1. 引言
为克服常规振动台试验中无法进行大型结构试验的限制,产生了基于地震模拟振动台的实时子结构试验方法 [1] [2] 。振动台子结构试验的特点之一是将数值模型得到的界面力施加到试验子结构上,传统方法是在振动台旁设置反力墙和动态作动器对试验子结构进行加载 [3] [4] [5] [6] 。Michel Bruneau等对二层结构进行了实时混合试验 [7] ,试验子结构与数值子结构的界面力由反力墙上的作动器来提供。受实验室空间和安装条件限制,如果振动台附近无法安置反力墙则这种试验就无法实现。同时,由于安装于反力墙上的作动器输出的位移是相对于静止地面的绝对位移,因此这种子结构试验需要使用具有较大行程的作动器。为解决上述问题,Narutoshi Nakata等提出了可控质量的振动台子结构试验方法 [8] 。主动质量驱动装置(Active Mass Driver,简称AMD)具有控制效果好、控制代价低等优点在高层
建筑、高耸结构抗风抗震 [9] 反应控制的应用中获得了成功,成为目前研究与应用非常广泛的一种振动控制设备 [10] [11] [12] [13] 。利用电液伺服型AMD装置作为振动台子结构试验的加载装置具有不需要反力墙,作动器行程要求低等诸多优点。因此本文根据开展振动台子结构试验的研究需要,在对液压伺服阀、液压动力机构和液压执行机构的性能需求进行分析的基础上 [14] [15] [16] ,研制了一种体积小、出力大、控制精度高的AMD系统,推导了AMD系统的系统模型;进行了AMD系统的性能试验。
2. AMD系统原理
纸型
电液伺服主动质量驱动系统(简称AMD)是电液伺服技术和液压技术相结合的产物,该系统由电液伺服阀驱动,伺服阀按照输入的指令进行变速度驱动、变向驱动和限速驱动。图1是采用电液伺服阀控制的电液伺服主动质量驱动系统原理图,由图1可知,它是液压开式回路:伺服阀阀芯位移→油液变量→执行器变速;伺服阀阀芯变向→油路变向→执行器变向。
AMD控制系统中最重要的部件是作动器系统,它是给结构施加控制力的执行机构,其工作性能直接影响到AMD系统的控制效果。图2为电液伺服AMD系统构成示意图。
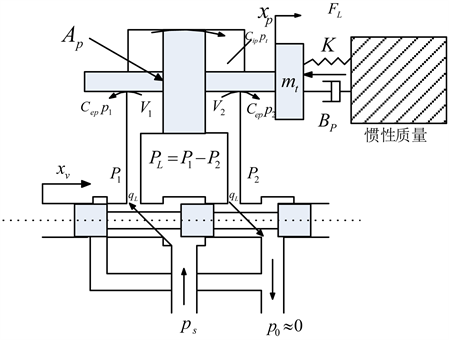
Figure 1. Curve: Schematic diagram of an electro-hydraulic servo AMD system
图1. 电液伺服AMD系统原理图
注:1-AMD机架;2-电液伺服作动器;3-电液伺服阀;4-惯性质量箱;5-直线导轨
Figure 2. Structure of electro-hydraulic servo AMD control system
图2. 电液伺服AMD机械构造原理图
电液伺服AMD系统的最大特点是充分发挥电液伺服阀的特性,通过改变伺服阀阀芯的移动方向、速度和位置来控制油缸的正反向、油缸速度、作用力和位置。同时,电液伺服系统与执行元件油缸可以做到较为理想的功率匹配。还具有作动器体积小,液压伺服元器件对外部环境要求低,系统动态特性好,使用寿命长,适用性广等优点,图3为本文研制的电液伺服AMD系统实物图。
3. AMD系统分析
基于能量转换观点,电液伺服系统实现了电能→液压能→机械能→负载运动的传递过程。AMD装置的机械系统包括惯性质量、液压伺服作动器和机架三部分组成。考虑作动器的液压伺服特性,给出了AMD装置的简化力学模型。
系统理论建模主要围绕伺服阀部分——伺服阀压力—流量数学模型,液压动力部分——作动器数学模型,液压执行部分——液压缸驱动负载的数学模型三部分展开。
3.1. 伺服阀压力–流量方程
(1)
式中:
为伺服阀系统的流量增益,且
(2)
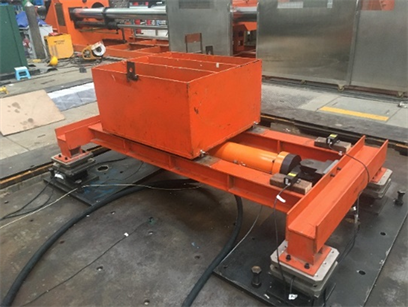
Figure 3. Physical diagram of electro-hydraulic servo AMD system
图3. 电液伺服AMD系统实物图
为伺服阀的流量–压力系数,
(3)
式中未说明符号意义如图1所示。
3.2. 作动器数学模型
根据流量连续性结合质量守恒定律,建立电液伺服阀控液压缸的方程为
(4)
式中
为液压缸两腔的总容积;
(5)
为液压缸总泄漏系数;
(6)
为液压缸内泄露系数;
为液压缸外泄露系数。
3.3. 液压缸执行机构力平衡方程
忽略库伦摩擦等非线性负载,根据牛顿第二运动定律,可得电液伺服作动器的输出力为
(7)
由上述分析可得电液伺服AMD系统的传递函数如式(8)所示,框如图4所示,控制器的传递函数用PID代替。
(8)
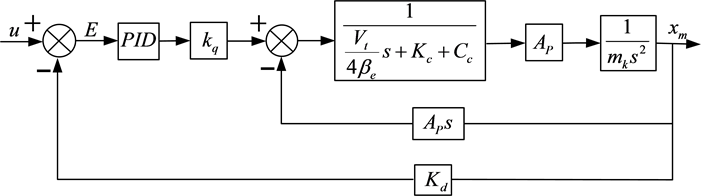
Figure 4. The block diagram of the transfer function of the electro-hydraulic servo system
图4. 电液伺服系统传递函数方块图
图中:
表示AMD系统惯性质量,
为惯性质量的实际位移,
为负载压力,
表示活塞等效截面积;
为作动器流量,
表示作动器腔内全容积,
为液压油体积弹性模量,
液压缸泄露系数;
表示伺服阀信号–流量增益,
为流量–压力系数。
4. AMD系统性能测试
AMD系统的设计参数为负载1000 kg,最大加速度20 m/s2,最大速度0.6 m/s,最大位移100 mm。为了检测AMD系统的实际性能与设计指标是否一致,将电液伺服AMD系统固定于地面上,进行PID控制下的位置闭环试验,分别输入白噪声、阶跃信号和正弦信号(97 mm,1 Hz;9 mm,9 Hz),在空载和负载(400 kg,1000 kg)两种不同情况下进行多组工况试验。
1) 对10 mm阶跃信号的响应,分为空载、400 kg和1000 kg进行测试测试结果如表1所示,阶跃信号响应曲线如图5所示。
阶跃信号测试表明,AMD装置可以很好的跟踪位移指令,响应速度较快,动态特性满足设计要求。
2) 通过正弦信号对AMD系统的基本性能进行测试,负载1000 kg,对于最大速度的测试要选取低频率大位移幅值的正弦信号,故选取97 mm,1 Hz。对于最大加速度的测量选取9 mm,9 Hz。通过反馈信号控制实际幅值大小。AMD系统的测试结果见图6~8。
根据图6的正弦信号,通过计算可以得到AMD系统最大速度0.615 m/s。通过工况(图8所示),通过外置传感器采集到的AMD系统最大加速度为27 m/s2。
3) 通过对AMD系统输入白噪声工况进行试验,对AMD系统参数进行辨识,建立AMD系统的传递函数。辨识算法采用最小二乘法,辨识结果如下所示。
(9)
5. 结论
经过上述分析与试验,结论如下:
1) 通过AMD系统负载1000 kg,在不同频率和幅值的正弦运动工况,测试到AMD系统的最大速度为0.6 m/s和最大加速度为27 m/s2,达到AMD系统设计目标,该AMD系统表现较好;
2) 对AMD系统进行参数辨识,得到了AMD系统的模型参数。为后续AMD系统用于振动台实时子结构试验提供加载装置;
3) 该系统动态特性好,出力大,控制灵活,刚度较好,系统稳定性好,精度高,但是当系统进行高频工况时,会出现幅值衰减和相位滞后,后续可以通过改进控制算法,改善这一弊端。
(a)
(b)
(c)
Figure 5. Step response curve. (a) Amplitude 10 mm, no load; (b) amplitude 10 mm, load 400 kg; (c) amplitude 10 mm, load 1000 kg
图5. 阶跃响应曲线。(a) 幅值10 mm,空载;(b) 幅值10 mm,负载质量400 kg;(c) 幅值10 mm,负载质量1000 kg
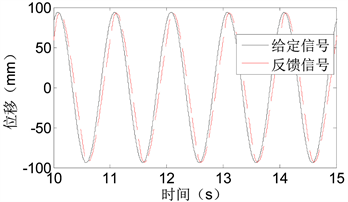
Figure 6. Load 1000 kg, amplitude 97 mm, 1 Hz, PID control
图6. 负载1000 kg,幅值97 mm,1 Hz,PID控制
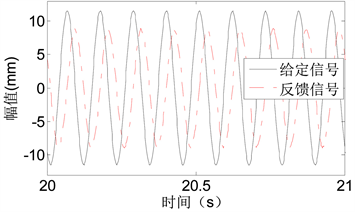
Figure 7. Load 1000 kg, amplitude 9 mm, 9 Hz, PID control
图7. 负载1000 kg,幅值9 mm,9 Hz,PID控制
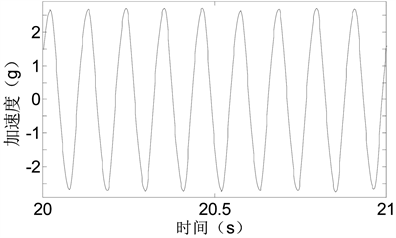
Figure 8. Load 1000 kg, amplitude 9 mm, 9 Hz, acceleration measurement signal
图8. 负载1000 kg,幅值9 mm,9 Hz,加速度测量信号
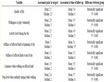
Table 1. Test result of step signal
表1. 阶跃信号测试结果
致谢
本文得到“工程抗震与结构诊治北京市重点实验室重点基金项目”和“国家留学基金”的部分资助,在此表示感谢。
基金项目
国家自然科学基金资助项目(51578024, 51278013)。
NOTES
*通讯作者。