1. 引言
半导体激光器以其体积小、质量轻、电光转换效率高、寿命长、波长覆盖范围广、高可靠性等优点已成为光电行业最有前途的产品,被广泛应用于国防(激光雷达、制导、引信等)和国民经济(光通信、材料加工、医疗美容)和科学研究等各领域 [1] [2] 。
随着半导体激光器技术的日趋成熟,高半导体激光器的功率密度和连续工作时间的增加,其工作过程中有源区温度(即结温)增加,阈值电流加大,有源区内电子和空穴会进行非辐射复合,非辐射复合的产生又进一步使有源区温度升高,进而形成了雪崩式恶性循环过程导致热饱和现象的发生引起的光学灾变损伤(COD)、烧孔、发光功率降低、禁带宽度降低、外微分量子效率下降、波长红移最终导致器件寿命及可靠性降低等问题,严重限制半导体激光器性能快速发展,芯片结温每增加10℃,器件的寿命就会减少一半 [3] 。因此需要将芯片焊接封装到散热热沉上,将激光器芯片产生的热量及时散出 [4] 。
本设计通过使用ANSYS Workbench软件,模拟分析研究半导体激光器热特性,芯片-热沉之间的热流的扩散规律。通过添加一层横向高热导率的石墨烯,改善了激光器管芯的热流扩散方式,使激光器芯片产生的大量热量先横向扩散加大热接触面积再经由热沉向下扩散,降低激光器芯片与热沉之间的界面热阻,提高输出功率。
2. 理论分析
半导体激光器在稳定工作后会产生大量的热量,热量的来源有以下几类 [4] [5] [6] :
1) 当电流注入有源区且小于阈值电流时,器件发出微弱的自发辐射光,没有激光产生,这部分注入的电流主要产生废热,热功率密度为QNR:
(1)
式中:d为有源区厚度,U为二极管压降,j为电流密度,ηi为内量子效率。
当注入有源区的电流超过阈值电流,伴随阈值电流的加大输出光功率急剧增加,能量损耗产生的废热,热功率密度计算公式为Qact:
(2)
式中:Qact为有源区的厚度,Vj为PN结上的电压降,j为注入电流密度,jth为阈值电流密度,ηsp为自发发射内量子效率,ηi为受激辐射内量子效率,fsp为自发辐射光子逃逸因子。
对于单管半导体激光器有源区温度由下式表示:
(3)
式中Tj为有源区温度,Tsink为热沉温度,V为结偏压,P为激光器的输出光功率,Rth为热阻。
激光器阈值电流与温度关系如下:
(4)
其中
代表室温下阈值电流密度,Tr代表室温,Ts表示温度对阈值电流影响的程度,是特征温度。由此可知,在室温Tr相同时,特征温度Ts越小,Ith随温度变化越大。
2) 除有源区外各层外延材料的损耗及电极层的电阻生成的热。
(5)
Q为热功率密度,pi为每层材料的电阻率。
3) 半导体激光激光器稳定的工作后的热传导方程为:
(6)
式中:T为温度,K为热传导系数。
半导体激光器斜率效率其表达式为:
(7)
式中,Pth为激光器在阈值电流下的光功率,Ith为阈值电流,e为电子电荷,hv代表光子能量,P为激光器正常工作时功率,I为注入电流。
半导体激光器输出光功率其表达式为:
(8)
Pth为阈值电流下激光器光功率,ηex外微量子效率,Ep为光子能量,e为电子电荷,I为激光器驱动电流,Ith为阈值电流。
半导体激光器功率效率其表达式为:
(9)
其中P为激光器光功率,I为工作电流,V为正向压降,r为半导体材料提点组和欧姆接触电阻。
半导体激光器C-mount封装结构模型如图1所示。模拟分析过程中所需材料参数如表1所示。
对于单管半导体激光器热分析,做出以下假设 [7] [8] [9] :
1) 半导体激光器工作过程中,内部的电子-空穴非辐射复合转换成光子产生的热量为主要热源。
2) 半导体激光器芯片腔长1.8 mm,热功率为10 W,热功率密度为7.407 × 109 W/m3,且各个外延
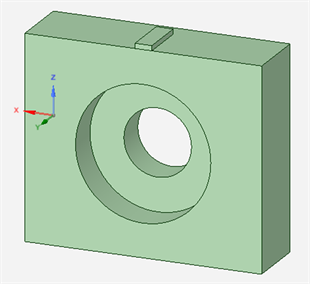
Figure 1. Workbench Model of c-mount package structure
图1. C-mount封装结构的workbench模型
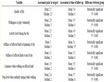
Table 1. Material parameters of the laser
表1. 激光器材料参数
层间厚度达到纳米级材料间热导率也极其相近,因此将芯片看作一个整体进行模拟分析计算。
3) 由于激光器芯片尺寸很小且非常薄,模拟过程计算温度不高,忽略芯片各个面的热辐射及空气对流散热。
4) 模拟计算中热沉下表面恒温20℃,同时选择两种热导率不同的焊料AuSn焊料和SnAgCu焊料对比焊料厚度及焊料热导率不同对半导体激光器的影响。
3. 模拟结果分析
不同的焊料厚度与芯片温度关系如图2所示。
从图2中看出当焊料厚度逐渐加厚时,激光器管芯温度反而会降低,但仅降低了0.2℃,由于焊料的导热系数要低于热沉很多,焊料厚度增加后易形成高阻层,但其厚度在0~10 μm变化内没有明显的高阻层形成,温度变化不明显,出于对芯片焊接的技术要求,需要一个基本厚度4 μm又因为AuSn焊料具有良好的浸润性、低粘滞性、抗疲劳性且不存在电迁移的现象,因此选择AuSn焊料来进行焊接封装。其中热阻计算公式为Rth:
(10)
式中T为有源区温度,T0为热沉底部温度,P为激光器功率。如图3所示激光器温度分布图可以得出焊料厚度为4 μm时激光器芯片温度为66.393℃,热阻为4.6 K/W。
从图4中热流可以看出,激光器芯片产生的大量热量都是通过与热沉的接触面扩散出去,其接触界面的热导率对管芯产生的热量的扩散起到至关重要的作用,而且可以明显看出芯片与热沉接触面附近热流量最大,散热效果最差,为了增强接触面散热引入高热导率石墨烯膜,石墨烯膜参数如表2所示,增加芯片与石墨烯层接触面热扩散面积使激光器芯片散热途径得到扩展,由于石墨烯具有很高的横向热导率,会使芯片产生的热量先延整个石墨烯层横向扩散,之后热量再向下扩散经由热沉散热,但由于石墨烯纵向热导率非常小,所以石墨烯层厚度不能太厚,否则将会造成热量在芯片周围聚集无法散开,最终致使有源区温度升高。设石墨烯层厚度为x,1 μm < x < 30 μm,通过改变石墨烯膜的厚度获得其芯片温度温度分布的影响。
如图5所示激光器芯片与热沉之间添加石墨烯层之后模拟结果,对比可知石墨烯层厚度为20 μm时,激光器管芯的温度降低约10℃。在图6中可以看出添加石墨烯层之后热量先横向扩展之后再向下传导,增加了热量的扩散面积,减少了芯片底部的热量堆积进而使芯片整体温度下降。
由此可知未填任何热界面材料的c-mount热沉和添加石墨烯膜之的热阻分别为4.6 K/W和3.5 K/W。
通过可以计算得出在不同的热阻下,功率和电流之间的有如图7所示关系,可以看出随着电流的加大,热阻小的激光器输出功率加大。添加了石墨烯层单管半导体激光器最大输出功率为18.5 W,而未添加石墨烯层的传统c-mount封装输出功率为15.4 W,由此可知,增加一层石墨烯层的单管半导体激光器使出功率提高近20%。
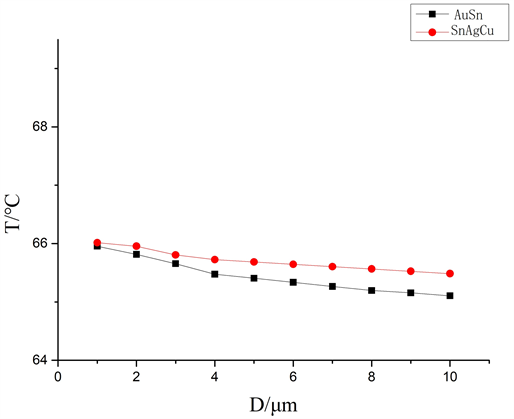
Figure 2. Relationship between solder thickness and temperature
图2. 焊料厚度与温度关系
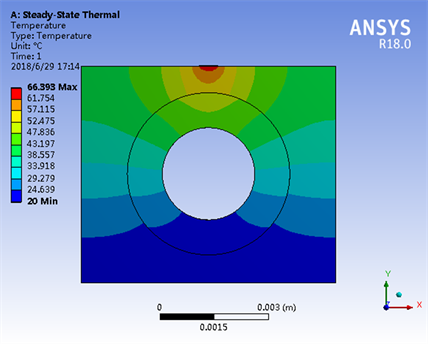
Figure 3. Laser temperature distribution cloud image
图3. 激光器温度分布云图
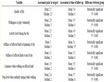
Table 2. Graphene layer parameter [10]
表2. 石墨烯层参数 [10]
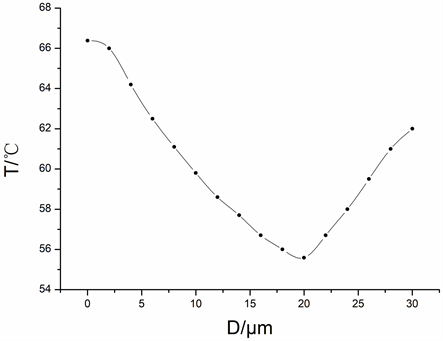
Figure 5. Relationship between graphene layer thickness and chip temperature
图5. 石墨烯层厚度与芯片温度关系图
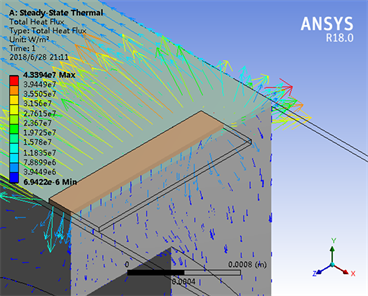
Figure 6. Heat flux vector diagram of the improved structure
图6. 优化后的热流矢量图
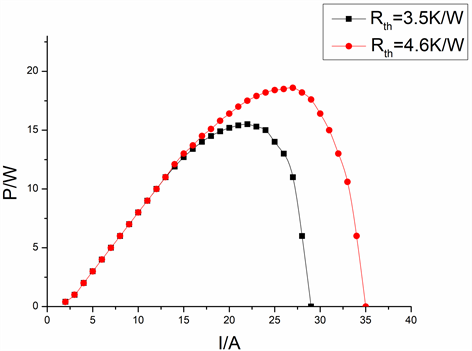
Figure 7. P-I Characteristics with different thermal resistance
图7. P-I特性曲线
4. 结论
为改善半导体激光器的散热特性,降低器件热阻,提高输出功率,在传统的c-mount热沉与激光器芯片间添加一层石墨烯层,分析热沉散热能力、热流分布、在不同热阻下的输出功率与传统c-mount封装结构进行对比,在环境温度为20℃,热功率为10 W时,为添加任何材料的c-mount封装的芯片温度达到66.393℃,计算热阻为4.6 K/W;添加高横向热导率的石墨烯膜层之后芯片温度为55.587℃,计算热阻为3.5 K/W,热流扩散效果明显,通过计算得到最大输出功率从15.4 W提升到18.5 W,提升了20%,结果证明,应用高热导率的石墨烯层的封装结构可以达到更好的散热效果。
基金项目
吉林省科技厅项目号20160101254JC和预研项目号6141XB010328。
NOTES
*通讯作者。