1. 引言
半导体微腔激光器成为近些年光子学及光电子学领域研究的热点之一 [1] [2]。其中,回音壁模式(Whispering Gallery Mode) [3] 微腔激光器具有体积小、阈值低、功耗低等优点,在光子集成电路和片上光互连光源等应用中具有极大优势 [4]。早期提出的WGM微腔激光器输出光功率具有各向同性,单一出光性较差 [5]。研究人员为解决该问题,提出了变形腔的概念,即通过改变微腔形状或者在圆形微腔中引入一个小缺陷,破坏其圆对称性来实现其定向输出 [6] [7]。其中蜗线形微腔既取得了较高的Q值,又获得了方向性较强的激光出射。微腔激光器出光方向的单一性,使微腔激光器能够利用阵列分布方式有效提高微腔激光器输出功率。
对半导体激光器阵列而言,阵列内各发光单元间的热串扰行为是限制半导体激光器阵列稳定性最主要的因素 [8]。半导体激光器阵列热串扰行为主要是由于有源区内废热因不能及时传导出,而大量的积累,并且在有源层、波导层及包层内沿横向传导所致。热串扰行为会使激光器工作时的温度升高,进而使器件的阈值电流升高、波长红移、模式不稳定、内部缺陷增加、器件的寿命降低等 [9]。研究阵列内发光单元间热串扰行为对于降低器件热阻,器件工作状态的合理选择,以及提高阵列内发光单元间的温度均匀性,降低阵列总光谱宽度等方面都是具有重要指导意义。为此我们使用ANSYS Workbench 18.0软件对微腔半导体激光器阵列进行有限元热分析 [10] [11],得出了较为理想的阵列周期以适应微腔半导体激光器高功率的发展要求。
2. 激光器阵列稳态热模拟
2.1. 模型建立
半导体激光器处于稳态工作时,可以利用微腔激光器的热流量密度分布、热量分布和最高温升分析表征器件结构的散热性能。因阵列内发光单元间的热串扰行为导致阵列达到稳态时阵列内各发光单元的温度急剧升高,阵列中心位置的发光单元受热串扰行为的影响最为严重。同时,通过半导体刻蚀工艺形成的激光器台面是粗糙且有一定角度的(通常为±10˚)。对于半径为100 μm的微盘腔激光器,以上因素对激光器阵列热分析影响可忽略不计。因此,在分析研究阵列内各发光单元之间热串扰行为模拟阵列稳态热分布时,假设阵列内各发光单元的输出功率一致,微腔激光器为侧壁光滑垂直且标准圆柱形的理想状态。
在半导体激光器内部,热产生机制主要由激光器芯片的结构及芯片外延材料的物理性质决定。根据其不同的生热本质,可将激光器芯片内部的热产生机制分为焦耳热、复合生热、汤姆森热、光吸收热。当半导体激光器处于工作状态时,上述四种热源机制是同时存在且相互影响的,无法完全将其完全加以区分。同时,对于实际的大功率半导体激光器阵列而言,受外延片的生长的均匀性并非完美、器件工作时注入电流的扩散过程也非均匀等因素的影响,使阵列中各发光单元的生热量不一致。因此,在本文的热特性模拟分析中,并未对各种热源进行区分,而是统一地假定热源集中于激光器芯片的有源区及上下波导层内,并且均匀分布于各发光单元区域内的理想状态。基于上述简化假设,当器件处于工作状态时,注入电能转化为光能和热能两部分。即
(1)
(2)
其中,W为器件工作时注入电能,Q为器件工作时产生的电能,Pout为器件输出功率,η为电光转换效率。因此,在有源区内各发光单元施加均匀的生热率载荷计算如式:
(3)
其中,V为有源区体积,N为阵列内包含的发光单元个数,d为有源区厚度,S发光单元有源区底面面积。
实际模拟时还忽略器件侧边与周围空气的自然对流换热及热辐射传热作用,即:
(4)
其中n为垂直于边界平面的单位向量,S为器件侧表面面积,不包括热沉底面。
假定器件各层材料之间满足温度及热流密度的连续性,
(5)
(6)
其中,i表示第i层材料。器件实际工作时,铜热沉底尺寸较大,故在模拟中认为热沉底部的温度保持25℃不变。
建立热分析模型,其尺寸、热导率等具体参数如表1所示。
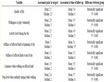
Table 1. Modeling parameters in ANSYS simulation
表1. ANSYS模拟中的建模参数
微盘腔半导体激光器阵列封装模型从上至下为:上电极、欧姆接触层、上波导层、有源层、下波导层、衬底层、下电极、In焊料、Cu热沉,建立模型如图1所示。对建立的模型进行添加材料、接触面定义、网格划分和工作条件荷载等条件设置,并进行运算。
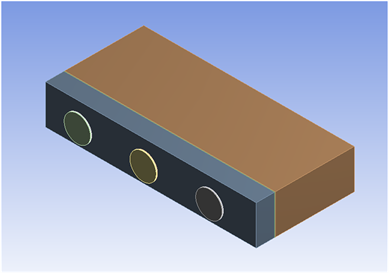
Figure 1. Micro-disk cavity semiconductor laser array model
图1. 微盘腔半导体激光器阵列模型图
2.2. 结果与讨论
对半径为100 μm微盘腔半导体激光器进行热流量密度模拟仿真,如图2为微盘腔激光器阵列热流矢量。图2中红色箭头为最大热流矢量即阵列边缘与热沉热传导散热热流量,最大热流量为2.6752 * 107 W/m2。蓝色箭头为最小热流矢量即上腔面与空气热对流散热热流量,最小热流量为10,423 W/m2。芯片热源的散热方式主要有与空气间热对流交换散热和与热沉间热传导散热两种。其中,起重要作用的是通过向下和向两侧传导到热沉进行散热的方式。但是,受阵列热串扰行为影响,各发光单元与热沉热传导散热热流量密度也不尽相同,发光单元间热流量小于边缘热流量。会造成阵列中的废热不能及时有效传导出。为此,探究理想的阵列周期能够大大减小阵列中热量的积累,增强阵列散热效果。
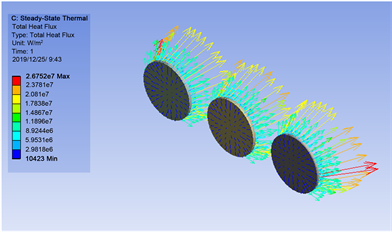
Figure 2. Heat flux vector diagram of micro-cavity laser array
图2. 微盘腔激光器阵列热流矢量图
对半径为100 μm微盘腔激光器阵列,分别以阵列周期为250 μm、450 μm、550 μm、700 μm进行稳态热模拟仿真,并对结果进行对比分析。如图3分别为阵列周期是250 μm、450 μm、550 μm、700 μm的温度分布云图。
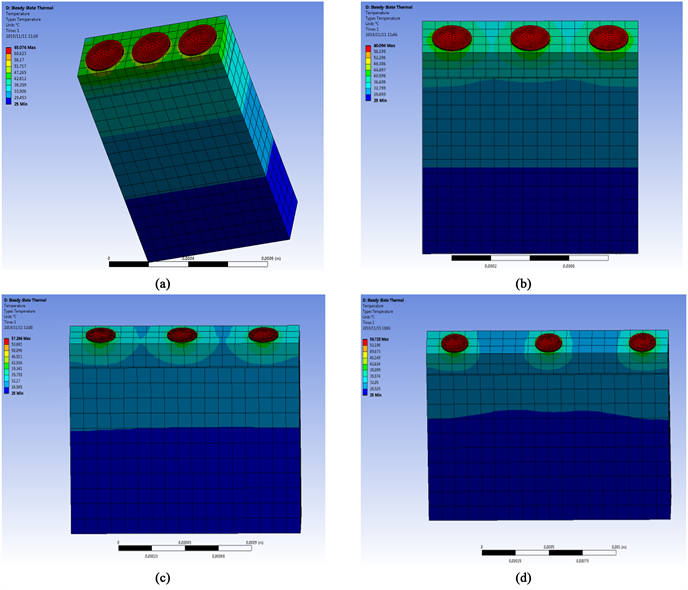
Figure 3. (a) 250 μm; (b) 450 μm; (c) 550 μm; (d) 700 μm array periodic heat distribution cloud map
图3. (a) 250 μm;(b) 450 μm;(c) 550 μm;(d) 700 μm阵列周期热分布云图
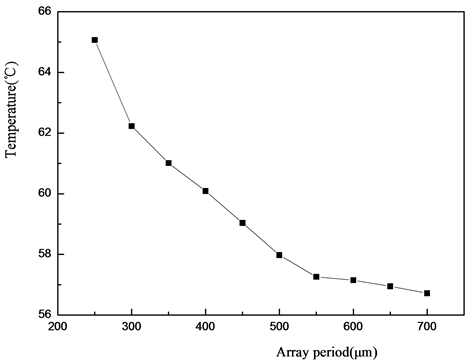
Figure 4. Curves of periodic and temperature variations of arrays
图4. 阵列周期和温度变化关系曲线图
如图3所示,图中芯片红色部分为最高温度,即微腔激光器最高温度集中在上腔面附近。微盘腔半导体激光器阵列周期为250 μm和400 μm时,器件最高温度分别为65.076℃、60.094℃,温升分别为40.076℃、35.094℃,温升有明显下降,各发光单元间热量有明显叠加,阵列热串扰行为严重。阵列周期为550 μm和700 μm时,器件最高温度分别为57.266℃、56.723℃,温升分别为32.266℃、31.723℃,温升变化不明显,各发光单元间热量无明显叠加,阵列热串扰行为有明显改善。进一步,对阵列周期从250 μm到700 μm进行定量对比分析,得到微腔激光器阵列周期与阵列最高温升关系,如图4所示。
由图4可知,随阵列周期增大器件最高温度逐渐下降。在阵列周期小于550 μm时,最高温度受阵列周期影响较大,温度变化较为明显。在阵列周期大于550 µm后温度变化趋于平稳,最高温度受阵列周期影响较小。也就是说,在阵列周期550 µm时半径为100 µm微腔激光器阵列可以达到较为理想的散热效果。
3. 结论
本文采用ANSYS有限元分析软件建立微腔半导体激光器阵列仿真模型,分析了在稳态条件下,不同阵列周期对芯片最高温度的影响,反应了不同微腔半导体激光器阵列周期的散热效果。发现对于半径为100 µm微腔激光器阵列,阵列周期为550 µm时阵列热串扰行为得到明显改善,有较为理想的散热效果。通过对微腔激光器阵列的模拟仿真,为后期微腔半导体激光器阵列的半导体工艺提供了理论依据。
NOTES
*通讯作者。