1. 概述
随着全球铁矿石消耗量增加,烧结粉矿资源持续减少,烧结粉矿质量也在不断劣化,出现性价比高的烧结粉矿资源供应不足的情况。为应对资源的变化,通过试验研究澳洲某高铝粉矿的特性以及对烧结的影响,根据试验结果提出在现有的烧结配矿和生产条件下的高铝粉矿烧结配矿方案,为高铝粉矿的使用打下基础。随着近年国际铁矿石供应商的兼并重组,铁矿石海运贸易量的70%以上被巴西和澳大利亚的三大供应商所控制,澳洲是铁矿石出口大国,但随着生产规模的扩大,其高品位矿石资源在减少,原有部分高品位矿山逐渐开采完,需要开采新的矿山进行替代,如近几年新出现的FMG公司,其铁矿石年产量由当初的不足500万吨,迅速成长为世界第四大铁矿石公司。除此之外,还有澳洲一些其它的小型铁矿石项目也在进行前期开采研究。宝钢湛江钢铁使用的铁矿石绝大部分依靠进口,由于澳洲离湛江钢铁运距短,巴西航线约40天,而澳洲只有8天,开发澳洲铁矿石新资源,有利于公司控制铁矿石库存,迅速适应日益竞争的市场。
2. 澳洲某高铝粉矿的物理化学指标情况
2.1. 化学成分情况
对澳洲某矿山送样的高铝粉矿进行实验室化学成分分析,并与澳洲FMG公司产的国王粉矿进行对比分析。结果表明,除了烧损低、Al2O3含量较高外,澳洲高铝粉矿与FMG国王粉的化学成分相似。尽管高铝粉矿的铁品位仅为56.98%,但是烧结过程中,随着高铝粉矿结晶水脱出,一定程度还提高了烧结矿铁品位。具体如表1所示。
进一步对澳洲某高铝粉矿不同粒级的化学成分进行分析,了解不同粒度高铝粉矿的化学成分变化情况,分别取核颗粒(+1 mm)、中间粒子(0.25~1 mm)以及粘附粒子(−0.25 mm)进行化学成分分析,结果如表2所示。可见,随着粒度变细,澳洲高铝粉矿的品质逐渐劣化,SiO2、Al2O3、P2O5和LOI均明显升高,导致全铁含量由57.49%降低至55.37%。由此推测,澳洲高铝粉矿的粘附粉(−0.25 mm粒级)风化程度较高,粘土的比例高。因此,如果矿山在实际开采中,可通过洗、选矿等方法去除细粒级中的泥质矿物以提高其含铁品位,减少杂质含量。具体分析结果如表2所示。
2.2. 粒度组成情况
对澳洲高铝粉矿的粒度组成与国王粉矿进行了对比分析,粒度组成情况如表3所示。
从表3可以看出,虽然两种粉矿平均粒度相差不大,但是澳洲高铝粉矿0.25~1 mm部分占比为27.1%,而国王粉矿为20%。理论上认为,烧结粉矿中粒度0.25~1 mm的部分,既不容易粘附别的颗粒,也不容易被别人粘附,一般要求该部分越小越好。
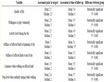
Table 1. Contrast of chemical content between the high Al and the king fines (%)
表1. 澳洲高铝粉矿的化学组成与国王粉矿对比(%)
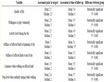
Table 2. Chemical compositions of Australia high Al fines (%)
表2. 澳洲高铝粉矿的化学组成(%)
注:CW为结晶水,LOI为烧失量。
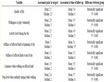
Table 3. The composition of Australia high Al in size (%)
表3. 澳洲高铝粉矿的粒度组成(%)
3. 澳洲某高铝粉矿烧结性能研究
3.1. 同化温度
铁矿石的同化性能是指铁矿石与CaO反应生成铁酸钙的能力,指铁矿石与氧化钙接触面开始反应的最低温度,用开始反应的最低温度来表示同化温度。同化温度越低,表明同化性越好,越容易生成液相。为此,对澳洲高铝粉矿进行同化温度分析,分析结果如图1所示。
从图1可以看出,该澳洲高铝铁矿粉,同化温度为1230℃,与FMG国王粉相比,同化温度略低,因此,该澳洲高铝铁矿粉具有较好的同化性能。
3.2. 液相流动性
液相流动性能是指在烧结过程中铁矿石与CaO反应生成的液相的流动能力,用以表征粘结相的有效粘结范围。液相流动性的好坏对最终烧结矿强度具有重要影响。一般而言,流动性能高,粘结周围物料的能力大,提高烧结矿强度,反之降低烧结矿强度。但是,粘结相的流动性过大可能影响烧结过程的透气性,从而降低烧结生产率,另一方面,液相流动性差,液相分布的均匀性差,液相对残余核颗粒的润湿性差,导致烧结矿中孔洞大小不均使得物料表面的粘结相层厚度变薄,烧结矿易形成薄壁大孔结构,从而烧结矿整体变脆、强度变差。此外,随着烧结温度的提高,液相流动性显著升高。这是因为随着烧结温度增加,液相生成量增加,此外,质点扩散速率增加,粘度下降,流动性变好 [1] 。
从图2可以看出,该澳洲高铝粉矿的液相流动性随温度升高而增大。与澳洲FMG国王粉相比,该澳洲高铝粉矿的液相流动性指数较高。当然铁矿石液相流动性并不是越高越好,一般情况下,通过配矿结构优化,将不同液相流动性的铁矿石进行组合,使烧结液相流动性控制在一定范围之内,以满足烧结高产高强度的需要。
3.3. 粘结相强度
烧结矿强度由残余颗粒强度、粘结相自身强度及粘结相与残余颗粒间的粘结强度共同决定。由于核颗粒(残余颗粒)一般强度较高,烧结矿的强度主要依赖粘结相自身强度及粘相对残余颗粒的粘结强度。粘结相自身强度是指铁矿石在烧结过程中形成的液相凝固后自身具有的强度,试验通过测定试样形成液相并冷凝固结后的抗压强度来评价各种铁矿石的粘结相自身强度。结合宝钢湛江钢铁高炉用料结果,烧结矿碱度为1.8左右,在此条件下进行烧结粘结相强度试验,试验结果如图3所示。
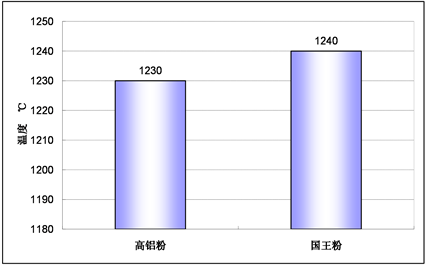
Figure 1. Assimilation beginning temperature (−0.25 mm)
图1. 铁矿石同化开始温度情况
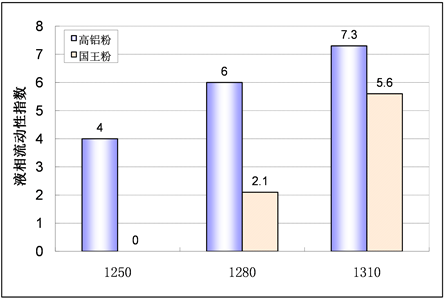
Figure 2. Contrast of the liquid phase fluidity index between the high Al and the king fines
图2. 铁矿石液相流动性能对比
4. 湛江钢铁使用澳洲某高铝粉矿的设想
湛江钢铁设计有两座5050立方的高炉,铁水产量为823万吨/年;两座550平米的烧结机,烧结矿设计产量为1226万吨/年,同时,还有一座年产500万吨的球团厂。湛江钢铁工艺特点就是烧结矿产能较大,球团的生产能力也大,故高炉的用矿结构可根市场据铁矿石价格情况,适时进行调整。烧结矿产能大,一座烧结机对应一座高炉,以及球团生产成本较高、稳定性不足,决定了湛江钢铁高炉炉料结构以烧结矿为主,球团矿、块矿作为必要补充的局面。
使用澳洲高Al2O3铁矿必然引起烧结矿中Al2O3含量提高,烧结矿作为高炉入炉主要含铁炉料,会带来高炉炉渣Al2O3上升。高炉炉渣主要成分是SiO2、CaO、MgO、Al2O3,另有少量的FeO、MgO和S。作为高炉渣中的重要组元——Al2O3是一种比较特殊的组元。当炉渣为二元碱度并在某一小范围内变化时,Al2O3含量的高低对炉渣黏度产生很大的影响。炼铁专业领域的传统观念认为高炉渣中的Al2O3量超过15%为高炉不可操作范围,大量的研究文献、教材和报告中也都有相关的定义。大部分观点认为Al2O3在10%~15%为合理的操作范围,大于15%会增加炉渣黏度,降低流动性能,给高炉操作带来不便 [2] 。2016年宝钢某高炉炉渣Al2O3含量情况如图4所示。
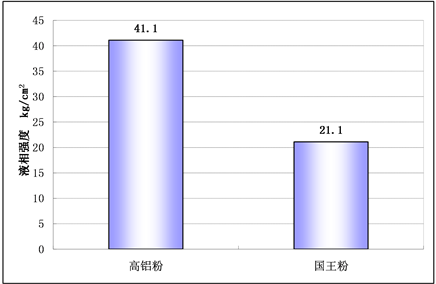
Figure 3. Bonding phase strength of iron ores at various basicity (kg/mm2)
图3. 铁矿石粘结相强度情况(kg/mm2)
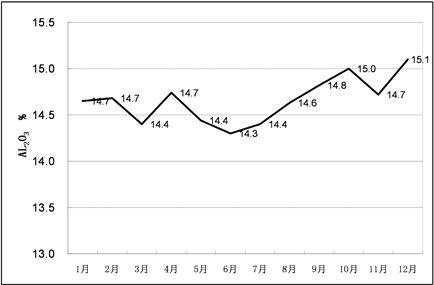
Figure 4. Al2O3 content in the BF slag of 2016
图4. 2016年炉渣Al2O3含量情况
宝钢股份宝山基地大型高炉炉渣Al2O3控制突破到15.3%,而且各项生产指标稳定 [2] 。就目前宝钢湛江钢铁高炉炉渣的情况,高炉炉渣Al2O3具有一定的提升空间。在目前高炉用矿结构条件下,使用10%高铝粉矿,高炉炉渣Al2O3上升约0.1个百分点,仍然满足大型高炉对炉渣的控制要求。
5. 结论
1) 澳洲高铝新矿粉是典型的褐铁矿品种,除三氧化二铝较高外,铁品位、二氧化硅以及硫、磷含量与澳洲FMG国王粉不相上下。
2) 澳洲高铝新矿粉的粒度组成合理,平均粒度超过3 mm,有利于改善烧结过程透气性能。
3) 澳洲高铝新矿粉具有较好的烧结性能,特别是同化温度低,液相流动性好,在低碱度条件下,可获得较好的液相粘结强度。
4) 基于目前全部使用进口铁矿石的结构和进口煤低灰炼焦的原燃料条件,具备使用一定比例的澳洲高铝烧结粉的条件。