1. 前言
随着我国的经济不断发展,工业和家庭用电的需求量越来越大。为了应对电力负荷巅峰期电量不够使用的情况,国家电网采用建设抽水蓄能水电站的方式,把电力负荷低谷期把充足富裕的电能转换为水利势能,然后在负荷巅峰期再把水利势能转化为电能。目前抽水蓄能水电站,朝着大容量、高水头的趋势发展。而高水头抽水蓄能水电站的高HD值,会要求其使用的压力钢管、肋板、岔管、蜗壳等材料减小壁厚及施工和焊接难度,且在复杂的气象条件下材料不会发生脆断,因此要求使用的钢板必须具有非常高的强度、塑性和低温韧性。现行水电站用压力钢管及蜗壳的制作钢板中,SX780CF是中国长江三峡集团公司企业标准QJ/CTG24-2015《大型水电工程高强度低焊接裂纹敏感性钢板技术条件》中的最高级别钢种。
南阳汉冶特钢本着“特种、特重、特厚”的生产理念,积极研发出120 mm厚的特厚SX780CF钢板。本文主要研究了特定成分下120 mm厚SX780CF的热处理工艺及组织性能。
2. 120 mm厚SX780CF钢板技术要求
120 mm厚SX780CF钢水熔炼分析及钢板成品分析结果,其化学成分、碳当量(Ceq)及焊接裂纹敏感性指数(Pcm)应符合表1规定:
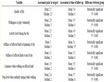
Table 1. The standard of SX780CF chemical composition
表1. SX780CF化学成分标准
a碳当量Ceq = C + Mn/6 + Si/24 + Ni/40 + Cr/5 + Mo/4 + V/14。b焊接裂纹敏感性指数Pcm = C + Si/30 + Mn/20 + Cu/20 + Ni/60 + Cr/20 + Mo/15 + V/10 + 5B。
120 mm厚SX780CF钢板经热处理后,力学性能及工艺性能应符合表2规定。
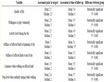
Table 2. The standard of SX780CF mechanical properties
表2. SX780CF力学性能标准
*A(δ5)表示LO = 5.65SO0.5时的断后伸长率,其中L0为原始标距,S0为原始横截面积。
3. 120 mm厚SX780CF冶炼成分
①120 mm厚SX780CF冶炼工艺流程如图1(a)~图1(i):
流程简介:a) 铁水(KR脱硫)采用双工位扒渣,铁水S含量 ≤ 50 ppm;b) 转炉顶底复吹,出钢C ≤ 0.07%,P ≤ 0.008%;c) 转炉出钢后进入一次VD脱C,吹氩使钢水中的残氧与C进行反应生成气体逸出,进而降低碳含量,VD出钢C含量0.03%~0.04%;d) 精炼采用大渣量工艺,白渣保持时间 ≥ 25 min。三加热调控SX780CF各成分在内控范围后,出钢进入第二次VD真空脱气,[H] ≤ 1.0 ppm;e) 水冷铜板结晶器锭模在浇铸之前摆好,并调整好锭型的尺寸,低温快浇,高温慢浇;f) 冷却10 h后夹钳脱模;g) 钢锭表面满板清理,确保无裂纹;h) SX780CF锭表面涂刷高温涂料,保证轧制后的钢板表面质量;i) 加热出炉、待轧制的SX780CF钢锭。
②冶炼最终成分如表3:
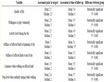
Table 3. The finally smelting composition of 120 mm SX780CF
表3. 120 mm SX780CF最终冶炼成分(wt%)
成分设计思路:对于C元素,其固溶强化能为钢板提供较高的强度增量,但对钢板的塑性、冲击韧性以及焊接性能非常不利。考虑到钢板的厚度较大,钢板1/2位置强度会难以保证,所以碳含量要求走标准上限,实际冶炼0.09%。Si可以提高钢板的淬透性与抗回火性,但对低温冲击韧性有着严重的不利影响,所以设计范围0.10%到0.15%。Mn也能够起到固溶强化的作用,同时能够扩大奥氏体相区,降低A→F转变的温度及Ms温度,在一定程度上能够细化铁素体晶粒,但对碳当量也有严重的影响,所以设计范围在1.10%到1.20%,实际冶炼含量1.16%。P能使钢产生冷脆和影响交叉滑移,S能使钢产生熔点低的FeS形成热脆和增加夹杂物颗粒,两者均属于有害元素,应该尽可能降低其含量。Nb、V、Ti在轧制形变过程中,形成Nb(C,N)、V(C,N)、Ti(C,N)等碳氮析出物,形成析出强化。同时微细的Nb(C,N)析出质点可以固定亚晶界,从而阻止奥氏体晶粒再长大,达到细化晶粒的目的。V可以显著提高钢的强度及抗回火性,同时不影响钢的韧性。Cr、Mo、B能够提高钢板强度和淬透性,使CCT曲线右移,这非常易于大厚度钢板在淬火过程中的组织转变。Ni在钢中为完全固溶元素,具有明显的降低冷脆转变温度的作用。Ni与Fe以互溶形式存在于a和g铁相中,通过其在晶粒内的吸附作用细化铁素体晶粒,提高钢的冲击韧性。Ni也同时是扩大奥氏体区元素,降低奥氏体的转变温度,从而影响到碳与合金元素的扩散速度,阻止奥氏体向珠光体转变,降低钢的临界冷却速度,可提高钢的淬透性,易使钢中出现贝氏体及马氏体。所以设计Ni含量走上限,充分保证SX780的低温冲击性能。
4. 120 mm厚SX780CF轧制工艺及组织
轧制采用“高温低速大压下”的轧制工艺,粗轧开轧温度1050℃,每道次压下量50 mm,连续4道次进行,充分破碎奥氏体晶粒,使其细小均匀,轧后进行IC冷却,防止因中间坯等待时间过长,使其破碎细化的晶粒继续长大,在钢板心部形成混晶。精轧开轧温度940℃,终轧温度860℃,轧后先进行RPC驰豫60 s,再进入ACC冷却,终冷温度 ≤ 750℃。
对120 mm厚SX780CF钢板进行头尾取样,检测其控轧态金相,金相显微镜为德国卡尔蔡司Axio Imger A1m,观察其厚度四分之一位置的组织,见图2、图3。
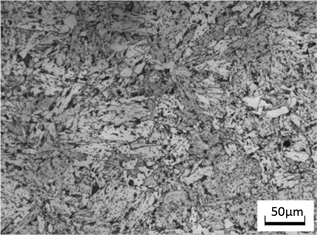
Figure 2. 1/4 position of head thickness, 200×, metallographic structure
图2. 头部厚度1/4位置,200×,金相组织
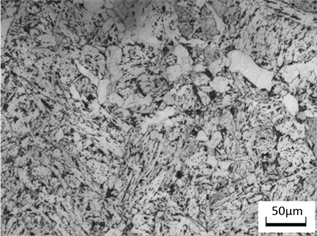
Figure 3. 1/4 position of tail thickness, 200×, metallographic structure
图3. 尾部厚度1/4位置,200×,金相组织
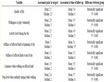
Table 4. The inclusion test results of SX780CF
表4. SX780CF夹杂物检测结果
根据金相检测结果及表4可以看到,控轧态试样基体组织贝氏体 + 铁素体 + 珠光体,头部铁素体晶粒度8.0级,比例10%,晶粒度较为均匀。尾部铁素体晶粒度7.0 + 9.0级,铁素体比例20%。贝氏体组织较粗大,存在较多岛状物,这会对冲击性能造成不利的影响。对夹杂物进行高倍观察,没有看到粗大的夹杂物,这可以排除粗大夹杂物对冲击性能的影响。
5. SX780CF的热处理工艺及组织性能
5.1. 120 mm厚SX780CF热处理工艺的确定
①淬火工艺的制定
淬火温度即钢完全奥氏体化的温度(Ac3点),温度越高,奥氏体化越充分,完全奥氏体化所需的时间越短。但奥氏体晶粒会随温度的升高而快速成长,粗大的晶粒会严重损害钢板的性能。根据经验公式:Ac3 = 937.2 − 476.5w(C) − 26.6w(Ni) + 56w(Si) + 142.8w(V) + 31.5w(Mo) − 19.7w(Mn) − 4.9w(Cr) − 16.3w(Cu) + 700w(P) + 56w(Al) − 19.1w(Ti),经计算得到钢板的完全奥氏体化温度为864℃,则淬火温度 = AC3 + (30~50)℃,所以淬火温度设定为920℃ ± 10℃。
保温时间越长奥氏体化也越完全,但同样会形成粗大的奥氏体晶粒。因SX780CF加入的合金元素较多,其中的Cr、Mo、V等元素会显著降低C在奥氏体在扩散速度,从而阻止奥氏体化的形成。其次由于合金元素的相对原子质量较大,其在相同温度下,其自身的扩散速度也非常慢,仅为C的千分之一到万分之一,所以奥氏体中合金的均匀化也需要较长时间。一般保温时间与钢板厚度有t = h × α的关系,h为钢板的厚度,α为保温系数,范围在1.6~2.4 min/mm。所以120 mm厚SX780CF的保温系数按2.4 min/mm确定,淬火保温时间为t = 120 × 2.4 = 288 min。用JMatPro模拟SX780CF淬火过程中的冷却转变曲线及端淬性,如图4和图5。
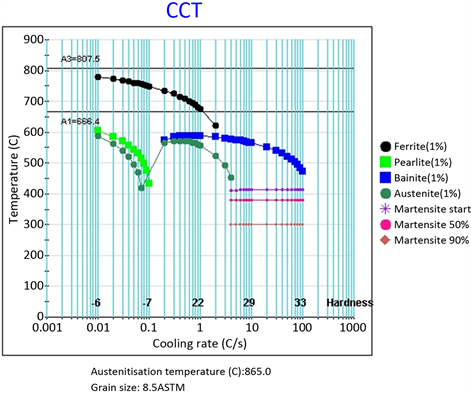
Figure 4. Curve: cooling transformation structure
图4. SX780冷却组织转变曲线
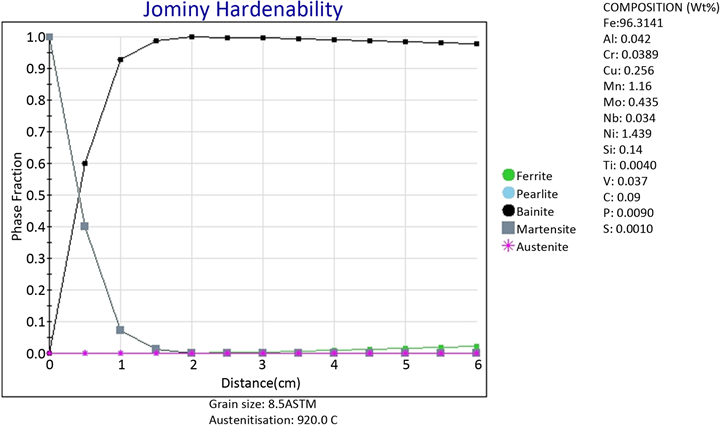
Figure 5. Curve: jominy hardenability
图5. SX780CF端淬模拟曲线
南阳汉冶特钢的辊压式淬火机,对于120 mm厚钢板的冷却速度在1.5℃/s,而越往钢板心部其冷速越低。再根据图4和图5,可以得出120 mm厚SX780CF淬火后组织为:表层以马氏体为主,而越往钢板厚度深处,则马氏体组织不断减少,贝氏体不断增多。
②回火工艺的制定
回火是将淬火或正火后的钢加热到Ar1以下某一选定温度,并保温一段时间,然后空冷,消除淬火或正火所产生的残余应力,降低钢脆性,防止开裂。同时增加钢的塑性和韧性,使钢板的强度与塑韧性具有良好匹配性。回火温度越高,时间越长,塑性韧性越好,但强度越低。为了得到较为综合的力学性能,必须要确定好回火温度与时间。利用JMatPro模拟SX780在不同回火温度、不同回火时间下的抗拉强度,如图6。
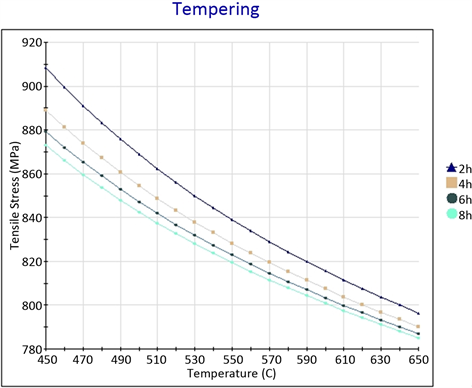
Figure 6. Curve: relationship between tempering temperature, time and yield strength
图6. SX780回火温度、时间与屈服强度的关系曲线
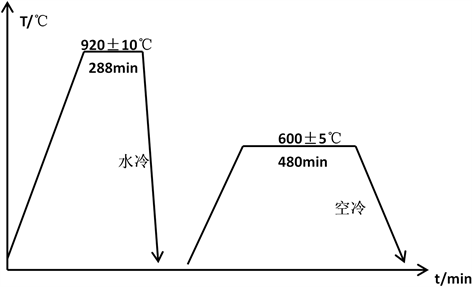
Figure 7. Heat treatment process of SX780CF
图7. SX780CF的热处理工艺
根据图6,在回火温度 = (450~650)℃及回火时间=(2~8) h范围内,抗拉强度均符合QJ/CTG24-2015标准。但回火温度越高、时间越长,应力消除越充分,钢板的塑韧性越好,所以为了保证钢板的综合力学性能,120 mm厚SX780CF回火工艺按600℃ + 8 h执行。则SX780CF热处理工艺如图7,取SX780CF淬火态试样进行电阻炉回火实验,检测其Q + T的性能如表5。其中取样、制备试样按照GB/T2975规定执行,低温冲击按GB/T229标准执行,在夏比摆锤冲击实验机(深圳新三思JB-300)上检测;拉伸性能试验按GB/T228标准执行,在液压万能材料试验机(山东时代WE1000)上检测,弯曲性能试验按GB/T232标准执行,在板材连续弯曲实验机(山东时代BW1000)上检测。
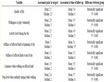
Table 5. The properties test results of SX780CF (Q + T)
表5. SX780CF(Q+T)性能检测结果
根据检测性能结果,SX780CF屈服强度、抗拉强度富余量均在30多MPa,富余量不大。−40℃横向冲击和5%应变时效冲击均存在个别低值,不满足三峡QJ/CTG24-2015标准。考虑到强度富余量不大,所以无法再通过升高回火温度、增加回火时间来提高钢板冲击韧性。
5.2. 冲击不和原因分析
对SX780CF回火后的试样进行电镜检测(日本日立S-3400),观察其厚度四分之一位置组织形貌,如图8。
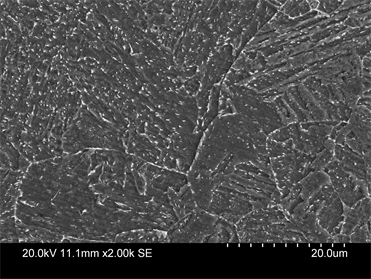
Figure 8. TEM test Results of samples (Q + T)
图8. SX780CF (Q + T)电镜检测结果
根据检测结果,SX780CF试样组织主要为贝氏体回火组织 + 回火索氏体,存在少量的粗大组织,这些不均匀的粗大组织可能是导致冲击不稳定的原因之一。因为淬火态的SX780CF有非常大的残余应力,其强度、硬度极高,而塑性韧性极差,汉冶特钢目前加工试样的带锯无法对其进行切割,所以只能根据淬火过程中的组织相变理论,以及结合回火后的组织性能来分析冲击不稳定的原因。
首先在淬火过程中,在Bs点以下及上贝氏体形成以上的温度范围内,会形成粒状贝氏体。其组织内分布有颗粒状小岛,这些小岛在高温下是富碳A,在继续的冷却过程中,会形成M/A。由于SX780CF合金含量较高,极大的降低了C的扩散系数,即使高温回火后,M/A也无法消除。根据研究表明,M/A为脆性相,带有尖角的粗大的M/A组元,由于其位错塞积所引起的应力集中,会在尖角处产生裂纹,从而降低材料的韧性和塑性;但M/A岛以细小点状或交错分布条状存在时可以改善钢的冲击韧性 [1] [2] 。根据刘莉的研究,钢板在检测落锤性能时,断口不合格分离的试样,其中心处M/A岛的数量明显更多,而且尺寸比较大。所以SX780CF冲击不稳定也可能为粗大的M/A导致 [3] 。根据陈雨来、张栋斌、余伟等人的研究,随着冷却速度的继续增加,碳原子扩散系数逐渐下降、扩散时间逐渐缩短,C难以充分扩散到奥氏体中,奥氏体只能在短程内富碳,使M/A 岛尺寸细小、分布弥散,且残余奥氏体相界面附近的奥氏体中碳含量也将降低,使得残余奥氏体不能稳定的存在,难以在低温时转变为M/A岛。所以可以通过提高冷却速度来细化和消除M/A组元,从而提高SX780CF的冲击韧性。
其次在回火过程中,回火索氏体它是由淬火钢板在600℃高温回火后,得到的一种铁素体 + 粒状渗碳体的机械混合物。其粒状碳化物越细小,受力时造成的应力集中越小(由细小的颗粒分散应力),微裂纹越不易产生和扩散,故钢的塑性、韧性越好。据此SX780CF冲击不稳定,也可能是因为回火索氏体中的粒状渗碳体大小不均匀造成的。粒状渗碳体是由钢板在回火过程中马氏体分解及残留奥氏体转变形成的,要想得到细小的粒状渗碳体,必须细化其原始转变前的组织,即细化马氏体及残留奥氏体组织。淬火过程中,通过增大钢板的冷却速度,急速降低C原子的移动速度,使其只能在极小的短程内扩散,从而快速的在α-Fe中形成过饱和的间隙固溶体,从而细化马氏体组织。根据研究,两次淬火甚至循环淬火液可以精细马氏体组织,其原理是第一次淬火后,马氏体内大量的位错在加热到奥氏体化后并不能完全消除,这些残留位错会在相变转变过程中提供更多的形核场所,从而可以细化组织 [4] [5] [6] 。所以对120 mm进行二次淬火,并且提高二次淬火时的冷却速度。同时回火时,应尽可能的降低回火温度及时间,这也能防止粒状的渗碳体继续球化长大。但考虑到三峡QJ/CTG24-2015标准要求回火温度不低于600℃,以及前期试样回火后的强度值富余量不大,所以回火工艺不变。
6. SX780CF两次淬火 + 回火后的组织性能
6.1. 提高淬火机的冷却能力
淬火机冷却系统由缝隙段(1对缝隙冷却喷头)、双联段(2对双联喷嘴)、高压三段(6对快冷喷嘴)及低压段(喷管)组成,其前三段均属于高压段,长度仅为3.6 m,其特点是距离短、流量大、压力高,淬火机的冷却能力主要是高压段提供。低压段长20 m,其冷却能力相对较小。为了提高淬火机的冷却能力,增大钢板的冷却速度,必须要增加辊压式淬火机的水泵水量及开口度。120 mm厚SX780CF两次淬火过程中,淬火机的设备参数对比如表6。
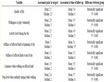
Table 6. When SX780CF twice quenching,comparison of equipment parameters of quenching machine
表6. SX780CF两次淬火时,淬火机的设备参数对比
可见淬火机各段流量增加明显,其对120 mm后钢板的冷却能力,可提高0.5~1.0℃/s。
6.2. 两次淬火+回火后的组织性能
经原回火工艺回火后,其组织性能如图9和表7。
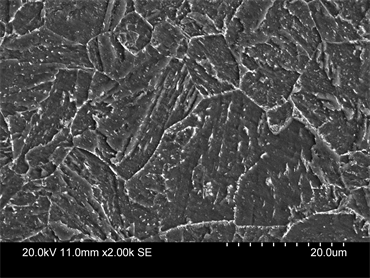
Figure 9. TEM test Results of samples (Q + Q + T)
图9. SX780CF (Q + Q + T)电镜检测结果
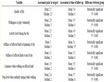
Table 7. The properties of SX780CF after twice quenching and tempering (Q + Q + T)
表7. 两次淬火+回火(Q + Q + T)后,SX780CF的性能
根据图9,可见其粒状渗碳体及M/A组元更加均匀细小,不存在粗大的异常组织,所以冲击值提高且更加稳定。同时冷却速度越大,淬火后形成的马氏体越多,其内部的位错密度也越大多,所以强度也随之提高。而回火后形成的回火索氏体也因马氏体的增多而增多,这种优良的韧性组织也对SX780CF的冲击性能大大有益。
7. 结论
1) 120mm厚SX780CF的热处理工艺为两次淬火(T = 920℃ ± 10℃, t = 288 min) + 回火(T = 600℃ ± 5℃, t = 480 min),其组织为回火索氏体 + 贝氏体回火组织;
2) SX780冲击不稳定的主要原因为组织不均匀,存在粗大的M/A及渗碳体颗粒导致;
3) 通过两次淬火以及增大冷却速度,可以增加并细化马氏体组织,回火后得到更多的细小而均匀的回火索氏体,这是SX780CF韧性大大提高的原因。同时冷却速度的增加也导致马氏体本身的增多及其内部的位错密度增多,这是SX780CF的强度提高的原因。