1. 引言
间隙研究一直是旋转机械研究领域内的热点问题,如叶轮与蜗壳间的间隙是研究动静干涉现象以及泵内部流动压力脉动的主要载体,有研究表明动静干涉是造成离心泵内部压力脉动并进一步引发泵的振动和噪声的主要原因 [1] [2] 。
密封口环间隙是泵内另一个重要的动静间隙 [3] ,通常口环作为静止部件固定在泵壳上,与叶轮的入口直段组成间隙密封,口环选取比叶轮材料硬度低一些的材料制作,从而保证泵在运转过程中,动静部件即使相碰也不会对叶轮造成损害。因此,由于泵运转过程中不可避免地发生振动,密封口环会随着泵运转时间增加而逐渐磨损,间隙会逐渐增大。此处的间隙增大一方面会使叶轮出口的高压流体更多的回流到进口造成容积损失增大,降低泵的效率 [4] [5] [6] ,另一方面会改变泵的内部流动状态,从而对泵的外特性产生重大影响,一些条件下会引起流体激振,并影响泵的受力和运转稳定性 [7] [8] [9] [10] 。
文中选取某潜没式液货泵为研究对象,建立了泵的主流道模型和密封口环间隙流道的水力模型,并保持主流道模型不变,对不同口环间隙值和偏心值下的间隙流道模型进行定常仿真计算,分析口环间隙对泵性能及流场的影响,探讨口环磨损后泵的性能变化规律。
2. 计算模型与边界条件
2.1. 间隙模型
所选取的潜没式液货泵泵头的结构如图1所示,该泵为单级悬臂式离心泵,上下各设计有一处密封口环,为了制造方便,两处密封口环间隙值保持一致,该泵的设计参数为流量300 m³/h,转速2620 r/min,扬程110 m,比转速为81.3。
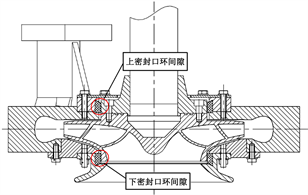
Figure 1. Pump head structure of submerged cargo pump
图1. 潜没式液货泵泵头结构
水体模型分为主流道模型和密封间隙流道模型两部分。主流道模型分为入口段、叶轮、蜗壳、出口段四个部分,密封流道模型分为下密封间隙模型和上密封间隙模型,如图2所示。
在ICEM中对模型进行网格划分,其中入口段,间隙模型采用结构化网格,其他采用非结构化网格,网格数量保证网格无关性要求。
2.2. 对比方案
用δ表示研究用泵的密封口环间隙值,用ε表示偏心值,如图3所示,Φ D1为密封口环内壁面直径,ΦD2为叶轮入口直径。由于模型具有周向对称性,故只研究一个方向的偏心即可。
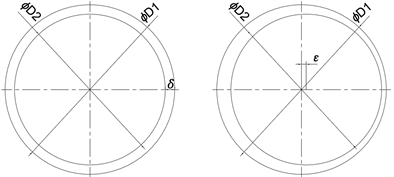
Figure 3. Definition of clearance and eccentricity of sealing ring
图3. 密封口环间隙与偏心定义
依据API610标准模型泵选用0.3 mm,但未考虑偏心。为考察不同间隙及偏心影响,泵的选取的δ和ε值分别如表1所示,共组成5种对比方案,其中方案1为设计方案。
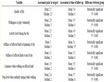
Table 1. Contrast table of research programs
表1. 研究方案对比表
2.3. 边界条件
采用CFX软件进行定常计算,选择SST湍流模型 [11] ,计算时设置入口条件为总压,出口条件为质量流量,壁面采用无滑移固壁边界,收敛精度设为10-5。间隙模型中与叶轮接触的壁面设置为旋转面,旋转速度与叶轮相同,其他壁面设为静止面。
3. 计算结果与分析
3.1. 试验验证
为验证数值计算方法的准确性,将数值计算结果与试验结果进行对比,如图4所示。
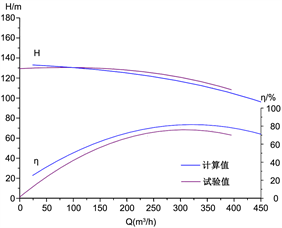
Figure 4. Comparisons between calculated and experimental values
图4. 计算值与试验值对比
从图4可以看出,计算的扬程与试验结果基本吻合,但小流量工况下计算值与试验值的变化趋势不一致,主要原因是小流量工况回流明显,影响了计算结果的准确性,这是目前无法避免的;计算效率与试验效率变化趋势基本一致,二者间存在一定的误差,主要原因是计算模型进行了简化处理,如壁面条件无法反映真实情况,忽略了轴承等机械损失等,都是导致试验效率低于计算效率的原因;额定工况下计算和试验扬程相对误差为3.57%,计算和试验效率相对误差为3.12%,均未超过一般工程误差5%,因此,文中采取的计算方法与计算结果准确可靠。
3.2. 外特性分析
图5分别为不同研究方案下泵的扬程(图5(a))、效率(图5(b))外特性曲线。
(a) 扬程曲线
(b) 效率曲线
Figure 5. External characteristic curves of different research schemes
图5. 不同研究方案下泵的外特性曲线
图5的规律表明,随着δ值从0.3 mm变化到0.7 mm,泵的扬程和效率均下降,说明密封口环间隙值增大会导致泵的性能下降,且文中的研究还表明,这一规律是呈线性变化的,即随着密封口环间隙线性增大,泵的扬程、效率线性下降,表现为性能曲线整体下移。
对比方案2、4、5的外特性计算结果发现,三种方案下泵的外特性曲线基本重合,说明偏心值基本不会影响泵的扬程和效率。
3.3. 间隙泄露量分析
表2为不同方案下泵上下密封口环间隙处的泄漏量,选取额定工况下的数据进行对比。
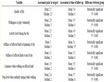
Table 2. Leakage of upper and lower sealing ring clearance
表2. 上下密封口环间隙泄漏量
(单位:kg/s)
从表2看出,间隙值增大,泄漏量也增大,偏心值增大,泄漏量基本不变,说明泄露量的大小只与间隙值有关,与偏心值关系不大。泄漏量大造成泵的容积效率低,进而降低泵的总效率,这与前文的分析是一致的。
3.4. 受力分析
表3为不同方案下泵叶轮上所受力的大小,其中Z向为旋转轴向。
(单位:N)
表3的对比结果表明,仅间隙变化且无偏心时泵的受力基本不变化;间隙不变且仅偏心变化时,随着偏心的增大,泵的轴向力基本不变,但径向力会明显增加,这对泵的运行不利,使泵运转过程中易产生振动和噪音。
4. 内部流动分析
4.1. 整体静压分布
为分析间隙值对整体模型流动状态的影响,选取x = 0截面分析额定工况下不同间隙时泵内的静压分布情况进行研究,如图6所示。
(a) δ = 0.3 mm
(b) δ = 0.5 mm
(c) δ = 0.7 mm
Figure 6. Cloud map of static pressure distribution in pump
图6. 泵内静压分布云图
从图6看出,泵内静压从入口到出口逐步提高,三种间隙下的静压分布规律基本吻合,区别在于蜗壳腔室内的静压是随着间隙增大而降低的,由此也说明间隙增大会引起泵扬程下降。另外,随着间隙增大,经过间隙回流到叶轮入口的液体流量(或称泄漏量)增加,间隙内的高压流体冲击到叶轮入口的低压流体中,影响了叶轮入口区域的液体流动稳定性,间隙越大,受影响的区域就越大,入口流域内的漩涡数量增加,流动损失随之增加,进而引起泵的效率也下降。
4.2. 间隙内静压和速度分布
为分析间隙内的流动状态,选取额定工况下不同间隙时下密封口环间隙内的静压和速度分布情况为研究对象,如图7所示。
由图7看出,间隙流道内的静压分布在入口处(间隙右侧)变化比较剧烈,先减小后增大,然后缓慢减小,直至出口,这种变化趋势在小间隙时表现更明显;速度分布中流体在经过间隙入口后流速有陡升,高速区基本占据整个间隙流道,随后速度慢慢降低,高速区慢慢靠近间隙旋转的内壁侧,这是流体轴向速度和周向速度共同叠加的结果。轴向速度由于壁面摩擦力的作用呈两侧近壁面速度低,中间速度高的分布特点;周向速度由于内侧壁面旋转产生的剪切力的作用呈外侧壁面的速度低,内侧壁面高的分布特点,二者叠加使得高速区靠近内壁面侧。
(a) δ = 0.3 mm
(b) δ = 0.5 mm
(c) δ = 0.7 mm
Figure 7. Cloud map of static pressure and velocity distribution
图7. 下密封口环间隙内静压和速度分布云图
图8是间隙内同一长度截面内平均静压和流速随间隙轴向长度变化的曲线,Z = 0 mm表示间隙入口截面。图8(a)的规律说明在经过间隙入口处的剧烈变化后,静压呈线性减小,且间隙越小,压降的梯度就越大。图8(b)的流速曲线说明流速在经过间隙入口处的陡升后线性下降,不同间隙时下降的趋势基本一致,但间隙内流速随间隙增大而增大,主要原因是流体自身黏性和壁面摩擦力对间隙内流体的流速有阻碍,而随着间隙增大,这种阻碍作用会慢慢减少,即间隙增大到一定程度,“密封”效果会大大降低。
(a) 静压随间隙长度变化曲线
(b) 速度随间隙长度变化曲线
Figure 8. Performance curve of test pump
图8. 试验泵的性能曲线
从图8可以得出,当间隙δ = 0.3 mm (方案1)时,间隙内静压梯度最大,流速最小,“密封”效果最好,当间隙δ = 0.5 mm (方案2)和δ = 0.7 mm (方案3)时,间隙内静压和流速变化已相差不大,“密封”效果越来越低,因此结合工程实际情况考虑,当间隙值达到0.5 mm时就应更换密封口环,即密封口环磨损量不应超过0.2 mm。
5. 结论
基于对某潜没式液货泵密封口环间隙的研究,得出如下结论:
1) 随着密封口环间隙线性增大,泵的扬程、效率线性下降,表现为性能曲线整体下移;密封口环的偏心只对泵的径向受力情况有影响,偏心越大,径向力会显著上升,对泵的运行产生不利影响。
2) 间隙内流体运动存在规律性,静压先陡降后增大然后线性减小,流速先上升后线性减小,间隙越小时压降的梯度越大,间隙内的流速也越低,“密封”效果越好。工程上从保证“密封”效果的角度考虑,口环磨损量超过0.2 mm时就应更换密封口环。
3) 文中从密封口环磨损后间隙增大对泵性能的影响这一角度来确定磨损量,实际泵在运行过程中,密封口环间隙增大还会引起泵的振动和噪音增加,此规律有待试验研究来揭示。
基金项目
工业和信息化部:大排量潜液泵系统技术研究(工信部联装[2013]411号)。
参考文献