1. 引言
1.1. 研究背景
AP1000蒸汽发生器系统(Steam Generator System,简称SGS)是核电站动力装置中连接一、二回路的枢纽设备。由于AP1000的特殊结构 [1] ,国家核安全监管部门对于该设备的役前和在役检测都提出了新的要求,其中就包括了蒸汽发生器出水接管和主泵连接焊缝的无损检测 [2] 。检测焊缝如图1所示。
针对其结构特点,我们已经设计了基于UR10机器人的检测机器人辅助臂 [3] ,如图2所示。UR10机器人与PITCH关节连接,末端关节搭载超声波探头架,深入SG接管焊缝处进行扫查 [4] 。本文将在此基础上,设计该机构的送入装置,对其进行力学性能分析,并完成其控制系统的设计。
1.2. 技术难点
图3(a)是正对SG水室人孔法兰外表面的栅格板夹层,表面过度粗糙是送入装置系统定位于栅格板上
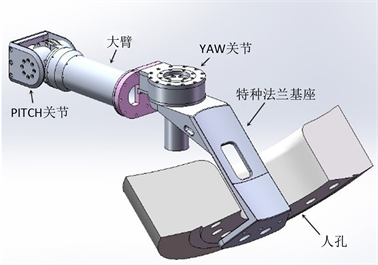
Figure 2. Auxiliary arm of inspection robot
图2. 检测机器人辅助臂
的最大阻碍之一。图3(b)是SG水室周围的过道,其宽度仅有约0.3 m,对装置的运输造成了较大的制约。
考虑到现场辐射,焊缝检测需要在较短的时间内进行,这就要求安装、扫查、拆除的整体流程在短时间完成。所以要对检测机器人进行模块化设计,并要求能在短时间内完成装配。
此外,检测机器人加上送入装置的自由度较多,且机器人在执行任务的过程中不能对蒸发器或检测装置造成损伤,这对其控制系统的设计提出了非常高的要求。
2. 送入装置的结构设计
结合设计需求和现场环境,设计的送入装置总体方案简图如图4。底座提供水平方向的自由度;升降机构提供上下升降的自由度,且在上下升降的同时,也会带动上平台的水平平动;摆臂机构提供选装自由度以调整辅助臂相对于人孔的位置。
2.1. 水平移动机构设计
水平移动机构是整个检测机器人的底座,将会直接固定在蒸汽发生器外围的栅格板上,升降机构则通过滑块导轨机构与其相连。经过计算,水平移动机构的重量在60 kg左右,且长度较长。考虑到0.3 m狭窄的过道,将整个水平移动机构直接运输进现场显然是不现实的。因此底座需要二次模块化。本文将整个水平移动机构划分为Part 1,Part 2,Part 3这3个部分。每个部分都有可调节高度地脚支撑并调节水平平衡。Part 1中还含有工装定位槽、滑块组件等用于快速装配。二次模块化之后水平移动机构使用同步带轮进行驱动,主要是利用同步带的可拆性。为了缩短装配时间,为同步带轮也设计了快速装配结构,并将其驱动装置放置于Part 1和Part 3上。三个部分最终结构设计分别如图5、图6、图7所示。
2.2. 升降机构与摆臂机构设计
升降机构提供了Z轴向自由度的移动和X轴向自由度的平动,两者结合控制着整个UR10机械臂和超声探头架的空间位置。摆臂机构用来配合辅助臂的特种法兰基座,使UR10机械臂能顺利进入SG水室。为了简化整个安装流程,减少操作人员滞留于核站工作间现场的时间,将这两部分进行合并为Part 4,三维模型如图8所示。
通过升降平台底部的滚珠丝杠,将丝杠螺母的水平运动转化为平台的竖直运动。目前市面上常见垂
直运动装置运动时,升降平台上下底板始终处于同一竖直平面,与现场工况相矛盾。通过对传统升降平台的结构进行改进,使得上平板在上升的同时,也会向前平动,避免与现场工况发生干涉。使用线性致动器取代传统的电机和谐波或RV减速器组合驱动,是为了避免与蒸汽发生器外壁的干涉情况,并且好处是使得摆臂机构更加平衡,有利于倾覆力矩的克服。
3. 快速装配设计
由于焊缝检测过程需要在短时间内完成,不仅需要对整体机构进行模块化设计,还需要各个模块之间能快速连接以缩短装配时间。
受限于现场条件问题,本文将整个结构分为了如上所述的Part 1~Part 4,并将之前设计的机器人辅助臂作为Part 5。现场安装时,需要将各个模块进行快速连接以完成快速装配。接下来将介绍各个部分之间的连接方式。
在装配过程中,一开始对于Part 1相对于人孔中心平面的位置校准十分困难,因此需要设计一个定位工装。配合人孔位置和Part 1上的定位卡口,通过工装上的升降装置,做到对Part 1迅速的安装和固定。
Part 1将会固定于现场的栅格板上,通过可调节高度地脚螺栓进行连接。当通过定位工装确定好人孔中心平面与水平移动机构的中间平面的位置以后,Part 2将会通过快接装置与Part 1相连。
首先Part 2将通过一组定位销迅速与Part 1确定好相对位置,接着通过水平式压紧器给Part 2进行压紧,实现与Part 1的快速连接。如图9所示。
Part 2和Part 3之间与上述Part 1和Part 2的连接有异曲同工之处,都是利用定位销和水平式压紧器进行快速连接。
Part 4要固定于Part 1之上,因为在运输过程中,为了减少滑块安装的复杂性,Part 1上的导轨滑块将和Part 1的导轨配合在一起,而滑块又需要和Part 4的底面平台相固定,因此滑块之上需要进行一个中间件的设计,用来与Part 4的底面平台快速连接。
其具体的设计三维图如图10所示。
所采用的快接方式和前面所讲的方式一样,只不过Part 4的底面平台将与上面设计的快接板相固连。快接板的机构为卡口式,配合底面平台可以先大致定位,再通过定位销精确定位。
另外Part 4作为运动模块,需要被同步带轮所驱动,因此底面平台与同步带之间也要形成快接装置。主要根据同步带的齿形进行设计,可以使同步带完美契合到夹板槽内部,在通过固定于底面平台底部的水平压紧器将其定位。
Part 5与Part 4的相连这通过螺栓连接。摆臂的形状是根据特种法兰基座所设计的,类似于一个卡槽,将特种法兰基座大致定位于其中,在通过螺栓连接即可。
Part 5与UR10利用UR10自身的孔,进行相应的螺纹连接即可。
最终的整机三维模型图如图11所示。
4. 送入装置控制系统的设计
4.1. 硬件设计
图12为控制系统的硬件结构总图。图13是执行模块的连接示意图。由于UR10机器人内置关节控制模块,通过以太网与其控制盒进行通讯 [4] ,即可实现上层运动控制,在硬件上不需要进行其他处理。以
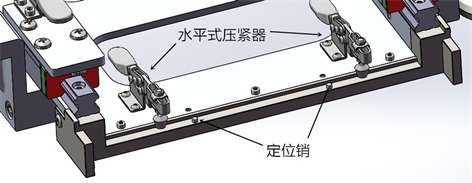
Figure 9. Quickly assembling device for Part 1 & Part 2
图9. Part 1与Part 2快接
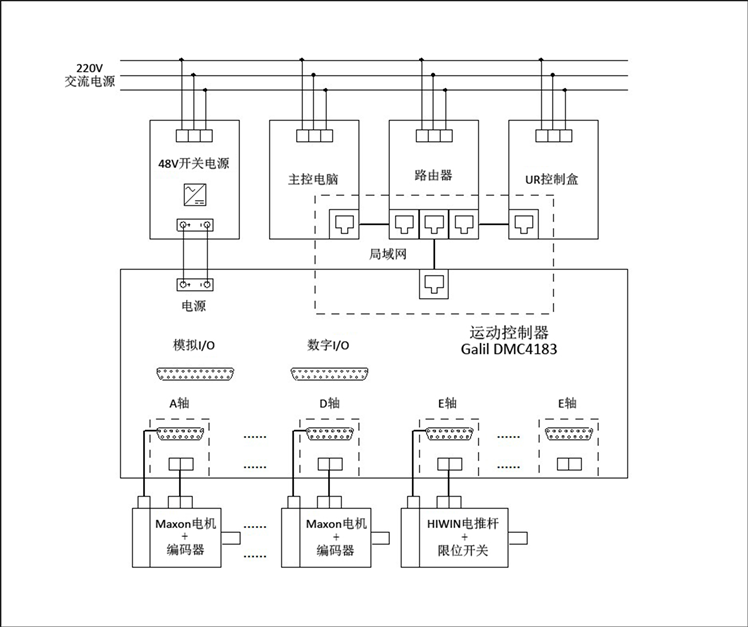
Figure 13. Executive module connection diagram
图13. 执行模块连接示意图
下将对底座的控制进行详细讨论。
项目中采用的是来自Galil的多轴运动控制器DMC41x3,并内置电机驱动器AMP430x0。运动控制器向驱动发送电机速度控制指令,驱动器根据指令调节电机两端的电压方向和幅值,从而控制电机速度;与电机相连的编码器信号反馈给运动控制器形成闭环的控制回路。
底座中有4个关节采用了MAXON的直流有刷电机作为驱动,为了实现关节位置的闭环控制,还需要结合对应的电机编码器。
线性致动器选择HIWIN线性致动器中的LAM2-2型号 [5] ,其控制较为简单。通过施加24伏电压进行电机的驱动,电压的正反决定运动方向;当运动到任意一个极限位置时触发相应的限位开关从而停止电机,同时通过对应的引脚输出电平信号。
4.2. 软件设计
本次研究中采用的Galil DMC 41x3运动控制器,支持USB,串口和以太网连接。与上位机建立物理连接之后,可根据应用场景选择官方软件进行操作或基于官方跨平台的函数库进行二次开发。利用Galil官方提供的GDK (Galil Design Kit)验证控制方式和控制逻辑无误后,需要基于Galil提供的函数库进行二次开发将电机的控制整合到主控软件中。
图14是通过调用函数向DMC4183发送指令的基本流程,根据实际应用发送不同的指令即可完成对电机的控制。项目中主要对各个轴的位置进行独立控制,控制逻辑和对应的指令如下:
1) 指定一个或多个轴的目标位置(PA指令)。
2) 指令各个轴的加速度和减速度(AC和DC指令)。
3) 指定各个轴的目标速度(SP指令)。
4) 驱动器使能(SH指令)
5) 根据当前设置开始运动(BG指令)。正常情况下,关节转动到指定位置之后自动停止。
6) 运动期间,可以查询当前各个轴的位置和速度等信息(TP和TV指令)。
以上与位置,速度和加速度相关的指令中都是以编码器信号个数而不是关节角度作为单位,需要在上位机中自行完成编码器信号个数和旋转角度之间的转换。
将Maxon电机,编码器和DMC4183控制器进行连接,并通过开关电源供电。通过计算机发送运动指令可以控制电机的位置,方向和转速。对底座电机进行简单测试,得到目标位置和实际位置分别是100000和99991个脉冲信号,定位误差小于0.01%。
5. 仿真
将机器人的3D模型导入V-REP进行模拟仿真。为了加快模拟速度,对机械结构进行了合理的简化。图15为模拟器界面。
以下将对检测过程进行仿真。其中UR10机器人的模拟器可以从Universal Robot的官方网站下载,
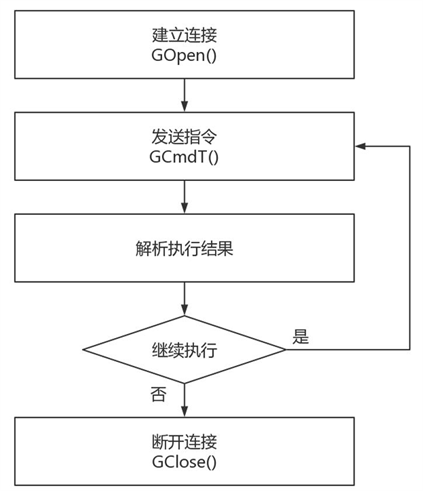
Figure 14. Galil C function library’s operational flowchart
图14. Galil C函数库的基本操作流程
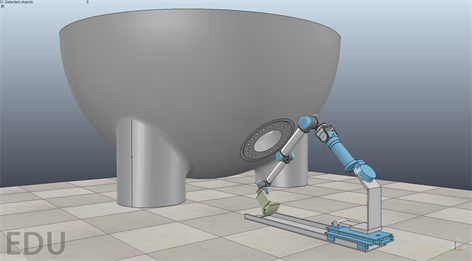
Figure 15. Simulator of the evaporator and the weld-inspection robot
图15. 检测系统和蒸发器的模拟器
而底座的控制器则由主控软件内部自行模拟。通过调节关节位置结合模拟器碰撞检测,规划出一条安装路径,将UR10通过人孔送入蒸发器。大致过程见图16。
6. 结语
经过三维软件的建模与仿真,确定该送入装置可以在不与蒸汽发生器产生碰撞的情况下将焊缝检测机器人从人孔中送入。将送入装置的控制系统整合至主控软件之后,主控软件已经实现了对底座和UR机械臂的控制。下一阶段,会将整个系统应用在1:1的蒸发器模型中,确认方案的可行性之后正式用于现场检测。