1. 引言
1) 四方车辆股份有限责任公司是中国主要的动车生产基地,其主要业务中转向架检修在国内一直处于前列,由于高速动车组的制造、检修是由铁道部指定的企业进行,并且本着返回原制造地检修的原则,中车内部有检修资格的四家企业——长客装备、青岛四方、唐车公司、南京浦镇车辆厂每年需检修的高档动车约2000辆,以此数量估算当前四方厂现有资源及能力已经越来越无法满足动车组修理的需求,增加产能已是目前急待解决的问题。
2) 当前国内转向架检修行业的发展一直落后于轨道车辆整体发展水平,由于重视程度不够,转向架的检修生产过程存在以下问题:
· 生产模式相对粗放,现有的产线还未实现数字化、柔性化,主要表现为物流系统无法满足突发性的周期短、数量大的生产订单,工位处时常发生物料积存或待料现象;对物料、人员的调度多为半人工半计算机作业,效率及准确度不高。
· 检修装配过程基本以手工作业为主,信息化技术如MES管理系统等还未能实现自顶至下的全数字化、可视化应用,生产现场缺乏对过程的实时把控和管理手段。
3) 世界轨道交通行业,目前最著名的四家企业为中国中车、加拿大庞巴迪运输、法国阿尔斯通公司和德国西门子公司,这些国际巨头均为全球主要的轨道交通装备供应商,可提供整套客运和运输系统的解决方案,同时也有产品的研发、设计、制造、修理、销售、租赁与技术服务的能力,业务遍及全世界各地,但在国内转向架检修行业,外国公司鲜有建树。国内轨道交通业务全部由中国中车承担,中国中车承继了中国北车、中国南车的全部业务和资产,主要承接轨道交通装备的制造、修理业务,铁道部每年均会通过招标确定各厂的厂修车、配件供给数量,通过招标会各车企均可根据自身技术优势及地缘优势,获得一定份额的检修定单。
2. 转向架检修装配线布局
2.1. 转向架检修装配线布局规划 [1]
通过对国内转向架生产企业先进经验总结后,本产线采用了成组布置的原则,其思想是将设备布置与工艺流程进行结合形成的一种布置方式,其主要优点:物料搬运距离最短,物流效率高;人工无效移动时间短,工位间衔接紧密;在制品低、准备时间短;具有较高的柔性。整个产线以物料自动化出入库系统、智能移动平台、智能化天车为物料流转的核心,通过生产车间LCS生产管理系统对现场的多种生产模式进行调度,实现多品种、小批量转向架检修装配的高效生产,其生产线工作逻辑如图1。
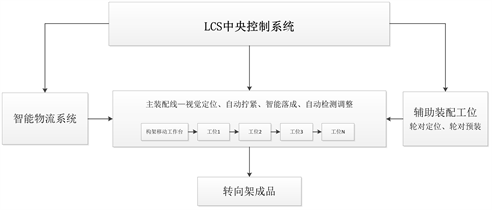
Figure 1. Process logic of the production line
图1. 生产线工作逻辑图
2.2. 转向架检修装配线作业区物流设计
整个转向架检修组装生产线的业务范围由10台AGV、2个立库(配盘立库、构架立库)和11个作业区(构架装配预组作业区、构架配线作业区、配盘作业区、构架装配作业区、轮对齐套作业区、线束预装作业区、零部件预装组作业区、落成组装作业区、转向架配线组装作业区、加载试验作业区、制动试验作业区)及一个智能吊组成。其中构架组装线和落成组装线各为两条。全部业务包含在两个厂房分区内,系统密集度很高,对物流设计、信息流设计提出了较高的要求。
2.3. 检修装配线转向架装配工艺设计 [2]
1) 以转向架五级修为例,当生产需求为节拍拉动模式时其构架组成装配工艺流程为图2。
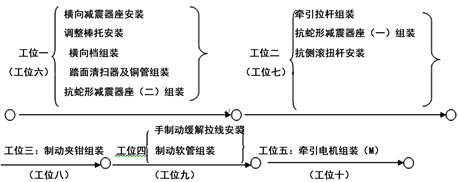
Figure 2. Assemble process of main-frame in pull mode
图2. 拉动模式下构架装配工艺流程示意图
其中构架在工位二、工位三、工位七、工位八等四个工位时构架处于反装状态,其他工位构架均处于正装状态。
2) 以转向架五级修为例,当生产需求为工位单元模式时其构架组成装配工艺流程为图3。
其中构架在工位一、工位三、工位五、工位六、工位八等五个工位时处于正装状态,其余工位为反装状态。
3. 转向架检修装配线物料配送系统设计 [3]
转向架装配检修车间在生产组织过程中考虑到检修品种、检修级别的多样性,一般采用工位呼叫的生产拉动模式,通过工位将生产过程中缺料信息反馈到生产调度系统,再由调度系统将配送指令下达到仓储系统进行物料供给来实现生产进程,而这种模式存在物流过程的连续性差;配送效率低;产线各工位的线边库不是缺料就是有积存。而这种问题产生的主要原因还是缺乏对物流信息及时、全面的采集以及高效、准确的数据分析。为此,新产线的车间级产线控制及物料配送LCS系统嵌入了齐套件的准时配送模型,该模型可根据采集到的现场过程数据经过实时计算,精准确定各类齐套件需配送的时间、工位和数量,再结合自动化的物料流转技术如自动输送线、智能移动工作平台等实现了对生产现场装配工位的主动配送服务,解决了被动响应所造成的一系列问题。
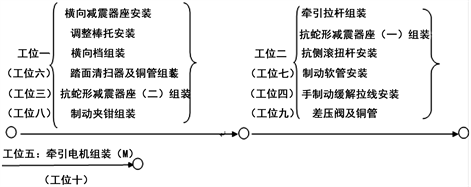
Figure 3. Assemble process of main-frame in working cell mode
图3. 工位单元模式下构架装配工艺流程示意图
3.1. 转向架检修装配线物料配送模型
这种基于神经网络的配送模型通过前期的训练及泛化,能很好地解决物料配送时间、配送工位、配送数量和配送装备调度的多目标优化问题,在现场生产过程数据的驱动下,模型不断对配送过程进行优化,通过反复迭代生成新的配送指令,给出配送建议,由人工进行最终决策或系统按一定的规则进行决策后,由自动化物料配送系统进行主动送料,从而达到真正的准时配送。
模型构建的主要运行机制采用了周期性事件驱动与突发性事件驱动相结合的模糊加权算法,正常状态下由程序后台按一定周期对产线数据进行采集并计算出理想的配送参数,当异常事件发生时如人工紧急插单、人工删单、设备故障及工位呼叫等情况,系统将停止发料并进行相应的中断子程序,在异常物料处理模式下,重新进行排产并对下一批配送的方案进行修正,其逻辑框图如图4。
3.2. 转向架检修装配线齐套件配送硬件设计
3.2.1. 配送系统布局及组成
零部件物流运输系统主要包括零部件配盘系统、零部件储运系统、电气控制系统和仓库管理及调度系统以及零部件装配物流系统组成。
零部件物流运输系统主要包括零部件收料、分拣、组盘、零部件信息自动采集、托盘信息采集、零部件自动传输、零部件防错、零部件自动存储、零部件自动上下料、自动出入库、零部件管理、零部件异常处理、相应物流调度控制、及与生产线控制系统之间的信息交互、报警、异常处理等硬件及软件。
3.2.2. 配盘及立库设计
配盘系统主要功能为根据生产计划将配盘区物料及时的配盘到托盘上。配盘区主要包括输送主线系统与配盘线系统,包含辊筒输送机、顶升移载机、顶升移栽转向台、提升机、顶升台、显示屏、手持终端及手持终端存放支架等设备(见图5)。
配盘区设有配盘台,配盘台用于零部件转盘、配盘所用。输送主线用于空-实托盘的转运。桥架钢平台用于提供托盘入库及紧急出口与让出移动工作台循环路线用。
每个配盘台人员根据配盘台上配置的显示屏显示的配料计划进行配料,每个配盘台上显示屏实时显示配盘情况。配盘台上设置托盘RFID阅读器,且每个配盘台上再配置两部手持终端扫描零部件(具有识别金属二维码功能)及其存放支架。
零部件在配盘台上配料完成后智能物料管理系统(WMS)根据零部件库房内托盘使用情况进行零部件托盘入库出库调度。实现零部件自动入库出库管理。
3.2.3. 移动工作台设计
传统的转向架装配多采用天车将装配中的构架在不同装配台位间进行吊转,天车的调度有很大的随意性,缺乏对整个装配线过程状况的感知,存在效率低、安全性差的问题,在新产线规划设计中,采用了AGV智能移动工作台替代天车进行构架的流转,由于没有了空中作业,安全性大为提高,同时二维码导航的AGV有定位精度高的优点,整个装配线共使用10台AGV小车,以立库系统为核心组成环形装配线,物料配送系统与装配工位紧密结合,实现高效率的组装作业。
4. 四方转向架检修装配线自动落成与自动检测、调整系统
转向架构架组装完成后需与轮对轴箱组成及驱动装置进行装配,组成完整的转向架,该过程在转向架装配环节中极为重要,目前车间落成作业由人工在天车的配合下,根据经验反复调整构架位置直至作业完成,对落成质量的控制也是通过目视检查的方法完成,检测项点为① 轴箱上下拉杆节点落入构架拉杆节点梯形槽接口内,② 轴箱体挡体组成与轴箱体挡体安装孔位对准时即为落成合格,这种生产模式要求落成时每一侧至少有一位操作者监督,发现问题时及时进行处理,操作过程复杂、效率低下、落成质量得不到保证。
为了解决此问题,在落成组装作业区落成工位的设计中采用了自动落成与自动检测、调整技术,通过整合先进的测量与数据处理技术,在落成过程中对构架姿态、轴距尺寸、轮对与构架侧梁基准面距离、对角线的尺寸等进行精确测量、调整,整套系统由智能天车、轮对定位台位、自动检测\调整装置组成,实现了转向架落成、调整的自动化作业(见图6)。
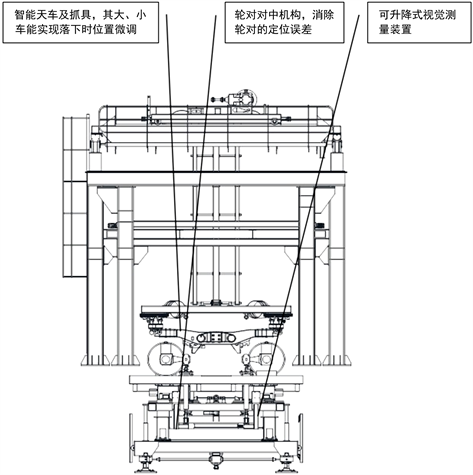
Figure 6. Design of automatic drop down
图6. 自动落成系统示意图
5. 数字化转向架装配技术在四方现场的应用
目前,该装配生产线已安装到四方车辆厂维修装配车间进行调试,已初步达成各项设计指标,结合现场调试发现的问题,正在对设计、工装、产线布局及各子系统等对应层级进行改进、优化,通过该产线的落地实施,对提升我国转向架装配线的数字化水平有一定的指导意义。
基金项目
本项目受中车青岛四方机车车辆股份有限公司《高速动车组关键零部件智能制造新模式应用》项目支持。
致谢
在本文的编写过程中,得到了《机械工程与技术》期刊各位编辑给予的大力支持,他们对文稿和图片进行了大量的修订,使该文得以顺利刊出,在此表示衷心的感谢。
参考文献