1. 引言
金属燃料作为含能添加剂和燃烧催化剂填充到推进剂和炸药中能提高其密度、爆热和发动机的比冲,因而广泛应用于航天与军事领域 [1] [2] [3] 。目前,金属燃料的研究主要集中在单质铝粉和铝基合金粉末当中,例如Al-Mg、Al-Li、Al-Ni、Al-Ti等等 [4] [5] [6] [7] 。这些合金粉末在一定程度上能缩短点火延迟时间、降低点火温度以及增强氧化程度,因而它们拥有更高的能量释放效率和能率释放速率 [8] [9] 。然而,这些金属依然存在一些本质上的缺陷。比如铝粉易团聚、燃烧不完全 [10] [11] [12] ;镁在发动机应用中存在低空燃比的问题 [13] 。锆是一种比较有代表性的高密度含能金属。一方面,高密度能够提高含能配方的体积比冲和能量密度 [14] 。另一方面,锆具有良好的点火性能和燃烧性能,它即使在高的负载下也能被点燃 [15] [16] 。这些优势使得锆渐渐成为研究金属燃料的重点。然而,锆也存在严重的不足。高的熔点以及熔炼过程中的成分偏析都严重限制了锆的发展,而且锆的含能远低于铝。因此,将铝和锆进行合金化形成Al3Zr/Al复合燃料不失为一个解决锆缺陷的新途径。目前,Al-Zr合金粉末的制备方法主要集中在自蔓延高温合成(SHS)以及非自耗电弧熔炼 [17] [18] [19] [20] 。然而,这些方法制备的粉末大都呈无规则块状,严重影响了合金燃料在含能配方中的使用性能。本文采用非自耗电弧熔炼以及紧耦合气雾化法制备Al3Zr/Al复合燃料,对其形貌、结构、物相以及热性质作了表征,并探究了Al3Zr/Al复合燃料的氧化机制。
2. 实验
2.1. Al3Zr/Al复合燃料的制备
不同锆含量的Al3Zr/Al复合燃料制备过程如下所述:在水冷模具中采用电弧熔炼技术对质量比为30:70的海绵锆(纯度,99.99%)和铝锭(纯度,99.95%)进行熔炼,得到Al-Zr合金锭子。熔炼之前,熔炼炉的样品室被抽成高真空状态(真空度 ≤ 4 × 10−3 Pa),然后充入氩气作为保护气氛直到常压。样品室内的残余氧气通过熔融的钛球吸收。制备的Al-Zr合金被反复熔炼八次以上以确保成分均匀。将熔炼好的Al-Zr合金置于紧耦合雾化设备当中雾化成粉。雾化条件为:雾化气氛为氩气,喷射压力5 MPa,最高加热温度为1500℃,真空度为20 Pa。雾化后,收集到的粉末通过200目的拍击筛进行分选。
2.2. 材料的表征
使用带EDS功能的电子显微镜观察粉末形貌,背散射图片用来观察粒子的形状与尺寸。适量的粉末被镶进环氧树脂中,经磨制与抛光,最后以体积比为HF:HCl:HNO3:H2O = 1:1.5:2.5:95的腐蚀液进行金相腐蚀。得到的样品用作粒子的横截面分析。激光粒度仪用来表征粉末的粒径分布。粉末的物相通过XRD来表征,图谱采集角度在10˚~90˚区间。粉末的热性质通过TG-DTA以及DSC来表征。TG-DTA的实验条件:加热温度从室温到1300℃,加热速度为20℃/min,气氛为O2,气流速度为20 mL/min;DSC的实验条件:加热温度从室温到1000℃,加热速度为10℃/min,气氛分别为O2和Ar,气流速度为20 mL/min。
3. 结果与讨论
3.1. Al3Zr/Al复合燃料的物相、粒径和形貌分析
图1为新工艺制备的Al3Zr/Al复合燃料的XRD图谱,纯Al粉作为参照。从图中可以看出,Al3Zr/Al复合燃料的物相组成为Al和Al3Zr两相。Al3Zr/Al复合燃料的XRD图谱中并没有单质锆的特征峰出现,这说明Zr与Al完全合金化,形成了金属间化合物Al3Zr。
图2为过200目筛分后的Al3Zr/Al复合燃料的粒径分布图。从图中可以看出,过筛后的粉末的平均直径为25.7 μm,尺寸分布较为均匀,有少量的大尺寸粒子出现,可能是由于少量Al-Zr复合粉末的流动性较差造成颗粒彼此之间的粘合形成的。图3为Al3Zr/Al复合燃料的SEM形貌图,从图中可以看出,除少数情况外,绝大部分粉体材料都呈高度球形,且没有明显的团聚现象发生。从图3(b)可以看出,颗粒表面粗糙,有鳞片状表皮堆积,晶界分明。鳞片状表皮的形成是由于颗粒在凝固过程中存在优先结晶面和结晶方向。因此,颗粒内部的某一相定然存在优先结晶面优先结晶出来。颗粒表面并非完全致密,这就为氧化提供了多个氧通道。相比于纯铝粉表面形成的致密氧化膜,Al3Zr/Al复合燃料拥有更高的热活性,更加容易被氧化。
适量的Al3Zr/Al复合燃料经热镶过程嵌入到环氧树脂中,后经研磨与抛光,得到横截面样品,在SEM背散射模式下观察Al3Zr/Al复合燃料内部结构组织。如图4所示,是Al3Zr/Al复合燃料复合燃料的
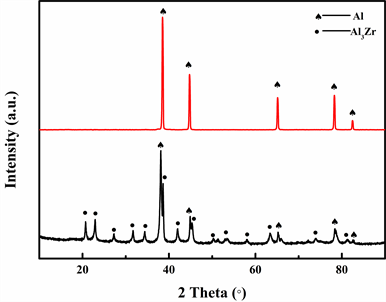
Figure 1. XRD patterns of Al3Zr/Al composite fuels
图1. Al3Zr/Al复合燃料的XRD图
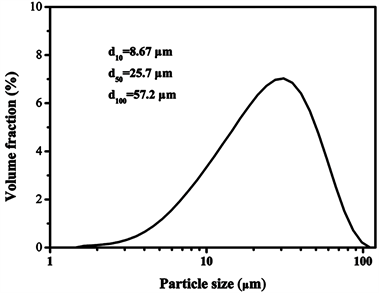
Figure 2. Particle size distribution for Al3Zr/Al composite fuels
图2. Al3Zr/Al复合燃料的粒径分布
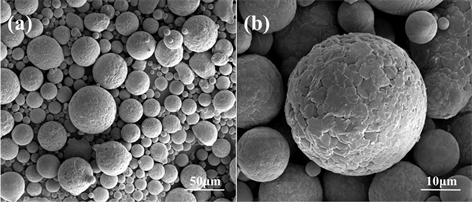
Figure 3. SEM images of Al3Zr/Al composite fuels
图3. Al3Zr/Al复合燃料的表面形貌图
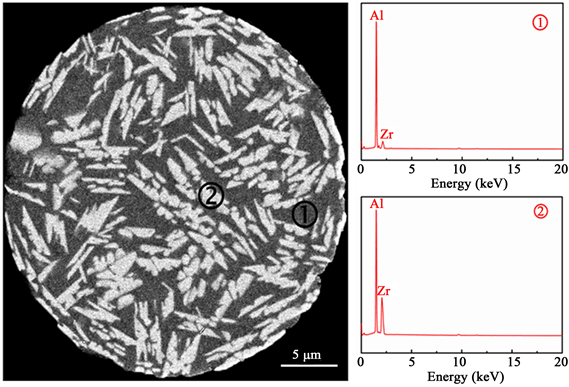
Figure 4. The cross-section morphologies and EDS patterns of Al3Zr/Alcomposite fuels
图4. Al3Zr/Al复合燃料截面的SEM图以及EDS图谱
横截面形貌图和EDS图。从图中可以清晰地看到,粉末内部呈现白色针状晶体嵌入到黑色基体当中的特殊结构,这些白色的晶体将基体隔开,具有晶粒细化的作用。EDS结果表明,白色晶体中的Al含量高达74.66 at%,而Zr含量为25.34 at.%。这个结果表明Al和Zr在熔炼过程中发生了金属间反应,形成了金属间化合物Al3Zr。而从EDS结果中Al和Zr的比例可以推测白色晶体就是Al3Zr。而从黑色基体中的EDS结果来看,Al含量高达96.82 at.%,可以推测黑色基体为过量的单质Al。而基体中出现的少量Zr,可能是由于在样品进行机械研磨的过程中,某一层Al颗粒被研磨得很薄,场发射的电子束可能检测到下一层的颗粒上导致的。因此,这少量的Zr含量可以忽略不计。故Al3Zr/Al复合燃料是由Al3Zr和过量的单质Al组成。这个结果与图中的XRD结果一致。Al3Zr/Al复合燃料内部形成了针状金属间化合物内嵌到基体中的特殊结构,这种特殊结构有可能促进Al3Zr/Al复合燃料的完全氧化。
3.2. Al3Zr/Al复合燃料热性能及氧化过程分析
Al3Zr/Al复合燃料的TG-DTA曲线如图5所示,其中Al粉作为参考系。从图中可以看出,Al3Zr/Al复合燃料对比纯铝粉,热分析曲线明显不同。纯Al粉的DTA曲线上有一个吸热峰和一个放热峰,吸热峰是由Al的熔化吸热造成的,而放热峰是Al的氧化放热引起的。对于Al3Zr/Al复合燃料而言,此时Al的吸热峰基本消失,而由一个在960℃附近处比较集中的放热峰和1100℃处比较平缓的放热峰组成。960℃处的放热是由于Al3Zr发生剧烈的氧化反应造成的,而1100℃处比较弱的放热则是由过量的单质Al氧化形成的。从TG曲线上可以看出,Al粉的增重较低,远低于完全氧化时的增重,表明Al粉氧化不完全;而对于Al3Zr/Al复合燃料,增重达到69.9%,是Al粉的两倍多,接近完全氧化时的增重,说明Al3Zr/Al复合燃料氧化是比较完全的。相比纯Al粉,Al3Zr/Al复合燃料放热提前,增重更明显。由此证明Al3Zr/Al复合燃料与纯Al粉相比,拥有更高的热反应活性,反应更完全。
为了探究Al3Zr/Al复合燃料在960℃放热的原因,将Al3Zr金属间化合物置于纯O2气氛下的管式加热炉中,在不同温度下进行氧化。图6显示的是Al3Zr分别在600℃,800℃,900℃和1000℃下氧化后的XRD图谱。从图中可以看出,Al3Zr在600℃时基本没有氧化。随着温度从600℃增加到800℃时,Al3Zr的峰开始消失,取而代之的是Al2O3,t-ZrO2和m-ZrO2的峰。当温度继续增加到900℃和1000℃时,氧化产物的晶型并没有发生明显的变化。这表明Al3Zr在800℃时氧化并不完全,氧化还在进一步发生。然而,氧化产物的类型并没有发生改变,且在960℃时并没有发生明显的晶型变化。基于以上分析可以推断,Al3Zr在960℃的放热反应与产物的晶型转变并无直接关系。
(a)
(b)
Figure 5. TG-DTA traces of Al3Zr/Al composite fuels
图5. Al3Zr/Al复合燃料的TG-DTA曲线
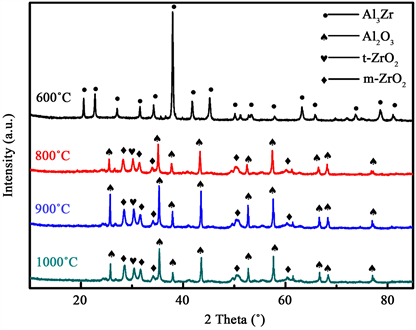
Figure 6. XRD patterns of oxidized Al3Zr intermetallic powders at different temperature
图6. Al3Zr金属间化合物粉末在不同温度下氧化产物的XRD图谱
为了证明Al3Zr在960℃放热与温度和氧化介质之间的关系,将对Al3Zr作DSC分析。如图7所示,是Al3Zr分别在Ar和O2气氛下的DSC曲线。从图中可以看出,在Ar气氛下,DSC曲线上从始至终没有出现放热峰,这表明温度与Al3Zr在960℃下放热并无关联。而反观在O2气氛下,在960℃下有一个十分明显的放热峰。从而可以说明,O2作为氧化介质参与到Al3Zr的氧化反应中,能引起Al3Zr在960℃集中放热。该反应过程是后续提到的Al3Zr的非选择性氧化过程。
综合以上描述与分析,为建立Al3Zr/Al复合燃料的氧化模型,将Al3Zr/Al复合燃料置于气氛烧结炉中,分别在1300℃和1500℃下进行氧化。图8显示的是不同温度下Al3Zr/Al复合燃料氧化产物的形貌图。从图中可以看出,粉末表面基本被氧化,出现大量的裂纹,甚至有一些外壳已经破裂,里面熔融的核心被暴露在外面。这个熔融的核心是由熔融的Al液包裹着Al3Zr形成的。从图中可以看出,核心已经消失,只剩下空壳留下。这个空壳是由Al2O3和ZrO2构成的。此时,粉末已完全氧化。图9显示的是随炉冷却后的氧化产物的XRD图谱。从图中可以看出,1300℃下的氧化产物主要由Al2O3,ZrO2,未反应完的Al和Al3Zr组成;而1500℃下的氧化产物仅由Al2O3和ZrO2组成,且所有的t-ZrO2全部转变为m-ZrO2。
3.3. Al3Zr/Al复合燃料的氧化机制与模型
图10显示的Al3Zr/Al复合燃料氧化过程示意图。这个新的氧化模型可以这样解释:开始,少量的O2穿过并不致密的Al3Zr/Al复合燃料表面,与颗粒内部的少量的铝粉进行缓慢的氧化,反应方程式如下所示:
(1)
随着温度的增加,达到Al熔点时,Al开始熔化并包裹着嵌在基体中的Al3Zr。Al3Zr由于其密度大略微下沉。当温度进一步升高直到点火温度之前,此时Al已完全熔化,而Al3Zr在有O2气氛下发生非选择性氧化,形成ZrO2和Al2O3。Al3Zr的非选择性氧化过程可由以下方程式来表述:
(2)
在这个氧化过程中,大量的热被释放出来而引起局部过热,这将导致极大的热膨胀和浓度梯度。加之Al3Zr有很低的收缩率,在高的体积膨胀下很容易破碎。从而使得晶粒得细化,反应更容易进行。而
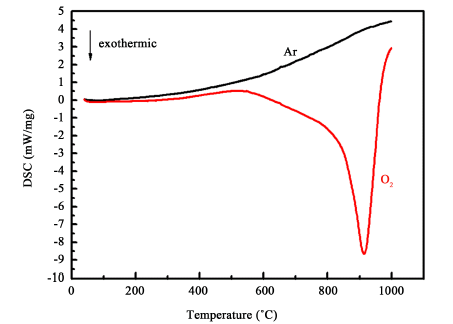
Figure 7. DSC curvesofAl3Zr intermetallic compounds at different atmosphere
图7. Al3Zr在不同气氛下的DSC曲线
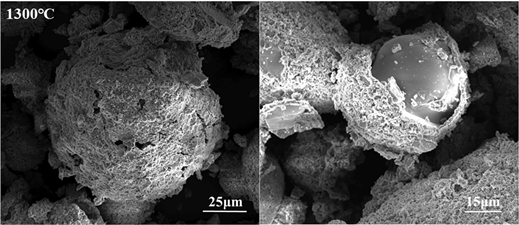
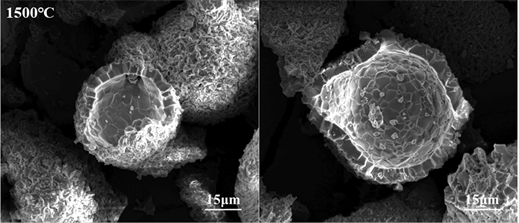
Figure 8. SEM images of Al3Zr/Al composite fuels oxidized at different temperature
图8. 不同温度下退火后Al3Zr/Al复合燃料的表面形貌图
Al3Zr/Al复合燃料内部特殊的结构使得针状的Al3Zr的氧化能够带动基体单质Al的氧化燃烧。两者热量叠加使得反应更加剧烈。同时,熔融的Al液与周围分散的小粒子也能发生反应 [21] [22] ,其反应式如下所示:
(3)
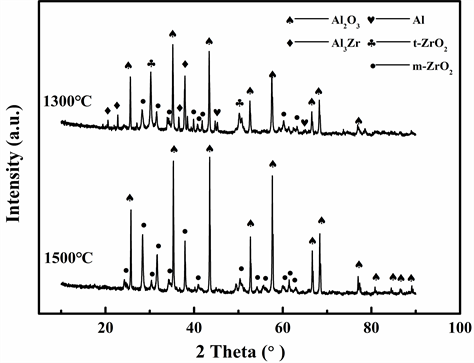
Figure 9. XRD patterns of Al3Zr/Al composite fuels oxidized at different temperature
图9. 不同温度下退火后Al3Zr/Al复合燃料的XRD图谱
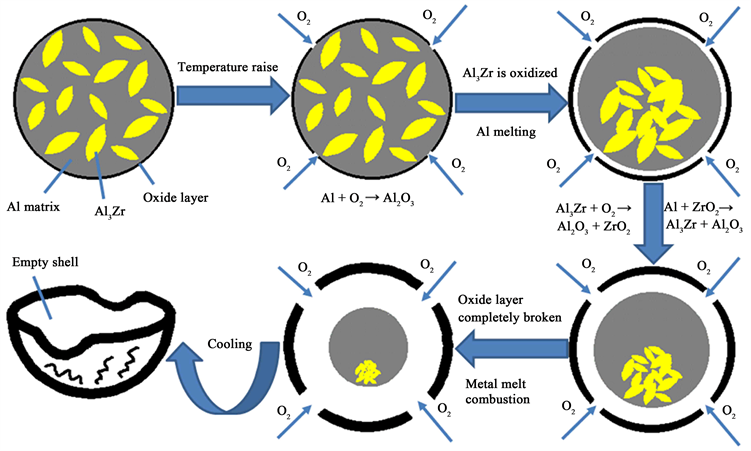
Figure 10. Scheme of oxidation process of Al3Zr/Al composite fuels
图10. Al3Zr/Al复合燃料的氧化过程示意图
这个反应在放热的同时还生产了新生的Al3Zr,而新生的Al3Zr又能参与到(2)中的反应中去。液态Al不断被消耗,反应剧烈进行。同时,粒子内部温度急剧上升,由于粒子内部与表面热膨胀系数的不同产生了巨大的压力差。外层非致密的表皮出现大量的裂纹,为外部O2的渗透提供了更多的通道,从而加速氧化过程的进行,使得裂纹进一步拓展和延伸,甚至导致外壳的破裂与剥落,因而使得内部的熔融Al液和Al3Zr完全暴露在O2下,促进粉末的完全氧化。这个过程足以使得整个颗粒发生崩塌,实现颗粒的完全氧化。
在Al3Zr/Al复合燃料氧化过程中,Zr含量扮演着重要的角色。在Zr含量在10~53 wt%的区间内,Al3Zr/Al复合燃料保持着Al过量的情况。Zr含量的多少决定着合金内部Al3Zr量的多少。而Al3Zr的量决定着反应的剧烈程度,在整个氧化过程中起至关重要的作用。因此,具有特殊结构的Al3Zr/Al复合燃料有望在推进剂和火炸药领域具有广阔的应用前景。
4. 结论
本文主要利用激光粒度仪、SEM、XRD、TG-DTA、TG-DSC等技术手段对新工艺制备的Al3Zr/Al复合燃料的尺寸、形貌、物相以及热性质进行表征,并探究其氧化机制,建立新的氧化模型。主要有如下结论:
1) 新工艺制备的Al3Zr/Al复合燃料成分均匀,呈高度球形状,粉末的平均粒径在25.7 μm。而XRD结果表明,Al3Zr/Al复合燃料由金属间化合物Al3Zr以及单质Al两相组成。
2) 与纯Al粉相比,Al3Zr/Al复合燃料有更低的放热温度,放热更加集中,且有更明显的增重,增重可达69.9%,表明Al3Zr/Al复合燃料比纯Al粉有更好的热活性。
3) Al3Zr金属间化合物在O2气氛下于960℃附近有明显的放热。
4) Al3Zr/Al复合燃料内部特殊的组织结构和Al3Zr的非选择性氧化促使Al3Zr/Al复合燃料均在960℃附近集中放热,从而导致整个复合粉末的完全氧化。
致 谢
感谢国家自然科学金和中国工程物理研究院联合基金(U1530127)、上海航天创新基金(SAST2015096)、航天科学基金以及华中科技大学分析测试中心对本研究工作的大力支持。
NOTES
*通讯作者。