1. 引言
在连铸坯的各类缺陷中,裂纹是重要的缺陷之一,约占各类缺陷的50% [1]。这些裂纹在后续的轧制工艺中可能会遗留在后续的产品中,进而严重影响实际生产中的工作效率。本文详细的综述了在实际生产中化学成分和连铸工艺对内部裂纹产生的影响,对于实际生产具有深刻的指导意义。
2. 连铸坯中的裂纹类型
按连铸铸坯裂纹发生位置、形态和危害程度,分为表面裂纹和内部裂纹,而内部裂纹由图1内裂图所示包括角部裂纹、中间裂纹、皮下裂纹、三角区裂纹和中心裂纹。
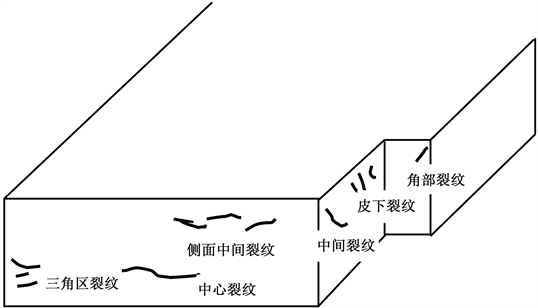
Figure 1. Diagram of internal crack [2]
图1. 内裂图 [2]
1) 角部裂纹:角部裂纹是在结晶器弯月面以下250 mm以内产生的,裂纹首先在固液交界面形成然后扩展。铸坯角部为二维传热,凝固最快,收缩最早,产生气隙后,传热减慢,坯壳较薄,鼓肚或菱变造成的拉应力作用于坯壳薄弱处而产生裂纹。角部内裂平行于拉坯方向,角部附近存在短的内部裂纹。影响连铸坯角部裂纹的因素 [3] 是:钢水成分、结晶器液面波动和二冷制度等。
2) 中间裂纹:内部裂纹产生的原因可以认为是由于板坯表面温度回升、轧辊间的凸度矫正、辊子配列不规范、弯曲矫直等在凝固界面上产生拉伸应力导致裂纹,并沿柱状晶薄弱处继续扩展到坯壳高强度所能抵抗应力为止。中间裂纹垂直于拉坯方向,分布在铸坯外形畸变很大之处者居多。影响连铸坯中间裂纹的因素 [4] 是:拉速、辊缝精度和压下量等。
3) 皮下裂纹:距离铸坯表面比较近,形状细小,皮下纵断面比较明显。皮下裂纹常因连铸辊间产生鼓肚变形或在二冷段内及进入空冷段时由于铸坯回热及相变应力而产生。根本原因是在800附近,Nb、V等碳化物、氮化物析出致使塑性下降而产生。影响连铸坯皮下裂纹的因素 [5] 有:炉间温差、硫含量和拉速等。
4) 三角区裂纹:出结晶器不久的铸坯,在离铸坯侧面150 mm的三角区内,刚凝固或未全凝固的铸坯,高温强度差,受到侧面强烈冷却所产生的热应力、侧导辊位置不当或积渣产生的机械应力、铸坯弧面冷却不良导致的鼓肚力和热应力、铸坯弧面支撑和夹持不良导致的鼓肚力和机械应力,这些应力或其总应力超过了钢坯高温强度时,就会产生裂纹。影响裂纹产生的应力因素 [6] 是:1) 侧导辊位置不当或积渣产生的机械应力;2) 铸坯弧面支撑和夹持不良导致的鼓肚应力;3) 二冷段夹辊的开口度偏差大或设备运行状态不佳。
5) 中心裂纹:铸坯中心液相穴在凝固点附近收缩或鼓肚造成的,同时表现为中心偏析线。中心裂纹发生在板坯中心部位,平行于宽面,在断面上可观察到开口状的缺陷。中心裂纹的成因主要有:因拉速变化产生不均匀的凝固壳;凝固末期的凝固通道的不均匀强冷;轧辊配列不合理而在凝固通道上产生异常压力阻止了钢水的填充。影响中心裂纹的因素 [7] 有:钢水过热度过高,拉速与温度不匹配和辊缝开口度扩大等等。
3. 内部裂纹产生原因分析
3.1. 钢水质量对内部裂纹产生的影响
3.1.1. 钢水温度对内部裂纹产生的影响
图2为过热度与裂纹发生率关系图,由图可以发现在浇铸过程中,如果浇注温度过高,会使铸坯柱
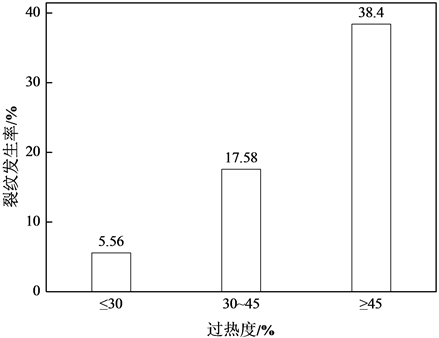
Figure 2. Diagram of the relationship between superheat and crack incidence [8]
图2. 过热度与裂纹发生率关系图 [8]
状晶发达,进而材料产生各相异性,裂纹容易扩展,并且易出现“搭桥”现象。与此同时,钢中气体和夹杂也会较高,铸坯收缩量大。在相同冷却强度时,铸坯坯壳变薄,高温力学强度相对较低,更易发生椭圆变形。特别是钢水温度高而拉速低,会从而导致铸机夹辊弯曲、变形或损坏,铸坯内部裂纹更易发生。因此控制钢水过热度有利于减少铸坯内部裂纹。
3.1.2. S对内部裂纹产生的影响
随着钢中w(S)的增加,内裂的出现相对几率随之增加。图3是钢液硫含量与裂纹发生率关系图,由于S与Fe形成FeS,其熔点较低(1190℃),并与Fe形成熔点更低(988℃)的共晶体;固体相与液体相共存的温度范围宽,S在δ铁及γ铁中的溶解度很小,随钢液的凝固,S将向液体部分富集,造成硫化物偏析。在各种应力作用下,柱状晶晶界硫化物富集处就会开裂,产生内部裂纹。
钢中的成品硫大于0.030%的炉次,出现的裂纹比例是冶炼比例10倍,而小于0.015%的裂纹比例明显降低。因此降低钢中的硫含量是控制裂纹的有效措施。
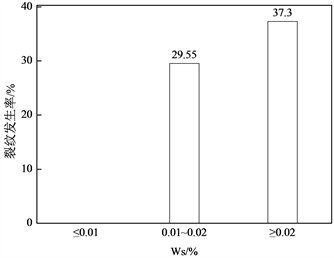
Figure 3. Diagram of relationship between sulfur content and crack incidence in molten steel [9]
图3. 钢液硫含量与裂纹发生率关系图 [9]
3.1.3. Cu、Sn、As、Sb对裂纹产生影响
这些元素的化学稳定性比铁强,是随着原材料带入的,在冶炼和精炼过程中不能被去除。尤其是在电炉中,随着返回废钢比的增加,带入这些残余元素的可能性也增大。Cu在钢锭凝固结晶过程中产生偏析,并在高温加热过程中,钢锭或钢坯的表层形成富铜富集带,锻造加工时,易出现锻裂开口热脆。Sn、Sb对产生锻裂的影响更严重,尤其是经真空精炼钢的热脆更为敏感 [12]。
因此,要控制钢中残留元素,须对原材料的准备工序提出严格要求,要精选废钢以及严格配料程序,选用较高纯度的铁水,用稀释方法控制残留元素。
3.1.4. P对内部裂纹产生的影响
钢水中的磷是有害元素之一 [11] ,会强烈降低固相线温度,推迟铸坯塑性能力的增加,降低钢的高温塑性。裂纹的根源在于显微偏析,由于显微偏析,在钢凝固过程中,因设备或操作因素出现难以避免的少量鼓肚和菱变,其横向拉应力可能使晶界上产生微裂纹,到二冷区后,微裂纹扩展成裂纹。
3.1.5. Mn对内部裂纹产生的影响
连铸坯中,由于Mn与S的亲合力大于Fe与S的亲合力,由图4钢中锰硫比与裂纹发生率关系图可以清楚的展示,当足够的Mn存在时,大部分S与Mn结合形成MnS。以棒状形式分散在奥氏体基体中,不易形成裂纹。当把钢中的[S]控制在≤0.020%时,同时要求提高[Mn]/[S],则大大降低裂纹的产生。
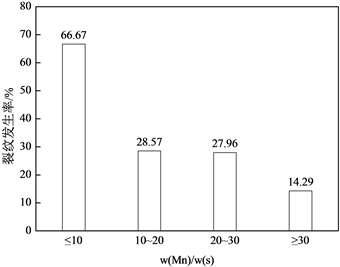
Figure 4. Diagram of relationship between manganese-sulfur ratio and crack incidence in steel [10]
图4. 钢中锰硫比与裂纹发生率关系图 [10]
3.1.6. Al、Nb对内部裂纹产生的影响
Al、Nb在连铸过程中,均能与N结合形成细小颗粒,对裂纹的产生和扩展产生很大影响 [13]。钢中Al和N含量较高可能会成为钢产生裂纹的重要原因之一。钢中的Al和N形成氮化铝,氮化铝颗粒在700℃~800℃时,会从铁素体中大量析出,从而使铁素体塑性降低。在冷却过程中,高温时形成的AlN会沿晶界析出成为应力集中源并形成微孔,微孔聚合形成细小裂纹,使得连铸坯的塑性变差。在二冷区热应力和矫直拉力等作用力下裂纹会进一步产生以及扩展。Nb是强碳化物、氮化物生成元素。Nb(C,N)的析出温度为950℃,正好落在奥氏体相低温区域,进而导致铸坯的高温延塑性变差。此外,Nb(C,N)会抑制奥氏体晶粒的长大。
3.2. 生产工艺对内部裂纹产生的影响
3.2.1. 二冷制度对内部裂纹产生的影响
连铸过程中,在矫直点的铸坯表面温度应大于900℃。凝固坯壳的传导热流是由喷射到铸坯表面的水滴带走,这样会保持铸坯表面温度不产生回温现象。此外,由于坯壳厚度随拉坯进行逐渐增厚,传热阻力也逐渐增加,铸坯表面不会产生过大的冷却,也不会使坯壳厚度呈比例增加;相反会带来表面温度急剧下降、温度梯度增加,坯壳应力相应增加,从而造成铸坯裂纹。
铸坯表面冷却不足,则铸坯表面回温过高,使凝固前沿产生热应力,产生内部裂纹。当冷却水强度过大时,铸坯经过喷水段的强冷后进入辐射冷却区,铸坯中心热量易向外传递,由于液芯温度高,坯壳温度较液芯温度低,使坯壳产生温度回升,引起坯壳膨胀,凝固前沿引起张力应变,当某一局部位置的张力应变超过该处的极限应变时,就会沿着柱状晶开裂,从而形成内裂。所以连铸机二次冷却区各段的冷却水量分配要符合冶金准则,减少或防止由于拉速产生的内裂纹缺陷 [14]。
3.2.2. 结晶器对内部裂纹产生的影响
连铸结晶器是宽面基本平行、窄面带有倒锥度的宽窄面铜板和结晶器足辊构成的组合式结晶器,结晶器在浇铸过程中,由于长时间受热应力和外力的作用,不可避免的会使结晶器铜板和足辊发生磨损、变形或位移,进而达不到连铸工艺要求,使初生坯壳在结晶器中的成长受到阻碍或坯壳受到损伤,从而导致连铸坯裂纹缺陷 [15]。
结晶器的材质应具有良好的抗热变形的能力,同时使结晶器的锥度在受热条件下具有一定的稳定性,不易发生菱变。因为当结晶器菱变后会使钝角角部气隙变大,坯壳生长慢,坯壳薄锐角角部气隙小,与结晶器接触紧密,使局部摩擦力增大。菱变还会使冷却水分布不均匀,造成局部强冷易产生纵向凹陷,成为角部纵裂纹和角部漏钢的发源地。结晶器锥度过小,与连铸坯的凝固线收缩率不适应,产生的气隙大,热阻增加,坯壳生长慢,回温快;而锥度过大,虽有利于传热和坯壳的生长,但连铸坯与结晶器间的摩擦力增加,使连铸坯受力增大,坯壳就易被拉裂。
3.2.3. 保护渣对裂纹产生的影响
保护渣需达到均匀流入、吸附夹杂、减少散热、提高润滑等多种效果,要求具有良好的铺展性、透气性、保温性及与钢种相匹配 [16]。钢水中的夹杂物上浮良好,保护渣吸收夹杂量较大,熔渣成分波动范围较大,需要保护渣具有良好的吸收夹杂物。钢水中的夹杂对保护渣变性的影响。熔渣吸收夹杂后,必然使保护渣性能发生较大变化,这影响了保护渣渣膜组成、润滑特性及热阻的稳定。
3.2.4. 拉速对内部裂纹产生的影响
拉速对连铸过程中铸坯表面温度影响较大。对内裂炉次进行分析统计,内裂缺陷出现在拉速变化频繁的炉次上较多,同时铸坯伴随着中心疏松和中心缩孔。图5拉速与内裂率关系图清楚的展示了,拉速过高、二次冷却过弱,使铸坯的液芯长度超过了铸机的冶金长度,拉出铸机后会形成大面积严重鼓肚。因此,拉速的稳定与否是形成铸坯内裂多少的重要原因之一。
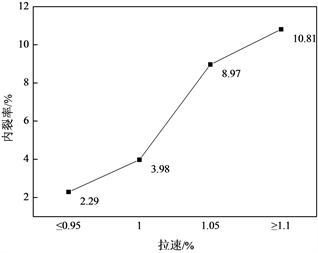
Figure 5. Diagram of relationship between tensile speed and crack incidence [17]
图5. 拉速与内裂率关系图 [17]
3.2.5. 扇形段设备对内部裂纹产生的影响
扇形段的设备状况良好是决定铸坯质量优良的重要保证,也是关键因素之一。在实际生产中,随着浇注炉数的增加,扇形段的对弧精度和辊缝值都会不可避免地发生偏差,这样就会造成铸坯在运行过程中,固液界面处所承受的应力如矫直应力、弯曲应力、鼓肚应力等都会增加,进而产生的塑性变形超过了所允许的钢的高温强度和极限应变值,从而产生内部裂纹 [18]。在设备状况出现问题的情况下,通过工艺控制只能减轻裂纹程度,很难使中间裂纹消失。但是,在对出现严重铸坯裂纹问题的,相应的扇形段进行更换后,铸坯质量明显提高。同时,优化工艺控制可以生产出内部质量无缺陷铸坯。
4. 减少连铸坯内部裂纹的措施
4.1. 钢水质量的保证
何宇明等人 [19] 研究了连铸板坯三角区裂纹的形成原因,提出了控制SS400、Q235等钢种连铸板坯的三角区裂纹的措施:1) 控制钢水成份,减少钢中有害元素如S、P、As,提高锰硫比,减少钢中夹杂和气体含量,提高钢的高温强度和延展性,无论任何钢种尽可能保持较低的S含量,既使SS400和Q235硫也不超过0.030%,有条件时把s控制在0.020%以下。2) 保持非16 Mn系列钢Mn/S比大于25,尽可能达到30以上。3) 控制SS400、Q235等钢的过氧化程度,保持终点C > 0.06%,适量增加脱氧合金用量,特别是保持0.010%以上酸溶铝含量,减少钢中氧含量。4) 控制钢中As含量,As不宜超过0.050%。5) 控制钢中P含量,P宜小于0.030%,尽可能控制在0.025%以内。
袁伟霞等人 [20] 对板坯中间裂纹进行了深入的研究。通过研究板坯中间裂纹的出现规律及其微观形态,明确了造成板坯中间裂纹的内在因素是钢中S、P元素的晶间偏析,并通过建立铸坯凝固过程微观偏析模型,计算出了钢中有害元素P、S在凝固过程中的实际偏析及其对钢的裂纹敏感性的危害。钢中的Cu、Sn、As、Sb等元素是随着原材料带入的,这些元素的化学稳定性比铁强,在冶炼和精炼过程中不能被去除,成为残留元素,这些元素含量高易造成表面和内部裂纹。
因此,要控制钢中残留元素,须对原材料的准备工序提出严格要求,要精选废钢以及严格配料程序,用较高纯度的生铁、海绵铁或热装一定比例铁水,用稀释方法控制残留元素。并通过对影响钢强度的因素进行分析,明确了钢中各成分对铸坯裂纹的作用机理:钢的强度与温度、成分、应变速度、凝固组织及冷却条件有关。由于连铸坯凝固的大部分热量是由二冷区导出的,所以建立严谨的二冷制度是很有必要的。连铸坯出二冷区后,会在铸坯厚度上产生很大的温度梯度,这时候就要求根据钢种、拉速选择合适的冷却水量,控制好冷却水的分布,使连铸坯表面达到均匀冷却。同时,对于二次冷却的状况,即喷嘴形状、性能、布置、喷水强度的分布,因此必须要经常检查喷嘴是否经常处于正常工作状态。
4.2. 建立合理的二冷制度
蔡开科等人 [21] 对铸坯的内部质量研究后认为,在铸坯的凝固组织中,发现等轴晶比柱状晶不易出现裂纹,因此低温浇注和电磁搅拌使组织等轴晶化,有利于阻止裂纹的发生。
陈雷等人 [22] 对铸坯中间裂纹研究后认为,中间裂纹多发生在方坯厚度1/4处,原因主要是二冷下段铸坯表面温度回升所形成的,当铸坯经过喷水段的强冷后进入辐射冷却区,铸坯中心热量易向外传递,使铸坯表面温度回升,坯壳受热膨胀,凝固前沿引起张力应变,当某一局部位置的张力应变超过该处的极限应变值时,就产生中间裂纹。铸坯表面温度回升越多,裂纹发生几率越大,因此要控制二冷区的冷却制度,使铸坯表面温度回升不超过100℃/m,此外当注温高拉速快,铸坯柱状晶发达时也会助长中间裂纹的发生。
张富强等人 [23] 对国内某钢厂板坯三角区裂纹进行了研究,发现三角区裂纹绝大多数发生于铸坯两侧距窄边约50 mm~120 mm处,而在中心(1/2宽度处)和两侧距中心400 mm~550 mm处生成中心裂纹。铸坯宽度大,中心裂纹和三角区裂纹发生频率高。并采用数值模拟的方法研究分析了宽度方向喷嘴布置和水流密度分布对铸坯温度场、铸坯角裂及三角区裂纹的影响。其通过开发新的二冷工艺,加强冷却,使铸坯宽度方向的冷却不均匀性得到改善,宽度方向三个不同位置铸坯表面温度的最大差别由过去的89℃减小至46℃,中心裂纹和三角区裂纹产生比率分别降低54%和41%;并通过严格控制凝固终点附近夹辊开口度,使中心裂纹和三角区裂纹得到较好控制。
4.3. 选取合适的结晶器和保护渣
对于结晶器,要选取合适的结晶器厚度,以保证高温下的刚性,因为结晶器在热应力作用下失去塑性,进而永久变形是产生裂纹的重要原因之一。同时要控制好结晶器的几何形状,合适的水缝尺寸,均匀冷却,合理的钢流运动和性能合适的保护渣,从而保证结晶器内坯壳的均匀生长和结晶器的坯壳厚度。
王悦新等 [24] 对连铸结晶器振动过程进行了有限元模拟,获得了结晶器振动周期内连铸坯表层应力分布,并分析了结晶器锥度、结晶器与铸坯间摩擦系数、拉速和铸坯厚度对连铸坯表层应力分布的影响。研究取结晶器正弦振动周期的4个特征时刻点位置,即正向最大点、零点、负向最大点、零点进行分析。
曹磊等人 [25] 针对包晶钢通过提高保护渣碱度,降低保护渣的黏度,改善铸坯坯壳与结晶器壁之间渣膜传热等技术,使铸坯的表面裂纹与皮下裂纹缺陷得到了有效控制。保护渣应勤加、少加、使保护渣均匀分布。郭文波等人通过优化保护渣成分和控制钢水条件,铸坯裂纹发生率得到了有效控制,Q235B钢铸坯表面纵裂纹发生率由6.47%降至2%以下,中板铸坯轧制裂纹发生率由2.64%降至0.9%以下。
4.4. 保证拉速稳定
生产中实施恒拉速浇注,提高了铸坯内部质量的均质化。恒速浇注既保证了生产组织和工艺的稳定,又保证了二冷水量变化不会太大,液相穴也不会发生太大变化,减少了铸坯内部裂纹。
梅山钢铁 [26] 对连铸生产阶段的各种情况下拉速调整进行试验、研究,分析大量数据并通过工艺、设备及操作结合实践。以自动控制为基础采用先进的控制方法,解决了求尽可能的保持恒拉速生产,但由于生产节奏、设备工艺及操作人员等各种因素导致钢水过热度的变化,必须对拉速进行适当和必要的调整,这是一对矛盾问题。
4.5. 完善扇形段设备
在实际生产中保证铸机良好的对弧精度和导辊状态,对减小铸坯凝固前沿应变、减轻铸坯内部裂纹尤为重要。在设备刚性足够的前提下,加强铸机设备维护和开口度的检测,保持设备运行正常,配合适当的生产工艺参数,对辊缝实行负误差控制,保证铸机辊缝偏差小于0.5 mm,确保支承辊不对中产生的位移小于0.5 mm,可以实现连铸机整个扇形段辊缝控制稳定,减少内部裂纹。
王保东等人 [27] 经过实践,对某钢厂弯曲段采用耳轴支承固定方式替代原来的抬轿式。并且在总间距不变的情况下,采用小辊径、多支点分节式结构,提高辊的刚度。同时,依据钢液的凝固收缩特性,依据动态轻压下原理,对该连铸机扇形段辊缝采用逐步收缩锥度来收缩辊缝。
5. 结论
1) 本文详述了内部裂纹类型、存在位置及特点。
2) 总结了连铸坯钢水的化学成分和钢水温度对连铸过程中连铸坯内部裂纹产生的影响。
3) 同时,详细总结了连铸工艺对连铸坯内部裂纹产生的影响。
4) 并且,对实际生产提出改进意见,包括对原材料的准备工序提出严格要求,优化二冷制度等连铸工艺。对降低内部裂纹发生率,减少生产的废品率具有深刻的指导意义。
基金项目
1) 河北省钢铁联合基金资助项目(E2018209195);2) 唐山市科技计划资助项目(18130203a);3) 华北理工大学大学生创新训练项目(X2018064)。
NOTES
*通讯作者。