1. 引言
2019年以来,商用车轻量化需求持续延续,其中悬架系统轻量化成为必然趋势。以商用车中牵引车为例,普通牵引车前悬架3片抛物线板簧,后悬架5片抛物线板簧;轻量化高端牵引车前悬架2片抛物线板簧,后悬架3片抛物线板簧,未来进一步轻量化方案为前悬架单片簧,后悬架轻量化3片簧。然而对于商用车中自卸车来说,同样存在轻量化需求,特别是自卸车后悬架系统轻量化(抛物线少片簧替代普通多片簧)需求也越来越强烈,同时自卸车对于其悬架系统的高疲劳性能要求也越来越高 [1]。悬架系统轻量化和高疲劳性能要求,必然要求其设计应力提高,这对商用车悬架系统使用原材料弹簧钢性能提出了更高的要求 [2]。结合国内弹簧钢冶炼及工业化水平,采用铌或铌钒微合金化技术,通过细晶强化和析出强化等途径,开发抗拉强度大于1500 MPa新型含Nb高强弹簧钢原材料LPD65,并对新型含Nb高强弹簧钢原材料LPD65的热处理性能、力学性能、疲劳性能进行研究 [3] [4] [5]。满足商用车悬架系统轻量化板簧设计需求,同时满足国内主机厂对轻量化悬架板簧疲劳寿命要求 [6] [7]。
2. 材料制备及试验方法
2.1. 高强弹簧钢LPD65制备
高强弹簧钢LPD65主要化学成份设计见表1,依据相应板簧设计需求,冶炼规格28 × 90 mm规格的弹簧钢原材料,用于材料化学成份、热处理性能和疲劳性能的研究。
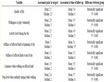
Table 1. Chemical compositions of LPD65 (Wt%)
表1. LPD65化学成份设计(Wt%)
2.2. 试验方法
LPD65冶炼完成后,使用Q4直读光谱仪进行化学成份检测;用WDW-G型电子万能拉伸试验机测试新材料热处理后试样机械力学性能;使用HR-15A型号洛氏硬度计检测新材料试样热处理后淬火硬度及回火硬度;用Nikon MA100型金相显微镜及JEOLJEM-1400型透射电镜,对新材料热处理试样进行组织观察;产品试制完成后,使用PSJ200型机械疲劳试验机进行台架疲劳试验及道路试验。
3. 结果与讨论
3.1. 化学成分分析
高强弹簧钢LPD65化学成份检测(表2)。由表可知,不同炉号冶炼的高强弹簧钢LPD65,其化学成份均符合化学成份设计要求,且各种化学元素成份相对均匀,这表明此化学成份设计满足冶炼要求,可以实现规模生产。
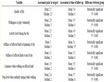
Table 2. Chemical composition analysis of LPD65 (Wt%)
表2. 高强弹簧钢LPD65成份分析(Wt%)
3.2. 力学性能分析
高强弹簧钢LPD65热处理后的力学性能要求如表3所示。在450℃ ± 20℃的回火范围内,弹簧钢的强度大于1450 Mpa,断面收缩率 ≥ 30%,断后伸长率 ≥ 9%。
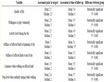
Table 3. Mechanical properties of LPD65 in the conventional heat treatment conditions
表3. 高强弹簧钢LPD65热处理力学性能
3.3. 组织结构与强韧化机理分析
图1为高强弹簧钢LPD65热处理后的金相组织,为细致的回火屈氏体,结合JB3782-84评级标准判定为1级;图2为高强弹簧钢LPD65热处理后的晶粒度照片,依据GB/T6394-2002金属平均晶粒度测定方法评定晶粒度为10级。图3为高强弹簧钢LPD65热处理后扫描电镜(1000倍)形貌,分析可知为典型回火屈氏体形貌,且组织分布均匀;图4为高强弹簧钢LPD65热处理后扫描电镜(5000倍)形貌,在均匀清晰的回火屈氏体形貌之中,弥散均匀分布碳化物颗粒。综上可知,高强弹簧钢LPD65经过热处理之后,可获得较细的回火屈氏体组织,另合金元素,特别是Nb元素的加入,形成了高性能碳化物的固溶体,且此种固溶体易偏聚在晶界处,阻碍晶粒长大。同时,在位错进行滑移时,高性能碳化物的固溶体对位错滑移产生钉扎作用,这也是高强弹簧钢LPD65具有较高强度和优良的塑韧性的根本原因。
3.4. 工艺性分析
表4是高强弹簧钢LPD65末端淬透性试验数据,图5是高强弹簧钢LPD65的未端淬透性试验曲线。新型高强弹簧钢LPD65具有较好的淬透性,完全能满足高应力少片板簧不同厚度原材料淬透性工艺需求。
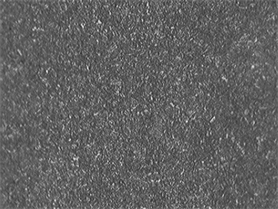
Figure 1. Tempered microstructure (500×)
图1. 回火金相组织(500×)
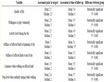
Table 4. The hardenability test of LPD65
表4. LPD65末端淬透性试验数据
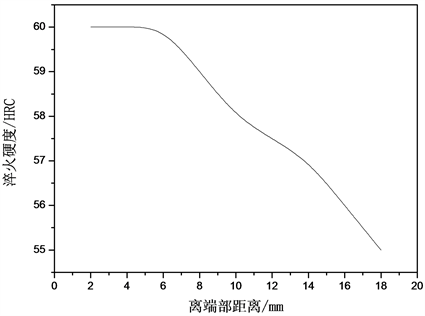
Figure 5. Hardenability curve of LPD65
图5. 高强弹簧钢LPD65淬透性曲线
3.5. 台架疲劳试验
图6是使用高强弹簧钢LPD65试制板簧进行台架试验结果。由图6可知:
1) 高强弹簧钢LPD65试制板簧,在国标台架试验条件,最大试验应力833 MPa,台架试验疲劳寿命是80万次未出现断裂,远远大于国标要求的10万次疲劳寿命,接近板簧设计无限寿命100万次;
2) 高强弹簧钢LPD65试制板簧,在主机厂台架试验条件,最大试验应力900 MPa,台架试验疲劳寿命是50万次未出现断裂,远远大于主机厂要求的16万次疲劳寿命;高强弹簧钢LPD65试制板簧,在
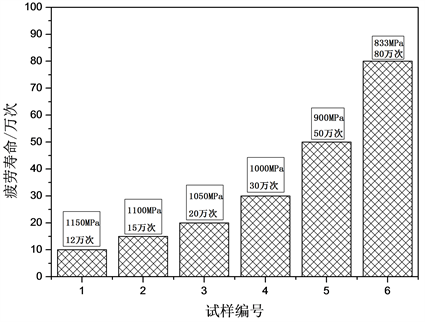
Figure 6. The fatigue test results of leaf spring using LPD65
图6. 高强弹簧钢LPD65试制板簧台架试验结果
主机厂台架试验条件,最大试验应力1000 MPa,台架试验疲劳寿命是30万次未出现断裂,远远大于主机厂要求的12万次疲劳寿命;高强弹簧钢LPD65试制板簧,在主机厂台架试验条件,最大试验应力1050MPa,台架试验疲劳寿命是20万次未出现断裂,远远大于主机厂要求的12万次疲劳寿命;高强弹簧钢LPD65试制板簧,在主机厂台架试验条件,最大试验应力1100 MPa,台架试验疲劳寿命是15万次未出现断裂,远远大于主机厂要求的12万次疲劳寿命,具有优异的疲劳特性;
3) 高强弹簧钢LPD65试制板簧,最大试验应力1150 MPa,台架试验疲劳寿命是12万次未出现断裂,也可以满足主机厂12万次疲劳寿命的要求,达到行业内绝对领先水平。
4. 结论
1) 研制新型含Nb高强弹簧钢LPD65,适用于商用车高应力、轻量化板簧产品。
2) 新型含Nb高强弹簧钢LPD65具有良好的热处理性能和淬透性,热处理后抗拉强度大于1450 MPa,略低于材料预想抗拉强度目标,后续需进一步进行热处理工艺研究,实现抗拉强度大于1500 MPa设计目标。LPD65中Nb元素的加入,形成了高性能碳化物的固溶体,其对位错滑移产生钉扎作用,使得高强弹簧钢具有高强度和优良的塑韧性。
3) 新型含Nb高强弹簧钢LPD65,试制板簧台架疲劳寿命优异,在国标的试验应力条件下,疲劳寿命接近100万次无限寿命;在高应力1150 MPa试验应力条件下,台架疲劳寿命可达到12万次未断,处于行业内绝对领先水平。