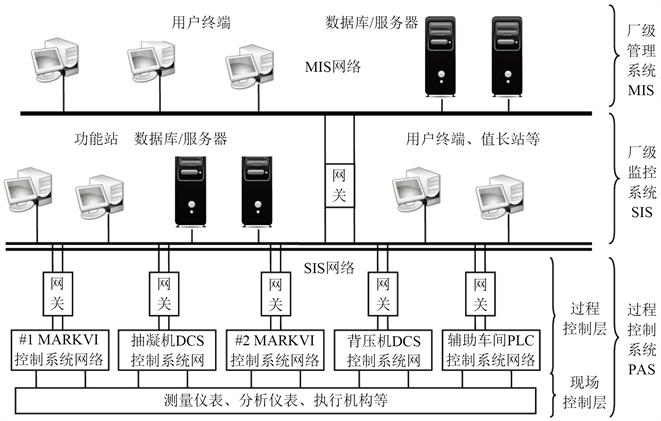
Figure 1. Topology diagram of combined cycle control system
图1. 联合循环控制系统层次图
中间层是SIS (Supervisory Information System,厂级监控信息系统)层,建立在PAS层之上,面向全厂的信息系统,通过整合过程控制层的信息、数据,实现厂级信息共享和实时监测,有效提高厂级管理效率。
最顶层是MIS (Management Information System,管理信息系统)层,负责全厂的管理,包括生产控制系统、运营管理系统、办公自动系统、辅助决策系统等。SIS层的数据会部分上传至MIS层,供其决策参考。
2.3. 测点读数
为监测热力系统的运行状况,每台机组均设置测量分析系统,并设置必要的在线仪表,信号送至DCS或者Mark VIe系统。测量仪表须安装在能读出测点代表性读数的位置,且便于安装维护。以汽水系统为例,每台机组设置1套集中水汽取样分析系统,提供水汽系统的连续取样,并能满足在线仪表分析和人工取样分析的条件,将取样参数和相关信息通过硬接线送至DCS系统,其监视及控制均在DCS系统中完成。水汽取样集中分析装置的每一块分析仪表应能送出4~20 mA DC标准信号。
3. Mark VIe系统
Mark VIe控制系统是GE公司于2004年基于网络化IO、100 MB以太网和Windows系统在原有的Mark Ve系统的基础上研制开发的通用分布式控制系统,该系统也是Speedtronic系列控制系统 [4] 中最新最先进的一个控制系统。从最初的Mark I到如今的Mark VIe,继电器、分列元件逐步为TMR (Triple Modular Redundant,三模块冗余)处理机、Windows系统所代替,可靠性、可利用率、应用适用性、维护便捷性都得到很大程度地提升 [2] [5] [6] [7] 。Mark VIe系统主要对燃机的启动、转速、负荷、排气温度、IGV (Inlet Guide Vane,进口导叶)、燃料等进行控制,对其超速、跳机、灭火、振动等进行保护。其网络结构如图2所示。
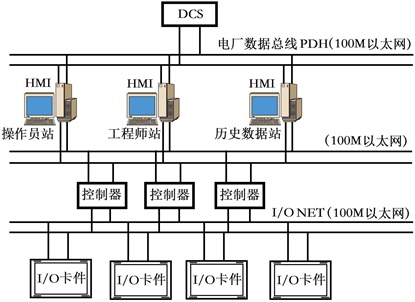
Figure 2. Network structure diagram of Mark VI e system
图2. Mark VIe系统网络结构图
Mark VIe系统最显著的特点就是其TMR结构 [2] ,其工作原理可简单理解为针对每一个测量信号配备三个独立传感器,三个传感器所接收的信号分别输入到三个控制模块中,经表决后输出一个信号。三冗余系统具有很高的可靠性,因为它对所有重要参数都使用三冗余传感器进行测量,这种系统当单信号故障后不会引起控制过程的中断。当三个信号表决时,任何一个错误的信号将被其它两个正常信号所屏蔽,对于开关量则是选择其中一致的信号作为输出,同时系统设计还提供故障信号的隔离功能。由于TMR结构的配置,单个模块的失效或单个通道的故障不会影响到整个系统的工作,且单通道的故障也可即时进行在线修复。
4. DCS系统
DCS系统是以微处理器为基础,全面融合计算机技术、测量控制技术、网络数字通信技术、显示与人机界面技术而成的现代控制系统。其主要特点在于分散控制和集中管理,即对生产过程进行集中监视、操作和管理,而控制任务由不同的计算机控制、完成。总的来说,DCS具有高可靠性、开放性、灵活性、易于维护、协调性、控制功能齐全等特点。也正因其十分显著的优点,大到1000 MW的助理单元机组,小到几十兆瓦的热电联产机组,到处都有DCS在保障其安全运行。
本文所针对的机组所采用的DCS系统在网络通讯方面分为四个不同的层次,分别由四层计算机网络相连,这四层计算机网络分别为:管理层、监控层、控制层、现场层。现场层由类现场总线及远程I/O总线构成,位于生产附近,用于连接远程I/O或现场总线仪表;控制层由位于控制柜内部的柜内低速总线及位于控制柜与人机接口间的高速总线构成,用于传递过程数据;监控层用于连接控制层工程师站、操作员站、历史记录站等人机接口站,传递以历史数据为主的过程监控数据;管理层用于连接各类管理计算机。DCS分层结构示意图如图3所示。Mark VIe和DCS系统的控制对象如图4所示。
5. 联合循环性能监测诊断系统
5.1. 监测诊断系统功能
所开发的机组性能监测诊断系统可实时地对运行参数进行在线监测及诊断。系统根据机组不同的负荷、工况提出重要运行参数的目标值,并根据实际运行参数的偏离情况定量分析对机组经济性的影响,同时通过诊断功能初步确定参数偏离原因,为优化运行提供指导 [8] 。
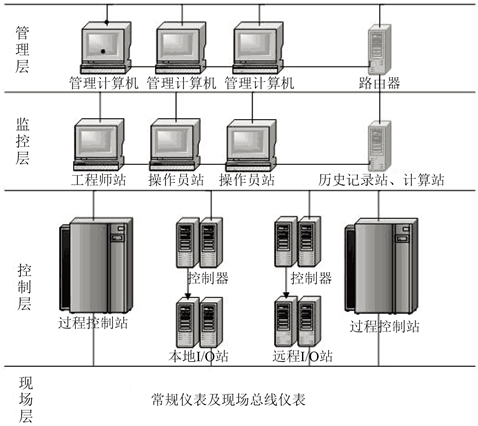
Figure 3. Schematic diagram of DCS hierarchical structure
图3. DCS分层结构示意图
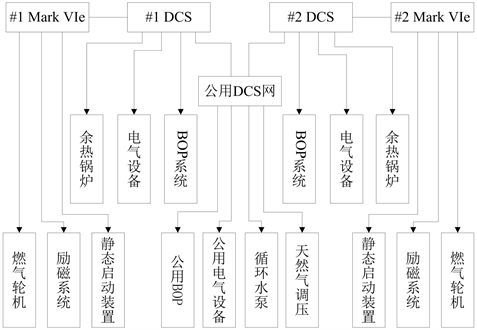
Figure 4. Mark VIe and DCS control object block diagram
图4. Mark VIe和DCS系统控制对象框图
5.2. 性能监测诊断平台OC6000e
性能监测诊断系统以GE新华控制工程公司的高性能、高可靠性的集成控制平台OC6000e平台为依托,该平台是一个建立在分步式控制系统基础上的模块化建模及运行的集成环境,以图形化模块为基本单位,通过模块间输入输出的连接来实现中间数据的传递,如图5所示,以此来构建数据交互和系统分析的整个过程。OC6000e平台现场控制器兼顾功能分布配置,实行硬件物理分散布置、信息集中管理的设计原则,所有处理器模件均冗余配置,一旦出现故障,该模件会被快速找到且报警。控制层网络和IO
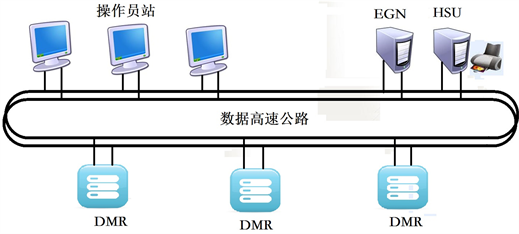
Figure 5. Schematic diagram of OC6000e
图5. OC6000e系统简图
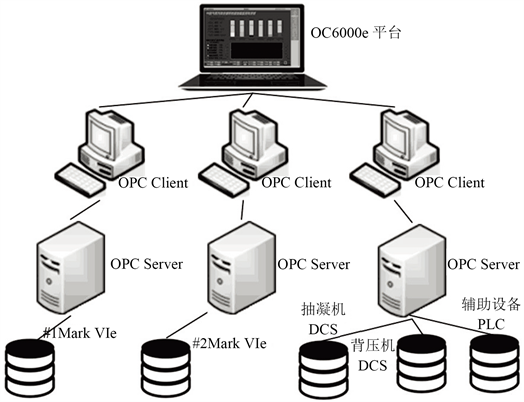
Figure 6. OC6000e data interaction network
图6. OC6000e数据交互网络
网络通过以太网通讯,采用GE公司统一的标准EGD协议,中介和延时大为减少,且所有I/O模块间同步可至1 ms的精度。
5.3. 性能监测诊断系统数据交互
性能监测诊断系统是建立在了联合循环机组过程控制系统之上的在线监测优化系统。OC6000e平台通过OPC (Object Linking and Embedding for Process Control,用于过程控制的对象链接和嵌入)技术读取Mark VIe和DCS系统中的数据,从而进行在线即时计算和分析,得出性能指标和耗差值。OPC技术利用微软的COM (Component Object Model,组件对象模型)/DCOM (Distributed Component Object Model,分布式组件对象模型)技术达成自动化控制的目的,用于向多个数据源通信,包括工业设备和信息数据库。OPC系统主要由OPC客户端和OPC服务器组成,两者通过通信接口进行数据交互。OPC服务器由服务器对象、组对象及项对象三个对象组成,能提供很多接口,而OPC客户端可无需考虑硬件设施的多样性,直接通过这些接口读取与OPC服务器端相连接的硬件设施所收集的数据,排除了不同软件和硬件之间以及不同软件之间的通信障碍。在性能监测诊断系统中,OPC技术可视为OC6000e平台和Mark VIe和DCS系统之间的桥梁和纽带,为电厂数据的存取与再现提供了统一的接口,显著减少数据集成的工作量。如图6所示,在龙游热电厂,3台监控主机分别与现场控制系统连接,其中2台与#1和#2燃气轮机的Mark VIe系统相连接,另1台与各DCS系统连接。控制系统通过专用通信协议将运行数据传输至3台监控主机后,监控主机集成OPC服务器。与3台OPC服务器相对应的是3台OPC客户端,可通过OPC接口读取传输至OPC服务器的Mark VIe和DCS系统收集的燃气轮机、余热锅炉、汽轮机、电气设备、辅助设备等的生产信息,并最终传输至OC6000e平台汇总。
6. 结论
1) 深入分析了“DCS + Mark VIe”控制模式的特点与整体结构、DCS以及Mark VIe系统在技术、经济上的综合优势;
2) 讨论了龙游热电厂性能监测诊断系统的数据传输模式,以COM/DCOM技术为基础的OPC系统,为数据源定义了统一开放的接口标准,为性能监测诊断系统开发中遇到的数据交互问题提供了新思路,能够切实结合组件技术与组态技术,实现在线动态组态。