1. 引言
隧道工程地质条件复杂,仅依靠围岩自身承载能力往往无法保证工程施工的安全性,因此,施工过程中选择合适支护结构是关键。在隧道钢筋混凝土衬砌施工中,全液压钢模台车的应用不仅可以提高混凝土施工质量,同时也能提高施工工效,节约成本。张志高等 [1] 在隧道混凝土衬砌中进行了组合钢模板支护;罗勇等 [2] 利用脚手架组合刚模板在深竖井混凝土衬砌中进行了应用。较多学者和工程技术人员开展了隧道工程组合钢模支护的研究与工程应用 [3] - [13] 。但特大断面隧道施工遇到衬砌断面由小变大时,在保障施工进度的情况下施工安全是一大难题,需要选择合适的支护结构体。本文以贵安新区浅埋软岩特大断面隧道群项目为工程背景,在小断面变大断面进行开挖时,设计了组合钢模衬砌支护结构,可为类似工程提供参考。
2. 工程概述
腾讯七星数据中心位于贵阳贵安新区金马大道与天府路交叉口西南侧,项目北临天府路、东接金马大道、南靠天玑路,东侧为白马大道。项目隧道土建部分为5条主体隧道(B1-B5) + 1条联络隧道(A1) + 11个立井排风井,是一项复杂的隧道洞库群工程,图1所示。隧道沿栖凤坡山体横向布置B1~B5隧道,隧道中心线线间距为46 m。B1隧道长232.5 m,B2~B5隧道长276.4 m,隧道净宽16.466 m、净高11.7 m,净断面182.4 m2。
隧道埋深0~36 m,地表土层零星分布,基岩出露较好,围岩为主要为三叠系下统安顺组(T^1a)强–中风化白云岩夹泥质白云岩,岩体节理裂隙较发育,呈碎石状松散结构、碎裂状结构,有覆盖层孔隙水和基岩裂隙水,雨季呈淋雨状出水。衬砌除洞口部分为明洞结构外,其余均为复合式衬砌结构。
3. 隧道围岩压力
根据上述工程概况,隧道群施工过程中相邻隧道产生压力叠加,应力集中系数增大,围岩的稳定受到影响。根据朗肯土压力理论,隧道围岩压力分布图2所示。
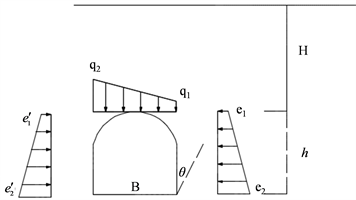
Figure 2. Calculation of surrounding rock pressure calculation of tunnel
图2. 隧道围岩压力计算简图
隧道外侧侧压力系数为λ1
(1)
隧道内侧侧压力系数为λ2
(2)
β为产生最大推力时外侧破裂角
(3)
隧道顶部外侧垂直压力q1和内侧垂直压力q2分别为:
(4)
(5)
式中,IV级围岩中θ = (0.7~0.9) × φ0;D为相邻隧道中间岩柱宽度,m;h为隧道洞高,m;H为隧道埋深,m。
隧道外侧顶部侧压力为e1,腰肢侧压力为e2
(6)
(7)
隧道外侧顶部侧压力为
,腰肢侧压力为
(8)
(9)
隧道岩体力学参数表1所示,根据以上公式,计算了隧道开挖不同埋深围岩压力表2所示。
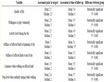
Table 2. Surrounding rock pressure of B1 tunnel excavation
表2. 隧道开挖围岩压力
4. 组合钢模结构设计与施工方法
现场实际施工中,全液压钢模台车以衬砌一般段洞身设计为依据,衬砌内模钢支撑由多节弧形型钢拱架组成。全液压台车由行走机构、台车架、模板纵梁、钢模板、模板垂直升降、侧向伸收机构及液压、电气控制等组成。在隧道扩大段衬砌钢筋绑扎完毕后,台车移动并按一般段衬砌内轮廓进行定位,支撑牢固,进行下一步自行加工衬砌内模钢支撑的架立施工,上部钢支撑与模板台车通过多节型钢拱架连接牢固,钢支撑间设连接筋连接,确认加固牢固后,将小钢模设在钢支撑背面一圈并与钢支撑连接牢固,图3所示。
根据朗肯土压力计算得到了隧道垂直压力、水平压力,考虑结构的稳定性、安全性,设计的组合钢模参数:钢模全长12 m,钢支撑外弧按设计内轮廓缩小2.5 cm,钢模板尺寸(长 × 宽 × 厚)为1.5 m × 0.3 m × 0.05 m,钢支撑与台车之间用型钢拱架焊接牢固。
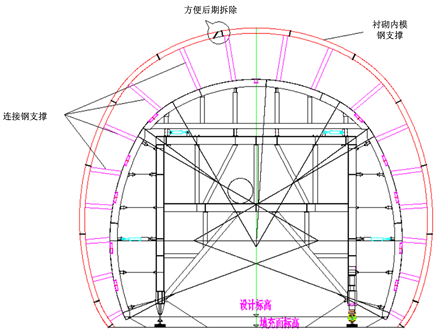
Figure 3. Schematic diagram of working principle of combined steel mold
图3. 组合钢模工作原理示意图
组合钢模台车在隧道混凝土衬砌施工过程中须完成仰拱及填充混凝土的施工作业。组合钢模衬砌段,防水作业台架按本标段一般衬砌段设计台架进行适当加宽、加高,保证安全可靠。待二衬钢筋绑扎完成,开始以下工作:
1) 衬砌内模钢支撑的架立
测量人员对衬砌内模钢支撑进行施工放样,现场利用防水作业台架,由边墙至拱顶顺序左右侧对称安装每一榀钢支撑,钢支撑由多节I25b弧形型钢拱架拼装而成,钢支撑之间通过Ф25纵向连接筋按环向间距1 m焊接牢固。型钢拱架按间距0.75 cm架立,架立、拼装过程中,由于断面较大,需按“架立一层、固定一节”的原则进行分层安装、分层固定,保证施工安全。
2) 台车就位及固定
衬砌内模钢支撑架立、固定完毕后,防水作业台架向前移动,开始进行台车定位工作。台车就位前,检查和清除台车上妨碍操作的障碍物,且每次支模衬砌前,模板工作面必须涂好脱模剂。台车按施工进尺移动就位,按一般段衬砌设计内轮廓进行定位,并支撑牢固。
3) 连接钢支撑作业
一般段台车定位完毕后,开始进行台车与钢支撑之间的钢支撑焊接作业。连接钢支撑按纵向间距0.75 m,环向设置于每榀拱架中间设置,由于台车钢模板由8节1.5 m钢模板组成,因此连接钢支撑正好坐落在模板缝与单节模板中间,达到受力均匀、有效防止模板变形的目的。
4) 钢模板安装
钢模板安装前提前涂刷脱模剂,沿架立完成后的衬砌内模钢支撑外弧安装钢模板,利用混凝土垫块控制钢筋保护层,将其与钢支撑绑扎牢固,确定合格后,进入堵头模板安装、施工缝防水工作。钢模板安装过程中需预留浇筑窗口,其窗口与台车所开窗口对应分布,拱顶设三道混凝土灌注孔及三道注浆孔,与台车灌注口相对应。
5) 混凝土浇筑
隧道衬砌结构采用C35钢筋混凝土,抗渗标号P6,采用分层、左右交替对称浇筑。浇筑时将混凝土送入浇筑工作面,采用平铺法浇筑方式,对混凝土进行平仓振捣,保证混凝土铺料厚度不超过500 mm,并且在混凝土施工中,对进入的混凝土应确保其均衡平整,避免及加大工作量。
在混凝土脱模后,由作业人员清扫模板表面,并涂刷脱模剂,之后进入下一隧道施工循环,直至施工结束。采用组合钢模浇筑二衬混凝土,大大提高了施工功效,节省了大量工期,有效的节约了施工成本。
5. 隧道开挖变形监测
隧道开挖后,围岩的位移是围岩和支护形态变化最直接、最明显的反映,净空的变化(收缩和扩张)是围岩变化最明显的体现。通过周边收敛和拱顶下沉监测,反馈围岩变化信息,及时指导施工,隧道围岩监测点布置图4所示。
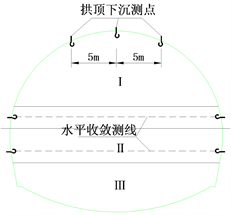
Figure 4. Tunnel deformation measurement point layout
图4. 隧道变形测点布置图
隧道拱顶下沉量、两帮水平移近量实测结果图5、图6所示。隧道开挖后,围岩和支护结构变形总体较小,随开挖时间增加,隧道两帮收敛位移和隧道拱顶沉降位移均呈缓慢增加至趋于平稳的趋势,开挖80天后,变形量基本稳定,其中,水平收敛均在6 mm以内,拱顶下沉在16 mm以内,均小于控制指标(35 mm)。以上监测结果表明隧道设计的初期支护结构是合理的、有效的、安全的,能控制围岩的变形和保证隧道的稳定性。
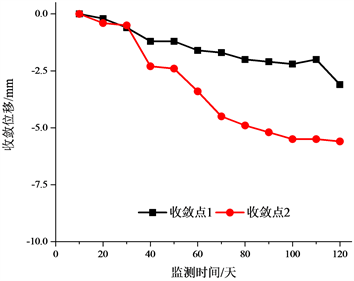
Figure 6. The deformation law of the two tunnels
图6. 隧道两帮变形量规律
6. 结论
1) 利用朗肯土压力理论,结合工程概况,计算了隧道围岩的垂直压力与水平压力,设计了组合钢模衬砌结构参数。
2) 特大断面隧道施工遇到衬砌断面由小变大时,提出了应用钢模台车与自制衬砌内模临时钢支撑相结合的方法,相比洞内组装台车省时省力,能提高施工进度、保证施工安全。
3) 隧道围岩变形监测结果表明,选用组合钢模衬砌作为本次隧道开挖支护的主要技术,对围岩扰动小,施工影响小,工程整体进度快。