1. 引言
轴流式风扇具有驱动风量大、工作效率高、结构简单等特点被广泛应用于发动机冷却系统。发动机冷却风扇工作在高压比、高转速、高负荷的复杂环境中,风扇叶片会产生一定程度的变形,这些变形会改变空气流动,从而影响风扇的气动性能。目前对冷却风扇气动性能分析多采用多重参考系法,其作为定常计算并不能真实模拟风扇实际工作状态,为克服这一缺点,本文采用流固耦合方法对风扇进行数值模拟计算。
国内外许多学者对流固耦合这一方法进行了大量的研究,周忠宁等 [1] 对流固耦合的叶片振动力特性进行了分析,结果表明在旋转预应力与耦合场的作用下,叶片模态频率与振型发生明显改变。Bazilevs Y. [2] 等借助流固耦合法对风力机叶片的疲劳强度进行了预测,得出风力机疲劳损伤位置一般出现在叶片前缘位置。Syed-shah Khalid等 [3] 采用CFX对风力机在不同风速下进行了双向流固耦合分析,结果表明无论是结构应力还是变形量双向流固耦合法计算的值均大于单向流固耦合计算值。Jo,Do-Youb Kim等 [4] 对某款风机借助单向流固耦合方法进行模拟计算,对风机叶片表面应力分布以及流线分布进行了分析。David W. [5] 对一款水平轴风力机的柔性叶片和刚性叶片分别进行了试验和数值仿真研究,结果表明无论是扭矩还是风能利用系数柔性叶片结果均大于刚性叶片。王军等 [6] 采用单向流固耦合法对空调轴流风机叶片的气动弹性进行了数值分析,结果表明刚化效应对风机自振频率有较大影响,风机自振频率随转速的增加而增大。张立茹等 [7] [8] 采用双向流固耦合法对实木材料和环氧树脂材料风力机叶片变形进行了相关研究,结果表明叶尖位置变形最大。谢军龙 [9] 等对空调外机旋转叶片进行流固耦合分析,得出考虑风轮材料对样机风轮变形有一定的影响,随着转速的增大,风压对叶片变形的影响变大。罗黎等 [10] 采用单向流固耦合理论,计算了在离心力与气动载荷的作用下轴流风扇的应力分布情况。
综上所述,双向流固耦合方法可以用于风扇气动性能的研究。许多学者已采用该方法对压气机 [11] [12] [13] 及风机转子 [14] [15] [16] 性能进行研究,但采用双向流固耦合法对发动机冷却风扇性能的研究相对较少。本文对发动机冷却风扇分别进行双向流固耦合法和多重参考系法仿真计算,并与试验对比分析。探究耦合作用下叶片变形对风扇气动性能的影响。
2. 发动机冷却风扇性能评价指标
根据发动机冷却风扇设计要求,主要通过风扇的静压及所消耗的功率和工作效率等参数来评价风扇的气动性能。发动机冷却系统的阻抗随着气体流量的变化而变化,因此静压、功率等性能参数也会有所改变。
如图1所示,风扇流量–静压曲线与冷却系统的阻抗曲线交点定义为风扇工作点,对应风扇在该系统中的工作功率及工作效率。在工作点附近的工作区域工作时风扇效率最高。因此在冷却系统匹配时应尽量避开小流量点和大流量点。在风扇气动性能试验中,可通过测量风室入口静压值得到风扇流量。具体计算如下:
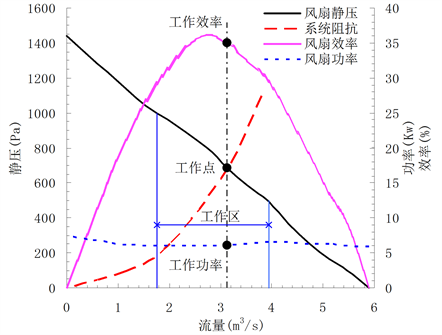
Figure 1. Matching diagram of fan performance curve and system impedance curve
图1. 风扇性能曲线与系统阻抗曲线匹配示意图
(1)
其中:
为编号i喷嘴的排出系数。di为i喷嘴的管道直径,单位为m。ΔP是由压力计测出的前风室与后风室间的压差单位为Pa。ρ为风室内空气密度,单位为Kg/m3。
工作过程中风扇压力分为静压与动压,静压作为风扇气动性能有效参数在试验测量过程中采用测量监测面的静压值计算得到,静压计算公式具体如下:
(2)
其中p0为试验大气压,psp0为监测面静压,pdp0为监测面动压,
进口到监测面间压力损失值,A0为监测面面积。
冷却风扇消耗的功率是指发动机传递给风扇的能量,可由发动机提供的输出功率计算得到,功率计算具体如下:
(3)
其中T为冷却风扇扭矩单位为N·m,n为冷却风扇转速单位为rpm。
冷却风扇静压有效功率与风扇的输入功率之比为风扇静压效率,具体计算如下:
(4)
一个高性能的发动机冷却风扇在实际工作中应是:在一定的静压下能够驱动更多的流量来保证发动机冷却系统的散热,同时其消耗的发动机功率也应尽可能的小,效率尽可能的高。
3. 冷却风扇性能试验与模型的确定
3.1. 冷却风扇性能测试方法
在国家标准《GB-T1236-2000工业通风机用标准化风道进行性能试验》 [17] 中选择规定的A型(自由进口–自由出口)风室装置对发动机冷却风扇性能进行试验,试验结构如图2所示。
试验装置主要由可变供气系统、前后风室及驱动电机组等部分组成。其中可变供气系统主要由节流阀1和辅助风机2组成;风室被分割成两个小风室分别为3和6,并用多个喷嘴5联通,两个风室里均设置了整流网分别为4和7用于梳理空气稳定流量,中间还设有两个压力计12、13用于测试风室内的压力与两个风室间的压差;驱动电机组主要包含驱动风扇的电机11与扭矩、速度传感器10;8为压力测量面用来监测静压。
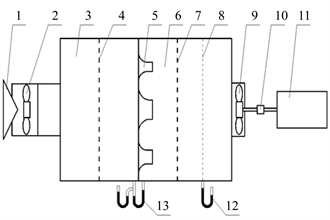
1-节流阀 2-辅助风机 3-前风室 4、7-整流网 5-喷嘴 6-后风室 8-压力监测面 9-被测风扇 10-转速、扭矩传感器 11-驱动电机 12、13-压力计(a) 试验台装置图 (b)试验台结构简图
Figure 2. Structure diagram of a type fan performance test device
图2. A型风扇性能测试装置结构示意图
3.2. 冷却风扇性能测试流程
在发动机冷却风扇的试验过程中,系统通过调节可变供气系统中的节流阀开度和辅助风机转速调节气体流量,控制喷嘴打开的个数调节其阻抗,通过从而得到以一定转速运转的风扇在不同流量点下的静压、功率及效率参数,最后拟合成发动机冷却风扇性能曲线。
发动机冷却风扇的常用材料为强度高抗冲击的塑料材料,本文选取一款直径为290 mm无环有轮毂的五叶片发动机冷却风扇为研究对象对其进行试验和仿真研究,试验中,选择上述A型试验装置,根据厂商要求,设定发动机冷却风扇转速为3000 rpm,对其在六个不同流量点进行试验计算。风扇结构参数具体如表1所示。
3.3. 冷却风扇性能计算的有限元模型建立
为准确模拟风扇试验过程,根据图2风扇性能试验台建立1:1有限元模型如图3所示。并对其细小结构进行了适当的简化处理,由于无法直接测试到风室的出口压力,故建立了一个流体流动区域进行流场分析和压力过渡。对流场进行分区化分,将整个流体域划分为旋转区、过渡区及静止区。利用Hypermesh软件对整个试验模型进行网格划分。由于固体域风扇模型是旋转对称且结构复杂,故采用切割法]将风扇模型切割为1/5进行非结构性网格划分,然后对网格进行轴向复制和旋转处理从而完成完整的风扇有限元模型。流体域采用非结构性网格对旋转区及过渡区进行划分,采用结构性网格对静止区进行划分。为节约计算资源节省计算时间本文对网格无关性进行了验证,对网格数量以及旋转区大小进行控制。由于风扇护风罩与叶尖间隙的大小对风扇性能有较大影响,旋转区域的设置也会影响计算结果,因此本文叶尖间隙设置与试验条件保持一致,旋转区尺寸为除风扇投影宽度外向轴向各延伸30 mm。经过多次计算得到风扇表面网格尺寸为3 mm左右,旋转区最大网格尺寸不超过10 mm时仿真结果稳定且有效。最终控制网格为固体域网格8.82万,旋转区域网格61.93万,过渡区域网格52.16万,进出口网格为27.3万。综上本文共采用1502100个网格单元对模型进行离散。
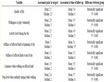
Table 1. Material parameters of fan model
表1. 风扇模型材料参数
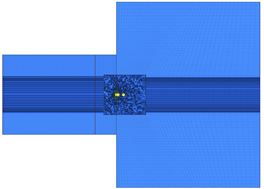
Figure 3. Finite element model for performance calculation of engine cooling fan
图3. 发动机冷却风扇性能计算有限元模型
3.4. 数值计算模型
模拟冷却风扇在流场中的工作过程时,流体流动在一定物理量上存在守恒。对于普通不可压缩的牛顿流体需满足以下:
连续性方程:
(5)
动量方程:
(6)
能量守恒方程:
(7)
其中,v是流体流动速度,ρ是流体密度,c是比热,T为环境温度,k为传热系数,S为粘性力。
4. 风扇气动性能仿真分析
4.1. 多重参考系法
多重参考系法是一种稳态计算方法,精度能满足一般工业要求,对资源占用较少且节约计算时间,因此工程上常用此方法对风扇的性能进行预测。本段基于发动机冷却风扇有限元模型,借助Fluent软件对发动机冷却风扇气动性能进行多重参考系模型(MRF)的仿真计算分析,流场的边界条件及求解设置如表2所示。
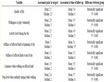
Table 2. Boundary conditions and solution settings
表2. 边界条件及求解设置
风扇的气动性能一般可由流量–静压曲线、流量–功率曲线、流量–效率曲线来表示。图4为转速为3000 rpm时不同流量下发动机冷却风扇性能参数的MRF仿真值与上文所得的试验值对比曲线。
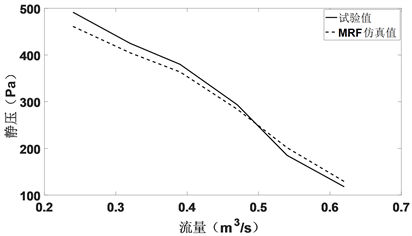
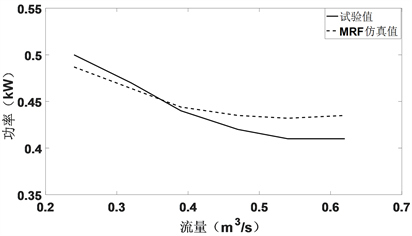
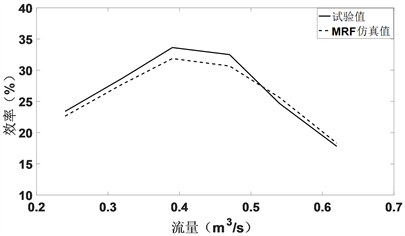
Figure 4. Fan performance comparison curve
图4. 风扇性能对比曲线
由图4风扇性能对比曲线可知MRF仿真计算得到的静压、功率、效率等性能参数值均与试验值吻合较好,三条仿真计算曲线与试验所得曲线在变化趋势上基本一致,只是在数值上有所差异。流量–静压曲线计算结果与试验结果比较接近,两者最大误差在6%以内。在大流量点流量–功率仿真结果误差偏大但仍在9%以内,且仿真计算结果和试验结果均是功率随流量的增大而减小,有一定的参考意义。验证了模型的准确性。多重参考系模型为定常计算模型,对近失速区的小流量点无法计算出合理的仿真值,故不考虑小流量点工况。大流量点误差逐渐变大的原因可能是MRF仿真计算过程没有考虑叶片变形。为探究这一问题继续对发动机冷却风扇进行双向流固耦合法仿真计算,分析叶片变形对仿真结果的影响。
4.2. 双向流固耦合法
双向流固耦合法是一种综合考虑结构与流场间相互作用的仿真方法。其减小了结构变形对仿真结果的影响,使仿真值更接近真实值。建立如图5所示的耦合平台。在fluent模块中对流体域进行设置,采用多重参考系法模拟风扇转动,边界条件及求解设置参照表2,与多重参考系法(MRF)不同的是求解器是采用压力基瞬态求解模拟流体流动,所有变量残差均设置为1 × 10−3,风扇叶片表面设置为流固耦合面,由于结构变形会影响流体流动因此需要进行动网格设置。固体域通过Transient Structural进行计算,对风扇结构进行约束设置并施加转速。在进行计算时结构场与流场应采用相同的时间步长。利用ANSYS Workbench提供的System Coupling实现流场计算与结构计算的数据传递。
双向流固耦合法与多重参考系法(MRF)计算得到的发动机冷却风扇性能参数对比曲线如图6所示。从图中可以看出采用双向流固耦合法计算得到的仿真值相比于MRF法计算的结果均更接近试验值。通过对发动机冷却风扇性能对比曲线分析可以得到:在给定流量下,对于静压,两种仿真计算的结果与试验结果均随流量的增加而减小,与理论相符,两种仿真计算结果均为小流量点偏低于试验值,大流量点偏高于试验值,在中间流量处仿真值与试验值拟合最好。多重参考系法计算值与试验值之间的平均误差为4.5%。双向流固耦合计算值与试验值之间的平均误差在3%以内。对于消耗功率,随着气体流量的增加,发动机冷却风扇所消耗的功率逐渐减小,且两种仿真计算结果与试验值之间的误差值均随流量的增加而增大、双向流固耦合计算结果误差范围为1.5%到4%之间,多重参考系计算结果误差范围为2%到9%之间。产生这种差别的主要原因之一就是多重参考系法所计算的结果仅仅是某一时刻下发动机冷却风扇的运行情况,无法考虑发动机冷却风扇叶片变形对仿真结果产生的影响,而且仿真过程中只考虑了气体载荷对风扇性能的影响,忽略了离心载荷对其性能的影响。双向流固耦合计算是实现流体与固体双向数据交换,综合考虑气体载荷、离心载荷。重力载荷以及叶片变形等实际运转情况下的性能参数。
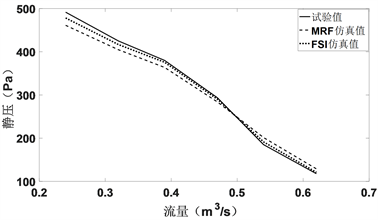
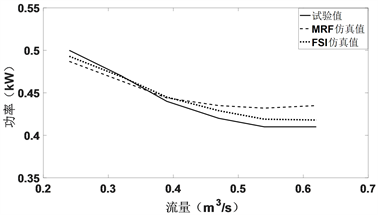
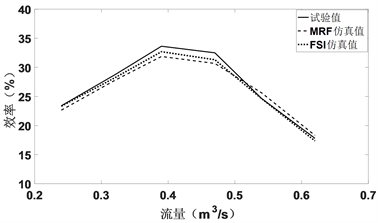
Figure 6. Comparison curve of fan fluid structure coupling performance
图6. 风扇流固耦合性能对比曲线
5. 流场特性分析
5.1. 风扇叶片压力场分析
图7为发动机冷却风扇耦合前后的压力面静压云图,由图可以看出耦合前后风扇压力面静压分布比较均匀,均由叶片前缘向后缘成递增趋势,静压最大区域主要分布在后缘偏叶尖位置,这是风扇叶片主要做工区域,耦合后叶片表面高压区分布更均匀且范围变大。
(a) 耦合前 (b) 耦合后
Figure 7. Static pressure cloud chart of fan pressure surface before and after coupling
图7. 耦合前后风扇压力面静压云图
图8为发动机冷却风扇耦合前后的吸力面静压云图,由图可以看出风扇叶片吸力面静压分布不均匀且以负压为主,耦合前后风扇吸力面静压最小值均出现在叶片端部靠近后缘位置。
(a) 耦合前 (b) 耦合后
Figure 8. Static pressure cloud chart of suction surface of fan before and after coupling
图8. 耦合前后风扇吸力面静压云图
5.2. 风扇叶片变形分析
图9给出了耦合下叶片在两个不同流量处的变形云图,风扇叶片结构在离心载荷和气动载荷共同作用下发生变形,从图中可以看出,不同流量下的叶片变形位置相似,只是数值上存在差异,风扇的叶片变形在数值上均从叶片前后缘向中部减小,叶根部位几乎无变形,叶片最大变形处均在风扇叶片前缘叶尖位置。且变形量波动最大的位置也为前缘叶尖处。这表明离心载荷一定时,风扇叶尖位置受气体载荷影响较大。风扇叶片结构变形会改变流场载荷的大小和分布,使风扇消耗的发动机功率发生改变。从而对风扇气动性能造成影响。
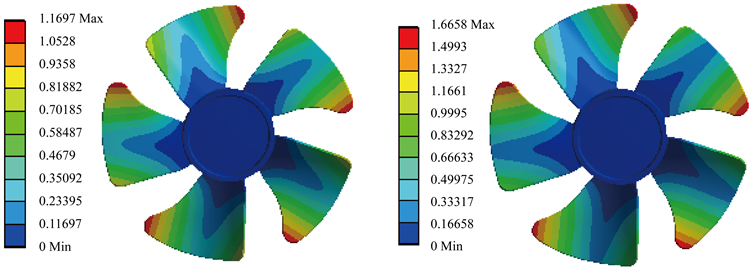
Figure 9. Cloud chart of fan deformation
图9. 风扇变形云图
5.3. 气体流量对风扇叶片变形的影响
发动机冷却风扇在工作的过程中会随着风量的变化引起气动载荷的变化,进而影响发动机冷却风扇叶片的变形,本文研究了气体流量对风扇叶片变形量的影响,图10为气体流量与叶片变形量的关系曲线。由图可知,当风扇转速一定时,叶片的变形量随着流量的增加先缓慢减小后逐渐增大。
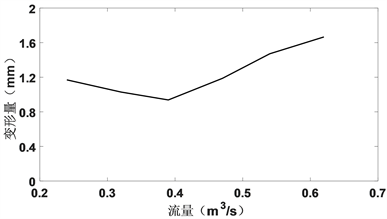
Figure 10. Curve of fan deformation with gas flow
图10. 风扇变形量随气体流量的变化曲线
6. 结论
本文针对发动机气动性能试验建立有限元模型,采用双向流固耦合法和多重参考系法对其进行仿真计算,通过性能对比曲线结合流场特性分析,得到结论如下:
(1) 不同的计算方法对仿真结果有较大的影响。在大流量点,采用双向流固耦合数值计算得到发动机冷却风扇气动性能参数比多重参考系数值计算得到的发动机冷却风扇性能参数更加接近试验值,计算误差有明显的下降趋势。
(2) 冷却风扇叶片在双向流固耦合作用下压力分布更加均匀,叶片压力面正值有所增加但并不明显,吸力面负压有明显降低。
(3) 采用双向流固耦合数值计算结果表明,流量对叶片变形影响较大,叶片变形量随流量的增大先减小后增大,且最大变形位置主要位于前缘叶尖处。