1. 引言
为满足软质手感及个性化的效果,传统的汽车门板中部插件一般采用包覆和低压注塑工艺 [1]。手工包覆工序繁杂、不环保;而低压注塑工艺在注塑完成后,需要修切掉多余的面料,投入更多的设备和人力,成本较高。长春富维安道拓汽车饰件系统有限公司开发了预裁软质小面料常压合模注塑技术(Pre-cutting small soft skin normal pressure close mold back injection technology,简称PC3S技术) [2]。与包覆工艺相比,PC3S技术一次注塑成型即可完成面料与骨架的复合过程,避免后续修切、翻边、喷胶、活化等工序;与传统的低压注塑技术相比,PC3S技术突破了依靠面料在模具分型面封胶的技术弊端,实现了面料尺寸小于产品尺寸,避免后续修切等工序,可提高约30%的面料利用率 [3]。
PC3S工艺使用的面料一般为PVC复合革 [4] 及复合织物 [5] 两种。面料结构分为三层:表皮层、发泡层及底布层。表皮层主要为PVC革或织物,与整车内饰的效果相匹配;发泡层一般为聚氨酯泡沫,使制件表面有柔软的手感,提高舒适度;底布层主要起到阻隔注塑料渗入发泡层及隔热作用,保护表皮层不会因温度过高而产生缺陷。相对于传统包覆工艺,采用PC3S工艺生产的制件局部面料会在高温下受到拉伸、挤压及不均匀受热,容易产生表面褶皱、凹坑等外观质量缺陷。PC3S为新开发工艺,尚未制定满足其工艺要求的面料标准,故本文以PVC面料表皮为研究对象,通过对其物理性能进行研究,找到影响制件表面质量的关键因素,确定指标要求,降低废品率。
2. 实验部分
2.1. 样品选取
基于富维安道拓公司一款门板中部插件,取5个缺陷件,10个合格件(两个厂家的产品各5个),取样,进行对比,如表1所示。合格件如图1(a)所示,不合格件的缺陷主要为褶皱,如图1(b)所示。
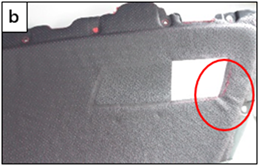
Figure 1. Door panel insert part manufactured by PC3S process. (a) OK Part; (b) NOK Part
图1. PC3S工艺制造的门板中部插件(a) 合格件;(b) 缺陷件
2.2. 检测项目
影响表皮质量的物理性能及检测标准等见表2。
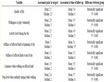
Table 2. Test items and standard
表2. 试验项目及检测标准
3. 结果与讨论
3.1. PVC复合面料厚度及面密度对制件表面质量影响分析
主机厂对表皮厚度的定义为4.6 ± 0.3 mm,面密度为1250 ± 150 g/m2。从表3~5可以看出,有缺陷样品及无缺陷样品厚度均在4.3~4.9 mm之间,面密度均在1100~1400 g/m2之间。PVC复合面料是按照客户对厚度和面密度要求开发的,所以缺陷件及合格件在厚度及面密度的检测值方面并没有差异,厚度和面密度对外观质量无影响。
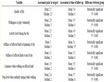
Table 3. 1 - 5 Samples thickness and density test result
表3. 1~5样品厚度和面密度测量结果
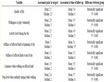
Table 4. 6 - 10 Samples thickness and density test result
表4. 6~10样品厚度和面密度测量结果
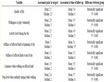
Table 5. 11 - 15 Samples thickness and density test result
表5. 11~15样品厚度和面密度测量结果
3.2. PVC复合面料撕裂力、再撕裂力及缝合撕裂力对制件表面质量影响分析
对PVC复合面料进行撕裂力,再撕裂力及缝合撕裂力测试,结果如图2所示,合格件和不合格件PVC复合面料的经向撕裂力均分布在700~1100 N范围内,纬向撕裂力分布在700~900 N范围内;经纬向再撕裂力值均分布在40~80 N范围内。缝口撕裂力较再撕裂力略有提升,经向分布在90~140 N之间,纬向分布在90~130 N之间。从数据上来看,从表面质量有缺陷的PVC复合面料样品撕裂力值与表面质量合格的制件撕裂力值分布范围一致,因此,可以判定撕裂力不是制件表面质量的影响因素。
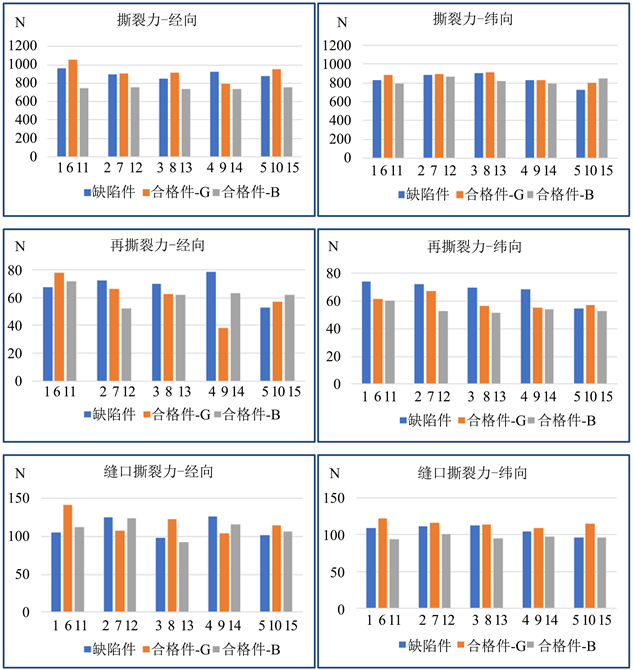
Figure 2. 1 - 15 Samples tear force test results
图2. 1~15样品撕裂力测量结果
3.3. PVC表皮与泡沫、泡沫与衬布之间的结合力对制件表面质量影响分析
从图3可以看出,表面有缺陷的制件与表面质量合格的制件结合力没有差别,面料与泡沫之间的结合力在30~50 N之间。结果表明泡沫、泡沫与衬布之间的结合力不是影响制件表面质量的主要因素。
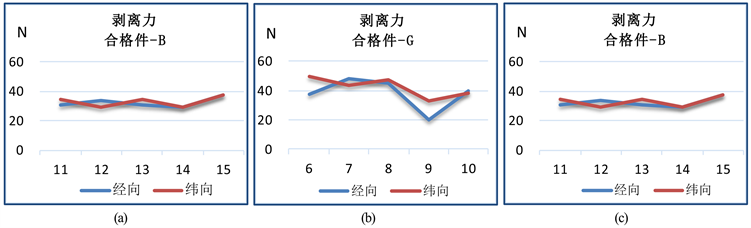
Figure 3. Different samples peel force test result. (a) NOK Parts-G, (b) OK Parts-G, (c) OK Parts-B
图3. 不同样品剥离力测试结果(a) 缺陷件-G,(b) 合格件-G,(c) 合格件-B
3.4. PVC复合面料静态伸长率及永久伸长率对制件表面质量影响分析
从图4可以看出,制件表面良好的PVC复合面料经向静态伸长率分布在4.4%~9.0%之间,纬向静态伸长率分布在9.3%~12.9%之间,纬向静态伸长率一般大于经向静态伸长率。从图中可以看出,制件表面有缺陷的PVC复合面料经向伸长率大于纬向伸长率,并且超出了合格件静态伸长率的范围。结合PC3S工艺过程分析,由于制件在受热冷却后会有经纬向不同程度的收缩,收缩不均匀会引起表面褶皱或者凹坑,PVC复合面料的静态伸长率经纬向差异越大,越容易引起褶皱,或者经向与纬向静态伸长率值异常。进一步比较经纬向静态伸长率差值(纬向–经向,如图5),制件表面良好的PVC复合面料的经纬向静态伸长率差值几乎集中在2.6%~7.5%之间,制件表面缺陷的PVC复合面料经纬向差值较大或者出现负值,所以静态伸长率及经纬向静态伸长率差值是影响PC3S工艺制造的制件表面质量的重要因素。
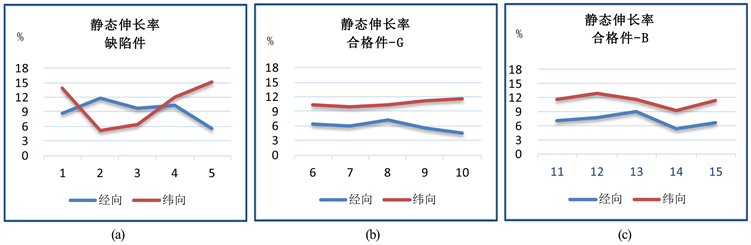
Figure 4. Different samples static elongation test result. (a) NOK Parts-G, (b) OK Parts-G, (c) OK Parts-B
图4. 不同样品静态伸长率测试结果。(a) 缺陷件-G,(b) 合格件-G,(c) 合格件-B
永久伸长率与静态伸长率的趋势基本一致(如图6),因其测量值较小,缺陷件与合格件差异并不明显,所以不作为衡量表面质量的重要指标之一。
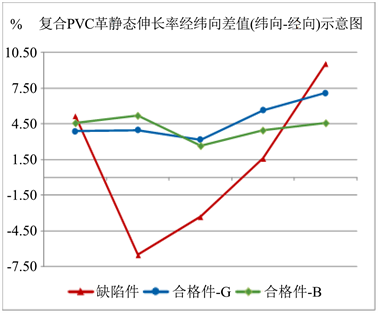
Figure 5. Different samples static elongation warp and weft difference (weft to warp)
图5. 不同样品静态伸长率经纬向差值(纬向–经向)
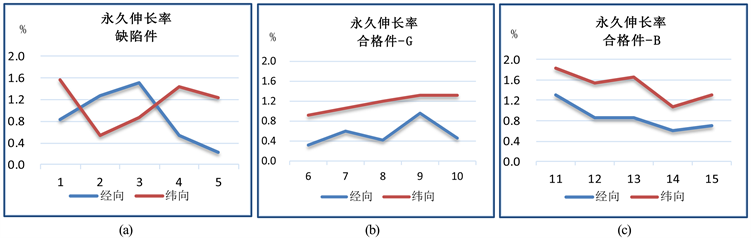
Figure 6. Different samples permanent elongation test result. (a) NOK Parts-G, (b) OK Parts-G, (c) OK Parts-B
图6. 不同样品永久伸长率测试结果。(a) 缺陷件-G,(b) 合格件-G,(c) 合格件-B
4. 结论
本文对PC3S工艺生产的门板中部插件PVC复合面料物理性能进行研究,结果表明静态伸长率及经纬向静态伸长率差值是影响制件表面缺陷的主要因素,在PVC复合面料经向静态伸长率为4.4%~9.0%,纬向静态伸长率为9.3%~12.9%。差值在2.6%~7.5%之间时,制件的表面质量良好。厚度、面密度、撕裂力、PVC表皮与泡沫、泡沫与衬布之间的结合力检测结果对制件表面质量影响不大,永久伸长率因其测量值较小,不作为衡量表面质量的重要指标之一。