1. 引言
刮板输送机是综采工作面的主要运输设备,能实现工作面运煤的连续性与实时性刮板输送机与采煤机相配合,能最大化保证工作面连续生产与推进的可靠性 [1] 。一方面,刮板输送机单位时间的运煤量受采煤机的割煤速度影响,工作面实际情况复杂,采煤机割煤速度受煤层条件、各工序相互配合等因素影响;另一方面,由于实际割煤、装煤工作的不连续性,刮板输送机运煤的持续时间也没有固定规律 [2] [3] 。目前现场生产过程中通常采用即时调节的手段,使刮板输送机运输速度与运煤量相互配合以达到机器效率的最大化 [4] 。国内外有关刮板输送机速度调节的研究成果显著,目前主要以变频调速方法应用最为广泛 [5] [6] 。通过使用变频调节,可以极大地改善刮板输送机的电机转速的精度,这就可以保证刮板输送机的运转速度能够及时满足运输需求,实现刮板输送机的启动方式改变为软启动,同时这种启动方式有其自身的优点,即解决了刮板输送机频繁断链的实际问题。通过对变频调速系统的研究应用,不仅实现链速随煤量的变化而变化,而且最终实现综采工作面刮板运输机控制系统节能降耗的目的,提高系统的安全性及可靠性。
2. 国内外发展现状及发展趋势
随着采煤工艺与采煤设备的不断发展与改进,超长工作面、中厚煤层一次采全高的矿井越来越多,煤炭产量随之急剧增长,这种生产情况下,传统的低效率、中短长度的刮板输送机难以满足生产现场煤炭运输的实际需求。为了满足现代化矿井的建设需要,更加凸显了研制与目前生产实际相匹配的刮板输送机的必要性。目前国内正常使用的刮板机链速大部分为1.2 m/s,最高仅为2.0 m/s左右,而国外输送机速度可达到3.5 m/s左右,国内外刮板输送机性能差异巨大,在链速提高方面我国仍需开展大量工作,为了降低煤炭开采运输成本,提高矿山经济效益,我国刮板机链速提高的研究工作更加紧迫 [7] 。
驱动装置作为整个刮板运输系统的核心动力装置,是刮板输送机高效率运输与持续稳定工作的保证,驱动装置的优化研究作为改善刮板输送机的运输效率的主要途径之一,一直是行业研究的热点问题。目前国际上用于刮板机的驱动装置主要有:CST驱动系统、电动机加液力耦合器传动装置、液体粘性传动调速装置、交流变频调速装置等。在我国,广泛使用的调速系统有直流晶闸管调速与变频调速系统,而在矿井生产现场采用的能源系统为交流电力,并且电控简单,并能实现恒转矩控制,所以变频调速得到广泛应用,并在未来的发展的前景非常广阔,是未来速度控制的核心 [8] 。
3. 刮板机工作原理及节能方法
刮板输送机型号选择为SGZ800/800,中部槽宽度800 mm,额定功率2 × 400 KW,链速1.2 m/s,运输量1200 t/h,是目前广泛使用在综采工作面的原煤运输设备。其原理是将原煤通过刮板链运输至转载机,是工作面“三机”之一 [9] 。
煤矿作为传统企业之一,升级转型是必然之路,而通过先进的控制系统,降低电能消耗,进一步降低企业成本更是意义重大。刮板输送机作为煤矿主要运输设备,在实际生产过程中输送机运煤量波动比较大,经常会出现皮带无煤空转或者在煤量很低情况下运转,由此造成了运煤效率低下的状况,产生了严重的电力浪费与机器利用率不足的现象。在这种状态下运转的刮板输送机其电动机工作处于一种较差状态,从而导致电动机的能量损失量较大,系统运转效率不高,使能源利用率大为降低,造成矿山能源浪费,开采成本增加。通过引用模糊控制,利用PLC等先进的控制技术,分析刮板机启动顺序及工作面生产流程曲线,较少刮板机空载时间,而煤量较大时,通过变频器提高设备转速,进而实现刮板机运量柔性可调,进一步降低设备能耗。
4. 变频器的运行原理及特征
变频器主要是使用电力半导体器件的通断功能,实现恒定电压、恒定频率的交流电与电压、频率可实时调整的交流电相互转化。目前使用较为广泛的变频器实现变频的方式是将电压由交流转换成直流再转换成交流,称之为VVVF变频或矢量控制变频。首先利用整流器将工频交流电源变为直流电源,然后再将直流电源变换为交流电源,并且实现频率和电压可控性,最后利用频率可控的交流电给电动机供电 [10] 。变频器构件如图1所示。
4.1. 交–直部分原理
整流电路:不可控全波整流桥主要有VD1、VD2、VD3、VD4、VD5、VD6共计六个整流二极管组成。当电源电压为1200 V时,选择反向耐压值为4200 V的二极管,二极管的正向电流根据电机的额定电流确定,一般取额定电流的1.414~2倍。如图2所示。
4.2. 直–交部分原理
V1~V6逆变管(IGBT绝缘栅双极型功率管):逆变管作为逆变电路的主要构件,是变频器的核心元件,可以将直流电转换为幅值和频率都可以调节的交流电。
D1~D6是续流二极:续流二极的作用主要表现为提供通道,一方面可以为电动机制动过程中再生电流返回直流电提供通道,另一方面为逆变管V1~V6提供通道,主要表现在交替导通和截止的换相过程 [11] 。
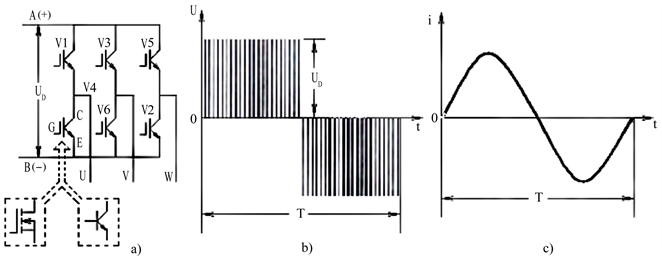
Figure 2. Inverse bridge structure diagram
图2. 逆变桥结构图
4.3. 控制部分:驱动板、电源板、控制板(CPU板)
驱动板:主要是将CPU生成的PWM脉冲经驱动电路产生符合要求的驱动信号激励IGBT输出电压。
电源板:开关电源向各电路板提供低压电源,包括:±5 V、±15 V、±24 V。向CPU及其控制电路、附属电路、显示面板等提供电源。
控制板(CPU板):又称为CPU板,其功能同人类大脑类似,通过接收处理信号,实现程序的控制。
5. 刮板运输机变频调速方式研究
煤矿井下所用的电机通常为Y系列低压鼠笼式三相异步电动机,Y系列电动机为同一系列电动机,其内部各配件参数、制造流程、方法均具有一定的相关性,这就使得同系列的电动机的特性曲线类似。
5.1. 分析刮板机运行电流与效率关系
众所周知,刮板机空载与重载最大区别就是电流变化,为能实现精准的控制,首先分析电流与效率特性曲线,得出设备运行最佳工况点,从而进行控制。考虑η/η额定变量与电机电流之间关系,绘制电机特性曲线(图3),曲线表示的函数关系能够满足不同型号的Y系列电机。
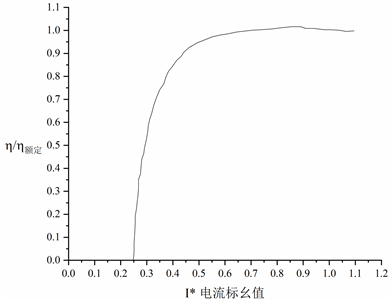
Figure 3. Motor current efficiency curve of Y
图3. Y系列电机电流–效率曲线
空载时输出功率P2 = 0,故η = 0。负荷初始值为0,当其从0增长时,电机总损耗ΣP呈缓慢增长趋势,效率曲线斜率值大,曲线增加速度快。定义变化损耗P* = Pcu1 + Pcu2 + Pad,不变损耗P*' = Pfe + Pmec,当P* = P*',效率η达到最大值。根据图3可知,当电流标幺值I*取值在0.8~0.9时,η值最大;I*大于0.6时,η保持较高值;I*小于0.6时,效率η取值下降,且下降速度很快,直至接近零值。因此,当I*大于0.7时,效率值可以满足节能需求,当I*小于0.7时,效果不满意,应考虑进行节能改造。对于I*小于0.6的电机,必须进行节能改造。而矿用电机的I*大都小于等于0.5,在该区间的效率η随着I*的变化而急剧变化 [12] 。
5.2. 频率变化时效率曲线
根据电机性能曲线,电压、电流、转距的关系,结合上述电流与效率的特性曲线,通过公式 [13] :
(1)
(2)
式中:η——效率,Pcu1——定子铜耗,PFe——电机铁耗,Pcu2——转子铜耗,Pω——机械损耗,PΔ——杂散损耗,Rm——励磁电阻,I1——定子电流,Im ——励磁电流,I'——转子归算电流。
从结果可知,当频率高于30 Hz时,电机可取得较高的运转效率。当电机在低频率下运转时,电机处于较低的运转效率模式。当频率为20 Hz时,电机的工作效率出现较大的下降,最大值约为0.6倍的最大效率,当频率为10 Hz时,电机运转效率难以保持恒定呈快速下降状态,仅为最大效率的40%。详见图4所示:
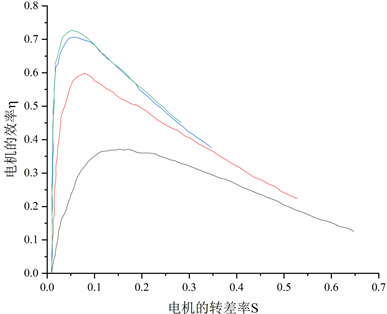
Figure 4. The torque lifting voltage is 100 V
图4. 转矩提升电压为100 V
依据以上分析,决定运输机的调速范围在35~50 Hz之间,这样,可以在保证运输量的情况下,可使调速电机在最高效率区间运行。
6. 变频调速系统组成及工作原理
刮板机工作站可以手动或自动向各工作站传达命令,控制速度的提升或降低,用于系统的最高指挥权。刮板机工作站拥有系统的知情权,可观察全系统每个工作站的运行信息。刮板机工作站的控制箱拥有系统最高权限,串口通讯采集工作面刮板机的运行速度、运行电流等数据,并且将数据送给其它工作站。两台变频器接收来自集控装置的起、停信号,控制驱动刮板输送机,并且将变频器的运行数据送给控制箱,如图5、图6所示。
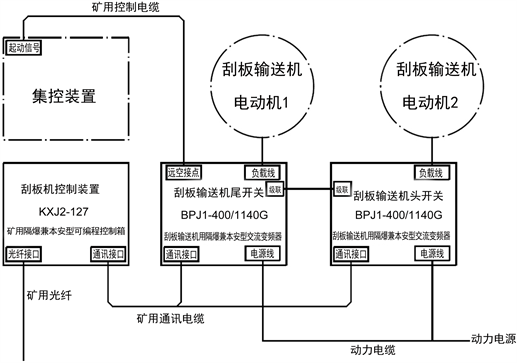
Figure 6. Working principle diagram of scraper workstation
图6. 刮板机工作站工作原理图
7. 现场试验及应用情况
7.1. 控制设计
电路图、供电图及网络控制图纸是根据现场的实际情况所设计的,并依据所设计的图纸确定PLC控制单元中的连线方式、布线位置及控制程序,最后编写控制触屏中的画面程序,将PLC控制单元与画面程序相连接。
7.2. 现场调试
为实现刮板机的高效运转,现场调试环节至关重要,首先进行变频器的调试,输送机在不同的运行工况下,输送机的速度根据工况进行及时调节,变频器是电机速度调节的主要手段。
在刮板机工作前通过检查在变频器不同的频率下链条转动及转速是否稳定,进而达到调速的功能,其次进行功率平衡的调试,依据电机平衡程序进而检测出其输出频率情况及刮板机运输煤量发生变化时电机的输出频率是否平衡,若电机输出功率不平衡是可能出现刮板机的停机及电机频率波动太大,因此为了保证刮板机能够正常平稳的工作需进行现场的调试,如首先检测减速器或者驱动部分是否能正常工作及功率平衡控制器的程序是否正常输出。进行功率平衡测试和软启动测试,结果见图7。

Figure 7. Power balance and start test diagram
图7. 功率平衡和启动测试图
7.3. 系统节能测试
通过对刮板机的变频调速改造,使其能够在不同的输送量的情况下刮板机以相应的速度运行,从而节约电能,进而减少矿方的成本投入,为了实现以上的功能,因此编写了没节能的程序与有节能的程序两种以供客户选择 [14] 。根据测试结果,在满载状态和轻载状态时分别改变链速,其能量消耗率如下表1:
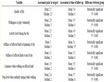
Table 1. Relationship between the filling rate and the power and the energy consumption rate
表1. 输送量恒定时功率及能量消耗率同填充率的关系
8. 结论
1) 通过对刮板输送机的控制系统的软起动、功率平衡、自动节能等工作原理的研究,进而形成了矿山智能化自动控制系统的技术,很好地解决了现场生产的实际问题。
2) 通过对刮板机的变频调速改造,使其能够在不同的输送量的情况下刮板机以相应的速度运行,从而节约电能,进而减少矿方的成本投入,为了同时实现以上节能与功率自动平衡的功能,需要重新编程序以同时实现这两种调解功能,提高了输送机运行控制的智能化。
3) 刮板机通过配套的变频器进而根据输送量的情况实现在线变频调节,从而提高了电机的工作效率、输送能力、机械转化效率,从而实现自动节能功能。当刮板机的节约电量达到20%左右时,电机的工作效率能一直保持在90%以上,且能保证电机满载起动,而刮板输送机的整体配件(链条、刮板、中部槽)的损耗率明显降低,实现了良好的经济效率。