1. 引言
起爆器是一种作为初始起爆源的航天火工装置,其内部容腔填充含能粉体材料作为能量物质,工作时利用电流使容腔内的电阻元件迅速发热,引燃与其接触的含能粉体实现换能,输出高温高压燃气或爆轰波,完成预定功能 [1] 。
起爆器内部所填充的含能粉体材料一般为起爆药、烟火药和猛炸药等火工药剂 [2] ,药剂装填在直径2 mm~8 mm的小容腔内,装填时需要通过加压达到一定的装填密度,以保证其发火性能。目前的装填过程均由人工来完成,操作人员手持装药容器将药剂通过漏斗状导向模具倒入起爆器壳体内部的装药容腔,然后放入压力机进行加压。在目前的装配过程中,操作人员直接与火工药剂接触,人机隔离程度低,存在较大的安全风险,特别是起爆药等火工药剂对静电、摩擦及撞击刺激非常敏感,人工操作不当容易引起药剂爆炸,威胁到操作人员人身安全。设计开发自动装填装置代替人工操作进行含能粉体材料的装填,是实现人机隔离解决上述安全风险的有效手段,对提高生产效率和过程安全性均有重要意义 [3] 。
目前在兵工和民爆领域已开展过多种含能粉体材料自动装填系统的研究,特别是在枪弹发射药和雷管炸药自动装填方面开发出了较为成熟的技术装备,并已实现工程化应用 [4] 。对于航天用起爆器,由于其装药容腔小、装药量精度要求高、工艺控制过程复杂,存在一定的技术障碍,尚无相关技术实现研究应用 [5] 。
2. 工作原理及系统组成
根据起爆器含能粉体材料装填的功能需求,设计的系统工作原理如图1所示。起爆器壳体上料后首先装入导向模具,然后将含能粉体通过导向模具倒入壳体内部,再通过加压装置进行压装,使得药剂粉体达到一定的装填密度,最终将模具卸下,完成整套装填流程。
起爆器含能粉体材料自动装填系统以机械执行机构为主体,以线式布局执行上述装填流程,系统由上下料模块、装模模块、装药模块、压药模块和退模模块组成,如图2所示。上下料模块的主要功能是起爆器壳体的自动上下料以及壳体标识的扫码识别;装模模块的主要功能是导向模具的自动定位和装配;装药模块的主要功能是药剂容器的自动拾取和药剂的自动装填;压药模块的主要功能是药剂的自动加压以及定位;退模模块的主要功能是压杆和导向模具的自动卸模。各模块依次布局在步进式传输线上,独立并行工作,但由于各项执行动作的节拍不一致,未充分发挥各执行器的生产效能,在模块设置时对执行器位置进行了调整,并在模块之间设置了流转等待工位以均衡节拍。
3. 关键技术研究
起爆器的装药量范围一般为10 mg~60 mg,精度要求为±1 mg以内。在自动装填系统的工作流程中,药剂先按目标重量分量后再逐份装填。在试验过程中,药剂粉体会在装药容器或模具中粘附,造成实际装药量的损失,甚至超出公差范围,影响装填质量。因此针对该问题进行了研究,以制定可靠的装药精度保障措施。
按照自动装填流程采用相应的装药容器和模具对实际装药量的损失进行量化验证,通过装药前后壳体重量的称量计算实际装药量,进一步计算出损失量。以某型起爆药为研究对象,在30个样本的小批量试验中,装药量超差率为63%,装药量损失在1.2 mg~2.7 mg范围内,平均装药量损失为1.6 mg。根据人工生产操作的经验,对于药剂的粘附损失问题,主要有吸湿和静电两项潜在的影响因素,首先采取了控制措施对这两项因素进行了验证。
对于药剂吸湿因素的验证,通过在装填之前进行烘干处理来实现。以最高安全烘干温度60℃为试验条件,按照烘干时间制定了1个对照组和12个试验组,每组3个样本,试验结果如图3所示。试验表明,吸湿因素对装药量损失有显著影响,通过烘干处理可降低装药量损失,60℃烘干2 h可作为优选控制参数。
对于药剂静电因素影响的验证,通过在装填环境中增加离子风来实现。在离子风机送风条件下进行装药试验,通过30个样本的试验统计,装药量损失在0.7 mg~1.5 mg范围内,平均装药量损失为0.93 mg。试验表明,静电因素对装药量损失有影响,通过离子风处理可降低装药量损失。
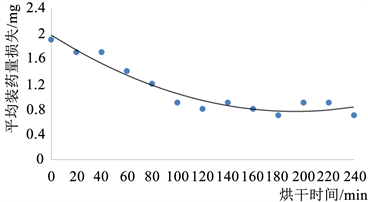
Figure 3. The test results of hygroscopic factors
图3. 吸湿因素影响试验结果
以上两项控制措施仍不能使装药量的损失降低到可忽略水平,拟增加振动措施使装药容器和模具中的药剂尽可能地落入装药容腔中,针对该方法进行了研究验证。通过振动试验台施加振动,按振动频率制定了1个对照组和10个试验组,每组3个样本,试验结果如图4所示。试验表明,增加振动措施可有效降低装药量损失,但振动频率存在适用范围,5 Hz~20 Hz范围内的振动有效,10 Hz可作为优选控制参数。

Figure 4. The test results of vibration measures
图4. 振动措施影响试验结果
应用各项控制措施,在60℃烘干2 h、10 Hz振动以及离子风处理条件下,通过30个样本的小批量试验统计,装药量超差率为0,装药量损失在0~0.2 mg范围内,平均装药量损失为0.1 mg。试验表明,各项措施的综合应用可将装药量损失控制在0.2 mg以下。基于该试验结论,将药剂分量的控制范围缩小,误差控制在(−0.8~1) mg范围内,可以保障装药量满足精度要求,相关措施及控制参数可应用于自动装填系统的开发。
4. 控制系统设计及实现
起爆器含能粉体材料自动装填系统要实现机器人、压机、各项直线模组以及各类执行气缸的的动作控制,以及相机、压力传感器、接近开关、光电开关等采集器的数据通讯,应用到的执行器及采集器达80余个。为适应大量的控制及通讯需求,采用了分级集中控制的方式,除了使用PLC进行执行控制外,还开发了上位机系统进行数据处理及状态监控,如图5所示。
系统最底层为执行层,由多种执行器和采集器接收上层触发信号,执行相应功能并反馈信号或数据,具体包括上下料机器人、装模定位模组、拾取气爪、装药机器人、压药伺服压机、卸模定位模组、模具定位接近开关、相机以及扫码器等。
系统中间层为控制层,为兼容各类执行器的控制需求,充分保障系统的稳定性及可拓展性,采用PLC控制器,并应用了I/O拓展及模拟量拓展模块。为适应系统各执行模块的并行工作需求,根据触发及反馈情况进行了联动控制。
系统最上层为监控层,为满足系统工作过程中压力、时间、状态照片等多项数据的记录处理需求,在工控机操作系统上开发了上位机控制软件,实时获取设备运行数据,将采集的产品序号、压力曲线、加压位置、保持时间等数据进行整理分析,并形成记录报表,保证生产过程的可追溯性。使用上位机软件还可体现出与更上层的数据平台的通讯优势,通过以太网使用WebService、Socket等常用的网络通讯技术,便能够与企业级MES等管理系统进行数据传递 [6] 。
5. 关键结构设计及实现
为了适应起爆器壳体在药剂自动装填过程中的连续上下料需求,实现无人化生产,系统在上下料模块采用托盘整垛上料、机器人逐个抓取的方式。如图6所示,整垛装有壳体的托盘来料后装入托盘上料位置,由机器人利用气爪将壳体抓起上料,整盘壳体抓取完后,利用锁紧平移机构将空盘移到下料位置码垛。壳体在装药完成后同样通过机器人抓取放入托盘中,当一个空盘摆满盘后,利用升降机构将该盘下移,平移机构将上料位的空盘叠放到上面,实现连续运转,该方式可实现600个以上壳体的连续上下料。
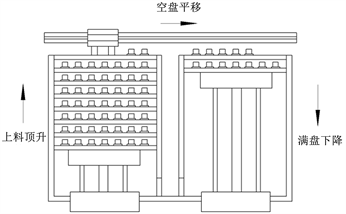
Figure 6. The mechanism of continuous feeding and discharging
图6. 连续上下料机构
为实现药剂装填过程中起爆器壳体的连续流转,各项定位及导向模具需要循环利用,起爆器壳体的定位底座固定在传输线上,在药剂装填完成后,压杆和导向模具会被依次取下,通过柔性传输线流转回安装工位,实现系统内循环使用。为适应模具的清理和更换需求,在流转过程中设置了压杆和导向模具的清理工位,并且兼容了人工和设备清理两种方式,实现了不间断在线清理和更换。
为保障药剂的装填密度,采用高精度伺服压药装置将壳体里面的药剂进行压实,压药结构主要由伺服压药机构、定位机构、位移测量机构、浮药处理机构等零部件组成。其工作过程为:传感器检测到起爆器壳体到位后,伺服压药装置下行,其上的定位装置首先接触模具进行定位;压药杆继续下行压药,同时发讯杆对位移传感器发讯测量;当压药杆运行到下限位置或达到设定力时,停止压药并开始保压;当达到保压时间后,伺服压药装置复位,压药杆缩回;上位机对压力和位移进行记录分析,形成压力曲线。
6. 应用效果
起爆器药剂装填性能一般通过起爆试验时的起爆压力峰值和及其获取时间这两项关键指标进行判定 [7] 。在某批利用本系统进行药剂自动装填的起爆器中,抽取了20份样本进行了起爆试验,其压力峰值标准范围为(28~32) MPa,峰值获取时间标准范围为起爆信号发出后(2.5~4.2) ms,试验结果如图7所示,样本数据均落在标准范围内,药剂装填性能满足标准要求。
目前该系统已实现工程化应用,在实际应用过程中,各批次起爆器均通过相关指标验收,系统在节约人力基础上的生产效率能够达到120份/h,经济效益显著。同时该系统脱离了人工操作,从本质上实现了人机隔离生产。
7. 结论
通过装药量精度控制关键技术的研究,采用药剂烘干、离子风除静电及振动装药处理的措施,能够有效解决装药量损失问题,结合控制系统及关键机构的设计实现,起爆器含能粉体材料自动装填系统得以完成开发。试验及应用结果表明,该系统能够满足起爆器含能粉体材料装填性能要求,并且得益于自动化手段的实现,能够有效节约人力成本,显著提升含能粉体材料装填过程的安全控制水平,具备广阔的应用前景。