1. 引言
细晶强化是一种具有显著效果的材料强化手段 [1] ,晶粒细化之后,塑性变形将在更多的细小晶粒内分散,应力集中较小,并且曲折高密度的晶界也有利于阻止裂纹的扩展。纳米晶体材料的概念在80年代初期由德国学者H. Gleiter教授首次提出 [2] ,由于该类材料存在大量晶界的独特结构而具有力、热、电、磁等方面特殊的性能。若将金属粗晶的尺寸由微观量级进一步减小至纳米量级,传统的金属材料也将呈现高强度、超塑性的优异性能,而且纳米金属材料所具有的大体积含量的高能量晶界也将会在材料的电化学活性、原子扩散等方面发挥巨大作用,从而拓宽传统金属材料的应用范围,使其重新焕发活力。
“纳米晶体(Nanocrystalline)材料”,或“纳米相(Nanophase)材料”,是单相或多相的多晶体,其晶粒尺度至少在一维是纳米级(典型的为1~100 nm)。这类金属纳米材料可以含晶体相、准晶相或非晶相,但至少有一相是晶体相 [3] 。块体纳米金属材料,由纳米量级尺寸晶粒与大量的晶界构成,基于其独特的结构特征,为深入研究界面结构与性能提供了良好的条件;而由小尺寸量子效应和晶界效应,纳米金属材料还可能表现出的一系列与普通多晶体和非晶态固体有本质差别的理化(包括磁、光、电、声等)及力学性能,也为提高材料的综合性能,发展新一代高性能材料创造了条件。
目前绝大多数的纳米材料仍是采用纳米金属晶体粉末在外压力作用下低温压制或烧结的方法合成。非晶晶化法是近年来发展迅速的一种方法,它是针对于非晶形成能力较强的合金系,经初步高速直流溅射、单辊或双辊旋淬法等工艺制得的非晶低维材料,然后进行热模压实、烧结得到块体,最后通过热处理晶化工艺(如等温退火、脉冲退火、激波诱导等),控制非晶态固体的晶化动力学过程得到纳米尺寸的晶粒。而形变纳米化(也称大塑性变形(Severe plastic deformation, SPD))是目前制备块状金属纳米材料很有优势的一种工艺方法,该方法具有较宽的适用范围,制备得到的试样致密,无残留缩孔,无杂质引入,是一种实用化前景良好的金属材料纳米化技术。
2. 大块材料纳米化
形变纳米化方法具有较宽的适用范围,制备得到的试样致密,无残留缩孔,无杂质引入。常用的工艺主要包括,等径角挤压法(Equal channel angular pressing, ECAP)和高压扭转变形法(Severe plastic torsion straining under high pressure, SPTS)。大量金属、合金的实验表明 [4] ,ECAP方法得到的晶粒平均直径200~300 nm,而SPTS法可以得到平均尺寸在50~150 nm的等轴细小晶粒,两种方法所提供的类似的等静压高压并导致较大变形量,形成带有大角度晶界的微观结构,且具有很高的位错密度。其晶粒中的非平衡界面、组织和性能的关系得到了广泛研究,Zhiguo Fan等人 [5] 利用八道次等径角挤压和低温冷轧制得到平均晶粒尺寸150 nm的组织,纯钛的强度增加到1218 MPa,塑性恢复至12.6%;李志明等人 [6] 采用以轧辊线速度不对称为主要特征的异步轧制方法在室温下轧制获得平均晶粒尺寸小于300 nm的纯钛TA1超细晶组织,纯钛内部有狭长剪切带均匀分布,组织中主要为等轴超细晶,亦存在少量晶粒和小角度晶界;材料的显微硬度比原始热轧态提高了60%,抗拉强度提高至740 MPa以上。超细的等轴晶粒结构是材料产生高强度、高硬度以及超塑性的重要条件。
3. 材料表面纳米化
表面自身纳米化(Surface Self-Nanocrystallization, SNC)是对多晶材料进行处理,增加材料表面的自由能,使粗晶组织逐渐细化至纳米量级,见图1(b)。它与表面涂层或沉积(如图1(a))的方式存在明显差异,是材料自身表面部分的晶粒细化至纳米量级,如图2。其主要特征是晶粒尺寸由表面开始沿厚度方向逐渐增大,纳米结构表层与基体之间不存在明显界面,与处理前相比材料的外形尺寸几乎不变。而且,不需考虑表层与基体之间的结合力,纳米结构层在使用过程中不会发生剥落和分离。这种方法既适合于材料的局部改性,又适合于材料综合性能的整体优化。因此该技术制备的结构材料具有很大的开发应用潜力。
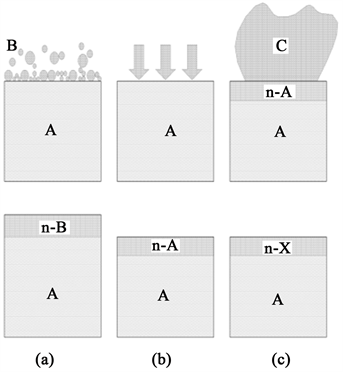
Figure 1. Schematic illustration of three types of surface nanocrystallization [7] . (a) Surface coating or deposition; (b) Surface self-nanocrystallization; (c) Hybrid surface nanocrystallization
图1. 表面纳米化的三种方式 [7] 。(a) 表面涂层或沉积;(b) 表面自身纳米化;(c) 两者的混合方式
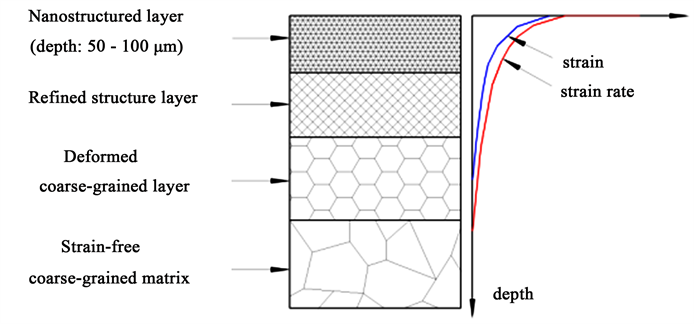
Figure 2. Schematic plot of micro-structure characteristics and distributions of strain and strain rate along depth in the surface nanocrystallization layer [8]
图2. 表面自纳米的组织结构与应变及应变速率随深度变化图 [8]
实现表面自纳米化主要有两种方法:表面机械加工处理法和非平衡热力学法。非平衡热力法主要是通过快速加热、快速冷却方式,使材料的表面部分在较短时间内熔化或发生相变,急速冷却,通过动力学来提高形核率,控制晶粒长大的速率,进而得到纳米量级的组织结构。快速加热的方法主要有激光加热和电子辐射等。此外,王积森等人 [9] 公开一种交流电处理金属材料表面纳米化的方法:在电镀装置的电镀液中,金属材料作为某一电极,在两电极上加载交流电源,金属材料体表面原子在电镀液中交流电的作用下不断的剥离与重组,最终表面形成具有纳米结构特征的表层。该种纳米化工艺成本低、设备简单,且材料在电镀液中进行处理,无宏观力作用,不会产生塑性形变,特别适于处理形状复杂或精密工件。处理后工件表面纳米层均匀,不存在死角,但厚度较小(一般10 nm~15 μm)。
机械加工表面自纳米化是机械外力施加载荷作用于材料表面,材料表面发生强烈的塑性变形,采用非平衡处理方法增加材料表面的自由能,使粗晶组织逐渐细化至纳米量级。利用该方法制备的材料晶粒尺度也可以达到10~20 nm。
4. 材料形变纳米化技术
目前,形变纳米化或强烈塑性变形法(Sever Plastic Deformation, SPD)常用的机械加工方法进行材料表面纳米化的方法有表面机械研磨(SMAT)、表面机械碾磨(SMGT)、超声喷丸(USSP)和高能喷丸(HESP)、超音速颗粒轰击(SFPB)、快速多重旋转碾压 (FMRR)、高压水射流等。
机械研磨法(Surface Mechanical Attrition Treatment, SMAT)是由卢柯和吕坚 [7] 在1999年提出的,首次将强烈的塑性变形应用于材料表面自纳米化。采用的设备如图3所示,在充入惰性保护气体的容器内部,在底部振动发生器的高频振动作用下弹丸小球产生高速振动,从不同方向反复、快速地撞击置于容器顶部的试样表面,金属表面发生多系孪晶或多系滑移而发生晶粒细化。该方法最先在钢铁材料上实现了表面纳米化 [7] [10] [11] ,随后又有国内外的其他研究人员对不锈钢 [12] [13] [14] 和纯钛及钛合金 [15] [16] [17] 、Cu [18] 和Al [19] [20] [21] 等有色金属材料进行了SMAT纳米化之后组织和性能的相关研究。
超声喷丸法(Ultrasonic Shot Peening, USSP) [22] 和高能喷丸(High-Energy Shot Peening, HESP) [23] [24] 是在SMAT的基础上,改进弹丸直径和振动频率等试验工艺参数,实现材料表面自纳米化的方法。类似的弹丸撞击的方法,还有美国K. Dai等 [25] 提出的表面纳米化和硬化(Surface Nanocrystallization and Hardening, SNH)方法,与SMAT主要不同点在于所使用的弹丸数量只有5个,称为五丸法(图4)。
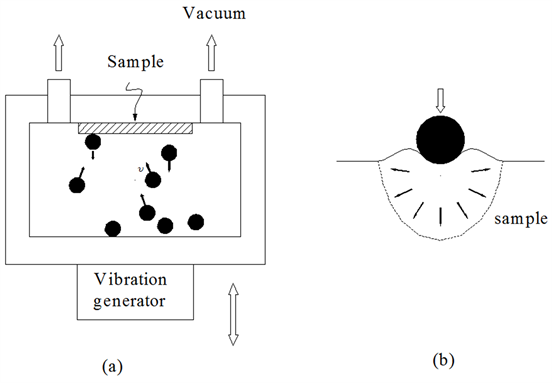
Figure 3. Self-nanocrystallization by surface mechanical attrition treatment [7]
图3. 表面机械研磨自纳米化 [7]
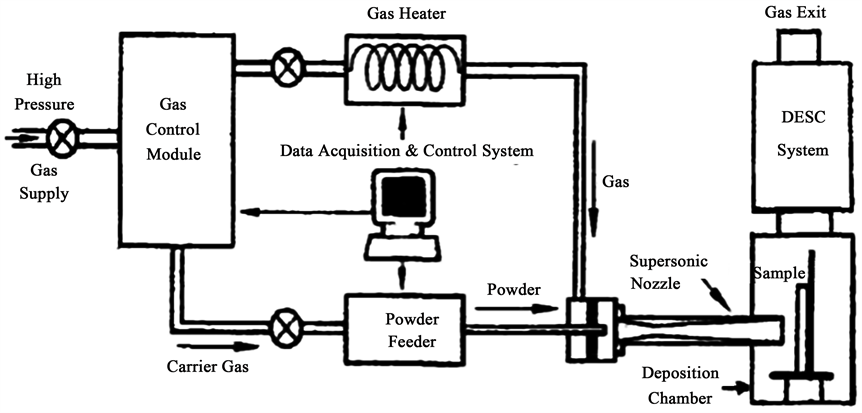
Figure 4. Schematic illustration of the ultrasonic shot peening set-up [22]
图4. 超音速颗粒轰击装置示意图 [22]
在传统喷丸技术基础上,日本的Yutaka Kameyama等人 [26] 采用超细的颗粒(通常10~200 μm)撞击材料表面达到修饰表面微观组织、改善材料综合性能的目的。沈阳金属研究所的熊天英提出的超音速颗粒轰击法(Supersonic Fine Particles Bombardment, SFPB) [27] 是一种适用于复杂形状和大面积金属构件的表面纳米化方法。喷丸法(Shot Peening, SP) [28] [29] 所用的设备一般与喷丸工艺的相同,但增大了喷丸时的空气压力(约0.5 MPa)和减小弹丸直径(小于0.8 mm)等协调喷丸工艺参数使材料表面纳米化。
除了传统的弹丸变形方式外,日本学者Masahide Satoa等 [30] 提出了丝刷法(Wire-Brush, WB),它通过不锈钢丝刷子的高速旋转和施加一定的压力使材料表面塑性变形、组织细化。此外,我国王东坡等人 [31] 使用的超声表面加工处理方法(Ultrasonic Surface Processing, USP)、乌克兰学者Bohdan N等 [32] 使用的Ultrasonic Impact Peening (UIP)和Y.S. Zhang等人 [33] 提出的Oscillating Sliding (OS)等技术都采用圆柱状的压头,以超声速的振动频率反复撞击试样表面,压头在撞击材料表面的同时可以旋转或压头不旋转而工件旋转。这里将它们称为压头振动法。表面机械碾磨(Surface Mechanical Grinding Treatment, SMGT) [34] 是一种用于轴类或柱状零件表面纳米化处理的工艺方法,装置及原理如图5所示,工件以速度υ旋转,半球状WC/Co压头沿工件的轴向运动,材料表面产生100 μm的塑性变形层。
快速多重旋转碾压(Fast Multiple Rotation Rolling, FMRR)是山东大学孙康宁等基于强烈塑性变形细化晶粒的原理提出的一种新的材料表面纳米化工艺。利用螺旋线状分布的硬质合金小球,在法向压力的作用下对金属材料表面实施反复旋转碾压,使金属材料表面的粗晶组织发生强烈塑性变形而逐渐细化至纳微米量级,如图5所示。目前,爨鹏飞等人已利用该工艺方法在316 L不锈钢、低碳钢表面成功制得表面平均晶粒尺寸12 nm、9 nm的纳米结构层,FMRR处理后的近表层硬度、整体抗拉强度、耐磨性均有显著提升,其纳米化机理以及热稳定性和耐蚀性也得到了定性研究。
最近孙康宁课题组利用一种高压纯水射流实现金属材料表面纳米化的新工艺,探究了高压水流压力、喷嘴行走速度和靶距对被处理材料表面质量的影响,成功实现了纯钛材料的表面纳米化。
5. 纳米化材料的组织、结构、性能变化
经过自纳米化处理之后,金属材料的表面形成纳米结构层,晶粒的尺寸随着深度的增加而不断增大,呈连续梯度变化,如图2所示。根据晶粒尺寸和应变大小,材料表面自纳米化之后的组织结构由表面
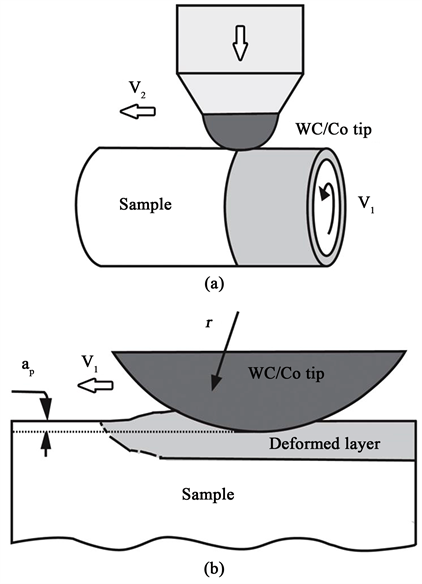
Figure 5. (a) The SMGT equipment of surface nanocrystallization; (b) The plastic deformation layer produced by the surface rolling of the material [34]
图5. (a) SMGT 纳米化装置示意图;(b) 材料表面碾压产生的塑性变形层 [34]
向内依次分为纳米晶层、细晶层、粗晶应变层、粗晶基体无应变层。一般材料处理之后纳米晶层在10~50 μm;细晶层一般200 μm左右,而粗晶变形层可以达到600 μm。工艺参数不同,各层的厚度就有所不同。TEM的观察结果表面,纳米晶为等轴状,晶粒取向呈随机分布,晶粒尺寸几十纳米,表面细晶层的晶粒尺寸在 100~1000 nm之间,在这一层中可以观察到大量塑性变形所产生的位错、位错墙、小角晶界和变形孪晶等。粗晶应变层和基体无应变部分的区别在于是否发生应变和加工硬化现象,它们的晶粒尺寸差别不大,粗晶应变层的组织结构与传统的应变组织相似。从表面纳米晶层到粗晶应变层都属于变形层,变形层的厚度与试验的工艺参数有关。
而材料表面晶粒纳米化的细化机制,主要与金属材料本身晶体结构及层错能(stacking fault energy, SFE)有关 [8] [35] 。在工业纯铁、Al合金 [20] 等高层错能金属材料纳米化的研究中发现,位错运动是主要的变形方式,晶粒细化则是通过位错的运动、增殖、交互作用以及湮灭、重排等多种作用,生成高密度的位错墙(Dense dislocation walls, DDWs)和位错缠结(Dislocation tangles, DTs)。而DDWs和DTs将原始晶粒分割成尺寸较小的单个位错胞(individual cells),变形量的不断增加又使得这些位错胞转变为较小取向差的亚晶界(Sub-boundaries),随着应变量的继续增大,越来越多的位错在亚晶界处湮灭和生成,晶界两侧的取向差不断增加最终变为大角度晶界,以上过程的不断重复使得原始粗晶不断细化得到纳米晶。
纳米晶体材料具有优异的性能,金属材料经表面机械加工自纳米化后获得的纳米晶层致密度高、污染少,并与基体材料的结合紧密,能显著优化材料的综合性能。
1) 力学性能
在表面进行纳米化处理之后,材料的表面硬度、抗拉强度、耐疲劳磨损强度都会得到有效的改善和提高,这主要与加工硬化和细晶强化有关。钢铁材料经过纳米化处理后,表面硬度可以提高两倍以上。在文献 [36] 中,结论显示室温下SMAT处理之后的316 L单轴屈服强度为1450 MPa,是粗晶材料的6倍,这种超高强度的材料性能与Hall-Petch关系是一致的。福州大学的杨晓华等人 [13] 研究指出:在表面机械研磨处理5 min时,316 L不锈钢的屈服强度得到迅速提高,而随着SMAT时间的增加,屈服强度增幅明显下降;抗拉强度随着SMAT时间的增加只有少量增加;同时,伸长率在处理5 min时明显下降,在15 min后下降幅度很小。文献 [17] 采用SMAT对纯钛进行纳米化处理60 min后,材料表层纳米层的抗拉强度为970 MPa,高于原始材料,可达到钛合金Ti-6Al-4V的强度范围(975 MPa)而纳米化之后的块体钛合金材料的延伸率下降为粗晶材料的59%。
2) 扩散性能(材料表面合金化)
纳米晶体结构中高密度晶界的存在,为原子扩散提供了大量的通道。晶界处多种非平衡缺陷以及大量的过剩能量都有利于化学反应,为化学热处理提供了理想的界面条件。纳米晶体结构层中原子扩散的驱动力会高于粗晶结构,尤其在能量较高的三叉晶界或界偶处,这种能量的变化更为明显。卑多慧等研究了表面纳米化预处理对低碳钢气体渗氮行为的影响,发现表面纳米晶化预处理可以有效降低氮势门槛值,氮原子在基体中的扩散系数和表面反应传递系数提高,使常规渗氮温度降低约50℃或者将渗氮时间缩短50%,在渗氮条件相同的情况下,化合物厚度成倍增加。薛群基院士领导的团队与吕坚教授用表面研磨纳米化技术优化脉冲直流辉光等离子技术渗氮处理的氮化效果,渗氮层的厚度和表面硬度都得到了显著提高,表面硬度分布梯度的改善也使得其耐磨性和负荷承载能力的提高3~10倍。
3) 耐蚀性能
纳米化之后材料晶粒尺度、结构、成分及状态的改变都会对材料的腐蚀性能造成影响。材料在表面纳米化处理之后,存在大量的晶界,具有很高的反应活性。而且,处理后表面粗糙度的增加和微观应力的存在,都将会对材料的耐蚀性能造成不利影响。但相反,表面纳米化使材料的活性原子数增加却可能使得钝性金属材料表面更易形成钝化膜,提高耐蚀性。Balusamy Thangaraj等人 [14] 针对表面研磨处理技术参数与不锈钢表面纳米层在林格氏液中的耐蚀性之间的关系作了一系列研究,发现纳米化处理使得材料耐蚀性能有不同程度的下降,当直径为2 mm小球SMAT处理15~30 min时,耐蚀性与原始样品相当。X. Y. Wang等人 [29] 研究了退火处理对纳米化之后的304SS不锈钢的耐蚀性的影响,认为350℃/60 min 的退火有利于表面钝化膜的形成,降低纳米晶结构层中的缺陷密度,从而使得 304SS在3.5%NaCl溶液中的耐蚀性得到改善。此外,材料表面纳米化后材料的抗应力腐蚀的性能会得到提高。王志平等人采用超音速微粒轰击技术对0Cr18Ni9Ti不锈钢焊接接头表面进行处理,并测量了表面处理后焊接接头抗应力腐蚀情况。结果表明,材料表面产生压应力层,样品在较低应力情况下,300 h以上应力腐蚀后试样仍未出现断裂,可见NC处理后样品的抗H2S应力腐蚀性能得到显著提高。
4) 生物学应用及表面纳米化复合工艺应用
力学性能研究表明,纳米钛合金材料的弹性模量明显下降,使其弹性模量与骨更接近,从而减少了由于应力遮挡导致骨质疏松进而引起假体松动的可能。另外纳米材料表面的粗糙度增加,增加了骨植入物接触面积,而且与骨组织本身的纳米结构类似。表面纳米化技术不仅保持了材料的生物力学性能,而且使其具有了纳米生物学的优点。
6. 结束语
金属材料的形变纳米化技术发展迅速,对传统金属材料的改性具有重要的研究意义和实用价值,目前存在的主要问题是实现对大块材料及复杂零件表面的形变纳米化,以及材料形变纳米化的低成本制备问题。这些核心问题的解决将为材料形变纳米化带来重要突破,目前类似快速多重旋转碾压(Fast Multiple Rotation Rolling, FMRR)等高效低成本技术都具有较好实用化的发展前景。
参考文献