1. 引言
众所周知,要设计并制造一辆完整的汽车是一个很复杂的过程。而FSAE中国大学生方程式汽车大赛要求一个大学生车队在一年之内设计并制造一辆小型并具有方程式赛车的操纵性能的较高性能的赛车。一个车队通常需要八到十二个月的时间来设计、制造、测试、准备和调试赛车,它极大的考验了车队队员们的设计能力和动手能力以及解决问题的能力。
而本文正是结合了在车队的实际工作,来为我们2016年的赛车设计并制造一套表现较为出色的排气系统,同时解决排气管的制造工艺以及性能评价等问题。
2. 绪论
2.1. 赛车排气系统与民用汽车排气系统性能比较
高性能表现赛车的排气系统的设计以及性能取向与民用汽车的排气系统很不一样。但排气管具有的最主要的作用还是为发动机排出废气保证发动机的正常工作并隔绝发动机产生的高温废气。对于民用汽车而言,考虑到制造成本问题,往往使用易于大量生产的材料进行排气系统的制造,而且在设计上也尽向节约成本的方向靠拢,并考虑国家的法律法规,还要考虑到尾气排放以及噪音的问题。而赛车的排气系统则恰恰相反,赛车对发动机的性能表现有很高的要求,如图1,赛车排气系统常常使用的是比较不易于量产的工艺以及材料。
而且从设计上来说,由于赛车排气系统使用的是费时又费力的制造工艺,所以在设计方面就没有什么限制,这样可以让设计者向着充分发挥发动机的工作性能的方向去自由发挥。
在排气系统的设计中,最重要的一个部分就是对于排气歧管的设计,既要考虑到利用发动机产生的废气的惯性来提高排气效率以及充量系数,从而获得更大的功率和扭矩。还要防止四个缸排出的废气相互干扰,所以要计算排气歧管的长度,并且保证四个缸的歧管长度相等,因为发动机在高速运转下的排气速度是极快的。
2.2. 赛事对排气噪音的要求
1) 赛车排气系统上必须安装有消音器。
2) 排气出口位置必须设计合理,使得赛车无论以任何速度行驶,车手都不会受到赛车尾气污染。
3) 排气系统最终出口不得处于后轴中心线后450 mm以外的位置,同时其离地距离不得高于600 mm。
4) 噪音等级上限,空挡时噪音等级上限为100 dB加权分贝。其他速度时噪音等级上限为110 dB [1] 。
3. 排气系统基本原理
3.1. 排气系统的作用
汽车排气系统最重要的作用就是将发动机排放的废气给排出发动机。
3.2. 排气系统设计理论
内燃发动机的工作主要是一个气体循环的过程,不同的配合会对发动机的性能产生很大的影响。本文主要讨论的是对排气系统的设计来对发动机的性能进行提升。
3.2.1. 压力波在管道中传播的特性
根据压力波在管道中传播的原理,当正压力波遇到管道开口端时,会向传播方向相反的方向反射一个负压力波,当正压力波遇到管道闭口端时,会向传播方向相反的方向反射一个正压力波;反之,当负压力波传播到管道开口端时,会向反方向反射一个正压力波,当负压力波传播到管道闭口端时,会向反方向发射一个负压力波 [2] 。
将发动机排气冲程看作是四冲程的第一个冲程,排气门打开时,气缸内是自由排气状态,根据压力波在管道中传播的原理,排气门附近产生一个正压力波,正压力波向排气出口方向传播,在遇到下一个管道端口时,反射一个负压力波向反方向传播。这时,如果排气管道的长度设计得合理,就能利用负压力波在排气门第二次打开时回到排气门附近,这时,就能利用负压力波的真空效应,将气缸内的废气抽出,这是提高排气效率的一个极为有效的方法。
3.2.2. 波动效应在排气歧管设计中的应用
为使赛车发动机的性能得到更大的提高,就要极为有效的来利用气体的波动效应来对排气歧管进行设计。
由于发动机在不同的转速条件下,废气排出的速度是不同的。根据比赛的情况,CBR600发动机7000~9000转是常用转速区间,所以,对于排气歧管的设计参数是根据8000转来确定的。
由于四冲程发动机本身有一个气门重叠角,这时候,根据CBR600发动机8000转时设计的排气歧管长度恰好能使歧管内发射的负压力波传递至排气门附近,这时就能极大的提高排气冲程的排气效率 [3] 。
4. 排气系统形式选择
上海工程技术大学2016年赛车使用了HONDA CBR600RR赛用摩托发动机,直列四缸,压缩比为12.2,排量为599 cc,最高马力:120 ps/13,500 rpm,最大扭力:6.73 kg-m/11,250 rpm。
4.1. 四出二排气形式
图2这种排气形式的优点就是较为简单,排气系统有两个出口,能够较大程度的减少气缸排出废气的相互干涉问题。但四出二的排气形式需要更多的管材来搭建排气系统,而且还要使用到两个消音器,这样增加了不小质量。
4.2. 四出一排气形式
图3的布置是直接将四个排气歧管的末端通过一个集合器合并到一根总管,其最大的优点就是使用的管材量最少。但这种排气形式在集合器处会发生较为严重的干涉问题。
4.3. 四出二出一排气形式
图4的排气形式就是将每两个工作情况相对应的气缸的排气歧管末端合并成两根二级歧管,再将这两根二级歧管给合并成一根总管,最后连接消音器。这样的排气形式就可以较为有效的解决集合处废气互相干涉的情况,而且使用到的管材也相对较少。
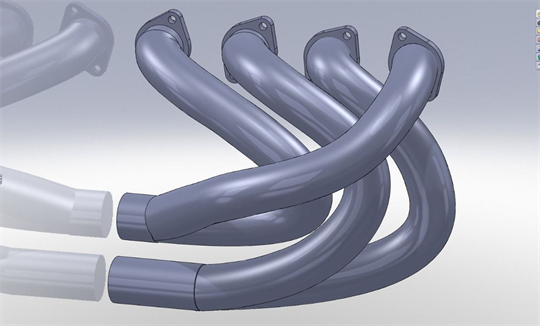
Figure 4. Four-two-one exhaust system
图4. 四出二出一排气形式
4.4. 排气形式选择
考虑到排气系统的轻量化、背压问题、干涉问题、噪音问题、制造加工等许多综合因素,设计方向最终确定为四出二出一的排气布置形式。
5. 排气系统设计
5.1. 排气歧管参数计算
排气歧管最基本的参数就是歧管的长度和歧管的直径。计算方式如下:
P3M排气歧管长度(inch)
ED:180˚ + 排气气门早于排气行程下止点开启曲轴转角(度)
RPM门早于发动机优化目标转速(rad/min)
P2.排气歧管长度(inch)
CC歧管发动机排量(cm3)
ID排气歧管内径(inch)
根据上面的公式 [4] 计算得以CBR600发动机在8000转的工作状态下的优化目标转速算得的P = 15.36 (in),ID = 1.18 (in)
5.2. 排气歧管法兰设计
由于排气歧管头段和发动机排气口的连接是靠发动机体上的丝杆,所以必须在排气歧管的头段焊接法兰来将排气歧管固定在发动机上。另有一个法兰将排气总管分为两段,这样便于安装和拆卸。
设计图如图5所示,总管法兰设置有四个螺栓孔,以方便尾段排气总管的角度调整。
5.3. 排气系统材料选用
考虑到排气系统使用到不同的金属管材对排气效率的影响以及对整车质量的影响,对于材料的选择还是进行了慎重的比对。
首先考虑304不锈钢管材,因为其耐腐蚀程度以及韧性都比较好,304不锈钢含8%左右的镍而403不含镍 [5] 。但是,其密度高,考虑到做全段排气系统的搭建,对整车的轻量化没有任何好处。
其次就是钛合金管材,主要考虑的是TC4钛铝合金,因为TC系列钛合金切削性能好,方便排气系统搭建时的手工加工,较于纯钛,其抗氧化性能好,硬度高,其耐高温效果也好。而且钛合金的质量轻,相比于使用全段不锈钢管,钛合金排气系统的质量仅仅是前者的七分之二。
综合所有因素考虑,排气系统的搭建最终选择了钛合金为搭建管材。
5.4. 排气系统模型构建
根据发动机四个气缸的点火顺序是一二四三,所以可以确定当一号缸在做排气冲程时,四号缸正好在做压缩冲程,将这两个气缸的歧管合并至一根二级歧管的话,可以最大程度上的避免它们之间在排气时有相互干涉的情况。二号和三号缸也如此。
模型如图6。
6. 排气系统设计分析
6.1. GT power软件对排气系统整体形式分析
在GT power软件里进行建模仿真以验证这种排气形式的可靠性。建模过程中所有发动机参数都根据CBR600发动机的参数设定,而排气系统的参数也使用设计时所确定的排气系统参数,进气系统的参数,使用的是今年赛车所设计的进气系统模型。
从图7中可以看出,这是按照CBR600发动机建立的一个直列四缸发动机,每个缸体容积为149.75 ml,压缩比为12.2。因为主要考虑的是这种排气形式是否能够较为有效的利用到发动机废气的波动效应,所以使用这个GT power模型主要分析的是排气歧管中的气体压力波动。
从图8中可以看出,这是一号缸的排气歧管排气门附近压力波动图,图中的波线是较为有规律的上下波动的,但在排气门附近的波峰位置还有些许不稳定,这是因为发动机在高速工作的情况下,排气口排出气体速度可能会发生偶尔的不匀的情况,也有可能是歧管合并处的接口形状导致的。
从整体上来看,压力的波动是较为均匀,有规律的,波峰波谷的位置也相差不大,没有紊乱的波线可以说明干涉的情况基本没有过多的发生。
6.2. ANSYS分析
ANSYS速度云图分析
从图9中可以发现,四个缸的排气门打开时,歧管头段的截面流速都是不均匀的,这是因为排气歧管在于发动机装配的头段就是弯曲的,这样才能保证排气系统的装配不与车架干涉,但是这段弯曲是对发动机的排气效果有影响的 [6] ,但是为了保证排气系统成功装配,只能够对这段弯头进行优化。
对歧管头段的弯头角度进行了改进,使得弯头在不影响排气系统装配的条件下,使其半径增大,这样能对气体流速问题起到较为合适的调整。
图10是改进后的截面气体流速分布图。
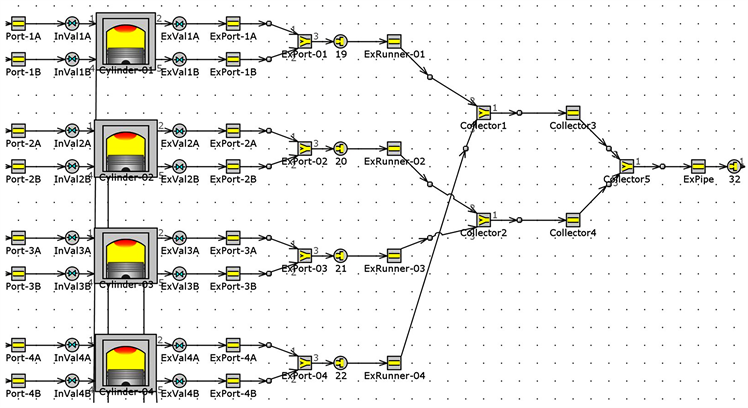
Figure 7. GT power engine modeling
图7. GT power发动机整体建模
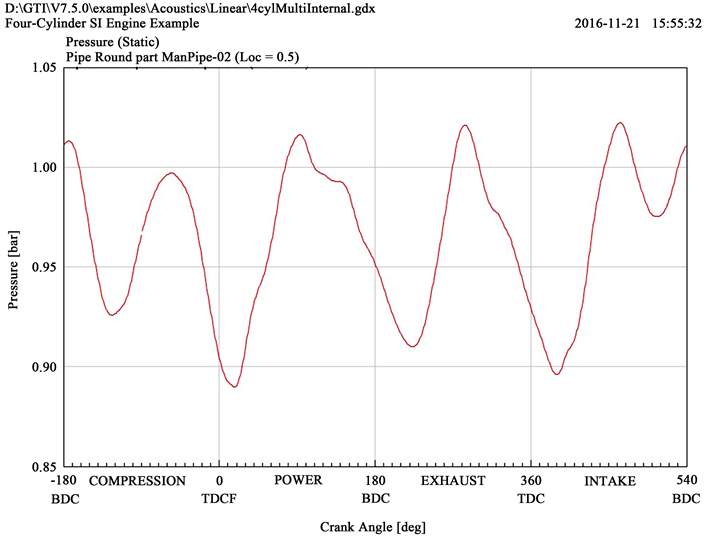
Figure 8. Simulation fluctuation diagram of exhaust pressure of No.1 cylinder
图8. 一号缸排气压力仿真波动图
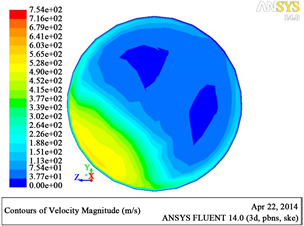
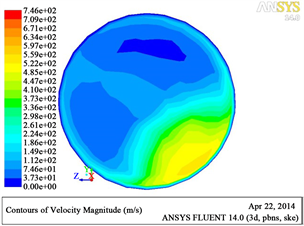
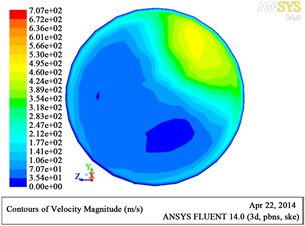
Figure 9. Velocity profile of section from 1 to 4 cylinder
图9. 一至四号缸截面速度云图
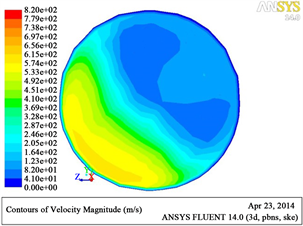
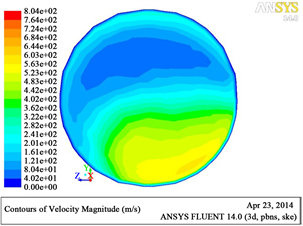

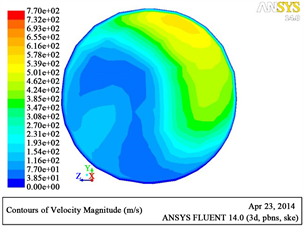
Figure 10. Improved velocity profile of section from 1 to 4 cylinder
图10. 四号缸改进后速度云图
7. 排气系统加工制作
7.1. 排气管弯头制作
由于购买的材料都是已加工好的钛合金弯头与直管,弯头与直管都有不同内径的,如图11弯头也分别有不同角度。所以对其进行加工,改变弯管与直管的接合处角度,这样才能搭出与模型中一致的排气系统。
在弯头制作时首先要根据几何关系计算需要切掉的角度(如图12),以及在弯头上切口的方向,另外使用到专用的弯管画线工具。
7.2. 排气管初步搭建
如图12加工完成的排气歧管在发动机上进行初步的搭建,使用透明胶作为固定材料,并标记了各段弯管和直管的配合关系。
7.3. 排气管焊接
首先是法兰盘与排气管的焊接,只有焊接完成法兰盘,才有办法将排气系统安装至发动机上。完成的排气总成如图13~图15。
测试状态如图16。最终完成的整个排气系统与赛车其他部件的配合都较为完美,不存在干涉的现象,而且与模型的形状参数一致,可以说排气系统的制造过程较为成功!
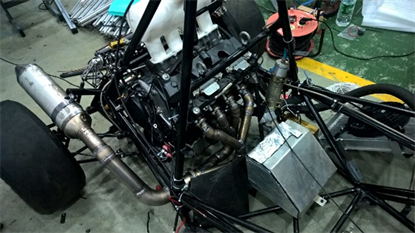
Figure 15. Exhaust system installation completed
图15. 排气系统在赛车上的安装
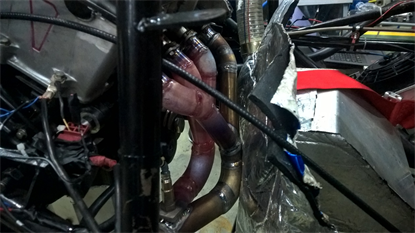
Figure 16. Exhaust system testing in the racing car
图16. 排气系统在赛车进行试验
8. 结论
通过对赛车整个排气系统的从设计到制造到实验的过程,较为良好的实现了最初的优化目标。本文主要完成的任务有:
1) 收集各方面关于排气原理以及优化案例的资料。
2) 根据赛规要求,完成排气形式的选择,根据资料对排气管的参数进行计算并得出结论。
3) 使用SolidWorks软件对整个排气系统进行建模。
4) 使用ANSYS及GT power等仿真软件对模型进行分析,通过分析得出的结果对原模型进行修改。
5) 对最终冻结的方案进行加工制作,并完成排气系统成品。
6) 完成排气系统的实际使用测试。