1. 引言
据统计,机械装备中80%的失效部件是由各种磨损和腐蚀造成的,其损耗占国民经济总收入的4%~7%,约占世界GDP的4%,每年消耗了世界30%的钢材,就我国而言,每年仅磨料磨损消耗的钢材就达到了300多万吨,造成了巨大的资源耗费 [1] 。针对我国每年大量的耐磨材料需求,我国已出现大量钢铁耐磨材料的制造企业,规模化生产耐磨奥氏体锰钢、耐磨白口铸铁、耐磨合金钢、耐磨球铁和耐磨钢铁基复合材料等耐磨材料。为了提升我国耐磨技术,促进我国耐磨材料制造行业的发展,通过与学术及技术交流、生产合作和贸易往来等方式,我国引进并消化吸收了一批工业发达国家的先进钢铁耐磨材料技术。同时,我国部分高等院校、科研院所和耐磨材料企业通过自主创新,研发了一批具有自主知识产权的钢铁耐磨材料技术,使耐磨材料行业的技术取得较大进步。作者将介绍近年来国内外钢铁耐磨材料技术的发展现状及研究进展,并就耐磨材料技术及产业发展提出几点建议。
2. 国外耐磨材料现状
随着耐磨技术和耐磨产业的快速发展,为了减少设备和工件磨损失效导致的经济损失,机械制造厂商开始大量使用高强度耐磨钢板,使得高强度耐磨钢板的需求量增长迅速。国外高强耐磨钢板在出售前已经过调质处理,强度一般 > l000 MPa,由于该种板材兼顾了超高强度及良好的塑性和韧性,被广泛应用于车辆、船舶、矿山设备、工程机械及水泥设备等方面。而我国HB400以上高强度级别耐磨钢还主要依赖进口,故我国冶金行业需重点研究与开发高强耐磨钢。目前已有多种耐磨钢材被开发出来,依照钢材成分来划分,耐磨钢可分为高锰钢,超高锰钢,低、中合金耐磨钢等 [2] 。依照钢材金相组织来划分,耐磨钢可分为奥氏体耐磨钢、贝氏体耐磨钢、马氏体耐磨钢以及贝氏体–马氏体耐磨钢。
芬兰罗奇金属的Raex瑞克斯系列、瑞典SSAB奥克隆德生产的HARDOX系列、德国迪林根的DILLIDUR系列、德国蒂森克虏伯的XAR系列和日本的JFE系列是目前国外耐磨钢板厂家主要生产的高性能耐磨钢板。
瑞典钢铁奥克隆德有限公司隶属于SSAB瑞典钢铁集团,拥有全球先进的高自动化淬火线,是世界最大的耐磨钢板和超高强度钢板制造商。根据不同硬度等级以及可供厚度,HARDOX悍达耐磨钢板可分为多种型号:HARDOX悍达400 (3~130 mm)、HARDOX悍达450 (3~80 mm)、HARDOX悍达500 (4~80 mm)、HARDOX悍达550 (10~50 mm)、HARDOX悍达600 (8~50 mm)、HiTuf (40~130 mm)和HARDOX Extreme硬度可达HB700 (10 mm, 25 mm)。由于合适的成分设计以及先进的生产工艺,悍达系列耐磨钢性能均匀,并具备高韧性、良好的弯曲和焊接等加工性能,HARDOX耐磨钢板能抵抗各种各样岩石、沙石及砾石的磨损,可用于制造铲斗、装载机、自卸车、破碎机、选粉机,溜槽以及各种耐磨衬板。
芬兰Ruukki罗奇在高强度特种钢材开发方向国际领先,Raex瑞克斯是一种具有高硬度和冲击韧性的高强度耐磨钢。Raex瑞克斯能够降低结构组件的磨损。Raex瑞克斯的轻量化设计在各种机械工程用途中得到了广泛的应用,如汽车行业、起重和运输行业以及采矿业,该钢材的供货厚度范围为2.00~80.00 mm。
德国迪林根公司的DILLIDUR400V耐磨钢淬火后平均硬度达到400 HB,可广泛应用于高磨损工况,并具备优良可加工性,且易于焊接。DILLIDUR400V可应用于土方机械、装载机械、挖泥船、翻卸式矿车、输送设备、自卸车、刀刃、切断破碎机、废物处理及回收设备。供货6~150 mm。同系列DILLIDUR500V耐磨钢平均硬度高达500 HB,厚度尺寸范围8~100 mm。
德国蒂森克虏伯钢铁公司(简称TKS)从20世纪60年代中期开始生产具有高耐磨性能的特殊结构钢板。TKS使用淬火或淬火加回火热处理,得到微观组织为致密的马氏体或贝氏体–马氏体的钢材。XAR系列钢板最大厚度可达100 mm,为了应对各种磨损工况,除传统的XAR400、450、500级别外,TKS还研发了3种可用于中低磨损工况的XAR300正火钢、可耐高温的XAR400W和用于高磨损工况的超硬级XAR600。可供选择的钢板硬度覆盖范围可达300~600 HB。
日本JFE钢铁公司从20世纪50年代中期开始生产和销售JFE EVERHARD系列耐磨钢板,JFE钢铁公司研发了超耐磨钢EH-SP,在保证钢板焊接和成型性的前提下,其耐磨性能已经超过HB500级。EH360LE和EH500LE钢板可在−40℃低温工况下依然保持良好韧性,同时具备良好的防焊裂能力,可保证焊缝的质量和安全性 [3] 。
我国宝武钢铁集团有限公司(简称宝钢)开发了BMS系列输送管道耐磨蚀钢,其中BMS1400供货厚度为3~15 mm,屈服强度 ≥ 1100 MPa,平均硬度达到450 HB,耐磨蚀性能约为Q235的两倍,同时焊接性能优良,且在−40℃低温工况下,冲击韧性αku ≥ 20 J/cm2保持良好韧性,现已成功应用于首艘由我国自主设计建造的亚洲最大自航绞吸挖泥船——“天鲲号”配套的疏浚管道。
3. 国内耐磨材料现状
3.1. 耐磨钢铁材料
3.1.1. 奥氏体耐磨锰钢
目前,Mnl3奥氏体锰钢仍是国内外生产和应用的主要系列,在日本等国家以屈服强度和耐磨性较高的Mnl3Cr2耐磨钢为主。奥氏体锰钢具有高韧性、易加工硬化等特点,在如圆锥式破碎机轧臼壁和破碎壁、旋回式破碎机衬板、大中型颚式破碎机颚板、大型锤式破碎机锤头以及大中型湿式矿山球磨机衬板等冲击载荷磨料磨损工况下,奥氏体锰钢依旧是主力耐磨钢材。标准化的出现说明奥氏体锰钢体系已较为成熟,奥氏体锰钢铸件国际标准(ISO 1352l:1999)于1999年被制定,我国则制订了高锰钢铸件国家标准(GB/T5680-2010)和铸造高锰钢金相国家标准(GB/T 13925-2010),为了突出高锰高韧性的特点,我国高锰钢铸件在国标中特别标出不含Mo、Ni的两个牌号ZGMnl3-2和ZGMnl3-3的冲击韧性αku ≥ 147 J/cm2 [4] 。
近年来,随着奥氏体锰钢制备的技术的不断进步,在其生产过程中可准确有效的控制Si和P含量,特别是限制P含量,部分出口锰钢P含量可低于0.04%。在高锰钢中添加V、Ti、Nb和Re等微量元素,可有效减少铸造高锰钢的夹渣,避免柱状晶和晶粒粗大。超高锰钢Mnl7(Mnl8)和Mn25等也得到生产和应用,其中碳含量为1.2%的120 Mn17钢被列入了奥氏体锰钢铸件国际标准。超高锰钢能够改善水韧处理后大断面厚锰钢韧性降低问题及锰钢低温韧性差等问题。但超高锰钢大冲击载荷磨料磨损工况下的耐磨性以及怎样选择相关的Mn、C含量及其配比等关键问题缺乏实际应用验证,尚待进一步研究。如何提高耐磨性并保持良好的冲击韧性是奥氏体锰钢发展的一个重要方向 [5] 。
3.1.2. 耐磨白口铸铁
耐磨白口铸铁由最初的普通白口铸铁发展出了镍硬铸铁和高铬铸铁,镍硬铸铁和高铬铸铁已成功的到较为广泛的应用。1928年Climax国际镍公司通过在普通白口铸铁中加入3.0%~5.0%Ni和1.5%~3.0%Cr,研制出铸态组织为(Fe, Cr)3C + 马氏体 + 奥氏体的镍硬铸铁。在铬含量较高的镍硬Ⅳ型铸铁中,由于部分M7C3型碳化物的存在阻碍了碳化物的网状分布,使其韧性得到改善。较普通白口铸铁,镍硬白口铸铁在强度、硬度和耐磨性方面更优,且生产工艺简单,但由于其碳化物主要构成是脆性较大的连续片状渗碳体,故较早广泛应用于泥浆泵泵体、球磨机衬板、磨煤机磨辊和冶金轧辊等。近来研究发现通过改进热处理方法,可获得贝氏体+回火马氏体组织镍硬铸铁,具备较高抗磨料磨损能力并保持良好力学性能。国外研究发现可通过Mn、Cu代替部分Ni,得到相同的性能 [6] 。
与镍硬铸铁同一时期出现的高铬铸铁的研究已取得了很大进展。研究表明,通过在高铬铸铁中加入一定量的V,可略去高温热处理工艺,直接制得高硬度的马氏体铸态组织,简化了生产流程 [7] ;通过在高铬铸铁中添加适量B并采用适当的热处理工艺,可以细化高铬铸铁中碳化物,增加基体的淬透性,在提高高铬铸铁的硬度的同时并改善其韧性,从而增加材料的耐磨性 [8] 。目前用于提高高铬铸铁韧性的主要方法有:微合金化、除气处理、热塑性变形、高温处理、悬浮铸造和过滤处理等,其机理是将高铬铸铁中碳化物的形态变为断续状或颗粒状,以此来增加韧性,使其能够应用于较大冲击载荷下的工况。由于该方面的研究尚未取得突破,为了兼顾高铬耐磨铸铁较高的硬度与良好的韧性,研发了多种镶铸工艺 [9] 。
3.1.3. 非锰系耐磨合金钢
非锰系耐磨合金钢根据碳含量的不同中可分为中碳、中高碳、高碳耐磨钢;根据合金元素含量不同可分为低合金、中合金和高合金耐磨钢;根据组织成分不同可分为奥氏体、珠光体、贝氏体、马氏体耐磨钢。目前研究的主要方向是合金钢的组织(如珠光体、贝氏体、马氏体等)与其耐磨性、强度、韧性之间的关系。此外合金钢中碳含量影响其组织成分和耐磨性,碳含量及成分组织共同决定了非锰系耐磨合金钢的耐磨性。
非锰系耐磨合金钢尤其是中碳中、低合金钢以综合提高钢的强度、硬度和韧性为主要研究方向,同时提升抗冲击及耐磨损能力。通过调整中碳中、低合金铸钢合金化、铸造工艺和热处理工艺,可改善其力学性能,应用于更多耐磨工况。此前国内外有研究者将0.30%碳含量多元低合金耐磨铸钢的硬度提高至HRC52 [10] ,目前又研发了出了兼顾高强度、高硬度及高韧性的中碳低合金铸钢,如硬度为HRC50、αku达200 J/cm2的钢种;硬度为HRC55、αku达100 J/cm2的钢种 [11] 。由于这类钢的强度与硬度大致呈正相关,可用硬度与韧性的关系来描述耐磨钢的综合性能,可通过关系式:HRC = 50 + 2.5x(1),αku = 200 − 50x(2),(其中x可取−1,0,1,2,3)大体上算得中碳低合金铸钢的硬度与韧性。可进一步拓宽中碳低合金铸钢的应用范围,延长使用寿命并取得更大经济效益 [12] 。
3.1.4. 耐磨损球铁
耐磨损球墨铸铁(abrasion-resistant ductile cast iron)是具有良好耐(抗)磨料磨损性能的球墨铸铁 [13] 。
具有一定韧性的高硬度马氏体耐磨球铁可通过液淬热处理制备得到,通过添加Mn等合金元素,铸造后再经过液淬热处理可制得高硬高韧的贝氏体–马氏体耐磨球铁。在国内这两类耐磨球铁已用于生产球磨机磨球和组合自固型衬板 [14] 。
等温淬火球墨铸铁(Austempered Ductile Iron,简称ADI)是指一定成分的球磨铸铁经等温淬火后得到的铸铁材料,它是近30年来研发的一种高科技铸铁材料。基于ADI等温淬火球铁具备高强度、一定韧性和良好加工硬化的特点,在国内外被用于制作齿轮、凸轮轴等易磨损件 [15] 。等温淬火含碳化物球墨铸铁(CADI),含有少量Cr元素,通过调整Cr含量可获得不同碳化物含量的CADI,CADI与ADI类似,也具有较高硬度、一定韧性和良好加工硬化特性,研发工作已收获一定成效,目前正试用于球磨机磨球 [16] 。
3.2. 耐磨复合材料
近年国内外耐磨材料研发的热点之一是钢铁基双液双金属耐磨复合材料,主要应用于一些磨损严重的工况。比利时MAGOTTEAUX公司研制出“Bimetal”钢铁双金属复合技术(将硬度HRC > 61的高铬铸铁耐磨层与αku > 245 J/cm2的低碳合金钢复合) [17] ;研发出以在球铁中镶嵌高硬度高铬铁的方式,制备大型立磨磨辊的“Duocast”复合技术 [18] ;研发通过镶嵌方法在立磨高铬合金磨盘(磨辊)表层添加异质高硬颗粒的“Xwin”技术;再结合Duocast和Xwin复合技术用于制备立磨磨辊 [19] 。该种复合铸造技术在磨辊和磨盘生产和应用中取得了良好效果,是一种值得借鉴的先进技术,可进一步简化、稳定工艺和控制生产成本 [20] 。近年来以复合大锤头(I > 90 kg)为标志的高锰钢镶铸硬质合金(或耐磨铸铁)复合材料已在国内得到应用,高铬铸铁/钢双液双金属复合材料大锤头也实现了产业化。复合大锤头使用年限远高于一般高锰钢锤头,双液复合大锤头使用寿命至少提高了1倍 [21] 。
陶瓷颗粒增强钢铁基耐磨复合材料日益受到国内外研究人员的关注。由于其生产成本和实际应用的限制,这类复合材料多被结合表面处理工艺制备成表层硬化复合材料。结合WC [22] 、TiC [23] 、Al2O3 [24] 、SiC [25] 等陶瓷颗粒高硬、耐磨及耐高温的特性,通过调整表面复合材料技术的工艺参数,使陶瓷颗粒与钢铁(液)产生冶金结合效果,在此基础上开发出多种钢铁基表面复合材料。使用铸渗技术(重力、压力、离心力、负压条件下),在易损件表面制备一定厚度的耐磨复合层,得到表面复合耐磨材料,可用于强烈滑动(滚动)摩擦磨损工况领域,特别是磨料磨损工况。其中WC等陶瓷颗粒增强钢铁基表面复合材料,已应用于轧钢导卫板和溜槽衬板的工业化生产 [26] 。重力铸造铸渗陶瓷颗粒增强表面复合层已现实厚度 > 15 mm,目前正在研究如何制得适用于较厚大耐磨件的多孔状A12O3等陶瓷预制体增强钢铁基表面复合材料 [27] 。如何减少或不使用粘接剂等添加剂,得到致密的冶金结合表面复合层,如何提高复合层致密度和增加复合层厚度(>20 mm),及如何在弧面等复杂表面上应用表层铸渗技术是铸渗表面复合技术亟需攻克的几个难点。
4. 耐磨表面技术
4.1. 表面淬火
表面淬火是将钢件的表面层淬透到一定的深度,而心部分仍保持未淬火状态的一种局部淬火的方法。根据加热方法不同,表面淬火可分为感应加热(高频、中频、工频)表面淬火、火焰加热表面淬火、电接触加热表面淬火、电解液加热表面淬火、激光加热表面淬火、电子束表面淬火等。感应加热和火焰加热在工业上应用最为广泛,各种表面淬火工艺的特点比较如表1所示。表面淬火可使工件获得高硬度,高耐磨性的表面,而心部仍然保持原有的良好韧性,常用于机床主轴齿轮,发动机的曲轴等 [28] 。
4.2. 渗氮处理
渗氮处理是指将工件置于一定温度及介质中使氮原子渗入表层的化学热处理工艺。经氮化处理的制品具有优异的耐磨性、耐疲劳性、耐蚀性及耐高温的特性。适用于各种高速传动精密齿轮、机床主轴(如镗杆、磨床主轴),高速柴油机曲轴、阀门等。
QPQ技术(Quench-Polish-Quench,即淬火–抛光–淬火)是由盐浴渗氮发展而来一种盐浴复合处理技术,复合渗氮工序和氧化工序,在氮化盐浴和氧化盐浴两种盐浴中处理工件,可在工件表面制得具有优
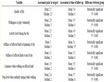
Table 1. The characteristics of various surface quenching techniques are compared
表1. 各种表面淬火工艺的特点比较
异耐磨性和抗蚀性的氮化物和氧化物复合渗层组织 [29] 。QPQ工艺将金属材料置于570℃ ± 10℃工作温度的盐浴中,金属表面在反应后会形成一层优质而致密的化合物层。该化合物完全由ε氮化铁组成,能够高效地提高金属表面的硬度、致密性、从而提高耐磨性能。处理后金属材料表面硬度值的高低主要取决于钢中的合金元素,合金元素含量越高,则其渗层硬度越高 [30] [31] 。其中碳钢、低合金钢,如20#、45#、T10、20Cr、40Cr等,渗层表面硬度500~700 HV;合金钢如3CrW8V、Crl2MoV、38CrMoAl、1Crl3和4Cr13等,渗层表面硬度850~1000 HV;高速钢、奥氏体不锈钢如淬火的Wl8Cr4V、W6Mo5Cr4V2及1Crl8Ni9Ti等渗层表面硬度1000~1250 HV;铸铁渗层表面硬度 > 500 HV等 [32] 。
4.3. 喷涂技术
1) 热喷涂技术
热喷涂技术是利用火焰、电弧或等离子体,将某种线状或粉末状的材料加热至熔化或半熔化状态,然后借助焰流本身或压缩空气加速形成熔滴,高速喷向经预处理后的基体表面,沉积形成涂层,可强化材料表面的耐磨、耐蚀、耐高温等性能。热喷涂金属耐磨涂层是研究和应用较早的喷涂涂层,常用的有金属(Mo, Ni)、碳素钢和低合金钢,不锈钢和Ni-Cr合金系列涂层 [33] [34] 。一般采用火焰喷涂、等离子喷涂、高速火焰喷涂及气体爆炸喷涂工艺。涂层与基体结合强度较高,耐磨性、耐蚀性好,可用于修复已磨损或预保护易磨损机械加工件 [35] 。
2) 冷喷涂技术
冷喷涂技术是近年来国际上的研究热点新兴技术之一,是一种以压缩气体(氮气、氦气、空气或混合气体等)作为加速介质,带动金属颗粒在固态下以极高速度撞击基板,使颗粒发生强烈塑性变形而沉积形成涂层的新型喷涂技术(如图1所示),其高温、低速的技术特点尤其适用于温度敏感(非晶、纳米晶等)、相变敏感(金属陶瓷等)、氧氮敏感(Cu, Ti等)材料涂层的制备,喷涂过程中对粉末粒子结构和基体几乎无热影响,制备的涂层具有高致密、耐腐蚀、耐磨损、防污损等优点,可显著提高涂层的致密性和降低孔隙率 [36] [37] 。
近年来,金属间化合物涂层和非晶态涂层得到了愈来愈多的应用。常见的金属件化合物涂层有Fe-Al、Ti-Al及Ni-Al合金涂层 [38] [39] [40] 。非晶态涂层被证明具有优异的耐磨耐蚀性,目前Fe-Ni-Cr-B-Si系合金涂层、Fe-Cr-B系合金涂层和Ni-Cr-Mo-B系合金涂层已得到初步应用 [41] [42] [43] 。
4.4. 硬面堆焊
硬面堆焊是使用焊接方法在工件表面或边缘熔敷一层硬面材料的表面强化技术。硬面堆焊主要包括:电弧堆焊、气焊堆焊、埋弧堆焊、等离子弧堆焊和激光堆焊等诸多方法 [44] 。不同的堆焊工艺对硬面合金层的微观组织和力学性能有重要的影响 [45] 。根据堆焊材料的形状可将堆焊材料分为丝状、带状、柱条状、
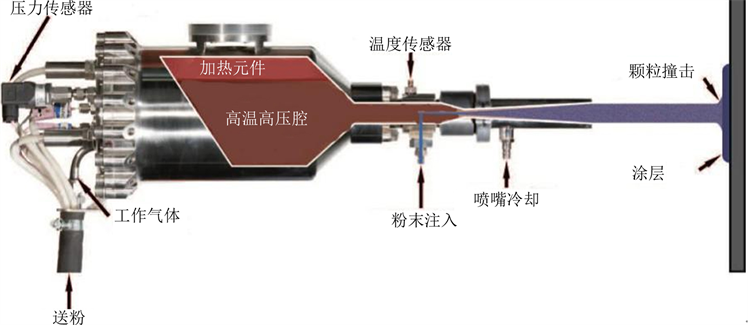
Figure 1. Schematic diagram of cold spraying
图1. 冷喷涂技术原理图
粉粒状、块状等。堆焊材料的使用性能由其化学成分决定。根据堆焊层的化学成分和组织结构,可将堆焊材料归纳为Fe基、Ni基、Co基、Cu基、和WC几大类 [46] 。由于Fe基堆焊合金成分变化范围宽,韧性和耐磨性配合好,能用于多种耐磨工况,且价格相对较低,其应用最为广泛。铁基合金中Fe-Cr-C系耐磨堆焊合金具有抗磨损性能优异且极具性价比,广泛应用于工矿企业的抗磨损部件 [47] ,如煤矿破碎机滚筒、衬板,鼠笼式粉碎机耐磨击棍,入料保护箱 [48] ,水泥厂排粉风机叶片、磨盘衬板 [49] ,石油钻杆接头耐磨带 [50] ,火力发电厂立式磨煤机磨辊,钢厂轧辊等。
4.5. 激光熔覆
激光熔覆又称激光涂覆或激光熔敷,是表面改性技术的一种重要方法,其实质是利用高能密度激光束将具有不同成分、性能的合金与基材表面快速熔化,在基材表面上快凝固形成与基材具有完全不同成分和性能的无裂纹、无气孔的冶金结合层 [51] 。
耐磨涂层是激光熔覆中研究最多、应用最广的涂层之一。激光熔覆涂层的耐磨性取决于不同增强相及其在熔覆层中的含量和分布。根据熔覆材料的不同,激光熔覆材料体系可分为:铁基合金、镍基合金、钴基合金和金属陶瓷等 [52] [53] ,熔覆层化学成分和加工工艺决定了熔覆层的组织结构,其组织和相组成又决定了覆涂层的耐磨性能 [54] 。其中激光熔覆铁基合金最为常用,适用于改善温度要求不高(˂400℃)的耐磨零件的耐磨性,所用粉末主要有不锈钢类和高铬铸铁类,分别适用于低碳钢和铸铁基体。其熔覆层组织为非平衡的奥氏体和M7C3碳化物,由于固溶强化、位错与碳化物交互作用使熔覆层具有920HV0.2的较高硬度 [55] [56] 。
4.6. 物理、化学气相沉积
气相沉积通常分为物理气相沉积(PVD)和化学气相沉积(CVD)。PVD是指在真空条件下,通过加热或使用高能密度的电子束蒸发成膜物质,生成蒸发粒子与离子,并在基体表面沉积成膜的方法。PVD制备薄膜的基本方法为真空蒸发镀膜、离子镀膜和溅射镀膜。PVD最初应用于航天、航空和半导体工业等领域,而在近几十年才开始着重研究应用PVD改善和强化机械零件的耐磨性能,目前该工艺已广泛地应用于工模具和机械零件的表面强化处理 [57] [58] 。
CVD是利用一种或几种气体(金属卤化物的蒸汽、氢气和其它化学成分的气体),在高温下进行分解、合成等气、固反应,或利用化学传输作用,在加热基体表面形成固态沉积层的方法。CVD技术用于表面强化始于20世纪60年代,目前采用CVD制备硬质膜已广泛用于强化各种工件的耐磨性能 [59] [60] 。
CVD处理温度住900℃以上,虽有很好的膜基结合强度,但钢基体发生软化,需再次真空淬火,工艺复杂易导致工件变形,因此目前主要用在硬质合金领域;PVD的处理温度可降至500℃以下,膜层残余压力高,易导致脆性开裂和剥落,且线性处理工件时须转动或摆动,致使真空室的设计难度增加和镀膜无效。为了兼具CVD和PVD的长处,发展了等离子体辅助化学气相沉积(PCVD)技术,利用等离子体而不单靠热激活来提高离子活性,处理温度可降到600℃以下,基本满足处理高速钢,热作模具钢等材料的温度范围,同时结合强度、残余应力等力学性能和均匀性、镀膜速率等工艺性能介于PVD和CVD之间。还可用于制备薄膜材料的多元合金化及梯度薄膜的制备,并广泛应用于增强工模具钢表面耐磨性能,如TiN、Ti(C, N)、(Ti, Al)N、DLC(类金刚石碳)等硬质膜 [61] [62] [63] 。
5. 耐磨材料行业发展
国外已对耐磨材料系统研究达100多年。高锰钢、合金钢、镍硬铸铁和各种白口铸铁及高铬铸铁等不同类型的耐磨材料的研发及生产工艺已较为完善。部分大公司已采用较为成熟的工艺和材料集中批量生产如球磨机磨球、衬板等一些耗费大的易损件,严格控制从冶炼到铸造和轧制以及后续热处理等工艺流程。制造工艺和设备的完善以及标准化为国外耐磨材料行业的主要发展方向。
经过多年研究与发展,国外耐磨材料的生产、应用已经趋于稳定,已形成独有的系列产品和国家标准、企业标准,通过较先进和现代化的生产设备和质量控制手段生产性价比高且质量稳定的耐磨材料,耐磨材料也从单一的钢铁材料发展到金属复合材料、粉末冶金材料、陶瓷及其复合材料、塑料(氨酯和橡胶聚)及其复合材料等多种材料,并将这三种材料组合使用,如复合钢与橡胶、陶瓷与金属、橡胶与陶瓷。国外耐磨材料基础理论和应用研究一同发展,耐磨材料含碳量范围可从0.3%至1.0%以上,合金元素含量则从低、中合金至高合金,开发了中、高碳或高碳合金耐磨钢,提高了耐磨钢的硬度及淬透性 [64] 。
耐磨材料在我国已历经一个多世纪的发展。近年,我国冶金、电力、水泥及煤炭等行业的蓬勃发展,促使耐磨材料行业快速发展,耐磨技术显著进步。我国耐磨材料产量已连续多年居世界首位,耐磨技术的研发也取得了长足进步。虽然我国已成为铸造大国,但是在高速发展的同时我国耐磨材料行业暴露出许多问题,耐磨产品质量和规模还远不及铸造强国。国产耐磨材料在强度、硬度和稳定性方面相对较差。从耐磨钢级别和规格来看,国外生产的耐磨钢布氏硬度覆盖600~700 HB,厚度规格覆盖6~120 mm,而国内生产的耐磨钢硬度最高到500 HB,厚度规格范围远小于国外产品;从性能上对比,国产NM360强度、硬度指标和国外产品相当,但其韧性指标还有一些差距。
国内耐磨材料市场分布较散,企业规模小,生产的机械化和自动化水平偏低,耐磨产品仍以低端产品为主。结合我国耐磨材料行业发展现状,我国耐磨材料可在以下几方面开展工作:
1) 开发新型的节能环保经济型耐磨材料
社会的发展必将淘汰一些高能耗和重污染的产品和企业。今后耐磨企业应当着重开发少用铬、钼、镍等贵重金属元素的耐磨钢铁材料以节约资源、降低成本。从合金成分设计和制备工艺流程发掘低成本材料制备潜力,大力开发低成本高性能的耐磨材料。
2) 研发耐磨复合材料
我国耐磨复合材料起步较晚与国外存在较大差距。结合我国实际耐磨工况特点,遵循耐磨复合材料的结构形式和耐磨材质的多样化,采用灵活的复合形式和多种材料(金属、陶瓷、塑料)及复合工艺制备耐磨材料部件。
3) 研发微合金化、细晶化耐磨钢
细晶化、微合金化、纯净化和均匀化是我国钢铁生产的努力方向,较大提高了钢铁材料的质量和性能。但钢铁耐磨材料在这方面还较为滞后,因此开发超细晶粒、微合金化耐磨钢应是耐磨钢铁材料发展的方向。
4) 采用表面强化技术
表面强化技术是提高和改善易磨损件耐磨性能的重要方法。采用表面热处理、热(冷)喷涂、激光熔覆、物理和化学气相沉积、镀层等表面强化技术不仅可强化工件表面耐磨性制备耐磨涂覆层,而且可对已磨损失效的部件进行修复。应注重表面强化技术在耐磨材料领域的应用。
5) 规范化、规模化生产,把控生产制备工艺
我国耐磨材料产品生产企业中小型企业多,设备相对落后,技术力量相对薄弱。由于我国冶炼、铸造、热处理工艺水平落后,较难提高耐磨钢的含碳量和合金含量,所以衬板多使用韧性较好的高锰钢。因此,为了确保生产高质量的耐磨产品,耐磨材料企业在生产过程中,应严格控制生产工艺,使生产规范化、规模化、现代化。