1. 引言
黄磷的生产通常采用电炉法,含磷炉气进入冷凝塔,其中的冷凝炉气中的磷蒸汽变为液态黄磷进入收磷槽,经精制得到成品黄磷,未冷凝炉气则为黄磷尾气。每生产1吨黄磷排放出的尾气量为2700~3000 Nm3,其主要成分为CO 85%~90%,还含有H2S、COS、CH4SH、AsH3、PH3、HF、氰化物等有害成分 [1][2][3]。本文着重分析黄磷尾气的预处理技术、现代分离技术和净化工艺的研究进展,并对黄磷尾气深度净化的可行性进行简单的论述。以期有效净化黄磷尾气制取高纯度CO,为后续高附加值化工产品的生产工艺提供洁净的原料气,真正实现资源、能源和环保的高度协调统一、推动化工可持续发展具有极其重要的意义。
2. 黄磷尾气净化技术
由于黄磷尾气中有害杂质种类较多,净化分离难度大,我国黄磷尾气的有效利用率不足40%。解决黄磷尾气的净化处理问题是提高黄磷尾气有效利用率的关键。目前,国内黄磷尾气净化处理技术主要包括:吸收法、吸附法和催化氧化法、催化水解法等。
2.1. 吸收法
1) 水洗法
水洗法是使用大量清水对黄磷尾气进行反复洗涤的方法,一般有两至三道工序,以有效除去粉尘、SiF4等机械杂质和焦油、泥巴磷等有毒害杂质。水洗工艺能吸收尾气中少量的HF、H2S、P4,同时可冷却尾气温度,但是对PH3没有作用。表1是黄磷尾气经水洗前后杂质组分含量的变化。其中氟的含量降低非常明显。
水洗后的黄磷尾气可作为燃料气用于烧结磷矿石与泥磷制酸,也可以用作硫磺制酸中的燃料。但由于其中的有毒成分如硫、氟、砷等会氧化生成有毒有害气体,造成二次污染,环境风险较大。
2) 水洗串碱洗法
水洗串碱洗法是在水洗法之后加入碱洗的过程 [4],工艺流程如图1所示。
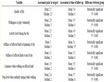
Table 1. Content variation of phosphorus exhaust before and after washing process (mg/m3)
表1. 黄磷尾气水洗前后组分含量变化(mg/m3)

Figure 1. String caustic washing process flow diagram
图1. 水洗串碱洗工艺流程图
黄磷尾气先经水洗降温后脱除尾气中大部分的粉尘和颗粒物,并除去部分H2S和HF;再通入填料塔中用浓度为5%~15%的氢氧化钠溶液进行洗涤,进一步吸收H2S、HF、CO2等酸性气体,主要反应机理如下 [5]:
3SiF4 + 4H2O → 2H2SiF6 + SiO2·H2O
H2S + 2NaOH→Na2S + 2H2O
CO2 + 2NaOH→Na2CO3 + 2H2O
P4 + 3H2O + 3NaOH → 3NaH2PO4 + PH3
HF+NaOH→NaF+H2O
显而易见,经水洗–碱洗过程能有效地提高黄磷尾气的净化效果 [6],脱硫率可达80%~99%,除氟率接近98%,对CO2的去除率约为50%。但碱洗液的NaOH浓度随反应进行而逐渐降低,PH值持续下降,导致杂质的去除效果逐渐减弱。需不断加入新鲜碱液以维持碱液浓度,从而确保尾气的净化效果。此外,由于PH3不是酸性气体,标准状态下在水中的溶解度仅为26 cm3/100 cm3,同时单质磷与碱的反应会产生少量PH3,从而导致PH3很难用水洗串碱洗的方法将其有效地脱除 [7]。
3) 氧化吸收法
氧化法是利用次磷酸钠、浓硫酸、过氧化氢等具有氧化性的试剂,对黄磷尾气进行氧化吸收,从而实现黄磷尾气的净化 [8][9][10]。相比于水洗串碱洗的方法,该方法能氧化PH3而使之脱除,但存在试剂消耗量大,操作复杂以及运行不稳定、设备易被腐蚀等缺点,吸收液不易回收,易造成二次污染,使得黄磷尾气不能得到较好的资源化利用。
2.2. 吸附法
1) 活性炭吸附
吸附法分为物理吸附法和化学吸附法。活性炭吸附法净化黄磷尾气分离和提纯工艺的关键是待处理气体各种组分可以高效的进行吸附和再生,需要根据尾气中的杂质含量来选择不同的工艺。当硫含量较高时,仅仅依靠吸附装置并不能保持较好的脱硫效果,同时该吸附为物理吸附和解吸过程,硫最终排入大气会危害环境,需增加脱硫工艺。此外,单质磷是气溶胶,极不易被吸附。因仅仅采用不加任何化学吸附剂的活性炭进行物理吸附,吸附量较低,一般只适用于微量气体的净化。因此,使用活性炭吸附法对黄磷尾气净化和提纯的工艺,适用性较差,脱磷脱硫效果有待于进一步的提高。
2) 变温变压吸附
采用变温和变压吸附法处理黄磷尾气,可以去除黄磷尾气中的磷、硫、CO2等杂质,达到提纯CO的目的,净化效果较好,再生容易 [11]。西南化工研究设计院开发的变温变压吸附法净化黄磷尾气 [12],其工艺流程见图2:a) 工艺直接采用变压吸附脱碳可同时脱除硫和CO2,达到净化目的,适合于尾气中硫含量较低或尾气量不大的情况;b) 工艺增加变压吸附脱硫工序脱除H2S,再进入脱碳工序,适合于尾气中杂质含量较高或尾气量较大的情况。
黄磷尾气经过传统的水洗除尘降温后进入变温吸附脱磷工艺,在常温下吸附杂质磷,变温吸附的再生采用加热方式,再生气加热后进入吸附塔加热吸附剂,杂质随着解析气流出,进行后处理。变温吸附后的尾气进入变压吸附工序,能同时脱除尾气中的碳和微量硫,经过该工序后,尾气CO的含量可达96%~99%,净化气能满足化工生产的要求。该工艺能有效地脱除PH3、流程简单、易控制、能耗低,但其工艺再生效率低、易造成二次污染、装置一次性投资较大,仅适用于含硫量低、尾气量小的情况 [13]。
2.3. 催化氧化法
催化氧化法是利用催化剂巨大的比表面积将目标气体吸附在催化剂表面,再通过负载的活性组分将黄磷尾气中的H2S氧化为单质硫、PH3氧化为P2O5、HCN氧化为N2和CO2。在对净化气要求较高的场合,为提高尾气中磷和硫的脱除效果,可采用催化剂进行催化氧化。在催化剂表面发生主要的氧化反应:
4PH3 + 8O2 = (P2O5)2 + 6H2O
4PH3 + 6O2 = (P2O3)2 + 6H2O
2H2S + O2 = 2S + 2H2O
4HCN + 5O2 = 4CO2 + N2 + 2H2O
2AsH3 + 3O2 = 2H3AsO3
AsH3 + 2O2 = H3AsO4
由于催化剂对P2O3、P2O5和S的吸附量远比P4、PH3和H2S大,氧化生成的P2O3、P2O5和S被催化剂表面所吸附,实现对杂质气体的净化。
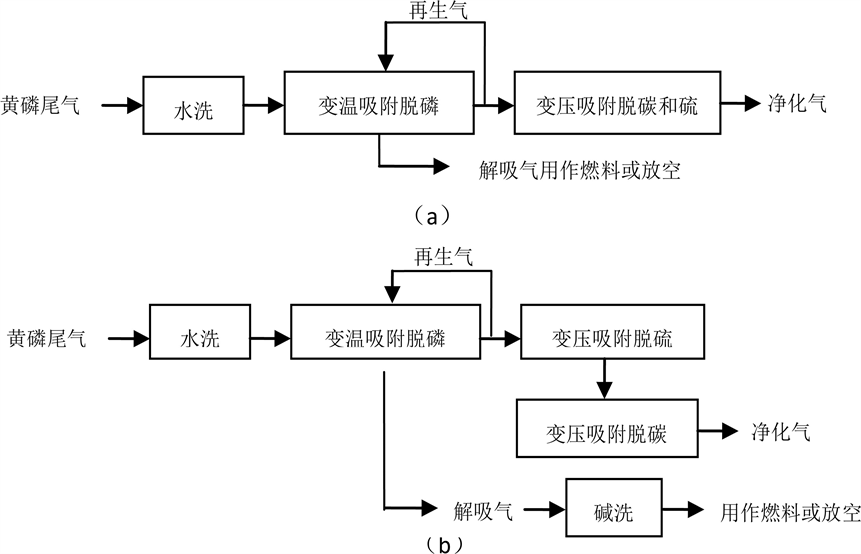
Figure 2. Variable temperature swing adsorption process flow diagram
图2. 变温变压吸附工艺流程图
3. 黄磷尾气深度净化技术
初步净化后的黄磷尾气仍含有微量的H2S、PH3、HCN等杂质,尤其是PH3会造成催化剂中毒 [14][15],需进行深度净化,进一步脱除PH3、HCN等杂质,使其满足用于生产较高附加值的化工产品原料的要求。
3.1. 碱洗–催化氧化法
碱洗–催化氧化法是对传统的水洗串碱洗工艺进行优化改进,在碱洗工艺后面增加固定床催化氧化工序 [16],其工艺流程见图3。黄磷尾气经过碱洗后,脱除尾气中的H2S、CO2和部分P4,由于P4和PH3在催化剂的作用下氧化为P2O3和P2O5,相比于P4和PH3,催化剂对P2O3和P2O5的吸附量较大,进而P2O3和P2O5被吸附于催化剂表面,使尾气得以深度净化。碱洗-催化氧化脱除黄磷尾气中的硫,采用碱洗的去除效率为88.1%~90%,单一催化剂催化氧化的去除率85%~90%,碱洗-催化氧化工艺去除效率可达99%。在温度110℃,氧体积分数1.5%条件下,净化后的尾气中H2S质量浓度 < 10 mg/m3,总磷的质量浓度 < 10 mg/m3,HF的质量浓度 < 5 mg/m3,能到达一碳化工原料气的要求。
3.2. 液相催化氧化
目前,对黄磷尾气中硫化氢、磷化氢等有害组分催化氧化的研究相对较少,亟待开发净化黄磷尾气净化的新技术。液相催化氧化法净化工业废气的研究日益受到广泛关注,液相催化氧化法是在催化剂的作用下,在水溶液中吸收和氧化气体中的还原性成分。
Shakirov等利用液相催化氧化法净化黄磷尾气 [17],黄磷尾气通过锰氧化物和硫酸铜的磷灰石悬浮液进行吸收净化,反应完的吸收液可用作肥料。由于黄磷尾气中氧含量较低,即使在补氧的情况下,磷、硫的氧化效率低,导致净化效率较低(<90%)。PDS法是利用双核酞菁钴磺酸盐碱性溶液作为吸收剂对黄
1——安全水封;2——水环真空泵;3——碱洗塔;4——旋风除雾器;5——钠氏泵;6——预热器;7——反应器;8——抽风机;9——水洗冷却塔
Figure 3. Alkaline wash-catalytic oxidation process flow chart
图3. 碱洗–催化氧化方法工艺流程图
磷尾气脱硫脱碳。何秀容 [18]等人研究了PDS催化剂在黄磷尾气中的催化活性,结果表明PDS催化剂对黄磷尾气中硫化物的脱除效果较好,能达到工业应用标准,且黄磷尾气中的杂质P、F、As对PDS催化剂的催化活性影响较小。PDS法的主要优势为:脱硫效率高,并能同时催化脱硫和氧化再生过程;碱用量小,能耗低;硫容量大,无二次污染 [19]。但该方法适用于黄磷尾气中的硫的质量浓度高于12 g/Nm3的情况,一般黄磷尾气中硫的浓度大概是0.6~3 g/Nm3 [2]。如果采用PDS法来处理,需要花更多的资源和成本去提高H2S的浓度,这显然与现在所提倡要建造资源节约型社会相背离。
昆明理工大学对黄磷尾气的深度净化做了许多研究,开发了黄磷尾气催化氧化技术。宁平等人提出了高效吸收-液相催化氧化耦合净化方法并建立了理论 [20],包括以下三个特点:1) 碱吸收转化和液相催化氧化同步进行;2) 将低活性气溶胶态P4碱吸收转化为PH3;3) 将液相催化氧化产生的H3PO4转化为可沉淀分离形态。
3.3. 低温微氧催化氧化
为了进一步净化黄磷尾气中的杂质组分,学者提出了低温微氧催化氧化净化方法 [21]。按一定的比例加入空气,使尾气含氧体积分数约1%,再经预热器加热至100℃~110℃后进入固定床;采用酸、碱、Cu(AC)2浸渍改性活性炭吸附净化低浓度H2S、PH3,得到了较好的吸附效果,尾气中的磷被氧化生成P2O5,和P2O3,而H2S则被氧化生成单质硫,这些氧化物被催化剂载体表面吸附,催化氧化后的气体可根据需要经水洗冷却后送人后工序。活性炭的再生采用空气氧化、水蒸汽冲洗、空气干燥三步得到了较好的再生效果并无二次污染。该技术已经应用于四川川投公司5000 m3/h黄磷尾气净化工程中,标志着黄磷尾气催化氧化技术进入了产业化阶段。
相比于水洗串碱洗、变温变压吸附以及硫酸铜洗等方法,黄磷尾气低温微氧催化氧化法没有温度、压力等特殊要求,操作条件低;工艺简单,处理成本低;能去除多种形态的磷、硫、砷,且各种杂质的浓度 ≤ 0.1 mg/m3,能达到10−6级,能够用于生产附加值价高的化工产品,使黄磷尾气得到有效地资源化利用。
4. 黄磷尾气深度净化技术对比分析
表2汇总了几种黄磷尾气深度净化工艺与传统净化方法技术经济指标的综合比较概况。黄磷尾气净化技术都是基于净化尾气中磷、硫、砷等有害组分,实现主要成分CO的综合利用。由表2可知,黄磷尾气深度净化技术以降低净化组分的去除成本、工艺流程复杂程度与投资成本等为标准,对比出低温微氧催化氧化法具有显著的优势,能够用于生产附加值价高的化工产品,使黄磷尾气得到有效地资源化利用。
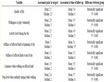
Table 2. Comprehensive contrast of different purified technology of yellow phosphorus exhaust
表2. 不同黄磷尾气深度净化工艺技术经济指标综合对比
5. 结语与展望
黄磷尾气中成分复杂,杂质组分的存在严重制约了其资源化利用的途径。吸收法净化黄磷尾气工艺成本高、易产生二次污染,从而限制了其工业应用。吸附法净化效率低,势必造成资源的浪费。传统的催化氧化法具有操作简单,净化效率高,催化剂易于再生等优点,是目前黄磷尾气净化的常用方法,但净化后的尾气仍存有少量的P4、H2S、PH3等组分。因此,研究黄磷尾气深度净化技术以有效脱除微量的H2S和PH3尤为必要。此外,针对黄磷尾气中HCN、COS等组分并不能实现完全净化是不利现状,HCN、COS的净化技术主要集中在水解法处理。因此,未来黄磷尾气深度净化技术的开发可致力于开发催化氧化-水解耦合新技术,通过一系列手段,提高技术的净化性能、适用性范围、催化剂的稳定性和使用寿命。
基金项目
云南省环保专项资金项目(2016WF001, 2017HM001)。
NOTES
*通讯作者。