1. 引言
7003铝合金属于中等强度铝合金,具有强度高、焊接性及成型性好等优点,作为一种轻质合金材料广泛应用在车辆、建筑、桥梁等领域中 [1] [2] [3]。众所周知,该合金为时效强化合金,其析出序列 [4] 为:过饱和固溶体(sss)→偏聚区(GP区)→亚稳相η’ (Mg(Zn, Cu,Al)2)→平衡相η(MgZn2)。一般认为,峰值时效(T6)状态下,该合金基体中析出高密度的半共格η’相,可使合金的力学性能最佳。但是,晶界上连续分布的析出相导致合金的耐腐蚀性能变差 [5]。对于目前高强的Al-Zn-Mg-Cu系合金而言,Cu元素的加入能够提高晶内析出相密度及晶界相的电位,使其阳极溶解速率和应力腐蚀裂纹扩展速率降低,力学性能提高。然而共晶的Al2CuMg相的增加对点蚀及断裂性能的降低尤为明显 [6],不适用于制备具有复杂形貌的型材。耐腐蚀性能是7xxx系铝合金材料服役过程中的一项重要参考指标,其在很大程度上限制了该合金在工程上的应用。
Zn和Mg作为主合金元素,显著影响Al-Zn-Mg合金的微观组织、力学性能与腐蚀性能,它们总量的增加必然使合金中沉淀强化相的体积分数增加,提高强度,但溶质浓度过高会对合金的韧性和抗应力腐蚀性能产生不利影响 [7] [8]。另外,Mg含量过高会导致熔铸过程中易发生氧化而产生气孔等铸造缺陷 [9],而Zn含量过高则易形成较大的内应力,降低抗晶间腐蚀性能,导致构件服役时容易出现晶间裂纹而断裂 [10]。因此,对Zn和Mg元素之间的比例调整尤其重要。有研究 [11] [12] 表明,Zn/Mg比值的大小改变了时效过程的析出序列,从而显著影响合金的强度。Zn/Mg比较高(Zn/Mg > 2.2)时,GP区主要转变为η’或η平衡相;Zn/Mg比较低(Zn/Mg ≤ 2.2)时,GP区主要转变为T’或T平衡相(Mg32(Al,Zn)49)。然而,在不改变析出序列的前提下,Zn/Mg比值对合金组织与性能方面的相关研究较少。
因此,本文以7003铝合金挤压型材为研究对象,在保证(Zn + Mg)总量不变的情况下,研究Zn/Mg比对力学性能与晶间腐蚀性能的影响,并揭示其影响机理。从而为该合金的成分优化与性能调控提供参考。
2. 实验材料与方法
2.1. 实验材料及热处理
实验材料为4.5 mm厚度的7003铝合金挤压型材。三种合金材料的(Zn + Mg)总量约为6.6 wt.%,其Zn/Mg比(质量分数比,下同)分别为11.4 (1#合金)、8.1 (2#合金)和6.1 (3#合金),其实际化学成分如表1所示。实验合金先在空气炉中进行480℃保温1 h的固溶处理,室温下水淬冷却,置于干燥的电阻炉中进行120℃的峰值时效。
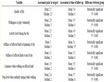
Table 1. Composition of 7003 aluminum alloy with different Zn/Mg ratios (wt.%)
表1. 不同Zn/Mg比的7003铝合金化学成分(mass fraction, %)
2.2. 性能测试
沿7003合金型材的挤压方向各取三组平行试样,采用320、600、800、1000目砂纸打磨试样的平行长度,试样标距为30 mm,在DDL100型电子万能材料试验机上进行室温拉伸性能测试,拉伸速度为2 mm/min,实验结束后通过测量断后标距计算试样的断后伸长率。
晶间腐蚀试验按照GB/T7988-2005标准执行,试样首先用无水乙醇清洗表面油污,采用400、600、800、1000、1500目砂纸将检测面打磨平滑,放入NaOH溶液中碱洗15 min,然后取出放入HNO3溶液中浸泡3 min至出光,用蒸馏水洗净并吹干。对试样的非检测面采用松香进行封装处理,平放于预先配置和经水浴锅预热至35 ± 2℃的晶间腐蚀溶液(57 g NaCl + 10 mL H2O2,用蒸馏水稀释至1 L)中浸泡6 h。实验结束后截取试样横截面用砂纸进行打磨并抛光,在OLYMPUS BX51M型光学显微镜(OM)下观察腐蚀形貌并测量最大腐蚀深度。
2.3. 微观组织观察
分别切取纵截面试样,采用400、600、800、1000、1500目砂纸进行打磨,机械抛光至表面无划痕。采用Zeiss EVO MA10型扫描电子显微镜(SEM)观察合金的微米级第二相分布情况,并对其进行能谱(EDS)分析。另外取三个薄片试样,用砂纸预磨至100 μm,冲成直径为3 mm的圆片,双喷减薄至50 μm,电解液为20% HNO3 + 80% CH3OH,电压为20 V,电流为50 mA,温度控制在−30 ± 5℃。采用TECNAIG2 F20型透射电子显微镜(TEM)观察合金晶内与晶界的纳米级第二相分布情况。
3. 实验结果
3.1. 室温拉伸性能
图1为三种不同Zn/Mg比合金时效后的室温拉伸试验结果。可见,合金的抗拉强度与屈服强度随着Zn/Mg比的降低而显著提高。1#、2#、3#合金的抗拉强度与屈服强度分别为333.2 MPa、407.3 MPa、446.9 MPa和269.4 MPa、352.9 MPa、397.2 MPa,Zn/Mg = 6.1合金的抗拉强度与屈服强度比Zn/Mg = 11.4合金分别提高了34.1%和47.4%。此外,1#、2#、3#合金的断后伸长率分别为18.4%、17.6%和17.3%。可见Zn/Mg比的降低对合金强度有明显的提升作用,而对断后伸长率的影响较小。

Figure 1. Tensile properties of alloys with different Zn/Mg ratios at room temperature
图1. 不同Zn/Mg比合金的室温拉伸性能
3.2. 晶间腐蚀
三种合金的晶间腐蚀形貌及其腐蚀深度的测定如图2所示。可见,三种合金的腐蚀形貌均为典型的晶间腐蚀形貌,腐蚀从表面沿垂直和水平方向侵蚀。1#、2#、3#合金的最大腐蚀深度分别为29.5 μm、25.9 μm和14.5 μm,其对应的腐蚀宽度分别为208.7 μm、110.1 μm和41.1 μm。综上可知,合金在相同的时效状态及浸泡条件下,随着Zn/Mg比的降低,其晶间腐蚀过程中最大扩展深度及宽度均呈现下降趋势,根据国标可评定合金的抗晶间腐蚀性能得以提升。
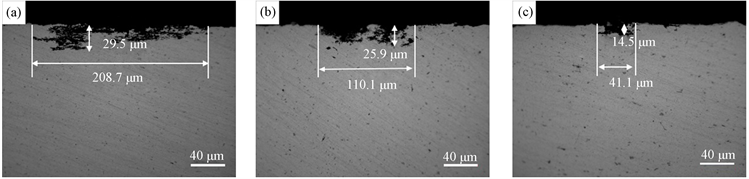
Figure 2. Intergranular corrosion morphologies of alloys with different Zn/Mg ratios: (a) 1# alloy; (b) 2# alloy; (c) 3# alloy
图2. 不同Zn/Mg比合金的晶间腐蚀形貌:(a) 1#合金;(b) 2#合金;(c) 3#合金
3.3. 微观组织
图3为不同Zn/Mg比合金的SEM图像与EDS分析谱图。由图3(a)、(b)、(c)可见,T6时效热处理状态下的第二相粒子在背散射电子模式下呈现白色且形态各异,沿着挤压方向不均匀分布在基体上。结合图3(d)的EDS分析结果可知,这些白色的第二相粒子主要为含Fe、Si元素的AlFeMnSi杂质相,并溶入其周围基体中的少量Zn、Mg原子。运用Image Pro Plus分析软件对试样多个区域的第二相粒子数目进行统计分析,结果显示1#、2#、3#合金基体单位面积上析出的第二相粒子数目分别为9609个/mm2、7852个/mm2、5216个/mm2。说明随着Zn/Mg比的降低,合金基体上析出的第二相粒子体积分数明显减少。
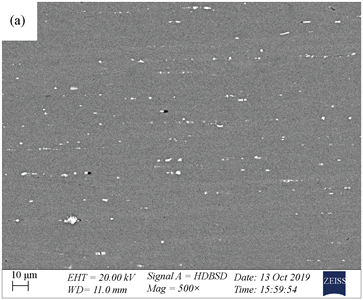

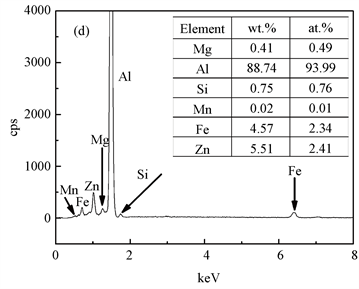
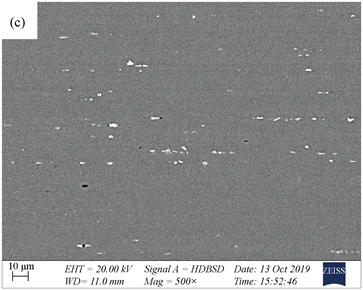
Figure 3. SEM images and EDS analysis of alloys with different Zn/Mg ratios: (a) 1# alloy; (b) 2# alloy; (c) 3# alloy; (d) EDS analysis of white phase
图3. 不同Zn/Mg比合金的SEM图像与EDS谱图:(a) 1#合金;(b) 2#合金;(c) 3#合金;(d) 白色相的EDS分析
图4所示为时效后三种不同Zn/Mg比合金的晶内与晶界纳米结构相的TEM图像。可见,在120℃峰值时效热处理后合金晶粒内部均匀析出圆盘状的纳米析出相,且在晶界处均出现明显的无沉淀析出带(PFZ)。由图4(a)、(c)、(e)中右下方的衍射斑点可知,电子沿<100>Al晶带轴入射,除了铝基体斑点,在晶向族{311}的1/3和2/3位置处出现了明显的衍射斑点,根据文献 [13] 可认为该析出粒子为η’相。另外,从图中可发现,1#合金的η’相尺寸相比于2#、3#合金较粗大,3#合金的η’相尺寸最小,2#合金介于两者之间。运用Image Pro Plus分析软件对多个区域的η’相密度进行统计分析。结果显示1#、2#、3#合金的η’相析出密度分别为6652个/μm2、8786个/μm2、11814个/μm2。三种合金在晶界上的析出情况如图4(b)、(d)、(f)所示。可见,1#合金的晶界处析出相密集且连续分布,PFZ宽度约为67.9 nm;2#合金的晶界相明显稀疏,PFZ宽度约为53.5 nm;3#合金的晶界相间距进一步增大,PFZ宽度缩小至39.3 nm。综上可知,随着Zn/Mg比的降低,合金晶粒内部析出的η’强化相的尺寸逐渐减小,数量密度逐渐增大,其晶界上的析出相逐渐从连续向断续分布状态转变,且析出相之间的间距变大,PFZ宽度逐渐减小。
4. 分析与讨论
Al-Zn-Mg合金的强化方式分别为固溶强化、晶界强化、位错强化和析出强化,固溶及晶界强化对于可时效强化铝合金而言贡献较少,位错密度在固溶过程中亦大量消失,因此本研究仅对其析出强化的贡献进行讨论,它的强化机制与析出相的种类和间隔密切相关。众所周知,在合金时效过程的析出序列中,亚稳的GP区及η′相对塑性变形过程中位错的绕过与切过的阻碍作用较为严重,显著影响合金的强度,而η相由于与基体不共格,强化效果减弱,因此合金在过时效(T7)阶段的强度明显低于T6态 [14]。三种实验合金均处于T6峰值时效状态,可保证合金晶内强化相的最大析出程度。1#、2#、3#合金的Zn/Mg质量分数比值分别为11.4、8.1、6.1,均高于MgZn2相的质量比(Zn/Mg = 5.4),说明在合金中Zn元素过量,故η’相的析出密度主要取决于Mg元素的含量。在Zn、Mg原子能够充分反应并转变为强化相的情况下,随着Zn/Mg比的降低,Mg原子浓度增加,溶质可反应浓度增加,促使反应自发向生成η’相的方向进行,最终使η’相的析出密度增加,间隔减小。因此,Zn/Mg比降低,合金的屈服强度和抗拉强度得到明显的提升。
在Zn/Mg比较高的合金中,由于Zn原子大量剩余,倾向于与Al、Fe、Mn、Si原子结合形成粗大的AlFeMnSi杂质相(图3所示),造成杂质相的体积分数的大量增加。该相与基体相邻界面非共格,塑性变形阶段易于形成应力集中,产生微裂纹并与基体分离,为宏观裂纹形成前提供损伤起始点。另一方面,时效析出机理为溶质扩散析出过程,随着Zn/Mg比的降低,基体中Zn原子浓度降低,Mg原子浓度增加。由于Mg原子的扩散系数低于Zn原子 [15],从晶内向晶界析出过程缓慢,降低整体溶质原子的扩散速率,加之η’相在晶内大量形核,故使PFZ窄化,强化晶界强度,对中高强铝合金断裂韧性的影响较为明显。因此,Zn/Mg比降低,在屈服强度增加的情况下增大了杂质相–基体界面及晶粒–晶粒相界面的应力差,但由于第二相粒子的减少及PFZ宽度的降低,降低了其空洞与裂纹的萌生和沿晶断裂倾向性,相对于单一调控Mg含量的合金而言,降低断后延伸率的下降程度,使强度和断裂韧性的关系得到良好调控。
Al-Zn-Mg合金腐蚀的发生往往与相电位差有关 [16],并且腐蚀的源头一般发生于粗大第二相及能量亚稳的晶界处。对于富含Fe,Si的杂质相,通常分布于晶界处及附近,与基体产生较大的电位差而引起周围的Al基质被侵蚀,因此一般被认为是点蚀或晶间腐蚀的起源。另一方面,对于晶界PFZ和晶内而言,晶界上MgZn2相的电位较低,优先发生阳极溶解,当晶界的析出相连续分布时,则形成了连贯的腐蚀通道,在腐蚀形态上表现为沿晶腐蚀。此外,Zn在铝中有很大的固溶度,在基体中十分稳定,而Mg容易在晶界上偏聚,形成较大的富Mg区 [17],此较大的富Mg区从晶界以及周围晶体的基质中汲取Zn原子,促进η’相粗化转变为η相。Zn/Mg比低的合金由于晶内析出高密度的η’相,晶界附近的η’相不断向晶界迁移,导致晶界上η’相互相吞噬长大,相之间的间距增大,在晶界上表现为断续分布。综上所述,随着Zn/Mg比的降低,杂质相的体积分数降低,减少了点蚀的触发,且晶界上析出相之间的间隔变大,PFZ变窄,降低了晶界相与周围基质的电位差,从而阻断了腐蚀过程,因此合金的抗晶间腐蚀性能提高。
5. 结论
1) 在Zn + Mg总量约为6.6 wt.%的7003-T6铝合金中,Zn/Mg比值从11.4降到6.1,合金的抗拉强度与屈服强度分别提高了34.1%和47.4%,延伸率仅降低了1.1%。合金的抗晶间腐蚀性能随着Zn/Mg比的降低而有所改善,其最大腐蚀深度与宽度均逐渐减小。
2) Zn/Mg比的降低增加了合金基体中Mg元素的含量,时效后析出更大密度的η’相,使合金的强度提高,同时降低了杂质第二相的体积分数和缩小了无沉淀析出带的宽度,相比于单一调控Mg含量的合金减少了断后延伸率的降低。晶界上Zn原子含量及溶质整体扩散系数的降低,对MgZn2相的长大过程不起阻碍作用,阻断晶界相的连续性,减缓了合金的沿晶腐蚀现象,使垂直和水平扩展腐蚀宽度分别降低了50.8%和80.3%。从力学与抗腐蚀性能方面考虑,在三种不同的比例中Zn/Mg比为6.1时Al-Zn-Mg合金的综合性能较佳。
基金项目
本文研究工作得到了“国家重点研发计划课题(2016YFB0300901)”“国家自然科学基金课题(51705539)”提供的资助。