1. 概述
3D打印技术(Three Dimensions Printing Technology)是快速成型技术的一种,它利用计算机三维建模软件来设计3D模型,所用材料一般为离散型的塑料、陶瓷或者金属粉末等 [1]。制造物体的方式与传统的整体加工的方式不同,是通过按照层数堆叠打印的方式来进行制造。3D打印技术由于这个特性,也被称作“增材制造”技术。这样的制造方式在加工过程中几乎不产生任何废料,对于原材料有着很高的利用率。在贵重金属材料的加工上有着突出优势。该项技术涵盖了三维建模、电子控制、复合材料科学、电子激光等多种技术。目前可以应用的3D打印加工工艺主要有光固化打印(SLA)、熔融沉积打印(FDM)、选择性激光烧结打印(SLS)以及聚合物喷射技术(Poly Jet)。其中金属材料的3D打印技术是3D打印技术中最重要的分支,也是最具有工业价值的领域。现阶段,金属材料的3D打印技术比较成熟的加工工艺主要有:激光工程净成形技术(LENS)、激光选区熔化技术(SLM)和电子束选区熔化技术(EBSM) [2] [3]。
从20世纪70年代开始,3D打印技术经过了几十年的发展已经越来越受到各个国家和市场的重视。可以查知的3D打印行业的2012年度行业报告(美国技术咨询服务协会Wohlers Associates发布)中提到,全球3D打印行业各个公司企业在2011年到2012年年底的营业额为17亿美元左右。截止到2012年年底,3D打印技术市场的年增长率为30%,3D打印行业市场情景巨大,是一个产值百亿美元的朝阳产业。
在现阶段3D打印技术在各个行业的分布仍然不太合理,这也是受3D打印技术自身特点所限制,消费电子领域仍然占主导地位,约20.3%;其他主要应用在汽车、医疗/牙科、工业/商业机器和航空航天领域。在民航领域,3D打印技术仍然有很大的发展空间。
2. 3D打印技术在民航机务维修领域研究现状
欧美发达国家很早就将目光锁定在3D打印技术行业。美、英、德等国的3D打印技术已经可以被应用方面到实际的生产制造领域。上述几个发达国家也是首先将3D打印技术应用于高精尖制造领域。在民航领域,3D打印技术已经得到了国外航空公司的广泛关注。波音、空客、通用电气等全球领先的航空制造企业都将3D打印技术列入企业的战略性发展计划 [4]。
在金属零部件制造方面,3D打印技术已经可以完整的制造各种金属零部件。西门子公司已于2014年成为全球制造业第一个可以利用3D打印技术进行金属零部件生产的制造公司。由此开始,民用航空领域也开始逐步应用3D打印技术。专业的3D打印技术研发公司——莫里斯技术(Morris Technologies)于2012年被美国通用电气(GE)收购,通用电气计划将该公司的3D打印技术应用于生产航空发动机的燃油喷嘴,并用于新一代民用航空发动机——Leap上;罗·罗公司也于2013年开始利用3D打印技术试制喷气发动机的金属零部件;美国的霍尼韦尔公司利用3D打印技术开始试制航空发动机的热交换器和金属支架;德国MTU公司也从2018年起开始研制使用3D打印技术制造形状复杂的高压导向器叶片组件 [5]。
我国的3D打印技术起步较晚,但是也在航空领域取得了辉煌的成果 [6]。成飞与沈飞在歼击机的研制过程中融入了3D打印技术,利用该项技术制造的钛合金复合零部件大幅度的减轻了飞机结构重量。在民航领域,中商飞设计制造的国产大飞机C919在设计过程中也大量采用了3D打印技术制造的钛合金技术部件。东航技术的3D打印技术以飞机部件的3D数学模型结合材料科学、飞机结构、快速成型等技术,通过电脑设计完成飞机部件数字切片,并将信息传递到3D打印机上,再经分层加工与叠加成型技术生成飞机部件实体,所制部件一次成型,实现了对所需部件的精确复制(见图1)。东航技术充分利用3D打印技术灵活生产、易于装配、快速更换等优势,有效提升供应链效率,降低部件采购成本,并建立起完整的部件设计与制造流程,在客舱定制化改造、公务机改造等领域表现出强大的工程能力,真正实现向航空部件制造领域的拓展 [7] [8]。
3. 机务维修现状分析以及3D打印应用优势分析
3.1. 机务维修领域现状分析
根据中国民航业2017年行业发展统计公报显示,截止2017年底,中国民用航空全行业运输飞机期末注册在册的飞机架数为3296架;中国到2017年为止共有已经颁发证件的有效运输机场229个;在民航航线方面,国内航线3615条,其中港澳台航线96条,国际航线803条;在飞行小时上,全行业完成通用航空生产飞行83.75万小时 [9]。中国的机务维修领域经历了几十年的发展,从无到有、从一穷二白到各大维修企业云集。形成了以北京飞机维修工程有限公司、广州飞机维修有限公司、中国东方航空股份有限公司维修基地为主体的三大民航维修系统维修基地,辅以厦门太古飞机工程有限公司、中国西南航空公司飞机维修基地、四川斯奈克玛发动机维修中心、摩天宇航空发动机维修公司等企业为主的部件维修基地。形成了以机体(内舱)、发动机、机载电子设备以及起落架(部件)为分类的包含了飞机各个主要部件维修、翻修、改装的多层次宽领域的维修格局。各大航空公司以及维修企业也都相对于发展初期有
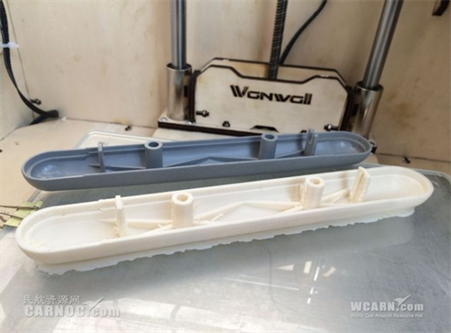
Figure 1. China eastern airlines pioneered the successful use of 3D printing technology to manufacture aircraft components.
图1. 东航首创成功运用3D打印技术制造飞机部件
了数量和质量上的提升。
但是,随着我国民航业不断发展,随之暴露出的问题也越来越多。
1) 人力资源与人员培养问题。维修企业所进行的机体部件维修和机载附部件维修工作需要许多机务维修领域专业人员进行,而我国的专业维修人员存在很大的行业缺口,一部分原因是我国国内的机务维修人员薪资水平相对于国外有着不小的差距,导致大量人才流失;更重要的原因是,成熟的机务维修人员匮乏严重,培养模式不成熟,效率低。这两方面的原因很大程度上阻碍了我国机务维修领域的健康发展。
2) 制造企业缺少核心技术。中国的机务维修企业一直深受缺少核心技术的困扰。国际上民航领域的OEM和MRO中的巨头公司诸如美国GE、波音、空客、罗尔斯罗伊斯、霍尼韦尔等一直对公司所掌握的关键性核心技术进行技术封锁,对与在中国市场上所展开的合作方式也一直是以所谓的“服务”模式来进行合作。在CAAC批准的中国国内各个维修机构可以修理的飞机部件近37,200项(次),这其中仅有30%是可以在国内完成修理的,近80%的部件需要国外公司进行不同方式的修理。这样的模式下无疑给中国的航空企业带来了很大的运营成本。
3) 航空公司航材管理的问题。截止2017年底,中国民用航空全行业运输飞机期末注册在册的飞机架数为3296架。如此庞大的机队规模,是中国国民经济发展的体现。但是三千多架飞机的日常运营无疑很大程度上的增加了各个航空公司的日常维护和维修成本。到目前为止,中国国内的各个航空公司在航材管理上仍然存在许多问题。首先是航材库存种类不科学;同时,各个公司一般情况下会大量采购常用的航化品、零部件以及密封件等航材,反而忽略一些不常用航材的采购;另外一个方面是航空公司的航材供应链存在诸多问题。这样的管理方式很大程度上是由于航材生产工艺的限制,改进航材生产工艺可以很大程度上觉得当前航材部门的问题。
3.2. 3D打印技术应用优势分析
现阶段机务维修领域存在的问题,这些问题在很大程度上阻碍了我国机务维修领域的高效发展,利用3D打印技术可以有效解决机务维修领域目前阶段存在的部分问题。
1) 3D打印技术解决航空发动机维修中零备件采购
3D打印技术已经得到了国外航空公司的广泛关注,3D打印的航空发动机零部件不断涌现(见表1)。据报道,西门子公司已于2014年成为全球工业制造业第1个在金属零部件实际生产中应用3D打印制造技术的公司。在发动机使用维护过程中,特别是进口发动机,到寿件、易损件、必换件等零部件是航空发动机维修企业最棘手的难题 [10]。
3D打印发动机零部件的出现解决了发动机维修所需备件的采购难题。通过掌握3D打印技术,制造出所需要的零备件,使原本采用传统方法短时间内无法满足设备、工艺等基础条件的航空发动机维修企
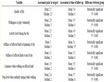
Table 1. Engine parts for 3D printing
表1. 3D打印的发动机零部件
业也具备了零部件制造能力。对于小批量需求的航空发动机维修企业来说,3D打印既节约了制造成本,又缩短了维修周期。
2) 3D打印技术提升航空发动机维修中零部件再制造能力
航空发动机关键核心部件在工作中损伤报废严重、报废量大、损伤模式复杂,成为制约发动机维修周期和成本的主要因素,如烧蚀、裂纹、异物打伤等,因此,压气机叶片、涡轮叶片等航空发动机关键核心部件的再制造技术是欧美发达国家严密封锁的关键核心技术。3D打印为再制造提供了个性化、高效率的实现手段,是欧美发达国家首选的航空发动机零部件再制造技术。3D打印技术作为航空发动机零部件再制造的重要技术手段,是目前国内外前沿研究技术和应用领域之一。
3) 3D打印再制造技术在高压涡轮叶片维修中的应用
某型航空发动高压涡轮工作叶片采用定向凝固镍基高温合金精密铸造而成。1个大修周期后高压涡轮工作叶片在工作中叶尖磨损严重,部分叶尖已磨损至凸台,平均磨损量为0.6~0.7 mm,43%的叶片已磨损至凸台。高压涡轮工作叶片在工作中与之配合的是外环上采用等离子喷涂制备的具有3层结构的NiCrAlY封严涂层。由于在NiCrAlY封严涂层的底层和中间层添加高温抗氧化钎料进行真空热处理,同时在面层中添加提高孔隙率的聚苯脂,具有较好的可磨耗性,但是该涂层硬度高(HR45Y = 55~75),因此,在工作中涡轮叶片叶尖易被封严涂层磨损。
分析表明,高压涡轮工作叶片叶尖主要是由于氧化和燃气腐蚀加剧了磨损。叶片为定向凝固组织,常规的氩弧焊、钎焊等技术难以实现定向组织修复。针对叶尖磨损故障和复杂型面的特点,采用激光净成形技术(LENS)对高压涡轮叶片进行3D打印再制造,再制造后的叶片接长组织呈定向晶,经过长期试车考核后满足航空发动机一个大修周期要求。
随着金属产品3D打印技术的不断成熟和航空发动机零部件3D打印技术体系的不断发展,3D打印技术将在解决航空发动机维修中的零备件采购难题、提升航空发动机零部件再制造能力、战场应急抢修等方面发挥着不可替代的作用 [11]。
4) 零部件制造的应用
传统的航空领域工业加工制造业在生产一件产品是需要配置一条完整的生产线,因航空产品需要满足CCAR规定的适航性要求,对于生产出的零部件所用材料、零部件强度、质量都有这比较硬性的高要求,这就要求航空零部件生产厂家的生产设备具有极高的精度。3D打印技术适用于各种结构复杂的小型零部件的快速制造。小型、复杂的零部件在大型高精度机床上很难加工,并且对于高精度机床的刀具要求极高,会大量增加制造成本。相比于传统加工制造技术,3D打印技术是一种增材制造技术,将在整体原材料上切削加工变为由若干个二维平面层层堆叠的加工方式,很大程度上降低了复杂零部件的制造难度。3D打印技术在零部件制造上最主要的特点就是可以忽略零部件结构上的复杂程度,利用3D打印制作任何复杂的零件都和制作一个等量耗材正方体的难度相当。这样的特点十分适合制造小型、多样化、结构复杂以及原材料价值高的零部件。
飞机异性零部件上的应用。在机务维修领域,会接触到很多外形结构复杂的异形零件。异形零件在飞机上一般不是需要经常更换的部件,但是飞机由于在高空环境下的极端环境以及发动机内部的极端环境下,可能发生结构的形变,飞机落地之后,温度、水分等物理条件的改变会导致异形零件发生腐蚀的情况。这时候可以利用3D打印制造出同样零件进行对比、测量判定磨损或者腐蚀情况。飞机上的某些异形零件是不容易进行拆装的,当需要进行尺寸、磨损以及腐蚀情况测量时,可以利用3D打印技术制造对应零部件进行在位的对比以及测量。根据3D打印的相同零部件对该零部件是否需要更换进行判定。
5) 机务维修人员培训方面的应用
机务专业院校由于自身资源所限,在航空领域或者机务维修领域专业课程的设置上仍然主要以讲授书本知识为主,很少有生动形象的实物操作机会,这样的教学体制下是不利于机务维修人才的培养。利用3D打印技术可以更加经济的制造出等比例的航空部件模型,实物的外观、结构、机械构件作动方式以及电控系统都可以直观立体的展现出来。原本生涩难以理解的课本知识甚至是英文知识在3D打印而成的仿真模型下会变得更加容易理解。
6) 在其他方面的应用
利用3D打印技术制造需要装配的部件进行装配实验,如果存在误差可以及时进行调整,减少了利用传统制造工艺制造带来的长时间的装配周期,同时也可以减少装配时因为反复拆装导致的零部件之间的连接固定结构损坏,导致部件无法使用,减少不必要的浪费。
利用3D打印技术快速生产特定使用的工具,特东工具针对特定位置,为机务维修工作节约了很多时间和成本。
4. 结语
尽管,有关3D打印行业在机务维修领域可应用的行业标准不明确,我国的相关适航审定法律法规也对这方面的规定不全面,这导致了3D打印技术在机务维修领域得不到大范围的应用。同时,因为3D打印技术还没有完全实现产业化,3D打印的成本、性价比问题也一直困扰着各个公司。这些问题无疑在很大程度上阻碍了3D打印在机务维修领域的发展。相信随着3D打印技术和机务维修领域的不断发展,我国的适航审定方面的法规将会更加完善,利用3D打印技术制造的各种零部件以及维修技术也会完全应用到机务维修领域,带动机务维修领域更加快速的发展。