1. 引言
刮板输送机在煤矿的开采中有着十分重要的意义,刮板输送机已向高强度、大功率、长运输距离、高可靠性方向发展 [1] ,刮板输送机的链传动系统的主要传动方式为链轮链环啮合传动 [2] 。在实际的煤矿综采工作环境下,链轮链环发生的故障率占刮板输送机总的故障率比很高,主要有以下现象:卡链、断链、跳牙、链轮断齿、链轮链窝压溃等 [3] 。其中断链会影响刮板输送机的正常工作,导致整个综采工作面工作效率大大降低。导致刮板输送机链轮链环出现故障的主要因素:设备在启动过程时 [4] 、在发生卡链时和物料冲击刮板链等现象对链传动系统产生瞬间冲击力 [5] [6] ;链轮多边形效应现象对链传动系统产生周期作用力 [7] ,长期工作中链传动系统关键部件有磨损和腐蚀现象导致链轮链环失效 [8] 。本文为了解决上述问题,运用Ansys进行数字模拟仿真 [9] ,分析了链轮链环瞬时启动时的力学特性 [10] [11] [12] ,并列举了几种摩擦形式 [13] ,为提高煤矿开采的工作效率提供理论依据。
2. 链轮链环的振动和冲击
在实际的煤矿开采工作过程中,刮板输送机的工作环境极其恶劣,受力复杂多变。根据传动系统自身特点和受到作用力的性质可以分为两类:一类是运输物料对刮板链碰撞或打击过程中受到的作用力,二是链传动关键部件的自身特点使链传动受到作用力。
由于工作性质的原因决定了链传动系统中链轮链环具有耐冲击、耐腐蚀和抗疲劳特点。但是运输的物料不均匀会使链传动系统出现片帮、卡链等现在冲击链传动系统;链轮多边形效应存在时链传动系统在工作过程中会是链轮与链环和链环之间反复冲击和振动。链传动系统出现故障的主要原因正是振动和冲击,最终会导致断链事故,影响综采工作面所有设备正常工作。
我们基于冲击冲击动力学理论和非线性接触理论考虑摩擦因素及啮合接触等因素运用ANSYS/LS-DYNA对启动过程中链环之间和链环与链轮啮合冲击过程进行数值模拟仿真,分析出启动时链条、链轮的应力分布、应变等动态特性,从而分析出链轮链环振动冲击特性。
2.1. 链环之间冲击模拟
本节以刮板输送机“SGZ764/630”型的链环为研究对象,链环参数为φ 30 × 108并对链环进行各截面相同的假设,对链条进行建模仿真,模型参数如表1所示。链环模型采用SOLID164单元模型,采用自动划分网格对链条模型划分,结果如图1。链条模型从左至右进行标号。
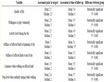
Table 1. Material characteristics of chain
表1. 链条材料特性
链环之间设置面–面自动接触,设滑动摩擦系数为0.2;静摩擦系数为0.1,据刮板输送机的实际情况,设刮板输送机速度为1 m/s,链条的张力为200 kN,模拟链环启动的瞬间。静止链环为链环1,随动链环为链环2,主动匀速运动链环为链环3,在模拟过程时,链条3右端被施加链张力和初速度,设置1秒仿真时间设置1秒,仿真后得链环在1秒的应力云图和加速度云图如图2和图3所示。

Figure 2. Equivalent force nephogram of the link contact
图2. 链环接触等效应力云图
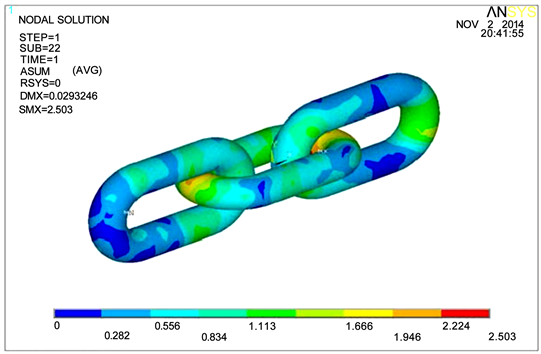
Figure 3. Acceleration nephogram of the link contact
图3. 链环接触加速度云图
结果表明:当刮板输送机启动时,链条的应力主要出现在两个链环的接触点上,链环1弯臂处为最大值,最大应力值等于498 MPa,接触部位应力次之的为随动链环2弯臂,主动部件为链环3,因为冲击碰撞作用的瞬间,最大应力出现在链环3弯臂处,它表明当被迫拉动时,应力值最明显。链环最大加速度为链条1右端直臂与弯臂连接过渡处,最大加速度等于2.503 m/s2,链环1与链环3产生的加速度大于链环2。为了在启动过程时链环的动态响应做更进一步的分析,分别把链环1、2、3弯臂接触区域上最大应力点(分别对应图1中的A、B、C、D点)绘制在同一坐标系中,做出这些点在0~1 s内应力变化的曲线,图4是三链环接触点最大等效应力曲线。
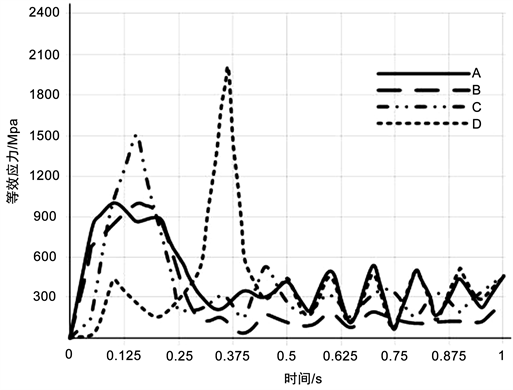
Figure 4. Stress curves of contact point
图4. 接触点应力曲线
仿真结果分析:启动1 s内链环之间不只是发生一次相互碰撞而是发生了7次碰撞,前两次相互碰撞最为激烈,之后5次趋向于平稳;因为链环2和链环1被链环3带动,首先在链环1与链环2之间发生相互碰撞并产生应力达到峰值,在0.2 s前后链环2右端接触应力达到峰值,在0.35 s前后链环3接触应力产生峰值,此后各接触点位置因为相互碰撞作用各接触点接触应力峰值延后,随后波动在确定值附近小范围内波动。
2.2. 链轮链环啮合冲击模拟
本节以SGZ764/630型综采工作面刮板输送机的链轮链环为研究对象,链轮的齿数为7,链环为φ 30 × 108,同时对链轮和链环做合理的简化假设,建立链轮链环啮合仿真模型,链环模型参数如表2。链轮链环有限元模型采用SHELL163、SOLID164单元类型,链环与轮齿分网较密,轮毂处分网较疏,网格划分,结果如图5示。
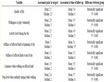
Table 2. Material characteristics of chain
表2. 链条材料特性
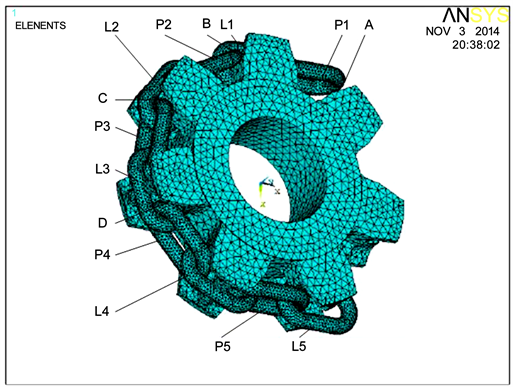
Figure 5. Overall network of chain link and sprocket meshing
图5. 链环链轮啮合整体划分网络
根据综采工作面刮板输送机的实际工况,假设其链条运行速度为1 m/s,链条张力为200 kN,链轮转矩60.9 KN∙m,转速3.97 rad/s。启动时,啮入端链环速度和电机转速降低,转矩增加,模拟过程中,链轮具有初始角速度3.97 rad/s,给链轮施加转矩载荷,0.05 s后增大为120 KN∙m,假设图中啮入端的链环P1施加固定约束,采用面–面自动接触,定义动、静摩擦系数依次为0.2和0.1,设置仿真时间为0.5 s进行求解。得到发生卡链时链轮链环冲击的变形云图和应力云图分别如图6和图7所示。
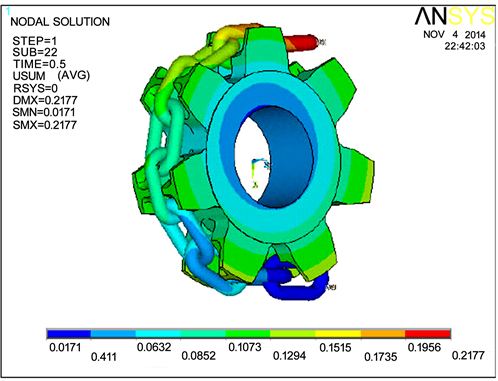
Figure 6. Aberration nephogram of chain link and sprocket meshing
图6. 链环链轮啮合变形云图
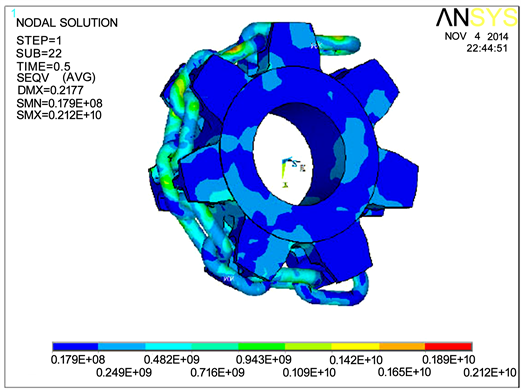
Figure 7. Stress nephogram of chain link and sprocket meshing
图7. 链环链轮啮合应力云图
从链环链轮啮合所有的位移仿真结果可以得出,启动时链环被链轮在转矩的作用下带动旋转,由于啮入端链环的约束,所以啮入端链环出现了比较大的位移,在链轮的拉动下啮入端链环变形为21.77 cm;从应力仿真结果可得应力变化最大主要存在链轮链窝、链环直臂、链环直臂与弯臂连接处,最大应力可达2120 Pa,链轮齿根和链窝出现了最大应力。为了便于对链轮链环啮合过程中啮合点的冲击动态响应做进一步的分析,测量了平链环与链轮链窝接触应力,各平环与链轮链窝接触点命名为A、B、C、D (如图1所示),将各点应力值绘制到同一个坐标系中得到瞬间接触应力曲线,如图8所示。
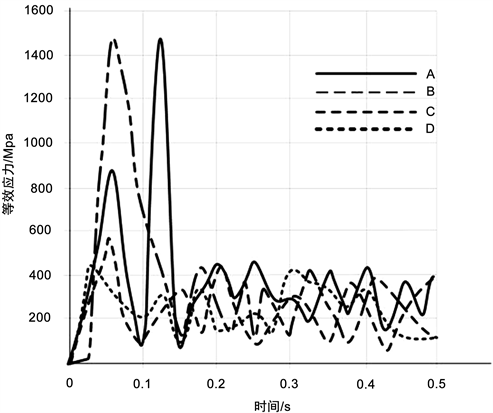
Figure 8. Stress curves of contact point on meshing area
图8. 啮合部位接触点应力曲线
仿真结果分析:启动时0.5 s内链轮链环之间并不是发生一次碰撞而是发生了6次相互碰撞,前两次碰撞最为强烈,之后4次趋于平稳,最大冲击力可达1450 MPa。
3. 链轮链环的磨损损伤和疲劳损伤
综采工作面刮板输送机链轮链环主要损伤种类还包括磨损失效和疲劳失效。在输送机上加载或减载物料都会产生松链或紧链现象,该现象会使链环与中部槽过度摩擦和链环之间相对滑动摩擦,同时也会造成链环与链轮啮合过程中出现冲击后再滑动摩擦等,摩擦会对链环链轮产生磨损。正常工作中,由于链轮多边形效应会使链传动系统受到周期性的作用力,这种周期性作用力会造成链轮链环出现疲劳裂纹,使链轮链环失效。
3.1. 链轮链环的磨损损伤
刮板输送机运行时,链传动系统将承受多种性质的载荷作用,处于一个非常复杂的工况环境,并且链条在张力、温度、频率等因素变化的情况相对运动,链环和链轮表面会不断损耗产生变形,造成链传动系统损伤。
按磨损形式分类:链轮链环磨损主要有黏附磨损、磨粒磨损、疲劳磨损、机械化学磨损和微动磨损等形式。磨损影响刮板输送机的使用寿命和可靠性。
关键部件按接触类型分类 [13] :刮板输送机链传动系统中磨损主要有链环与链环之间、链环与刮板、链环与中部槽、链环与物料和链环与链轮等。在链环与物料、链环之间以及链环与链轮之间是最明显的接触磨损形式。下面主要介绍两种接触类型的磨损。
3.1.1. 链环与物料之间的磨损
综采工作面刮板输送机链条暴露在开发环境下,运输的物料中并且夹杂矸石、金属颗粒和腐蚀性颗粒等杂质与链环反复接触,这些硬度比链环高的细小物质会使链环产生犁沟,进而该处会产生塑性变形,当硬度比链环高的细小物质再次作用在产生塑性变形出犁沟出会加深该犁沟并产生更大的塑性变形,这样反复作用犁沟形成裂纹使链环失效。
3.1.2. 链环与链轮之间磨损
链环与链轮啮合过程中,由于受到随机载荷、多边形性效应和物料掺杂在链轮链窝,影响链轮链环啮合,链轮链环在啮合过程中会有啮入冲击力、啮入滑动、啮出滑动等现象,磨损位置主要在链轮链窝处,链窝的磨损原因包括接触疲劳磨损、点蚀磨损、磨粒磨损、胶合磨损等,其中接触疲劳磨损是主要原因。在重载荷和冲击载荷的双重作用下圆环链和链轮之间产生了缝隙,与此同时,在变力重载荷作用下链轮链窝接触区域产生最大应力,使得链传动系统链窝接触区域会产生疲劳磨损。该疲劳磨损不仅导致连环链轮之间的间隙加大而且传动过程中的冲击载荷也会变大,反过来更加大了接触疲劳磨损,影响了链轮的使用寿命。当硬度大于链轮链环的物料掺杂在链环上啮入链轮时会使链轮链窝和链环啮合点出现犁沟,啮入滑动和啮出滑动会使链轮链环接触点温度瞬间升高使链轮链环出现塑性变形,这是磨粒磨损,使之造成链轮链环失效。
3.2. 链轮链环疲劳损伤
由于综采工作面刮板输送机在实际工作中存在随机冲击载荷和链轮的多边形效应,使啮合在链轮上的链条的速度具有周期性振动,造成链轮链环的疲劳损伤,降低了刮板输送机的可靠性。
关键部件出现疲劳损伤的形式有:链环在最大应力位置出现疲劳裂纹,发生断裂;链轮链窝接触面压溃。
链环疲劳损伤一般分为:出现裂纹,裂纹扩展和最终断裂三个阶段。链环在周期性脉动载荷作用下出现裂纹,在应力的作用下,裂纹增大,当裂纹增大到一定程度时该处的强度急剧下降,在周期性载荷力作用下该处的裂纹急剧增大直至链环断裂出现断链。链环的疲劳过程与链轮的材料、加工过程和受力情况息息相关。由于链条是有链环环环相扣相连接,在链环直臂和弯臂受拉应力和剪应力的作用,链环直臂处主要受拉压力,该处容易出现最大应力;焊接部分如果有缺陷,在受拉应力时也会出现最大应力,最终导致疲劳损伤;立链环在工作中,溜槽连接处的棱角会划伤立链环的表面,使立链环出现裂纹,导致出现应力集中现象,使链环出现损伤。
链轮是该系统的传动部件,链轮的设计质量对刮板输送机的正确啮合以及可靠性有重要影响。此外,链轮的承载能力和质量的提高对未来刮板输送机的发展方向有着重要影响。影响链传动系统损伤的因素有:几何形状、材料性质、表面状态、残余应力、应力集中、载荷频率、温度和环境等影响。只有充分的理解各种因素影响链传动系统关键部件的疲劳强度规律,才能更好的找到抗疲劳的有效途径。
1) 几何尺寸影响:几何尺寸和部件的疲劳强度成反比例关系。
2) 材料性质:圆环链和链轮在选择材料过程中既要满足强度要求,又要考虑到需具有良好的抗疲劳性能。
3) 残余应力:构件在生产制造过程中,在多重工艺的相互作用下,仍有部分作用和影响停留在构件中。残余应力严重影响结构的疲劳强度度、抗腐蚀开裂和高温蠕变开裂能力。
4) 表面状态:链轮链环接触的表面状态,表面状态所受应力越高,产生的缺陷就越多;材料表面层约束越少,链轮链环相对滑动和链环之间相对滑动都容易出现开裂现象所以零件的表面状态也影响其疲劳强度。
5) 载荷频率:零件的加载时间和频率受最大应力载荷的影响,在外载荷作用下零件进行塑性变形之后,变形量与最大应力载荷的作用时间成正比。
6) 温度和环境:链轮链环在腐蚀环境下表面材料会发生氧化形成氧化膜,在疲劳载荷作用下氧化膜会出现局部开裂现象。材料表面易形成腐蚀坑,腐蚀坑处易产生应力集中,反过来加速了裂纹的扩大,降低了使用寿命。
4. 结论
本文主要分析了综采工作面刮板输送机链轮链环损伤形式,主要分为链环之间的振动、冲击和正常工作磨损损伤及疲劳损伤。第一节主要利用冲击理论并用有限元软件分析了启动过程中链环之间和链轮链环之间冲击力过程;第二节主要分析了链轮链环磨损损伤的原因和种类、链轮链环疲劳损伤的原因,因此我们提出了改善链轮链环的加工材料,提高材料质量,降低材质中杂质的百分率,进一步提高抗磨损能力;改进零部件的材料特性和加工工艺,严格控制链轮形状和链环的节距尺寸偏差,使其在一个高标准的合理范围内,降低裂纹的产生,降低表面的残余应力,防止裂纹的扩展,提高链轮链环接触区域抗疲劳腐蚀强度;改变链轮链窝的形状或链轮链环接触形式,将链轮与圆环链的啮合接触形式由点接触变为线(面)接触;严格控制工作过程中冲击力的大小,在入料口添加导向挡板等改进措施。提出的改进措施能提高链轮链环的抗磨损能力和延长使用寿命。