1. 引言
油田进入中高含水期,油井因含水上升带来诸多问题。在开采成本不断攀升、采出水处理规模不断增大,环保压力日趋突出等问题,导致油井过早地停产或废弃,处理设备投入和操作费用攀升。加拿大Centre for Engineering Inc. [1] 于1991年进行了井下油水旋流分离和同井回注研究,并于1994年首次在Alliance油田进行了名为“ESP AQWANOT” (井下分离)的工业试验并获得成功。井下增压泵与油水分离技术相结合,形成井下油水分离同井注采系统,有效降低高含水期油藏开发的投入与成本,成为解决上述问题有效途径。
2. 井下分离技术及其工作原理
同井采油注水技术,简称同井注采,是指在同一油井中,当存在两个或两个以上不同地层时,产出液由一层或多层产出,利用井下油水分离装置对采出液进行油水分离,将低含水产液举升至地面,高含水产液回注注入层,在同一井筒内同时实现注入与采出。井下油水分离系统包括许多组成部分,但最主要的包括两部分,即油水分离器和提供举升动力和注入动力的泵。根据井下分离原理的不同,井下油水分离器主要包括重力分离式(主要与有杆泵组合作业)和水力旋流器两类。动力泵包括潜油电泵、螺杆泵、有杆泵及其组合。其中,以潜油电泵和螺杆泵为动力泵的结构形式应用最为广泛,技术也最为成熟。同井注采工艺技术可降低无效产液,降低举升能耗和地面处理成本,使高含水区块实现经济生产,可以使因高含水关停的井恢复生产。
2.1. 旋流分离技术
旋流分离是将液流的高速切向直线运动在旋流分离器几何结构的约束下转变成强旋转运动。在离心力的作用下,两种混合在一起且不互溶的液体中,重相介质沿外旋流向下运移至底流口排出;轻相介质顺内旋流沿溢流口排出。常规水力旋流器的主体结构包括入口、旋流腔、锥段、溢流管和底流管等。
旋流分离器的分离效果受结构选型、结构参数、分散相含量、介质粘度、密度差、入口压力及流量等等多因素影响。国内外学者对旋流分离器优化开展大量的研究工作。在结构形式及结构参数优化方面,贺杰 [2] 等曾经针对液-液水力旋流器入口、旋流腔长度、锥角大小、溢流口直径及溢流管伸入长度等参数进行了大量的对比实验。袁惠新 [3]、Thew [4] 及褚良银等对溢流管结构开展优化。美国的Petty [5] 等提出了反向流水力旋流器的结构形式,利用旋流腔的顶部增加的旋流稳定器结构实现水力旋流器同向出液的问题。在操作参数研究方面,倪玲英 [6] 等针对分流比对水力旋流器压力降和压降比的影响进行了研究,影响旋流器油–水分离性能,认为分流比的合理选择非常重要。舒朝晖 [7] 等研究了旋流器入口流量与旋流器边壁油滴粒径变化。文和平 [8]、蒋明虎 [9] 等在实验研究中对旋流器的压力降、入口压力、出口压力等参数开展模拟分析。
2.2. 重力分离技术
重力沉降法是利用油水密度差和不互溶性,在静止或者层流状态下实现油滴、悬浮物与水的分离。其特点是对任何浓度的含油污水都能进行处理,但其处理出水往往达不到排放标准,一般作为初处理。该类方法设备结构简单,易操作,除油效果稳定,可去除水中的浮油、部分的分散油,对溶解油或乳化油不适用。
曲占庆 [10] 等对重力式井下油水分离器的分离原理进行了研究,分析了在重力油水分离器中影响分离器效果的因素后,根据重力基本分离原理和重力分离器设计原则试制出一种新型的重力式油水分离器,并且进行了室内模拟实验。对分离器结构参数和混合液流态对油水分离效果的影响进行了深入研究,实验得出不同流态下合理的分离器结构设计原则。韩洪升 [11],崔海清 [12],杨树人 [13] 等对多杯等流型油水分离器进行了深入的研究,根据室内实验和理论分析,分析影响分离器分离效果的主要因素,对分离器结构、沉降杯形状进行了优化,设计出新型多杯等流型油水分离器,该分离器分离效果明显,可以提高原油产量,降低含水率。
3. 国内外同井注采技术现状
3.1. 国外研究及应用现状
截止目前,国外许多大的石油公司开发了诸多井下油水分离设备以减少采油成本和处理采出水费用,如加拿大工程研究中心(C-FER)、美国Vortoil公司、美国Reda公司等。美国、法国、德国、加拿大及俄罗斯等国均进行同井注采工艺的理论研究和现场试验。自1994年由水力旋流分离器和电潜泵组成的同井注采工艺首次在Alliance油田试验时起,同井注采技术已进行多口井的现场试,般采用水力旋流式同井注采工艺和重力式同井注采工艺。Veil及Voss [14] 等人统计美国及加拿大同井注采工艺应用59口井。其中,三分之二的采用重力分离型井下分离器。统计井数中30口井生产层为碳酸盐岩层,24口井产层为砂岩地层。19个井下分离注入层位为碳酸盐岩层,32口井的注入层为砂岩。试验井中,19口井原油产量上升,12口井产量下降。采用水力旋流式油井产量增幅达432%~1162%。重力分离同井注采应用油井产量增长幅度从106%~233%。虽然国外在同井注采技术研发应用逐渐成熟,但是在应用同时也暴露出同井注采工艺管柱寿命、油水分离效果差、难以实现长期有效注入等问题。
3.2. 国内研究现状
从20世纪末开始就有部分高校及石油企业联合起来进行同井采注的项目研究。东北石油大学、中国石油大学(华东)、江汉石油机械研究所、大港油田设计院等在文献收集分析、基础理论及室内实验方面开展初步研究。胜利油田、中海油、辽河油田、大庆油田等均在同井注采工艺上开展相关研发与应用。但由于各自工艺需求及目标储层差异性,形成了不同特点的同井注采工艺。
2004年,胜利油田采用抽油机与水力旋流分离相结合进行一口同井注采井现场试验,该工艺初期见到了很好的效果,地面产液量降低,受效井增液变化明显。连续运转3个月后由于出砂严重、井口被冻、设备损坏和资金短缺等原因将整套系统起出。
2007年,河南新庄油田、渤海油田、冀东油田先后开展双电泵同井注采工艺试验。其中渤海油田在7寸套管生产井采用电潜泵与水力旋流分离相结合的注采工艺,现场试验4口井。
2012年至今,大庆油田依托863项目开展有杆泵同井注采,双螺杆泵同井注采及螺杆泵采电泵注的组合同井注采工艺,现场试验24井次以上,成为国内目前推广试验井数最多的油田。
4. 同井注采技术类型及其应用情况
常见井下油水分离系统按动力泵的选取不同可分为潜油电泵井下分离系统、螺杆泵井下分离系统和双流泵井下分离系统。其中,以潜油电泵和螺杆泵为动力泵的结构形式应用最为广泛,技术也最为成熟,可在现有设备基础上进行改造。近年来双液流泵的研发,也在国外井下油水分离系统中得到了一定的应用。下面依次对以潜油电泵、螺杆泵及双液流泵为动力泵的三大类井下油水分离系统的组成及工作原理进行简要介绍。
同井注采工艺在美国、加拿大、俄罗斯及我国应用报道较多,其中美国主要采用水力旋流与电潜泵组合的工艺,二俄罗斯发展螺杆泵注采为主的工艺,我国引进吸收条件下逐渐形成电潜泵、螺杆本及有杆泵三种动力主体的同井注采工艺。
4.1. 电潜泵同井注采工艺
电潜泵同井注采工艺适用于产液量较大的高含水油井,利用旋流式井下分离后经电泵举升和诸如底层,实现同井注采。根据电泵及电机数量不同,电潜泵/旋流分离器井下油水分离方案可分为以下三种。
4.1.1. 单泵单电机同井注采工艺
单泵单电机同井注采工艺由一个电潜泵、旋流分离器和封隔器等组成(图1)。经产层产出流体经电潜泵增压,进入井下水力旋流分离器实现油水分离,低含水产出液从旋流器上溢口进入油管并举升至地面;高含水产出液经底流口注入注水层位。该系统中注入和举升的能量均由同一台电泵提供。该工艺优点是结构相对简单,成本较低,但是由于产出液经电泵后易形成乳化,旋流分离效果不理想。
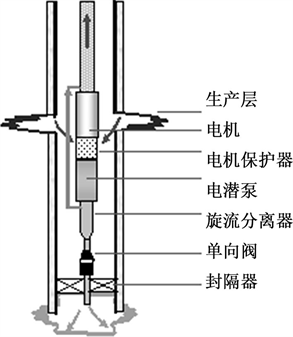
Figure 1. Schematic diagram of a single-pump single-motor downhole oil-water separation system
图1. 单泵单电机井下油水分离系统示意图
4.1.2. 双泵单电机同井注采工艺
双泵单电机系统由两个电潜泵、旋流分离器和封隔器等组成(图2)。一台电机驱动两个电泵。根据旋流器与注水泵的连接方式的不同可以分为两种方案,于旋流器的上游,则称压进式;若泵安装于旋流器的下游,则称为抽吸式。因此双泵单电机同井注采工艺包括两种:①产出流体进入下端注入泵经增压后进入旋流器分离,其低含水产出液进入上端采油泵举升到地面,高含水产出液直接注入注水层。②产出液旋流器分离,从旋流器上出口溢出低含水产出液进入上端采油泵举升至地面,旋流器底部流口流出的富高含水产出液进入下端注入泵增压后注入注水层。双泵工艺适用于排量高,举升能量要求大的深井。
4.1.3. 双泵双电机同井注采工艺
双泵双电机同井注采工艺采用两套电泵及两套电机(图3)。产出液经旋流器分离后,低含水产出液经上端采出泵举升至地面,高含水产出液经下端注入泵注入注水层。该工艺实现先旋流分离,后分别经两个不同的井下电潜泵增压,适用于深井及注入压力要求较高的高产液量井。
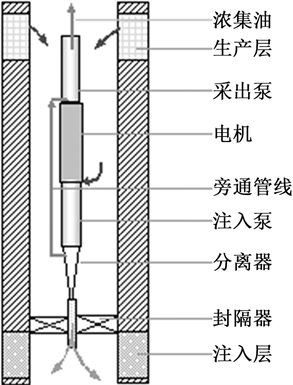
Figure 2. Schematic diagram of a dual-pump single-motor downhole oil-water separation system
图2. 双泵单电机井下油水分离系统示意图
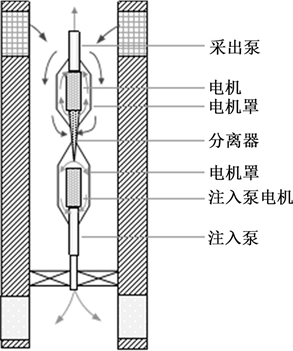
Figure 3. Dual-pump dual-motor downhole oil-water separation system
图3. 双泵双马达井下油水分离系统
4.2. 螺杆泵同井注采工艺
4.2.1. 单螺杆泵同井注采工艺
单螺杆泵同井注采工艺由采出螺杆泵、水力旋流器、注入螺杆泵、动力传递系统等组成(图4)。产出液经产出层产出,进入井下水力旋流器分离,在旋流分离器中低含水流体经旋流器上溢口经旁通管进入油管举升至地面。高含水流体经旋流器底流口进入动力泵增压注入注水层。
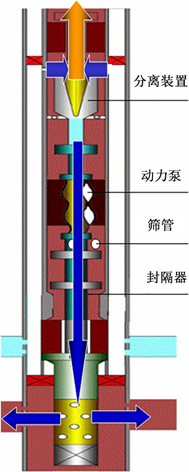
Figure 4. Single screw pump injection and production process in the same well
图4. 单螺杆泵同井注采工艺图
4.2.2. 双螺杆泵同井注采工艺
双螺杆泵同井注采工艺通过双层油管结构的井下多层封隔工艺管柱保证产层和注入层的封隔 [15],利用联轴器带动条件下地面泵同时驱动两个同轴螺杆泵分别进行分离液的举升和回注。其具体结构见图5。
4.3. 有杆泵同井注采工艺
4.3.1. 重力分离 + 双作用泵同井注采工艺
双作用泵同井注采工艺采用井下封隔器将生产层和注入层由分隔,由一台双作用泵提供举升和注入能量。油井产出液在井筒中进行重力分离,使双作用泵的柱塞上部位于富含油区,下部位于富含水区。来自生产层的油水混合液在油套环形空间内利用重力沉降分离。上冲程时上泵腔举升浓集油,下泵腔吸入分离水(图6(a));下冲程时上腔吸入浓集油,下腔在抽油杆柱及环空动液面压力作用下注分离水(图6(b))。
该系统适用于动液面高注入压力较低,生产层和注入层相距较大的油井。在使用中,除单作用泵存在的下行阻力外,还会产生由于上下柱塞面积差而引起的附加下行阻力。随着面积差的增大和沉没度的
减小,附加下行阻力将会增加。对于注水量或注入压力高和沉没度低的井容易发生抽油杆下部弯曲,下行阻力过大,下行困难而出现难以维持生产的情况。
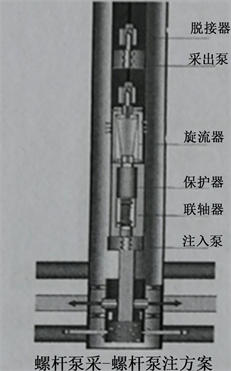
Figure 5. Twin-screw pump injection and production process in the same well
图5. 双螺杆泵同井注采工艺图
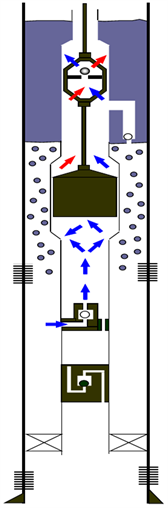
Figure 6. Double-action pump downhole oil-water separation system
图6. 双作用泵井下油水分离系统
4.3.2. 重力分离 + 双凡尔串联泵同井注采工艺
双凡尔串联泵同井注采工艺 [16] (图7)由双凡尔串联泵和封隔器组成。双凡尔串联泵中密封柱塞将泵体分为上下两个单作用泵,上下冲程中分别驱动泵体上下泵腔和凡尔工作。在重力分异条件下,上冲程过程中上泵吸入低含水产出液,下泵吸入高含水产出液。下冲程时上泵腔排出低含水产出液至地面,下泵腔排出高含水产出液至注入层。
该工艺中上下泵的柱塞直径相同,消除了柱塞面积差带来的附加阻力,但会增加上行悬点载荷。如减小下泵柱塞直径将会有助于提高注入压力,但会减小注入量。
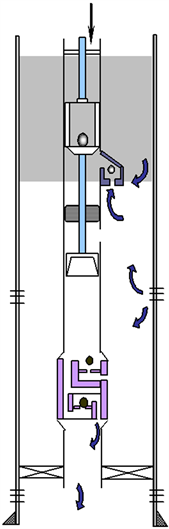
Figure 7. Double-valve series double-pump system
图7. 双凡尔串联双泵系统
4.3.3. 旋流分离 + 双作用泵同井注采工艺
旋流分离双作用泵同井注采工艺由旋流分离器、抽油注水双作用泵组成(如图8)。产层产出液经液固分离固相,后经旋流分离成高含水产出液和低含水产出液。抽油注水双作用泵上冲程过程中吸入高含水产出液至泵体,排出低含水产出液至地面;下冲程过程中排出高含水产出液至注入层,吸入低含水产出液至泵体。
4.4. 螺杆泵采电潜泵注组合同井注采工艺
如图9,螺杆泵采电潜泵注组合同井注采工艺主要由采出螺杆泵、水力旋流器、倒置注入电泵等组成。该工艺采用电泵注入,提升注入液量与注入压力;注入与采出为两套独立系统,与分离设备可调配性能高,保证了高效分离。
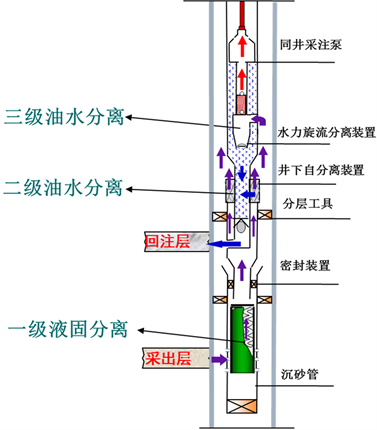
Figure 8. Cyclone separation + double-acting pump injection and production process in the same well
图8. 旋流分离 + 双作用泵同井注采工艺
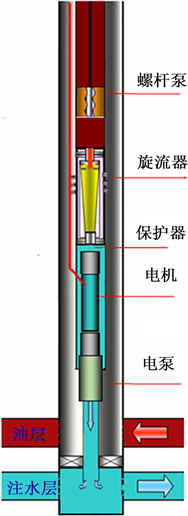
Figure 9. Screw pump production electric submersible pump injection combination with the same well injection production process
图9. 螺杆泵采电潜泵注组合同井注采工艺
5. 井下油水分离技术发展及应用的关键问题
同井注采技术因其具备降低采油成本,减少石油和天然气业务对环境影响,降低饮用水地下水源污染,节省地面投资方面等多方面的优势,但是因其应用过程中仍存在诸多制约,经多年发展仍未能大规模推广应用。
5.1. 井下油水分离技术研究面临的技术难点
井下油水分离同井回注技术是中高含水期解决水处理问题以及环境问题的关键技术之一。但是,由于涉及的系统较复杂,并且该项技术现在尚不能在油田推广使用,许多技术还尚有待于进一步完善。根据调研情况,在井下进行油水分离和同井回注也存在着诸多不足
1) 由于井下分离难以达到地面分离的效果,注入水中通常会含有目的层难以满足长期的注水水质达不到我国现行水质控制指标,应充分估计水中含油浓度和固体悬浮物超标对油田生产的长远影响。
2) 从实际应用来看,井下分离、同井回注的工作质量监控上还有待加强。其注入水含油浓度难以监测。
3) 井下分离设备安装后,油井生产和注水参数调节余地很小,尤其是单井注水压力及注水量可调控程度受限。
4) 由于完井和修井作业费用昂贵,所以应提高井内设备可靠性和使用寿命。另外,应对井筒内各种参数进行监控和自动调节,即研制一套完善的智能系统 [17] [18]。
5.2. 应用过程中失效原因分析
1) 注入问题 [19]。为了使同井注采工艺正常工作,注水层必须具有足够的渗透性和孔隙度。注水层的较差注入性,不匹配的流体注入或注入参数导致的砂粒运移等都是影响注入性的关键。
2) 封隔问题。为了保护产层及地下水,注入层上下的固井质量必须达到要求,以封隔上下的生产层或地下水。另外,隔层厚度较小时难以满足注水时引起层间压力差而形成窜层。
3) 堵塞问题。储层出砂、结垢等问题会带来注入储层的堵塞问题。
4) 腐蚀与结垢。矿场实践表明腐蚀和结垢问题广泛存在。
5) 设计缺陷。只有两名操作员报告了工具设计的问题。Chevron在Rangely矿场试验 [20] 表明由于泵选型偏小导致试验失败。Southward实验表明其分离室太短导致井下分离效果不理想。
6. 应用前景展望
1) 近年来国内外同井注采技术逐渐由早期试验开始推广应用,形成了以旋流分离及重力分析两种井下分离方式为主要分类的有杆泵同井注采工艺、电泵同井注采工艺、螺杆泵同井注采工艺以及螺杆泵和电泵组合同井注采工艺
2) 同井注采工艺在应用过程中表现出其局限性,研究者也正在研发新型的同井注采工艺,比如新型重力和聚结组合分离器 [21],水力旋流器和改进泵送耦合系统 [22],表面涂覆磁性纳米粒子提高井下油水分离效果 [23],井下水锥控制技术 [24],叶片式管道分离器 [25],可应用于井下各种膜基油水分离技术 [26] 等。
7. 结论
1) 经多年发展,国内外发展了电潜泵、射流泵和有杆泵为动力,旋流分离和重力分离为分离方式的同井注采工艺。
2) 同井注采工艺在降低采油成本,减少石油和天然气业务对环境影响,降低饮用水地下水源污染,节省地面投资方面等多方面存在优势,具有较好的应用前景。
3) 受地质条件、油藏认识及工艺成熟度等影响,同井注采工艺仍存在诸多难点。但国内外研究者围绕关键问题持续攻关将为其应用提供更好的选择。
基金项目
国家科技重大专项(2016ZX05053-002)。
NOTES
*通讯作者。