1. 引言
镁处理技术是近年发展起来的新兴非金属夹杂物控制技术,通过向钢中加入金属镁或镁合金以达到净化钢液、变质夹杂以及合金化的效果。金属镁的添加可有效变质钢中非金属夹杂物为镁系夹杂,进而控制夹杂物以细小、弥散的状态分布 [1] [2] [3] [4] 。此外,镁系夹杂物可诱导晶内针状铁素体的形成 [5] [6] ,有利于钢材焊接热影响区的组织控制和力学性能的改善。目前镁处理技术已经在船板钢、管线钢等焊接用钢中得到应用,但对于硫系易切削钢来说相关研究和技术应用的报道还较少。
硫系易切削钢是一种通过向钢中添加硫以降低切削抗力、改善切削性能的钢种,其切削性能主要取决于钢中存在的硫化锰夹杂物。但是硫化锰为塑性夹杂物,在轧制过程中易随钢材变形呈条状分布,进而导致钢材力学性能各向异性以及切削性能的恶化 [7] [8] [9] 。为提升硫系易切削钢的综合性能,控制夹杂物的形态和分布是关键,因此将镁处理技术引入到硫系易切削钢生产中。目前,镁处理技术还需要解决如下关键问题:1) 硫系易切削钢中镁处理能否有效变质夹杂物,这关系到镁处理是否适用于硫系易切削钢;2) 镁处理时钢液中镁含量应如何控制,这涉及到镁处理的效果。为此,本文以Si-Mn脱氧硫系易切削钢为例,通过FactSage热力学计算研究了Mg加入量对钢液成分及析出相的影响。本研究结果有助于扩展镁处理技术的应用领域,对于完善硫系易切削钢夹杂物控制理论具有重要意义。
2. 热力学计算方法
表1为国家标准GB/T 1371-2008中典型硫系易切削钢牌号及化学成分,由表可知易切削钢中S元素含量在0.08%~0.33%范围内。基于此,本文计算了S元素质量分数在0.01%~0.4%范围内Mg-Si-Mn-O-S钢液体系在1600˚C的夹杂物优势区域图。为避免FeS等低熔点相在奥氏体晶界析出并促进易切削相MnS生成,易切削钢中一般加入0.7%~1.2%的Mn元素,热力学计算时Mn元素含量取为定值1.0%。
由MnO-SiO2二元相图 [10] 可知,Mn-Si复合脱氧产物有SiO2固相夹杂物和MnO-SiO2液相夹杂物两类。由MgO-SiO2二元相图(见图1)可知,Mg-Si复合脱氧产物包括MgO、SiO2和2MgO·SiO2固相夹杂物以及MgO-SiO2液相夹杂物。此外,由于S的存在,Mg-Si-Mn-O-S钢液体系中析出相还包括MgS和MnS
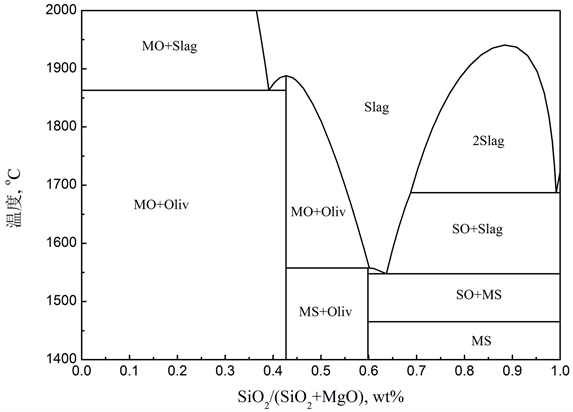
Figure 1. Binary phase diagram of MgO-SiO2. Slag: MgO-SiO2-MnO, MO: MgO, Oliv: 2MgO∙SiO2, MS: MgO∙SiO2, SO: SiO2
图1. MgO-SiO2二元相图。Slag: MgO-SiO2-MnO, MO: MgO, Oliv: 2MgO∙SiO2, MS: MgO·SiO2, SO: SiO2
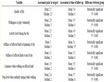
Table 1. Chemical composition of sulfur free-cutting steel
表1. 硫系易切削钢牌号及化学成分
两类固相硫化物夹杂。通常钢液中夹杂物析出的热力学采用质量分数1%假想溶液为标态,瓦格纳近似式对钢液中的溶质元素活度进行计算,并以纯物质为标态将析出的固相夹杂物活度设定为1 [11] [12] 。此种方法适用于只有固相夹杂物析出的简单钢液体系,但对于有液相夹杂物析出的复杂多元多相钢液体系则需要借助FactSage软件进行计算 [13] [14] 。
与传统的瓦格纳近似式计算钢液中溶质元素活度不同,FactSage采用“缔合物”来表征溶质元素间的相互作用,然后选择以纯物质为标态的亨利定律对反应式的吉布斯自由能进行计算 [15] 。对于复杂的熔体,采用准化学模型进行热力学计算 [16] [17] 。借助计算机强大的数值计算和处理功能,FactSage能够对复杂多元多相平衡体系进行模拟计算并对钢液成分及析出相进行预测 [18] [19] 。
在下面的热力学计算中,基于FTmisc和FToxid数据库采用FactSage中Phase Diagram模块绘制Mg-Si-Mn-O-S钢液体系在1600˚C时的夹杂物优势区域图,通过Equilib模块研究镁处理对钢液成分及夹杂物析出相的影响。
3. 结果与讨论
图2为不同脱氧条件下Mg-Si-Mn-O-S钢液体系在1600˚C时的夹杂物优势区域图,其中红色线为氧化物夹杂和硫化物夹杂分界线。红色线左侧蓝色区域为氧化物夹杂优势区,红色线右侧黄色区域为
(a)
(b)
Figure 2. Stability diagram of inclusion in Mg-Si-Mn-O-S steel at 1600˚C. SO: SiO2, Slag: MgO-SiO2-MnO, Oliv: 2MgO∙SiO2, MO: MgO, MS: MgS
图2. 1600˚C时Mg-Si-Mn-O-S体系夹杂物优势区域图。SO: SiO2, Slag: MgO-SiO2-MnO, Oliv: 2MgO∙SiO2, MO: MgO, MS: MgS
硫化物夹杂优势区。与钢液平衡的氧化物相为SiO2-MnO (或SiO2)、MgO-SiO2-MnO、2MgO·SiO2和MgO,而与钢液平衡的硫化物相为MgS。随着钢液中S含量增加MgO稳定区缩小、MgS稳定区增大,而S含量变化对SiO2-MnO (或SiO2)、MgO-SiO2-MnO和2MgO·SiO2稳定区影响不大。由以上的分析可知,硫系易切削钢进行镁处理时,若要避免MgS的生成应控制钢液成分落在左侧氧化物夹杂稳定区,若要变质硫化物夹杂应控制钢液成分落在右侧硫化物夹杂稳定区。综上可知,精准控制钢中Mg含量是硫系易切削钢镁处理的关键。
为探究镁处理对硫系易切削钢成分及析出相的影响,进一步采用FactSage中Equilib模块计算了吨钢Mg加入量对Mg-0.2/1.0Si-1.0Mn-0.2S-0.01O钢液体系成分及夹杂物析出量的影响,计算结果如图3所示。图3(a)为Si含量为0.2%时,钢液成分及夹杂物析出量随Mg加入量的变化关系。根据钢液成分及析出相变化特点,硫系易切削钢镁处理过程可分为6个阶段。
第I阶段,吨钢Mg加入量低于0.01 kg/t,钢中溶解Mg含量在0.0001%以下,此时钢液中只存在MgO-SiO2-MnO液相夹杂物。随着Mg加入量的提高,钢液中溶解Mg含量增加,溶解O含量缓慢下降,发生反应(1)。此阶段与钢液平衡溶解O含量在0.0070%以上,
(1)
第II阶段,吨钢Mg加入量在0.01~0.025 kg/t,钢中溶解Mg含量在0.0001%~0.0002%范围,MgO-SiO2-MnO液相夹杂物与2MgO∙SiO2在钢中共存。随着Mg加入量的增加,MgO-SiO2-MnO2液相夹杂物向MgO∙SiO2固相夹杂物转变,发生反应(2)。此阶段与钢液平衡溶解O含量在0.0070%~0.0060%范围,
(2)
第III阶段,吨钢Mg加入量在0.025~0.064 kg/t,钢中溶解Mg含量在0.0002%~0.0008%范围,钢中只存在2MgO∙SiO2固相夹杂物。随着Mg加入量的提高,钢液中溶解Mg含量快速增加,与钢液平衡溶解O含量从0.0060%降低至0.0020%,这主要是由于反应(3)的发生。
(3)
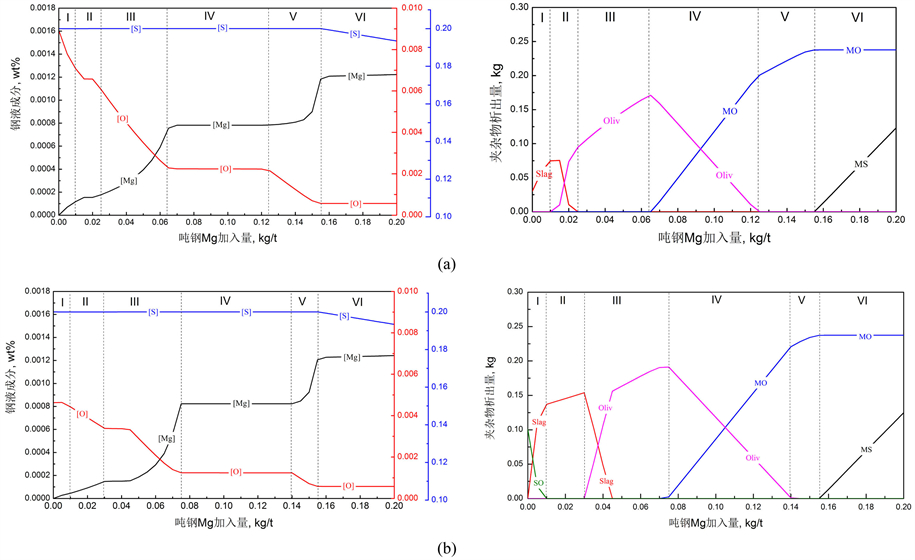
Figure 3. Effect of Mg addition on the steel composition and inclusion. SO: SiO2, Slag: MgO-SiO2-MnO, Oliv: 2MgO∙SiO2, MO: MgO, MS: MgS. (a) Si = 0.2%, Mn = 1.0%, T.O = 0.01%; (b) Si = 1.0%, Mn = 1.0%, T.O = 0.01%
图3. Mg加入量对钢液成分及析出相的影响。SO: SiO2, Slag: MgO-SiO2-MnO, Oliv: 2MgO∙SiO2, MO: MgO, MS: MgS。(a) Si = 0.2%, Mn = 1.0%, T.O = 0.01%; (b) Si = 1.0%, Mn = 1.0%, T.O = 0.01%
第IV阶段,吨钢Mg加入量在0.064~0.125 kg/t,钢中溶解Mg和O含量保持不变,2MgO∙SiO2与MgO在钢中平衡共存。随着Mg加量的提高,2MgO∙SiO2的生成量减少而MgO析出量增加,这主要是因为发生了反应(4)。
(4)
第V阶段,吨钢Mg加入量在0.125~0.155 kg/t,钢中溶解Mg含量在0.0008%~0.0012%范围,钢中只存在MgO夹杂。随着反应(5)的进行,与钢液平衡溶解O含量进一步降低至0.0006%。
(5)
第VI阶段,吨钢Mg加入量在0.155 kg/t以上,钢中溶解Mg含量维持在0.0012%,MgS从钢液中析出,发生反应(6)。随着Mg加入量的提高,MgS的析出量呈线性增加。
(6)
由以上的分析可知,随着Mg加入量的提高,夹杂物的生成顺序为MnO-SiO2(l) → MgO-SiO2-MnO(l) → 2MgO·SiO2(s) → MgO(s) → MgS(s)。
图3(b)为Si = 1.0%时,吨钢Mg加入量对钢液成分及析出相的影响。Mg加入到钢液后会将固相脱氧产物SiO2变质为MgO-SiO2-MnO液相夹杂物。与Si = 0.2%时类似,当钢液中溶解Mg含量在0.0002%~0.0008%时,2MgO∙SiO2与钢液平衡;当溶解Mg含量在0.0008%~0.0012%时,MgO与钢液平衡。当钢液中溶解Mg含量在0.0012%以上时,MgS从钢液中析出。
4. 结论
本文通过热力学计算探究了Mg加入量对硫系易切削钢成分及析出相的影响,得到如下结论:
1) 含S钢液体系Mg-0.2/1.0Si-1.0Mn-0.01O-0.2S中,当钢中溶解Mg含量在0.0002%以下时,与钢液平衡析出相为MgO-SiO2-MnO液相氧夹杂;当钢中溶解Mg含量在0.0002%~0.0008%范围内,与钢液平衡析出相为2MgO∙SiO2固相夹杂;当钢液中溶解Mg含量在0.0008%~0.0012%时,与钢液平衡析出相为MgO固相夹杂;当钢液中溶解Mg含量在0.0012%以上时,MgO和MgS与钢液平衡共存。
2) 硫系易切削钢镁处理时,随着钢中Mg加入量的提高,夹杂物生成顺序为MnO-SiO2(l)或SiO2(s) → MnO-SiO2-MgO(l) → 2MgO·SiO2(s) → MgO(s) → MgS(s)。
基金项目
国家自然科学基金项目(51674069,51374060)和国家重点研发计划项目(2017YFC0805100)。
NOTES
*通讯作者。