1. 引言
在燃油喷射系统中,低压燃油通过高压油泵的压缩进入高压油管,再从喷油嘴处喷出。由于燃油的流入和喷出是间歇性的,这会导致高压油管内压力产生波动,从而使得每次喷出的燃油量都不同,进而影响到发动机的工作效率。
对此我们要对以下问题进行探讨研究,以实现对高压油管的压力控制。
1) 该问题讨论的高压油管其内腔长500 mm,直径10 mm。高压油管左侧有一供油入口A,小孔直径1.4 mm,供油持续的时间长短由单向阀控制,且单向阀每打开一次后需要关闭10 ms。在高压油管右侧有一喷油器每次喷油2.4 ms,工作周期为100 ms,从题目中可以得到喷油器工作时喷油的速率变化图。高压油泵在入口A提供160 MPa的恒定压力,且高压油管内的初始压力为100 MPa。在第一问中,我们需要找到一个合适的单向阀每次的开启时长t,使得高压油管内的压力尽可能稳定在100 MPa左右。而在第二问中,我们需要找到合适的单向阀开启时长使得管内压力分别在经过约2 s、5 s和10 s后从100 MPa增加到150 MPa,并稳定下来。
2) 在系统的运行过程中,高压油管处的燃油来自高压油泵的柱塞腔出口,柱塞腔的内直径5 mm。通过喷油嘴的针阀控制喷油。每次从油泵流入油管的燃油流量受凸轮的控制,题目所给的附件1 [1] 中我们可以得到凸轮边缘曲线与角度的关系,从而得到凸轮的具体形状。当柱塞向上运动时,在泵内的燃油被压缩,泵内压力增大;当泵内的压力高于高压油管内压力时,单向阀就会被打开,燃油就会向油管中流入。当柱塞运动到最高位置时,柱塞腔残余的容积为20 mm3;柱塞运动到最低位置时,泵内充满低压燃油,其压力为0.5 MPa。喷油嘴处针阀直径为2.5 mm,其密封座是半角为9˚的圆锥,且最下端喷孔的直径为1.4 mm。针阀的高度提升,则喷油嘴向外喷油,若针阀高度提升为0,则不向外喷油。一个喷油周期内针阀升程与时间的关系见题目所给的附件2 [1]。在这个问题中我们将找到一个合适的凸轮角速度
,使得高压油管内的压力尽量稳定在100 MPa左右。
3) 在第三个问题中,首先,在题目二的基础上增加一个喷油嘴,对此情况进行分析讨论,找到最合适的供油与喷油方案。其次,在上述基础上,往高压油管左侧增加一个单向减压阀,其直径为1.4 mm,该阀可以在打开后将高压油管的燃油释放到低压管道中。我们将对此状况进行建模分析讨论,给出合适的供油与减压阀控制方案。
本论文所要解决的具体问题,可参见全国大学生数学建模竞赛网站2019年试题 [1]。
2. 问题分析
针对问题一,由题意,我们根据燃油进出高压油管系统的结构特征以及其工作原理,结合题目中注1所给提示,利用密度公式、流体在管道中流动的特性、流量相关公式以及注2所给公式,对包含燃油的压力变化量与密度变化量的公式进行推导整理,最终构建高压油管燃油流通计算模型。当进入高压油管中的燃油流量与喷出的燃油流量相同时,管内的压力能保持稳定状态,由此我们可以借助建立的模型对满足上述条件下的单向阀开启时长进行求解。第二小问,利用MATLAB对高压油管内压力的变化过程进行计算,得到在经过约2 s、5 s和10 s后,管内压力从100 MPa增加到150 MPa,并稳定下来的单向阀开启时长。
针对问题二,利用高压油泵的工作原理,建立类似问题一中模型的高压油泵模型。结合模型一、二,为了使得高压油管内的压力尽量稳定在初始压力,需要让高压油泵向油管输送的燃油量与喷油嘴处喷出的量尽可能相等。喷出量我们可以通过针阀的周期性运动计算得到,输送量与凸轮的角速度有着直接关系,由此我们便可确定满足题目条件的凸轮角速度。
针对问题三,首先增加一个喷油嘴,即增加了燃油的流出流量,这使得原先的供油可能不足以满足需求,结合问题二的分析研究,我们可以通过调整凸轮的角速度增加燃油的输送量。其次再安装一个单向减压阀,它可以使燃油回流到外部低压油路处,从而使得油管内压力减小,即导致燃油的流出量的增加。我们设计了两个方案,一是通过高压油管内的压力,二是设置开启的时机和时长来控制单向减压阀。
3. 模型假设
为了模型建立的方便,我们提出了以下这几条基本假设:
1) 假设在一次喷射过程中燃油的温度不变;
2) 不考虑高压系统中各个零件的形变状况的影响;
3) 忽略压力传导所消耗的时间;
4) 不考虑加工问题导致的泄露;
5) 假设题目所给的数据真实可靠。
4. 符号说明
我们给文中所用符号及其说明,见表1。
5. 模型建立与求解
5.1. 模型一:高压油管燃油流通模型
5.1.1. 模型的准备
根据题意,我们希望建立关于燃油进入和喷出间歇性工作对高压油管内压力造成影响的模型,用以描述高压油管内燃油的流动。通过查阅大量资料 [2],我们发现该题所述系统的工作原理与高压共轨燃油喷射系统的工作原理类似,由此可以将其看做高压共轨燃油喷射系统的简化系统。于是我们以该系统的结构特点和工作原理为基础,建立以下计算模型。
5.1.2. 模型的建立
燃油的压力变化量与密度变化量成正比,其比例系数为
,其中
为燃油的密度,密度与压力有关,E为弹性模量,它与压力的关系可以通过题目所给的附件3 [1] 得到,这部分内容我们将在模型一的后半部分进行分析探讨。
根据相关原理,我们可以得到如下公式:
(1)
通过密度公式
,又由于高压油管在燃油运输过程中是刚性的,我们将密度公式代入公式(1)后得到:
(2)
其中V由高压油管的内半径R与管道内腔长度L决定,表达式为
。
由于流体在管道中流动满足如下公式:
(3)
其中S代表截面面积,
为流体密度,x为流体在管道中流动位移,我们可将公式(2)改写为:
(4)
又因为
,我们可以得到:
(5)
通过流量 = 截面积 × 流体速率,即
,将此代入公式(5)并整理可得到:
(6)
其中Q代表流入高压油管的燃油流量
与流出的燃油流量之差
,即
。
1) 高压油泵向高压油管流入的燃油流量
:
(7)
式中,流量系数
,流通面积
(
为供油入口A处小孔直径),
为高压油泵与油管交界处前后燃油压力差,
为高压侧成燃油密度。
2) 高压油管从喷油嘴流出的燃油流量
:
(8)
式中流量系数
,流通面积
(
为喷口B处小孔直径),
为高压油管与喷油嘴交界处前后燃油压力差,
为高压侧成燃油密度。
综上所述,我们可以得到高压油管燃油流通模型:
(9)
通过查阅相关文献 [3],我们发现弹性模量E与压力P有关,故上述公式(9)可记为:
(10)
5.1.3. 问题一:单向阀每次开启时长的求解
通过公式(9)我们可以发现,在高压油管内压力保持不变的情况下,即
时,可以得到
,即
。由此需要单向阀每次开启的时长应满足流入管道内的燃油流量与流出的燃油流量相等,从而使得长期工作也能保持管道内压力不变。
由题目中给出的喷油速率-时间图像,我们可以计算得到高压油管从喷油嘴流出的燃油流量
为:
(11)
其中
为喷油器每秒工作次数。由此计算得到
,它表示一秒内喷油嘴喷出的燃油流量。
而高压油泵向高压油管流入的燃油流量
,根据公式(7)并将具体数值代入,我们可以得到:
(12)
正常情况下,燃油密度
跟随压力变化的关系式 [4] 为:
(13)
其中
表示在压力为100 MPa时燃油的密度,
。将
代入,即可得到此时
。将此结果代入公式(12),即可得到流入的燃油流量
,它表示在单向阀开启时间下,每毫秒(ms)喷出的燃油流量,由于需要
,且单位相同,我们可以得出
,表示每秒钟喷出的燃油流量与进入的流量相同,n表示一秒内开启单向阀次数,t表示每次开启单向阀时间。再与
进行联立,最终计算得到单向阀每次开启的时长约为0.302 ms。
5.1.4. 问题一:调整单向阀开启时长
问题一的第二小问是通过调整单向阀每次开启的时长,使得高压油管内的压力在分别经过约2 s、5 s和10 s后稳定在150 MPa。我们采用MATLAB迭代的方式,模拟出高压油管中的压力从100 MPa到150 MPa直至稳定的过程。根据问题要求,分别在2 s、5 s、10 s内完成该过程,并求出不同时间要求下单向阀开启的时间。下面我们以2 s为例,对该问题进行求解。
在第一小问中我们已经求得当单向阀开启时间约为0.302 ms时,此时高压油管内的压力几乎处于稳定状态,即管内压力稳定在100 MPa左右。因此我们将单向阀开启时间约束在0.3~1.2 ms范围内,并以0.001 ms为步长,观察不同的时长对管内压力的影响,求得既满足在2 s内完成高压油管内压力从100 MPa增加到150 MPa并稳定在150 MPa,又满足单向阀开启时间最短的阀开启时间t。其次,我们以0.1 ms为步长设置0~12,000 ms的循环来表示时间的推移,记为T。在MATLAB中设置矩阵
用于存储不同阀值不同时刻下燃油的压力。根据前文公式(6)得到燃油压力的计算公式为:
(14)
其中E为弹性模量,V为高压油管体积,
为流入高压油管的燃油流量,
为流出的燃油流量,
为前一时刻燃油压力。
1) 弹性模量E
我们通过对题目所给的附件3 [1] 中弹性模量与压力的数值进行曲线拟合,得到弹性模量与压力的关系式:
(15)
下图图1为我们利用题目所给的附件3 [1] 中的数据对压力和弹性模量数值进行拟合的曲线图,其中横轴为压力(MPa),纵轴为弹性模量(MPa),黑色散点是对题目所给的附件3 [1] 中时数据描点,红色细线为我们拟合的曲线。拟合代码见附录1,并且我们对结果进行了残差分析,结果越接近1说明拟合程度越好,我们得到的结果为0.999998,因此在下文中需要计算弹性模量时,我们将运用此拟合方程计算。
(16)
2) 流入高压油管的燃油流量
:
(17)
其中
为前一时刻燃油压力,
为前一时刻压力下燃油密度,其计算公式见公式(13)。
3) 高压油管流出的燃油流量
:
计算
时我们需要判断当前时间喷油器是否开启或是处于开启时的什么状态。喷油器每秒工作10次,每次工作时喷油时间为2.4 ms,由此将100 ms记为一个工作周期,根据题目中所给的喷油速率示意图,我们通过对T除以100的余数(记为rem)跟图示时间进行比较,取该时刻下与前一时刻时的燃油流量的均值,即
作为最终所要求的
,整理化简后我们得到如下公式:
(18)
综上所述,利用公式(14)~(18)可求得不同阀值不同时刻下燃油的压力P在矩阵
中记录下来。
同理在经过约5 s和10 s的计算方法与以上相同,完整的MATLAB程序代码见附录2,由此我们得到分别经过约2 s、5 s和10 s后高压油管内压力从100 MPa增加到150 MPa并稳定时,单向阀开启时长的设置,结果如下表2所示:
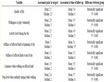
Table 2. Opening time of one-way valve
表2. 单向阀开启时长
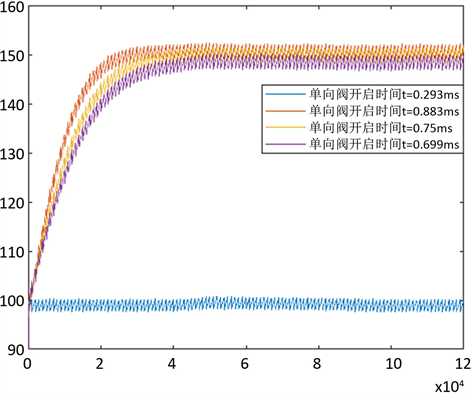
Figure 2. Schematic diagram of pressure variation with time for different opening time of one-way valve
图2. 单向阀不同开启时长压力随时间变化示意图
上图2是我们利用MATLAB迭代对高压油管内压力进行仿真模拟,得到满足问题一第二小问要求的不同单向阀开启时长下,高压油管内压力随时间变化的示意图,其中横轴表示时间(ms),纵轴表示压力(MPa)。橙色线表示经过约2 s时间达到要求的单向阀开启时长,黄色线表示经过约5 s,紫色线表示经过约10 s的情形。从图中我们可以发现刚开始时,高压油管内的压力上升幅度很大,很快就到达150 MPa附近,之后逐渐向150 MPa逼近,最后围绕150 MPa上下波动,即高压油管压力值在合理的范围内波动,表明燃油喷射的稳定性。
5.2. 模型二:高压油泵运作模型
5.2.1. 模型的准备
1) 凸轮
通过查阅题目所给的附件1 [1] 中凸轮边缘曲线与角度的关系,利用题目所给的附件1 [1] 中的数据,可以绘出凸轮的边缘曲线图,见图3。
该凸轮对柱塞位置h的影响可以记为
,又因为
,所以h是一个关于
和t的函数,并呈现出周期性的性质,其周期
。
根据题目中的描述以及查阅关于高温油泵的资料 [5],我们描绘出了高压油泵的简单示意图,见图4。
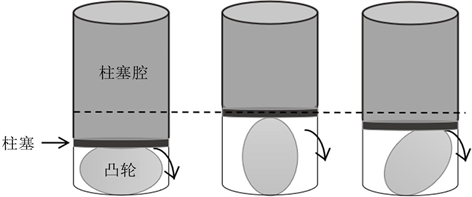
Figure 4. Simple schematic diagram of high pressure oil pump
图4. 高压油泵简单示意图
由上图4可以分析出高压油泵的工作原理:随着凸轮的旋转,柱塞上下起伏,从而对上方的柱塞腔内燃油进行压缩,增大压力直至高压油泵内燃油压力大于高压油管内的燃油压力,打开单向阀,将高压油泵中的燃油输入到高压油管中。
2) 针阀
由题意,我们绘制出针阀的运作图像:
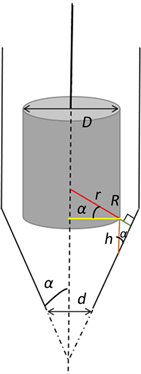
Figure 5. Operation diagram of needle valve
图5. 针阀的运作图
上图5中,D代表针阀的直径,d代表最下端喷口的直径,
为密封座圆锥的半角,h为针阀距最下端喷口的距离,在图中用棕色线条表示。其中燃油流通面积S可以表示为
,
表示大圆锥的侧面积,
表示小圆锥的侧面积。
圆锥侧面积计算公式为
,R为圆锥半径,L为圆锥底面周长。
(19)
通过上述公式,我们可以表示出燃油的流通面积S:
(20)
5.2.2. 模型的建立
假设柱塞与凸轮的强度和刚性足够大且没有变形,在运动过程中没有冲击震动的现象,根据高压油泵的原理,我们可以建立了类似模型一的高压油泵模型:
(21)
其中
代表高压油泵压入柱塞腔中的流量,
代表油泵向油管输出的燃油流量。
1) 压入高压油泵的燃油流量
:
通过题目我们可以发现当柱塞处于下止位点时,柱塞腔内充满了低压燃油,且压力为0.5 MPa,随着凸轮的运作,柱塞向上运动时,低压燃油被迅速压缩,柱塞腔内压力增大,在这个过程中进入的燃油量可以用公式
表示,其中S代表柱塞的底面积,利用公式
得到,v可以通过
计算得到,即
(22)
其中
为柱塞的直径,即柱塞腔内直径,h为柱塞距离高压油泵最低位置的高度。
2) 流入高压油管的燃油流量
:
当柱塞向上挤压柱塞腔内的燃油时,柱塞腔容积减小,燃油的压力增加。当高压油泵内的燃油压力
大于高压油管内的燃油压力
的时候,位于这两个组件中间的单向阀将会开启,会有部分燃油被从压力较高的高压油泵处推入高压油管中,这部分的燃油流量记为
,在这个过程当中流向高压油管的流量可以通过注2中的公式
来计算,故有:
(23)
其中A为小孔的截面面积,
代表高压油泵区域的燃油压力,
代表高压油管区域的燃油压力。
将模型一、二结合起来,以
作为两个模型间的桥梁,其中
为这一时刻压入高压油泵的燃油流量,
为前一时刻流入高压油管的燃油流量,这就将高压油泵与高压油管联系起来,使其成为一个整体性的模型:
(24)
其中
为前后两个时刻下压入高压油泵的燃油流量,
为前后两个时刻流入高压油管的燃油流量,
为喷油嘴外的压力。
5.2.3. 问题二:确定凸轮的角速度
根据题意我们知道凸轮控制柱塞的上下运动。柱塞向上运动时柱塞腔容积减少,高压油泵内压强增大,当高压油泵内压强高于高压油管内压强时(高压油管内压力初始值100 MPa),开启单向阀,向高压油管中输入燃油;柱塞向下运动时柱塞腔容积增大,从外部吸入0.5 MPa的低压燃油,当柱塞达到下止点时柱塞腔内充满0.5 MPa的低压燃油。当凸轮角速度增大时,单位时间内凸轮带动柱塞上下运动的频率上升,由于单位时间内单向阀开启的时间与柱塞上下运动的频率呈正相关,这使得单位时间内从高压油泵流到油管中得燃油流量增加。又由于喷油嘴B处的开启与关闭呈现周期性变化,因此单位时间内喷油嘴B处的燃油流量基本处于定值。
根据公式
,存在一个凸轮角速度
,使得单位时间内,开启单向阀时,高压油泵向高压油管输入的燃油流量与喷油嘴B处喷出的燃油流量几乎相等,使得高压油管内压强基本稳定在100 MPa。
由此对于问题二的求解,我们以上面的模型为基础,在MATLAB中进行迭代,计算得到能够使管道压力
稳定在100 MPa周围的角速度
。下图为不同角速度下,油管内压力随时间的变化图。
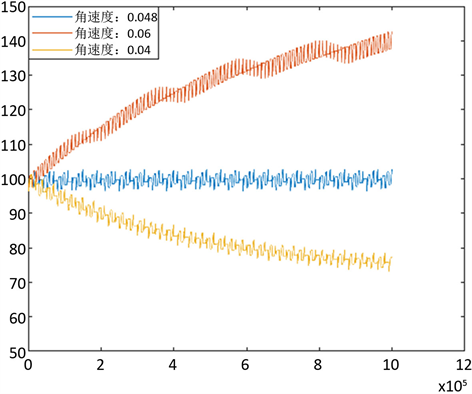
Figure 6. Different cam angular velocity pressure changes with time
图6. 不同凸轮角速度压力随时间的变化
上图6中,横轴为时间推移,纵轴为高压油管内压力变化。根据上图我们可以发现:
当凸轮角速度小于
时,高压油泵向高压油管输入的燃油流量小于喷油嘴B处放出的燃油流量,高压油管内压力处于逐渐降低的状态。
当凸齿轮角速度大于
时,高压油泵向高压油管输入的燃油流量大于喷油嘴B处放出的燃油流量,高压油管内压强处于逐渐升高的状态。
5.3. 模型三:双喷口高压燃油喷射系统模型
5.3.1. 问题三:增加一个喷油嘴后,喷油和供油策略的调整
在问题三中,我们对模型一进行改进,使其拥有两个喷射口。
(25)
其中
代表从高压油泵模型中流入的燃油流量,
代表从喷射器1流出的燃油流量,
代表从喷射器2流出的燃油流量。
1) 双喷油嘴同时运作
我们先使两个喷油嘴在同一时刻运作,得到的结果如下:
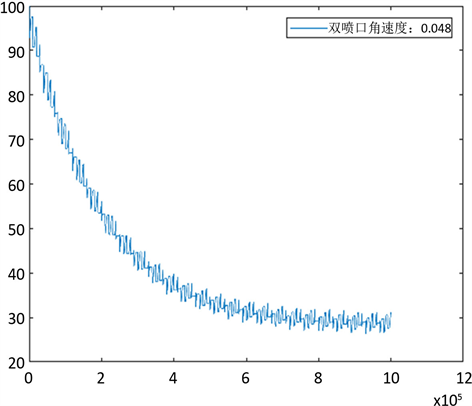
Figure 7. Image of pressure in the tubing changing with time when two injectors work together
图7. 两个喷油嘴共同工作时油管内压力随时间变化图像
上图7横轴表示时间从0~10 s,纵轴表示高压油管内的压力。从图中我们发现由于增加了一个喷油嘴,喷油流量超过了供油流量,导致高压油管内的压力随时间逐渐下降,为了保持压力稳定,我们需要对高压油泵的供油流量进行调整。
通过问题二的求解过程,我们知道随着凸轮角速度
的增大,高压油泵系统中的
也会随之增大,从而导致高压油泵与高压油管之间的压力差增大,进一步增大高压油管部分的流入燃油流量
。所以为了增大
,我们利用MATLAB对凸轮角速度
进行了调整,找到了一个能够使高压油管区域的压力P数值随时间在100 MPa周围波动的新的凸轮角速度
。
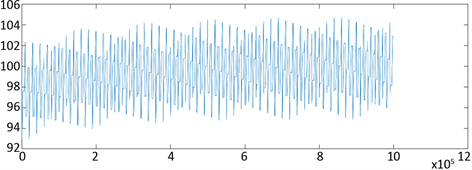
Figure 8. When
Image of pressure in the tube as a function of time
图8.
时管内压力随时间的变化图像
从图8中可以发现当
为0.096 rad/ms时,油管内压力围绕100 MPa上下波动。
接下来为了衡量管内压力的波动程度,我们计算了方差
的大小,其中方差越大代表波动程度越大,其公式如下:
(26)
当
等于0.096 rad/ms且两个喷油嘴同时运作时,其方差为5.6896 × 106。
2) 两个喷油嘴邻接运作
第一个喷油嘴运行结束后,第二个喷油嘴紧接着开始运作的状况下,管内压力变化如图所示:
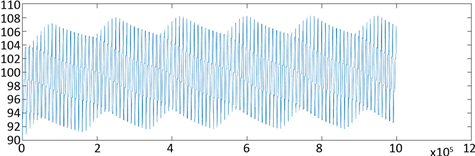
Figure 9. Image of pressure change in time two injector nozzles adjacency operating in the oil pipe
图9. 两个喷油嘴邻接运作油管内压力随时间变化图像
从图9中我们可以发现,此运作状态下油管内压力也围绕100 MPa上下波动,这种状况下的
等于0.192 rad/ms,其方差为1.6890 × 107。由此可以发现邻接工作时的方差大于同时运作时的方差,即邻接工作时管内压力的波动程度更大,说明这种方式劣于同时运作。
两个喷油嘴均匀运作
由题目所给的附件2 [1] 可得第一个喷油嘴工作时长为2.45 ms且在100 ms之内只工作一次,所以我们将这100 ms均分为两个部分,第一个喷油嘴于[0, 2.45] ms期间工作,第二个喷油嘴于[50, 52.45] ms期间工作。由此得到的结果如下图所示:
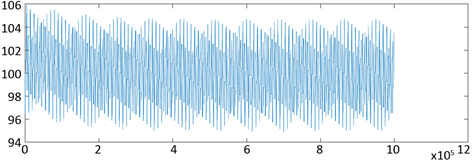
Figure 10. Two injectors evenly operate the pressure inside the tubing as a function of time
图10. 两个喷油嘴均匀运作油管内压力随时间变化图像
从图10中我们可以发现,此运作状态下油管内压力也围绕100 MPa上下波动,这种状况下的
等于0.192 rad/ms,其方差为4.9560 × 106。由此可以发现均匀工作时的方差小于同时运作时的方差,即均匀工作时管内压力的波动程度更小,说明这种方式优于同时运作。
综上所述,通过测试不同的喷油嘴工作方案,我们发现当两个喷油嘴均匀工作时的方差最小,且这种方案下的凸轮角速度为0.192 rad/ms。
5.3.2. 问题三:双喷口带单向减压阀的高压燃油喷射系统
通过查阅文献 [6],我们了解到单向减压阀由单向阀与减压阀并联而成的组件,是一种用于降低流体压力。在这个问题里,我们将对之前建立的模型进行再次改进,在其中加入单向减压阀导致的燃油流出
,即将公式(23)改写为:
(27)
其中新加入的变量
可以表示为如下形式:
(28)
其中
。
基于上述模型改进,我们可以找到减压阀的两种控制方案:
方案一:由时间t决定是否开启单向减压阀;
方案二:由高压油管内的压力
决定是否开启单向减压阀。
接下来我们将分别对这两种状况利用MATLAB进行迭代计算,通过调整对应的约束条件观察两种控制方案是否能够有效地使管内压力保持稳定,并计算出满足这个条件的情况下的供油状况。
1) 方案一:由时间t决定是否开启单向减压阀
在方案一中我们控制单向减压阀的条件为开启时长与开启时间间隔。利用MATLAB计算在不同开启时长和开启时间间隔情况下凸轮角速度
和方差
的值,发现当结果满足管内压力围绕100 MPa上下波动时,其方差远远大于不开启单向减压阀时的方差。
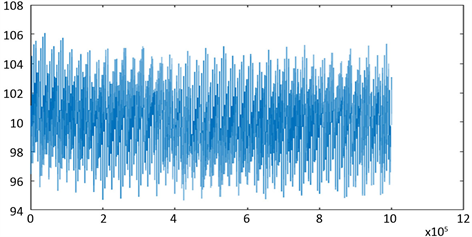
Figure 11. When scheme 1 the image of the pressure in the tube changes with time
图11. 方案一时管内压力随时间变化图像
从图11中我们可以观察到方案一时压力波动十分剧烈,所以我们认为方案一的效果并不好。
2) 方案二:由高压油管内的压力
决定是否开启单向减压阀
该方案中,我们将设置通过不断改变单向减压阀开关条件,来观察高压油管内压力
的图像变化。当管内压力与低压燃油的压力差,即与单向减压阀出口内外压力差大于某个阈值时开启该减压阀。
(29)
其中
为我们设定的压力差阈值。利用MATLAB计算得到能使方差最小的结果如图所示:
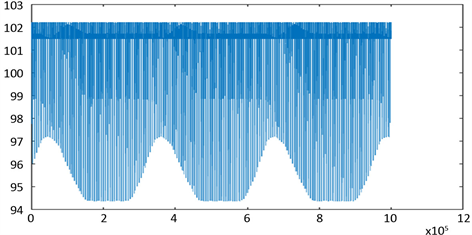
Figure 12. When scheme 2 the pressure inside the tube changes with time
图12. 方案二时管内压力随时间变化图像
根据图12我们可以发现管内的压力上涨被减压阀严格控制,在该方案下的凸轮角速度为0.63 rad/ms,其方差为3.8973 × 106。
综上所述,针对该问我们最终确定的供油方案为凸轮角速度
,单向减压阀控制方案为当管内与低压油管压力差大于101 MPa时,开启单向减压阀。
6. 模型的评价与改进
6.1. 模型的优点
1) 本文在模型的建立过程中,用到了密度方程、燃油流动的方程以及系统零件的运动方程等,为仿真提供了理论依据。
2) 本文通过对系统结构和工作原理的分析,清楚系统的整个物理过程,建立了系统的详细数学模型,在此基础上,利用MATLAB编写计算仿真的模型。
6.2. 模型的缺点
1) 本文在利用MATLAB模拟仿真时,对高压油泵、高压油管、喷油器等仿真模型都做了一些简化,会导致仿真结果有所误差,同时模拟仿真时内部也会出现系统的误差。
2) 本文在研究过程中,忽略了燃油发热等造成的系统内部温度变化对整个系统的影响,对模型的计算结果可能会造成一定的影响。
6.3. 模型的改进
此文中在模型建立过程中并没有考虑温度的变化造成的影响,可以加入燃油的热效应对系统的影响,对模型的个别参数进行一定的修正。本文研究的整个系统其实是一项涉及多领域的复杂而系统的工作,在建模中应尽量全面的考虑影响该系统的因素,对整个数学模型进行细化研究,提高系统计算的准确性。
基金项目
浙江省自然科学基金(LQ18A010007),国家自然科学基金(11901145)。