1. 引言
宝钢炼铁厂原料单元煤场承担着公司内所有焦煤、动力煤和大部分喷吹煤贮存、输送任务。该煤场始建于上世纪80年代,共有10个料条(含干煤棚2个料条)和10台堆、取料设备(含干煤棚1台堆取料机),理论储量约77万吨,受品种等因素的影响实际储量为60万吨左右。
煤场除干煤棚内两个料条外,其余全为露天存放。受风力、雨水等影响,造成煤场扬尘及雨水冲刷形成的料堆塌方、排水夹料等,环境污染严重、物料损耗率高 [1] 。
为减少露天堆放的负面影响,宝钢炼铁厂采用防尘网、定时洒水、喷洒表面凝固剂等多种方式来减少现场扬尘和物料损耗 [2] ,但是抑尘效果容易受到天气影响,发生反复。
近年来,煤筒仓逐渐在钢铁行业中得到应用,采用筒仓贮煤可以大大提高单位面积的堆存量,而且在降低贮煤的损耗、改善环境方面也有较好的效果。
2. 改造内容与目标
2.1. 改造内容
本工程改造和新建的工艺设施包括:筒仓输入系统、筒仓本体设施及筒仓输出系统三部分。工艺流程详见图1。
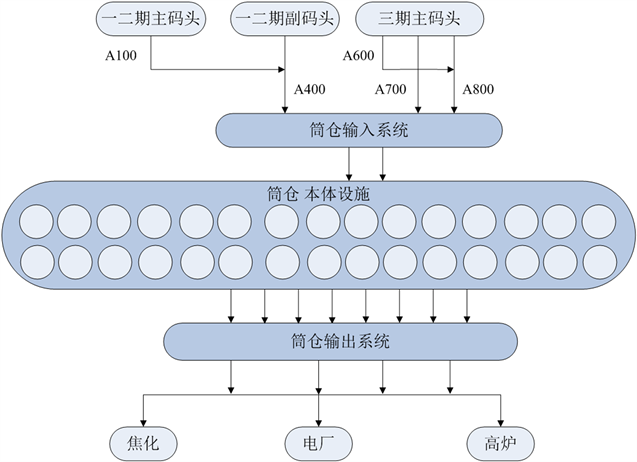
Figure 1. Process flow chart of silo cluster storage
图1. 筒仓贮存工艺流程图
1) 筒仓输入系统:包括一二期主码头、一二期副码头、三期主码头到煤筒仓的3个工艺流程。一二期主、副码头来煤不能同时进入筒仓,最多2个输入系统同时进入筒仓。其中,一二期主码头和三期主码头胶带机输入系统输送能力为3600 t/h,一二期副码头胶带机输入系统输送能力为1200 t/h。
2) 筒仓输出系统:包括煤筒仓到一二期焦化、三期焦化、电厂、高炉的4个工艺流程,系统能力为1200 t/h。
3) 筒仓本体设施:煤场E、F料条中分步建设两排筒仓,每排15个,共计30个。仓体直径(内径)为24 m,仓顶高度46 m,单个筒仓最大贮量约1.4万t,采用钢筋混凝土结构。① 筒仓顶部的输入系统:物料通过输入系统胶带机输送到筒仓顶部后,经移动可逆胶带机向筒仓顶部的布料胶带机供料,再经卸料车将煤卸入指定的筒仓。② 筒仓底部的输出系统:仓下采用旋转卸料机排料,单个筒仓下部设置有2个供旋转卸料机行走用的通道,旋转卸料机可在通道内往返行走,旋转卸料机采用变频控制,每台旋转卸料机排料能力设定为700 t/h、850 t/h和1200 t/h三档,筒仓卸料时单台旋转卸料机作业。
2.2. 改造目标
1) 改善煤场区域环境:通过将煤场E、F料条改建成筒仓型式,可以有效减少该区域内的物料扬尘、暴雨天气的物料流失以及减轻对周边大气及河流的环境污染。
2) 节能降本:改建后省去了露天贮煤洒水抑尘的环节,同时减少了降雨影响,有效降低物料的含水率,从而降低用户的生产能耗。用筒仓储煤估算可降低物料水分约3%。此外,使用筒仓贮存物料可以有效降低因大风大雨造成的物料流失,估算可降低物料损耗约0.15%。
3) 煤筒仓与原先的堆取料机作业相比,可以提高劳动效率、降低工作强度。
3. 项目改造过程管理
3.1. 物流保障策略
筒仓施工期间,CE/CF料条停用、CA料场避让出8米左右的通道;9#堆料机停用、1#取料机作业范围从双边减为单边且单边作业面积下降60%,10#堆取料机作业范围从双边减为单边且单边作业面积下降82.5%。受上述情况影响,煤场输入系统能力下降约30%、贮存能力下降约26%、输出系统能力下降约28% (详见表1)。
为确保焦炉、电厂和高炉的正常生产,通过输送系统能力和安全库存天数测算、与相关部门协调,制定了相应的物流保障对策:
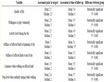
Table 1. The influence of silo construction on the storage and transport capacity of the coal yard
表1. 筒仓施工对煤场贮存和输送能力影响测算
注:计算依据《2013年原料生产技术年报》。
1) 堆取能力:
① 在台风、雨季和冬季期间,为确保用煤安全性,租用宝钢原料码头附近的罗泾港备8~10万吨煤,确保煤库存满足安全天数的要求。
② 调整输入系统A100系对原料码头的作业方式,将一期码头A100系作业由卸矿为主更改为以卸载煤船为主。
2) 取料能力:
① 在10#、11#堆取料机上增设堆积溜槽挡板,在料场堆积过程中可分流送至用户槽,增加煤场输出能力。同时,输出的下游系统连锁需连接至增设挡板。一旦下游系统停机,挡板可自动切换至料场堆积模式,不影响输入系统的作业。
② 在10#、11#堆取料机下的地面皮带增加移动小皮带,当堆取料机在料场西侧进行堆积作业时,东侧可以使用铲车配合移动小皮带进行输出作业,从而增加输出能力。
③ 在CA料场增设2台移动式取料机,补充1#取料能力的损失。
④ 打破原有的品种配置集中管理方式,采取混合配置模式,即在筒仓施工期间CD料场焦、肥、气、肥气煤全配置,CH料场配置焦、肥、气煤。
⑤ 进一步增加贮存喷吹煤的干煤棚的输入量,充分发挥16#堆取料机的输出能力。
3.2. 改造施工难点及对策
1) 工程量大,需投入大量劳动力
本工程是宝钢首次大规模建设的筒仓群,劳动力需求量大且专业性较强,对滑模施工的作业层考察、选择、管理相当重要。项目部择优选取两支专业筒仓滑模班组,进行本工程的筒仓主体结构施工,由项目部统一负责三通一平、材料物资供应、现场协调和监督管理工作。工程实施过程中,进行施工班组间的质量、进度、安全、文明施工等竞赛,设立考评制度并写入合同条款,使班组间相互竞争、相互促进,从而提高工程项目的总体管理水平。
2) 部分区域场地狭窄、地上地下障碍物多
输入及输出系统的部分区域是在原有建筑设施的缝隙中实施。施工空间狭窄,周围设施密集,给基础施工和吊装作业带来非常大的难度,施工时对生产设施进行有效硬隔离围护,以保证人员及设备安全。
输入及输出系统的部分区域打桩作业采用钻孔灌注桩,桩及土建开挖施工需先挖探沟。开挖处如果有地下设施则采用人工开挖,并由生产方安排专业人员进行旁站监护。对特殊区域的转运站和胶带机桁架的具体施工方案由项目组编制安全合理的专项作业计划;支架和桁架尽量采用场外组装、整体吊装方法避免对周围设施、交通的影响。
3) 施工危险因素多
① 筒仓基础埋深约4.2 m,周边料场都有料堆,对基坑施工有一定的影响。基础施工时做好排水、边坡防护、基坑围护等措施。
② 筒仓土建上部结构施工属于高空作业,因此在筒仓滑模操作平台上应设置封闭的安全栏杆,上下操作平台设置马道,各筒仓操作平台间设置安全通道。
③ 输入系统及输出系统施工区域纵横交错的胶带机多、在线改造项目多并且需在较多运行胶带机中穿插施工,因此机械伤害、高空落物、防结构坍塌等伤害的危险因素多。施工中,施工方同生产方保持密切联系沟通,对生产设施进行有效硬隔离围护以便保证人员及设备安全;转运站结构及胶带机桁架支架的安装做好临时登高的有效措施,确保安装作业人员的安全;采取大型吊车将组装好的桁架一次吊装到位,尽量减少人员高空作业,高空作业人员要作好三穿一戴工作。
4) 施工生产交叉,施工区域牵涉部门较多,新老系统改造和接口较多
筒仓本体施工主要对1#取料机作业有较大的影响,根据相关数据和现场实测,1#取料机作业时配重与南侧筒仓外壁的最近距离只有2.5 m。施工期间,施工方与生产方密切配合,调整1#取料机工作角度,保持安全距离。筒仓上部钢结构及设备吊装期间,将起重机占位部位与1#取料机相互错开,避免相互碰撞,确有矛盾时优先保证生产。
本工程施工涉及的部门多,主要有炼铁厂、运输部、能环部、绿化公司、建筑维修公司等相关单位和职能部门。在施工过程中,建立应急协调机制、定期例会制度结合书面计划协调、专题报告、专项方案会审、施工前确认、强化过程跟踪和协调,事后确认和总结等措施,确保了协调顺畅、分工明确、责任明晰、工作顺畅。
对众多的接口实施,利用定修、年修或者日修来完成,编制工时工序计划,即按小时编写应完成的接口改造工作内容,提前做好停机前的一切准备工作,调配足够的劳动力和机具在规定的时间内顺利完成接口改造工作。原有设备拆除过程中,采取相应的特殊措施对电缆等设备进行保护,避免对生产造成影响。
4. 改造成果
如图2所示本改造工程前后对比图,本次改造工程从2014年底开始施工,2016年底完成筒仓及相关输入、输出系统的土建、机电安装及调试。
2016底年至今,如图3所示,原料煤场区域每平方公里年均降尘量从2016年的11.7 t/(km2∙m)降低
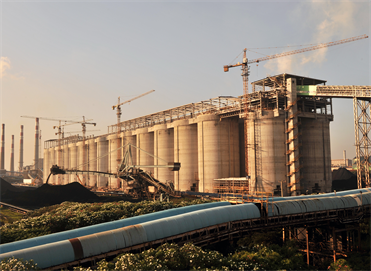
Figure 2. Realistic construction picture of the silo cluster
图2. 筒仓施工前后对比实景图
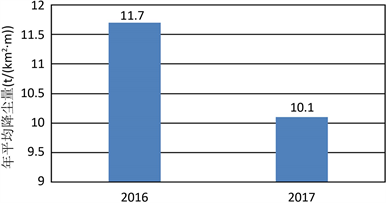
Figure 3. Airborne dust quantity of coal yard in 2016~2017
图3. 2016~2017年宝钢原料单元煤场降尘量
至2017年的10.1 t/(km2∙m),降幅约为14%。此外,根据2016~2017年盘库情况,原料单元煤场物料损耗率下降约0.3%,降幅约为32%。
5. 结论
宝钢炼铁厂对原料单元煤场E、F料条实施封闭改造,分步建设两排筒仓,每排15个共计30个,单个筒仓直径(内径)为24 m,最大贮量约1.4万t/个。通过合理安排输入、输出、堆积作业,优化焦煤、电煤、喷吹煤的物流平衡,确保了筒仓施工期间用户的原燃料供应稳定。筒仓建成后,煤场的降尘量、物料损耗得到明显下降,说明改造工程是可行和有效的。