1. 引言
帘线钢是超洁净钢的代表产品,它具有弹性好、强度高、抗冲击等优异的力学性能且使用寿命长 [1] [2]。帘线钢在拉拔成丝后,直径一般为0.15~0.38 mm,因此在生产中对冶炼、轧制、加工等每个环节都有特殊的要求,特别是对钢中夹杂物的大小、形状和可变形性的要求非常严格。所以帘线钢被誉为“线材中的极品”、“线材皇冠上的明珠” [3]。一般来说,钢帘线拉得越细,生产难度越大。最小线径是衡量帘线钢生产技术水平的重要标准。目前我国帘线钢大多能拉到Φ0.22 mm左右,武钢、兴澄特钢等少数几家试拉成功Φ0.175 mm。欧洲、巴西等一些钢厂可以拉到Φ0.15 mm,而日本神户则可以拉到Φ0.08 mm以下 [4]。拉成如此细丝,任何稍大尺寸的硬性夹杂、偏析、非常规组织、内部及表面缺陷都可能是致命的,都可能造成断丝,可见生产难度之高 [5]。因此,为了拉出强度更高、线径更细的帘线钢丝,需严格控制帘线钢的各个生产环节。本文从帘线钢的生产工艺过程及钢帘线的铅浴淬火,水浴淬火和电镀工艺的最新研究进展进行综述。
2. 钢帘线的拉丝过程
典型的钢帘线生产工艺如图1所示,大部分钢帘线厂家都是使用Φ5.5 mm通过控冷技术得到具有索氏体组织的钢帘线盘条。检验合格后,先对盘条进行表面处理,初拉至Φ2.2~3.2 mm,加热奥氏体化,然后进行铅浴淬火处理;再中拉至Φ0.8~1.6 mm,进行二次铅浴或者流化床等温淬火,镀铜、镀锌,从而达到满足要求的力学性能、金相组织和镀层质量;在最终的湿式拔丝中进行600~1000 m/min的高速拔丝,拉拔至Φ0.15~0.38 mm,再进一步通过对超细丝施加强烈的扭转应力使之形成帘线,经矫直后送检 [6]。
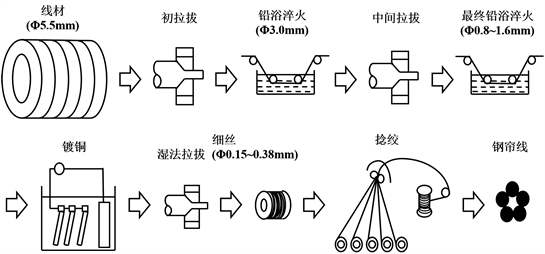
Figure 1. Production process of steel cord [6]
图1. 钢帘线的生产工艺 [6]
帘线钢的生产工艺,总的分为两种冶炼流程:(1) 高炉→铁水预处理→转炉冶炼→精炼(一次或多次)→连铸;(2) 电炉→精炼(一次或多次)→连铸或模铸。国内外各帘线钢生产厂家的大致的工艺流程如表1所示。
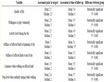
Table 1. Technological process of cord steel manufacturers at home and abroad [7]
表1. 国内外帘线钢生产厂家的工艺流程 [7]
3. 盘条的处理
拉拔前要对盘条进行预处理,使其符合拉拔的条件,降低拉拔中的阻力。盘条在拉拔前要将表面产生的氧化皮及在储存过程中表面产生的杂质清除干净,机械法和化学法是清除盘条表面氧化皮和其它杂质的两种主要方法。
机械法:对盘条的氧化皮施加外力使其疏松、破裂、剥落。可借助剥壳机、抛光机、喷砂机和钢丝刷等工具进行清理,常用剥壳机将盘条反复弯曲而使氧化皮剥落。化学法:利用氧化皮与化学溶剂发生反应而使其从盘条上剥落并在溶剂中溶解,常采用酸洗法。为使盘条表面杂质清除干净,机械法和化学法一般同时使用。为增加拉拔时的润滑作用,拉拔前盘条还要进行干燥、涂硼处理 [8]。
4. 淬火热处理
热处理可以调节盘条或半成品的物理性能,可分为中间热处理和最终热处理。中间热处理可以消除钢丝在拉拔时产生的加工硬化,恢复其塑性以满足使用要求;最终热处理可以使钢丝获得均匀的索氏体组织,其组织具有很高的抗拉强度,减少了钢帘线在生产过程中的断丝现象,现在钢丝的中间热处理和最终热处理均采用淬火方式。钢帘线的淬火方式主要有铅浴淬火、水浴淬火和流化床淬火,钢丝等温铅浴淬火最为普遍 [9]。柳州钢铁集团和广西大学合作,提出了热处理加热过程数学模型,通过计算机技术,实现加热过程的自动控制。
4.1. 铅浴淬火
4.1.1. 铅浴淬火工作原理
帘线钢丝的铅浴淬火如图2所示,原理是根据钢的等温转变C曲线,让过冷奥氏体在600℃左右的铅液中进行等温转变,产生适合深度拉拔的索氏体组织。因铅液具有高热容、高导热率、流动性好、化学性能稳定、耐腐蚀、耐热冲击等特性,所以钢丝的等温转变过程比较容易实现 [10]。

Figure 2. Schematic diagram of lead bath quenching of steel wire [11]
图2. 钢丝铅浴淬火示意图 [11]
铅浴淬火热处理生产线的工艺流程:放线→铅淬火→水洗→酸洗→水洗→磷化→清洗→涂硼砂→烘干→收线 [12]。
4.1.2. 铅浴淬火工艺参数
钢丝铅浴淬火的工艺参数主要有:钢丝的加热温度、铅浴温度和走线速度。连续展开式铅浴热处理的走线速度,由钢丝的在炉时间和铅浴时间决定 [13]。
1) 钢丝在炉加热温度及在炉时间的控制
按照Fe-C相图钢丝奥氏体化加热温度一般为Ac3以上30℃~50℃ [14],但在连续奥氏体化过程中,加热温度在Ac3以上100℃~200℃。因较高的温度可以使钢丝在短时间内达到奥氏体均匀化,在索氏体转变区得到粗晶粒、均匀的索氏体组织。此外,较高温度可以避免或减少钢丝在奥氏体化后析出先共析铁素体 [15]。但钢丝加热温度过高会使钢丝表面氧化严重、增加能耗和金属烧损、铅浴时易使钢丝表面挂铅、钢丝产生脱碳等缺陷。
钢丝连续奥氏体化过程中,铁素体会发生相变转变成奥氏体,转变的孕育期由加热温度和加热速度共同决定。加热温度越高,加热速度越快,转变的孕育期越短,转变所需的时间也越短。为确保奥氏体完全均匀化,现场的明火炉通常采用高温快速加热的方式 [16]。
高温快速加热,奥氏体晶粒成核速度大于成长速度,从而可以细化晶粒、保证钢丝的充分奥氏体化。但若钢丝的温度过高会使奥氏体晶粒粗化,在铅浴过程中易形成魏体组织,使钢丝强度降低,脆性增大 [17]。所以,一般将钢丝在炉加热温度控制在900℃~950℃ [18]。
钢丝加热温度计算的经验公式常见以下两种 [19] :
(1)
(2)
式中TD:钢丝的加热温度(℃),C:钢丝的含碳量(%),D:钢丝直径(mm)。
此外,达到相同的温度,粗钢丝比细钢丝所吸收的热量更多,可以通过延长加热时间来确保粗钢丝完全热透和奥氏体均匀化 [20]。
2) 铅浴温度及铅浴时间的控制
从加热炉出来进入铅槽冷却,钢丝发生奥氏体分解,铅浴温度的选择决定了钢丝经铅浴后是否获得均匀索氏体。铅浴温度与钢丝的含碳量、化学成分及钢丝直径有关。钢丝等温铅浴淬火过程中,过冷度决定了奥氏体转变后的组织。过冷度太小,易产生条块状或网状铁素体组织;过冷度太大,易产生贝氏体或马氏体组织 [21]。
按照TTT曲线为获得均匀索氏体组织,钢丝的铅浴温度为600℃~650℃ [22]。但因在奥氏体化时钢丝的加热比较充分,铅浴温度由线温和明火炉的DV值决定,考虑到相变时温度回复,通常将铅浴温度控制在550℃左右。
计算铅浴温度的经验公式如下 [19] :
(3)
式中TB:铅浴温度(℃),D:钢丝直径(mm),C:钢丝的含碳量(%)。
实际生产中应减少铅浴温度,因高温钢丝不断从加热炉进入铅槽,带入很多热量,铅槽内尤其在进口处温度升高,使冷却速度降低。钢丝铅浴时间必须大于奥氏体分解需要的时间,否则奥氏体等温转变不完全。钢丝中剩余的过冷奥氏体离开铅槽以后,在低温时转变成马氏体,严重影响成品钢丝的质量 [23]。
于同仁等人 [24] 发明一种1960 MPa级海洋工程用镀锌钢丝绳及其生产方法。其生产方法为:采用电炉冶炼→LF + RH真空精炼→大圆坯连铸→加热→初轧开坯→连轧→轧制方坯→探伤、修磨→高线加热炉加热→控轧控冷→减定径机→吐丝机→盘条成品→铅浴淬火→拉拔钢丝→热镀锌→生产钢丝绳→包装入库。与现有技术相比,其采用优化的控轧控冷轧制工艺,避免出现网状渗碳体和马氏体,可得到索氏体化率90%以上的金相组织。
4.1.3. 铅浴淬火的缺点
虽然铅浴淬火在很多企业都广泛应用,但这种热处理方式能耗较高,会产生对人体和环境有害的铅尘,再加上全球范围内实行“禁铅”运动,铅浴淬火工艺终将会被淘汰 [25] [26]。为防止铅浴淬火被取消后影响到钢丝的质量,金属制品行业开始寻找既节能环保又高效稳定的淬火方式 [27]。
4.2. 水浴淬火
4.2.1. 水浴淬火工作原理
帘线钢丝的水浴淬火如图3所示,钢丝在炉加热后内部组织转变成奥氏体组织,随后进入水浴淬火液中。钢丝冷却发生放热现象,高温使水汽化在钢丝表面形成蒸汽膜,钢丝在蒸汽膜中继续冷却 [28]。进入核沸腾阶段时,钢丝的冷却速度太快,容易产生马氏体组织,为了降低钢丝的冷速,在水浴中加一些高分子化合物,增大水和蒸汽表面张力,缩短蒸汽膜破裂时间。水浴淬火除了能够满足各种钢丝的生产工艺要求,还具有无污染无飞溅,对工人的伤害较小,设备的投资成本低,维护相对简单等优点 [29]。
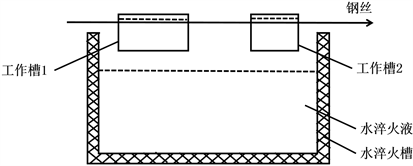
Figure 3. Schematic diagram of steel wire water bath quenching [11]
图3. 钢丝水浴淬火示意图 [11]
4.2.2. 水浴淬火工艺控制
采用双段式水浴淬火对帘线钢丝进行淬火热处理,双段式水浴由工作槽1、空气段和工作槽2组成。水浴淬火时,通过调节这三个工作段的长度来控制水浴淬火工艺过程。钢丝在炉加热后进入工作槽1中冷却,此时的组织是过冷奥氏体;随后钢丝在空气段中开始发生索氏体转变,因相变过程中会放出较多的热量,导致我们看到的钢丝呈现升温后的红色;当钢丝进入工作槽2中时索氏体化充分进行,从工作槽2出来后钢丝索氏体化转变结束。钢丝的冷却曲线如图4所示。因调节工作槽2的长度很难对钢丝索氏体化进行控制,所以我们一般只调节工作槽1和空气段的长度来达到钢丝所需的力学性能 [29]。
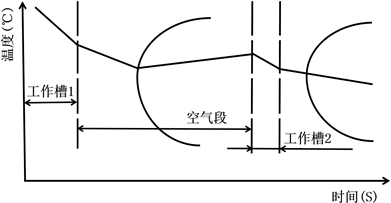
Figure 4. Water bath quenching cooling curve of steel wire [11]
图4. 钢丝水浴淬火冷却曲线 [11]
陈红献等人 [30] 发明一种钢丝感应加热水浴淬火热处理工艺。该工艺是将钢丝从工字轮放线机引出、并经定位装置水平输出后,经过中频感应加热器和超音频感应加热器进行两级感应加热,接着进入保温炉保温、并充分奥氏体化,随后再经过在水浴槽中快速冷却以完成钢丝索氏体组织的转变,接着再经空气自然冷却和水冷槽冷却回归常温状态,最后在牵引机的带动下钢丝被收卷至工字轮收线机的卷筒上。此工艺可获得高性能的索氏体组织,提高钢丝的综合机械性能。
4.2.3. 水浴淬火的缺点
水浴淬火是一种不等温不连续的淬火工艺。一般情况下,若钢丝和水直接接触冷却,将会得到马氏体组织。要确保钢丝在水浴中平稳运行,不能在水浴中停留时间太长,否则会造成钢丝的脆性断裂。水浴淬火有较多的缺陷,例如不同钢丝需要配置不同浓度的溶液,溶液中的有机物易老化,工艺的稳定性差,不易控制 [21]。
5. 电镀工艺
镀铜除了防腐和装饰之外,还具有提高钢丝的导电性能、增加钢丝进一步拉拔时的润滑性能、增加钢丝和橡胶的结合强度等功能。
国内钢丝镀铜有化学镀和电镀两种工艺方法。化学镀设备简单,但镀层结合强度较差,形成的镀层厚度较薄,不允许对镀铜后的钢丝进一步拉拔。电镀铜质量较高,镀层和钢丝之间结合紧密,可控制镀层所需的厚度,适用于镀铜后钢丝还需进一步拉拔的场合 [31]。
钢丝电镀大多采用对环境影响较小的无氰镀铜工艺。无氰镀铜采用预镀–正镀两步镀铜工艺,先使用一种电镀铜工艺进行预镀以确保镀层和钢丝之间结合紧密。但预镀工艺的电流范围较为狭窄,沉积速度慢,普通零件采用延长电镀时间来增加镀层厚度,但由于钢丝需要在高速下进行电镀,施镀时间仅有几十秒钟,为在短时间内沉积出较厚的铜层,一般正镀采用沉积速度较快的硫酸盐镀铜工艺 [31]。
5.1. 工艺流程
钢丝拉拔分为干式拉丝和湿式拉丝,初拉和中拉采用干式拉丝,细拉采用湿式拉丝,且润滑条件好,总压缩率大,钢丝拉拔后具有一定的镀层厚度。现场镀敷工艺采取先镀铜、后镀锌,经热扩散得到铜锌合金。热扩散后镀铜钢丝还要在磷酸溶液中进行磷化处理,以去除微量氧化锌并形成磷化膜,磷化膜具有微孔结构和良好的延展性,有利于随后的湿拉。钢丝镀敷层可以达到防腐和提高附着力的目的,最后通过合股成绳,把湿拉后的单丝捻制成各种结构的钢帘线 [32] [33]。
经冷拉拔形成的钢丝会产生加工硬化现象,需要进行铅浴淬火处理,使其弹性达到使用要求 [34]。
5.1.1. 酸洗
铅浴淬火处理后,钢丝表面的有机物会被高温碳化。残留在钢丝表面的碳化物及氧化层会影响镀层与钢丝进一步的结合,酸洗可以确保干净的钢丝进入镀铜流程,沉积出结合紧密的镀层。常用的电解酸洗液配方及工艺参数:H2SO4:150~200 mL/L,若丁:1~2 g/L,阴极电流密度:8~10 A/dm2,时间:3~5 s,线速度20~30 m/min [35]。
5.1.2. 碱性预镀铜
在酸性镀铜前,钢丝先在碱性焦磷酸铜镀液中沉积一层薄铜,来加强钢丝和酸性镀层间的结合力。焦铜液中含有较多的柠檬酸铵及少量的氨水,具有改善镀液分散、促进阳极溶解、加强镀液缓冲、提高镀层光亮度的作用,还具有阻止铜离子在钢丝表面上产生置换反应的能力。常用的焦磷酸盐镀铜液配方及工艺参数:Cu2P2O7:80~90 g/L,K4P2O7:320~380 g/L,(NH4)2HC6H5O7:20~25 g/L,NH4OH:2~3 mL/L,PH值:8.2~8.8,温度:30℃~50℃,阴极电流密度:5~10 A/dm2,线速度20~30 m/min,沉积速度10~15 m/min [36]。
5.1.3. 酸性正镀铜
钢丝经预镀铜后,需要进入酸性镀铜液中加厚沉积。钢丝在酸性镀铜液中,其阴极电流密度远远高于普通镀铜用的电流密度,镀液温度也随之升高。但镀层在较高的温度会产生结构疏松,镀层粗糙等后果,因此仍需将镀液温度控制在38℃~40℃。常用的硫酸盐镀铜液配方及工艺参数:CuSO4·5H2O:170~200 g/L,H2SO4:25~30 mL/L,温度:25℃~50℃,阴极电流密度:30~45 A/dm2,线速度20~30 m/min,沉积速度60~70 m/min [37]。
田栋等人 [38] 发明一种钢帘线无氰亚铜电镀黄铜及黄铜镀层的钝化方法。此方法有效解决目前钢帘线无氰电镀黄铜时镀层成分难以控制、结合力差、耐蚀性差的技术问题。钢帘线无氰亚铜电镀黄铜步骤:(1) 无氰亚铜电镀黄铜溶液的配制;(2) 钢帘线前处理;(3) 钢帘线无氰亚铜电镀黄铜。电镀后,可获到成分稳定、结合力良好的黄铜镀层。黄铜镀层的钝化方法:将镀有黄铜镀层的钢帘线浸入钝化溶液中化学钝化即可。此方法可降低钢帘线的生产成本,用于钢帘线的大规模工业生产。
6. 结语
进入21世纪以后,中国的帘线钢市场发展迅速,对子午线轮胎用的帘线钢线材需求不断增大。但由于帘线钢具有极高的技术工艺难度,对帘线钢的各个生产环节质量要求严格,因此国内能够大批量生产品种多、质量高的帘线钢企业较少。通过控制钢帘线的拉丝、盘条的处理、钢帘线的铅浴淬火,水浴淬火和电镀等生产工艺过程,调节好铅浴淬火和镀铜的工艺参数,是提升钢帘线质量的重要措施。未来帘线钢企业应加快研制强度更高、线径更细的帘线钢丝,同时进一步提高钢丝的稳定性。
基金项目
广西重大科技专项(桂科AA18242013-2)。
NOTES
*通讯作者。