1. 引言
气力输送技术起源于19世纪上半叶,具有密闭、安全、清洁、易实现连续自动化操作等优点,在能源、化工、冶金、医药和食品加工等领域运用非常广泛,但主要以稀相输送为主。由于稀相输送的输送速度较快,物料及管道磨损严重,需要的输送气量大,动力消耗高,因此,具有高输送固气比、低能耗等优点的密相输送技术近年来得到广泛关注 [1] [2] [3] [4] [5] 。利用粉体的“流态化”特性进行输送的流化罐式气力输送是实现密相输送的有效措施之一,流化罐式气力输送所消耗的能量比粉体未流化时要小得多,同时具有输送固气比高、输送速度低、构造简单、维护方便等优点。流化罐输送出料方式有两种基本形式:上出料式和下出料式。不同出料方式及流化罐内物料的流化状态,对输料的稳定性、输送能力以及输送固气比等特征参数都会产生影响 [6] 。至今,对于上出料式流化罐密相气力输送系统的特性已有较多研究 [7] [8] [9] ,但有关下出料流化罐密相气力输送系统的研究报道较少,而关于不同出料方式的发送料特性的研究则鲜有报道 [10] [11] 。
气力输送系统是利用安装在其起点的空气压缩机,将高于大气压的空气通入供料装置中,与粉料混合后进入管道并输送到终点的收粉罐内,空气经过滤后排放到大气中。在流化罐内,流化气体通过流化罐底部气体预分布室及气体分布板进入罐内,稳压气体经发送罐顶部加入料罐,在密闭的发送罐中,稳压气一部分用于消除由于粉料位下降而造成的罐内压力下降,维持正常输送时发送罐的压力平衡,另一部分则穿过粉料层经提升管进入输送管路。料层处于流动的气流中,既受到了气流的静压推动,又将气体的动能转化为粉料的动能,当气流速度小于粉料下落速度时,粉料呈下落状态;当气流速度等于粉料下落速度时粉料在气流中呈现不上不下的浮动状态,这时的气流速度称为该粉料的悬浮速度;当气流速度大于粉料的悬浮速度后,粉料就会随着气流流动从而进入出料管开始输送。
本文的目的是研究流化罐发送料的特性,考察流化罐罐压、顶部稳压气量与底部流化气量及不同出料方式的发送料特性。
2. 实验原料及装置
2.1. 实验用原料
首先测试了表征粉料流态化特征的基本参数,包括松装密度、振实密度、真密度、休止角、崩溃角、分散度、霍尔流动性等。实验用PVC粉的基本参数,如表1所示。
2.2. 实验装置
为了研究流化罐式发送料及不同出料方式的输送特性,设计制作了模拟粉料喷吹的流态化输送实验系统,如图1所示。包括上出料和下出料两种方式,流化罐上、下出料带压密相气力输送系统均由气源系统、料罐系统(包括流化罐和收粉罐)、输送管道系统、测量传感器和数据采集及控制系统四部分组成。两种输送系统除采用不同的初始出料管道外,其余部分都相同,输送系统流程如图1(a)所示为上出料输送系统的示意图,图1(b)是下出料输送系统的示意图。
气源系统由空气压缩机、稳压阀、空气干燥净化机和储气罐组成。空气经过空气压缩机、稳压阀和空气干燥净化机进入储气罐,为实验提供高压输送气体。
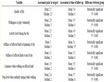
Table 1. The basic parameters of PVC
表1. PVC粉的基本参数
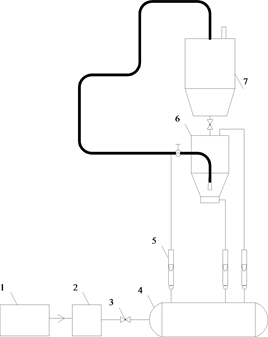
(a) (b)1,空压机; 2,空气干燥净化机; 3,稳压阀; 4,储气罐; 5,转子流量计; 6,流化罐; 7,收粉罐
Figure 1. Schematic setup of the pneumatic conveying experiment facility. (a) Lateral discharge; (b) Bottom discharge
图1. 上出料和下出料的流化罐发送料实验装置示意图。(a) 上出料,(b)下出料
料罐系统包括一个容积为0.236 m3,高1 m的流化罐和一个容积为0.566 m3,高1.6 m的收粉罐,两个料罐均可以承受一定的压力,被两个输送系统所共用。流化罐底部设有流化气,通过料罐底部气体预分布室及气体分布板流化煤粉,被流化的煤粉具有流体特性,易于流动和输送,稳压气从流化罐顶部吹入,其中一部分用于稳定流化罐压力,一部分用于置换被发送出流化罐的粉料空出来的体积,锥部加压气从流化罐锥部以多管环形方式导入。下出料输送系统流化罐底部气体分布板中心开有一孔,输料管通过分布板中心孔从流化罐底部伸出。上出料输送系统流化罐底部气体分布板上则没有小孔,输料管的出料口在分布板上部向上延伸,通过弯管从流化罐侧面伸出罐外。收粉罐顶部装有布袋,输送过程中,布袋与大气相通。
输送管道是内径为35 mm的有机玻璃管,出料口附近弯管是曲率半径为200 mm的有机玻璃管,其余弯管是曲率半径为200 mm的铁弯管,上出料输送管道总长约14 m,下出料输送管道总长约16 m。下出料管路系统相对于上出料有所不同:增加了两个竖直管段,其一是与下出料管相连的下降管约300 mm;其二是下水平管向上转弯后与上水平管相连的竖直管增加了约1400 mm。输送管道的水平段、垂直段、水平弯管段和垂直弯管段分别布置了相距1 m的两个测压孔,以测量和计算相应位置的压力和压差。在流化罐不同高度位置及分布板上部和下部也设置了测压孔。流化罐的支架底座下部布置了电子秤,精度为0.2%,以计量罐内煤粉的重量变化,得到喷粉量。流化气量、稳压气量、二次补气量采用玻璃转子流量计测量。
实验过程中,压力、重量等由传感器测量经数据采集系统被记录保存,形成原始实验数据,数据采样频率为200 Hz,数据输出频率为1 Hz。
3. 结果与讨论
3.1. 稳压气量与底部流化气量之比对喷粉量和固气比的影响
流化罐罐内压力与送入罐内的气体量(稳压气体量和底部流化气体量)密切相关,在此实验过程中,二次补气量保持4 m3/h不变,稳压气量与流化气量之和保持不变,即在维持流化罐内压力稳定的情况下,改变二者比例。如图2和图3所示为稳压气量和流化气量之比与粉料喷吹量和固气比的关系。
从图2和图3可以看出,喷吹量和固气比随顶部稳压与底部流化之比的变化趋势是一样的,随着顶部稳压气量的减小、底部流化气量的增加,喷吹量和固气比先增大后减小,在顶部稳压:底部流化 = 2:8时达到最大,分别为2718 kg/h和110 kg/kg。在稳压气量较小流化气量较大时,一部分流化气量代替稳压气量用于补充料位下降造成的罐内压力下降,所以气体分布板上粉料的流化效果较差,单位体积气体的输送能力较小,喷吹量和固气比较低。在稳压气量增大过程中,一部分从粉料层穿透至提升管入口附近,经提升管进入输送管道,起到输送风的作用,气固两相流出口速度增加,粉料质量流量增大;此时流化气量不再代替稳压气量用于补充压力所以粉料的流化效果好转,单位体积气体的输送能力增大,固气比增大,并在稳压气量:流化气量为2:8时粉料喷吹量和固气比达到最大。继续增大稳压气量减小流化气量,粉料流化效果越来越差,粉料质量流量开始呈现逐渐减小的趋势,固气比也随之降低。
3.2. 流化罐罐压对喷粉量和固气比的影响
在实验过程中,气力输送管路上的二次补气量稳定为4 m3/h、流化罐顶部稳压气量和底部流化气量之比为2:8,通过改变上出料输送系统中充入流化罐内的顶部稳压和底部流化气体量之和调节流化罐内压力,收粉罐出口与大气相通。图4和图5为流化罐压力与粉料喷吹量和固气质量比的关系。粉料喷吹量(即质量流量)是单位时间内流化罐发送出来的粉料质量,是表征该气力输送系统输送能力的参数。固气比是输送管道内粉料质量流量与气体质量流量之比。
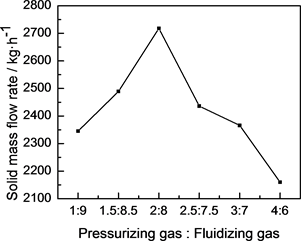
Figure 2. Solids mass flow rate vs. Pressurizing gas /Fluidizing gas ratio
图2. 稳压与流化气量之比与粉料喷吹量关系
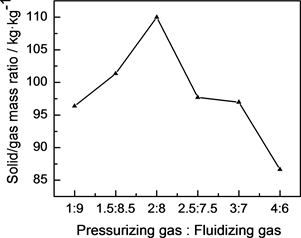
Figure 3. Solids/gas mass ratio vs. Pressurizing gas /Fluidizing gas ratio
图3. 稳压与流化气量之比与固气比关系
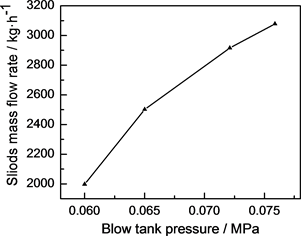
Figure 4. Solids mass flow rate vs. conveying pres- sure
图4. 流化罐罐压与粉料喷吹量关系
从图4和图5可以看出,流化罐罐内压力对喷吹量和固气比的影响是很大的。由图4、图5可以看出,随着流化罐罐压的增大,喷粉量持续增大,而固气比先急剧增加后增加不明显。这是因为,一方面流化罐罐压的增加直接提高了流化罐和收粉罐之间的输送压差,粉料受到的驱动力增加,促进了粉料的
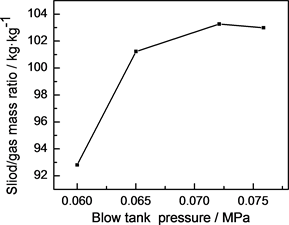
Figure 5. Solids/gas mass ratio vs. conveying pressure
图5. 流化罐罐压与固气比关系
流动,另一方面是由于流化罐的压力增加,气相密度提高,这样也增加了作用在粉料上的曳力,对流动也起到了促进作用。
3.3. 上出料和下出料发送料特性比较
3.3.1. 粉料移动和出料特性
图6是气力输送过程中流化罐内粉料料面下降的实拍照片。从图6可以看出,喷粉罐内粉料是典型的漏斗形下降,中心气流发达,随着料层降低,料面逐渐趋于平坦均匀。
图7是上下出料系统气固流动出料情况示意图,从流化气体与固体粉料的作用上来讲,在罐内压力的推动下,上出料方式可有效利用流化气体的向上动能和对粉料的曳力携带粉料进入上出料管(如图7中(a),出料比较均匀,不易堵塞,在适当的二次补气作用下实现稳定输送;而下出料方式,一方面,出料漏斗对向上的流化气体有一定的阻扰,同时,粉料流需完成180˚的反向进入下出料口(如图7中(b)),由于流动方向的改变,气固的撞击作用需要消耗比上出料更高的气体动能;另一方面,进入下出料口的粉料,由于气体动能和压力能的推动加上粉体自由下沉的重力作用,粉料下降弯管处受到的挤压高于上出料弯管,容易造成壅堵,增加出料阻力,需及时补充二次补气保证正常出料和稳定输送。所以,如果实际需要采用下出料,一方面,可以提高输送动力(压差)来提供更大的驱动力;另一方面,建议在距下出料管出口0.5 m左右处增加二次补气,避免下料管集料堵塞。
3.3.2. 粉料发送特性
在上下出料方式比较实验过程中,应用了两种比较方式来进行,一是两种输送方式均保持相同的流化气量和稳压气量,如表2中的上出料和下出料Ⅰ所示;二是保持上下出料输送系统的流化罐罐内压力相同,如表2中的上出料和下出料Ⅱ所示。在保持流化气量和稳压气量相同,即上下出料方式实验过程中均保持顶部稳压流量:底部流化流量 = 2:8,顶部稳压流量 + 底部流化流量 = 12 m3/h,二次补气流量为4 m3/h的情况下,由于出料方式的改变、出料管局部阻力和输送管路系统的变化导致流化罐内的压力不同,上出料罐内压力为0.07 MPa,而下出料罐内压力增加为0.08 MPa;为保证流化罐罐内压力相同,需将下出料稳压气量和底部流化气量之和调整为了6 m3/h (比例保持2:8不变),这样下出料罐内压力也稳定为0.07 MPa,二次补气量保持为4 m3/h不变,其喷粉量和固气比见表2。
在上述各操作参数条件下,流化罐发送料和管道输送均能稳定进行。从表2可见,在相同的流化罐罐内压力(0.07 MPa)下,上出料输送方式的喷粉量远高于下出料输送方式,而由于下出料方式的流化气体量降低,表现为下出料气力输送的固气比大于上出料。从表2还可以看出,在流化气体气量相同的情况
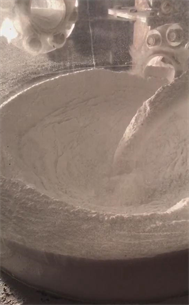
Figure 6. Solid flow way of the lateral discharges
图6. 流化罐内料面下降实物照片
(a)
(b)
Figure 7. Gas-solid flow way of the different discharges. (a) Lateral discharge; (b) Bottom discharge
图7. 上下出料系统气固流动出料情况示意图。(a) 上出料,(b)下出料
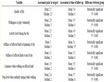
Table 2. Conveying characteristics of different discharge types
表2. 不同出料方式发送粉料情况比较
下,下出料的罐内压力比上出料的罐内压力高,从0.07 MPa增加为0.08 MPa,下出料方式的喷粉量和固气比均高于上出料方式,这主要是因为下出料流化罐罐内压力的增加引起喷粉量增加,与前述2.2节的实验结果一致。
图8为上出料和下出料两种方式的流化罐重量随时间的变化情况。由图8可见,在相同的罐内压力(0.07 MPa)的条件下,下出料流化罐发送料从启动到稳定需要的时间明显比上出料需要的时间长,发送相
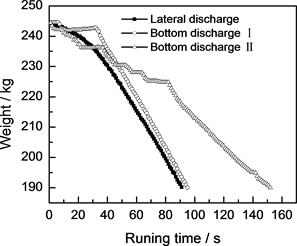
Figure 8. Time history of solid mass in discharge blow tank
图8. 喷吹罐内粉料质量随时间的变化
同质量的粉料(60 kg),下出料所用的时间比上出料多约三分之一。由图8还可见,当流化气量相同(上出料罐内压力为0.07 MPa,下出料罐内压力为0.08 MPa)时,下出料由于下降管中有积料,发料启动需要的时间比上出料的时间长,发送相同质量的粉料(60 kg)所用时间,下出料方式约长于上出料方式。
3.3.3. 出料管的局部阻力特性
此处出料管的局部阻力特性是指从流化罐内出料喉口至二次补气装置前的出料管段的局部阻力及局部阻力系数。流化气体携带粉料流过弯管的压损,可以表示为弯管中纯空气的压损与输送粉料的附加压损之和。纯空气流经弯管的压损,可以表示为
(1)
式(1)中,
是标况下弯管中空气密度,u是标况下弯管中的流速。对于光滑弯管,空气压损系数ξ与雷诺准数Re、弯曲角和R0/D(弯曲半径与管道直径之比)有关。可用下式求得 [12] :
(2)
(3)
其中:θ0是弯管的弯曲角(度);b为系数,根据弯曲角确定。
本研究中,弯管
,
,所以,
。
对于流化罐罐压为0.07 MPa的上出料和下出料以及流化罐罐压为0.08 MPa的下出料,在标况下,
,可得空气流经出料管的局部阻力系数为:
。
输送物料的附加压损为粉料颗粒进入弯管后受离心力的作用在外侧壁附近滑动,并与管壁反复冲击而损失动能,为此通过弯管后要求气流给予加速,该压损要比相应的直管大得多。假设冲击以后,颗粒在空气阻力、离心力、重力作用下,以定速沿外侧壁做圆周运动,引起的附加阻力可表示为 [12] :
(4)
则总压损可写为:
(5)
式(4)和(5)中,λ是输送物料时的附加阻力损失的表观阻力系数;
是固气比。
将实验过程中测得的流化罐罐内至二次补气前的压力差
和计算得到的
分别代入式(5)中,计算得到:上出料发送粉料时的附加压损的阻力系数
;下出料的附加压损的阻力系数
和
。由此可见,下出料出料管的局部压损和局部阻力系数均大于上出料。
4. 结论
综上所述,通过实验研究流化罐罐压、顶部稳压气量与底部流化气量及不同出料方式的发送料特性,得出结论如下:
1) 随着流化罐压力的增加,喷粉量持续增加,固气比先急剧增加后趋于缓慢;
2) 喷粉量和固气比随加压流量与流化流量之比增加均是先增加后减小,在2:8处均达到最大;
3) 在相同流化罐压力下,上出料方式的喷粉量大于下出料;
4) 在相同流化罐压力下,发送相同质量的粉料,下出料所用的时间比上出料约多三分之一;
5) 下出料出料管的局部压损和局部阻力系数均大于上出料。
基金项目
国家自然科学基金项目资助(51374263, 51674052)。