1. 引言
随着“中国速度”的快速发展,对航天、航空等领域所使用的高温轴承材料提出了更高的挑战。因为高温轴承所处的工作环境十分恶劣。例如:航空发动机压缩机和主轴处使用的滚动轴承我们通常称为主轴轴承,主轴轴承的温度高达300℃,接触应力也在2 Gpa以上。正是因为航空发动机所处的运行工况环境十分的苛刻复杂,所以使得高温轴承容易发生磨损失效,轴承一旦发生失效,会导致传动系统的精度降低,从而振动急剧增大,容易造成重大事故。Ni3Al-Ni3V是新型镍基超超合金,具有高蠕变断裂寿命、高硬度、低热膨胀系数和高导热性,而且在宽温度范围内具有高拉伸强度、高断裂韧性和≥2 %室温拉伸延伸率 [1] [2]。目前,Ni3Al-Ni3V主要在以下3个领域展现了应用前景:1) 作为高温滚珠轴承的内圈和外圈应用于发动机,使用寿命较SUS440C提高了20倍 [3]。2) 等离子渗氮Ni3Al-Ni3V作为搅拌摩擦焊的焊头,焊接SS400和SUS430,焊头的肩部没有磨损,搅拌针的形状没有变化 [4] [5],也没有污染的现象。3) 作为粘结剂,替代Ni和Co制备硬质合金 [6],常温~900℃的硬度均高于Co-TiC硬质合金。
由于Ni3Al-Ni3V合金磨损性能的国内外研究报道比较少,又考虑到前期研究发现Ni3Al在室温下会发生环境致脆特性 [7] [8],磨削加工工件容易导致表面裂纹而报废。因此,本文作者以Ni3Al-Ni3V合金为研究对象,系统分析了合金在不同载荷、不同速度下的摩擦磨损性能与机理,并且为了进一步提高Ni3Al-Ni3V合金的摩擦磨损性能对合金做了表面渗碳处理,为Ni3Al-Ni3V合金应用到高温轴承领域中提供了参考。
2. 试验材料与方法
2.1. 试验材料
实验选取高纯Ni、高纯Ni-B、高纯Al和高纯Al-V为原料,按名义成分75Ni-8.5Al-16.5V (at.%)配置含有0.001 wt.% B的Ni3Al-Ni3V合金,合金在高真空电弧炉中熔炼成合金铸锭,为了保证化学成份的均匀,对合金锭反复熔炼3次以上。采用线切割方法切取厚度为4 mm的合金试样,表面磨至1200#砂纸,抛光。采用固溶时效工艺(1100℃ × 48 h → 1000℃ × 24 h)和气体渗碳工艺(950℃ × 48 h) 处理合金试样。试样抛光后,经丙酮 + 乙醇超声波清洗,烘干待用。
2.2. 试验设备及参数
测试合金的摩擦磨损性能所用的试验设备为HRS-2M型往复磨损试验机。试验在室内温度26℃、空气湿度70%的大气环境下进行。与合金对磨的试件为Si3N4陶瓷球,在试验设备的控制板块设置其加载条件,测试载荷为10 N和45 N滑动速度分别为0.05 m/s、0.1 m/s、0.2 m/s,单次往复滑动距离为10 mm,实验时间为30 min。取摩擦系数稳定后的平均值,磨损体积由NanoMap-500LS型三维接触式表面轮廓仪测量,按照公式W = V/(F∙L) (W为磨损率,V为磨损体积,F为载荷,L为滑动距离)计算磨损率。取三次试验结果的均值。
2.3. 分析设备
采用配置了能谱仪(EDS)的S-3400N扫描电子显微镜(SEM)观察Ni3Al-Ni3V合金的微观组织及磨损表面和横截面形貌。利用D/Max-RB型X射线衍射仪分析Ni3Al-Ni3V合金的相组成。合金的硬度用HV-1000数显显微硬度计测量,加载时间为15 s,载荷为50 g,取五次试验结果的均值。
3. 实验结果
3.1. Ni3Al-Ni3V合金的显微组织与硬度
图1是Ni3Al-Ni3V合金的SEM组织图片。从图1(a)可以看出,固溶Ni3Al-Ni3V合金的组织由网状的黑色相和块状的白色相构成,XRD (图1(f))和EDS分析表明,白色相为Ni3Al相,黑色相为Ni3Al + Ni3V复合相,其中,Ni3Al为软相,Ni3Al + Ni3V复合相为硬相 [1] - [6]。渗碳Ni3Al-Ni3V合金表面呈现出白色块状形貌和黑色片状或块状形貌(图1(b)),XRD (图1(f))分析表明,主要存在Ni3Al、Ni3V、V2C相、Al4C3相和少量的Ni相;高倍SEM图片可以发现,白色块状表面主要由短棒状V2C相 [9] 构成(图1(c)),黑色块状表面主要由堆簇起来镶嵌在块状Al4C3相 [10] 中的短棒状V2C相组成(图1(d));从横截面可以看出(图1(e)),合金表面生成了厚约4 μm的碳化物层和约6 μm的富Ni相过渡层,渗碳组织致密,与基体合金结合良好。
从表1 Ni3Al-Ni3V合金的表面硬度,可以看出:Ni3Al-Ni3V合金的硬度高于Ni3Al合金,这是由于Ni3Al + Ni3V复合相的强化导致的;V2C的硬度超过了2000 HV [11],然而,固溶Ni3Al-Ni3V合金的硬度高于渗碳Ni3Al-Ni3V合金,这可能是由于碳化物层较薄,棱锥状的压头压破碳化物层,压入硬度较低的富Ni相过渡层导致的。
3.2. Ni3Al-Ni3V合金的摩擦磨损性能
图2所示为Ni3Al-Ni3V合金的摩擦磨损性能曲线。从图2(a)可以发现:不同载荷下,合金的摩擦系数随着滑动速率的增加而降低;渗碳Ni3Al-Ni3V合金的摩擦系数低于固溶Ni3Al-Ni3V合金,这是由于V2C和Al4C3构成的碳化物层具有较高的硬度和弹性模量,磨损中其弹性变形及实际接触面积均较小导致的 [12]。从图2(b)可以发现:渗碳Ni3Al-Ni3V合金的磨损率低于固溶Ni3Al-Ni3V合金,表明表面渗碳可以有效地强化Ni3Al-Ni3V合金的耐磨损特性;然而,高载荷和高滑动速度下,渗碳Ni3Al-Ni3V合金发生耐磨损特性不足的问题。
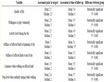
Table 1. Hardness of Ni3Al-Ni3V alloy
表1. Ni3Al-Ni3V合金的硬度
(a) Ni3Al-Ni3V合金组织 (b) 低倍渗碳Ni3Al-Ni3V合金表面形貌
(c) 高倍渗碳Ni3Al-Ni3V合金表面白色块状形貌 (d) 高倍渗碳Ni3Al-Ni3V合金表面黑色块状形貌
(e) 渗碳Ni3Al-Ni3V合金横截面 (f) XRD
Figure 1. Microstructure and XRD pattern of Ni3Al-Ni3V alloy and carburized Ni3Al-Ni3V alloy
图1. 标准试验系统结果曲线
(a) (b)
Figure 2. Friction and Wear Properties of Ni3Al-Ni3V alloy and carburized Ni3Al-Ni3V alloy
图2. Ni3Al-Ni3V及渗碳Ni3Al-Ni3V合金的摩擦磨损性能
3.3. Ni3Al-Ni3V合金的磨损表面形貌分析
图3为固溶Ni3Al-Ni3V合金的磨损表面形貌。可以发现,10 N + 0.05 m/s下,合金磨损表面呈现犁沟、剥落和裂纹特征(图3(a)),高倍磨损表面呈现显著的平行和垂直于磨损方向的裂纹(图3(b))和轻微的粘着磨损特征,剥落是以薄片形状脱离母材的,发生了磨损环境脆性 [7] [8] [13];随滑动速度的提高,磨损表面粘着磨损特征增强,犁沟、剥落与裂纹特征减弱(图3(c)和图3(d));随载荷的增加,磨损表面呈现犁沟、粘着、剥落和裂纹特征(图3(e)),高倍磨损表面呈现显著的擦伤特征(图3(f)),这是由于在高载荷下,真实接触面积占更大可利用的表观接触面积,以致松散的磨损粒子一旦生成就无法脱离开,故擦伤了Ni3Al-Ni3V合金 [12]。当45 N + 0.1 m/s时,随滑动速度增加,磨损表面粘着、剥落与裂纹特征增强,犁沟特征减弱(图3(g)和图3(h))。
(a) 10 N + 0.05 m/s (b) 10 N + 0.05 m/s高倍SEM
(c) 10 N + 0.1 m/s (d) 10 N + 0.2 m/s
(e) 45 N + 0.05 m/s (f) 45N +0 .05 m/s高倍SEM
(g) 45 N + 0.1 m/s (h) 45 N + 0.2 m/s
Figure 3. Wear surface morphology of Ni3Al-Ni3V alloy
图3. Ni3Al-Ni3V合金磨损表面形貌
图4为渗碳Ni3Al-Ni3V合金的磨损表面形貌。可以发现,10 N + 0.05 m/s下,合金磨损表面呈现犁沟特征(图4(a));随滑动速度的提高,磨损表面环境脆性特征逐渐增强(图4(b)和图4(c)),这说明磨损深度到达了Ni3Al-Ni3V基体;随载荷的增加,磨损表面犁沟特征增强(图4(d)),并呈现轻微的粘着磨损特征,EDS分析表明,磨损深度到达了富Ni相过渡层。当45 N + 0.1 m/s时,磨损表面粘着、剥落与裂纹特征增强,犁沟特征减弱,并出现环境脆性特征(图4(e)和图4(f)),这可能是由于表面碳化物层和富Ni相过渡层已被磨掉,磨损发生在Ni3Al-Ni3V表面,故随滑动速度的提高,环境脆性特征增强,相应的磨损率与Ni3Al-Ni3V合金相近。
(a) 10 N + 0.05 m/s (b) 10 N + 0.1 m/s
(c) 10 N + 0.2 m/s (d) 45 N + 0.05 m/s
(e) 45 N + 0.1 m/s (f) 45 N + 0.2 m/s
Figure 4. Wear surface morphology of carburized Ni3Al-Ni3V alloy
图4. 渗碳Ni3Al-Ni3V合金磨损表面形貌
4. 分析与讨论
4.1. Ni3Al-Ni3V合金的磨损环境脆性机理
根据李玉芳 [14] 等的研究发现金属化合物Ni3Al合金在大气环境中呈现严重的环境脆性是由空气中的水汽诱发的,并且含Ni3Al相的镍基超合金在氢气环境中会发生氢脆的现象 [15] [16] [17]。脆化步骤有:空气中的水分子同Ni3Al中的Al元素发生表面反应 [18] [19] [20]:2Al + 3H2O → Al2O3 + 6H形成的原子H和原子H不断向合金内部扩散并聚集到裂纹尖端塑性区,从而造成合金具有沿晶界断裂趋势或脆性穿晶断裂。所以暴露在大气中的Ni3Al表面只有同水汽发生反应生成原子态H才会导致环境脆性,并且Ni3Al有对水汽诱发的环境致脆敏感性高的特征。Ni3Al-Ni3V合金的室温磨损环境脆性可能是因为Si3N4陶瓷球的连续挤压产生塑性变形和表面微凸体的犁沟作用,Ni3Al-Ni3V合金不断地有“新”表面暴露在环境中。空气中的水汽通过吸附作用与“新”表面接触,合金中的Ni3Al相的活泼原子Al与它发生化学反应生成原子H,原子H逐步向合金内部扩散聚集;当磨损接触区的交变应力大于合金的疲劳极限时,材料表面将引起裂纹萌生,原子H在应力作用下聚集在裂纹尖端塑性区并且引发脆化。磨损表面产生的原子H逐步扩散并聚集,同时破坏了Ni3Al-Ni3V合金磨损表面的完整性,经原子H脆化后的合金表面疏松,很快被Si3N4陶瓷球磨掉增加了合金材料的损失量 [21]。
合金对环境敏感性的主要影响因素是合金中的活泼金属组元及其含量。在磨损过程中,合金的一活泼组元与水汽发生反应的化学方程式如下:
(1)
其中A为活泼金属组元元素,x,y为化学方程式系数。上式化学反应发生的难易程度可以用来评价合金中活泼组元的环境敏感性,通过计算化学反应的Gibbs自由能变化
,则合金活泼组元环境敏感性高 [22]。
Ni3Al-Ni3V合金中主要组成元素与水汽反应生成氧化物的Gibbs自由能变化如表2所示。可知Ni3Al-Ni3V合金中Al和V元素的Gibbs自由能变化
,属于环境敏感性高的元素。所以,合金磨损过程中,暴露在大气中的“新”表面上的活泼组元与水汽发生反应,析出高逸度的原子态H,从而导致环境脆性。
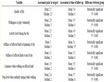
Table 2. The main component of the alloy representative Gibbs free energy of oxide formation
表2. 合金主要组元的代表性氧化物生成Gibbs自由能
对于二元以上合金,其环境敏感性与活泼组元的敏感性和含量有关。若合金中含有对环境不敏感的不活泼组元,则合金的环境敏感性与活泼组元和不活泼组元的相对含量有关。二元合金与水汽发生反应可用。下式来表述 [22]:
(2)
其中A,B为合金中不同的组元,x,y,r,t,u,v为化学方程式系数。Ni3Al-Ni3V合金中不同组元对环境敏感性程度也大不相同(表2),其中合金Ni元素所占的原子百分比达75%,Ni与H2O发生反应生成NiO的Gibbs自由能变化为26 KJ/mol (表2),属于环境不敏感元素。
考虑到Ni3Al-Ni3V合金中Al的Gibbs自由能最小(−290 KJ/mol),环境敏感性最高,所以将合金中Ni, Al两组元代入(2)式得:
(3)
由(3)式和元素守恒(物料守恒)得:
(4)
令反应方程式的
,反应处于平衡状态,则得到合金中环境敏感的Ni-Al临界含量比,其中H2O,Al2O3和NiO常温标准状态下Gibbs自由能分别为−237.13 KJ/mol,−1582.3 KJ/mol,−211.7 KJ/mol [23]。代入到(3)式中得:
(5)
联立(4)和(5)可计算Al的临界含量为5.53 at.%。试样Al元素占Ni3Al-Ni3V合金原子百分比为8.5%,Al + V元素原子百分比之和达到25%,所以,Ni3Al-Ni3V合金对大气中的水汽敏感性高,磨损过程中敏感组元易与水汽发生反应导致环境脆性。
鉴于Ni3V是以Ni3Al + Ni3V复合相的组织结构分布在合金基体中,因而,Ni3V对合金的环境脆性的作用机制还有待于进一步设计实验进行研究。
4.2. Ni3Al-Ni3V合金的粘着磨损机理
Si3N4硬度高,具有良好的抗粘着特性,当Si3N4表面微凸体犁削合金磨损表面形成的软金属Ni3Al-Ni3V磨屑逐渐积累在Si3N4陶瓷球表面上时,最终使陶瓷球与Ni3Al-Ni3V之间的滑动变成Ni3Al-Ni3V与Ni3Al-Ni3V之间的滑动,这时结点与两个表面皆为同一金属,然而变形和熔接会使结点硬化并使其剪切强度显著提高,故剪切很少发生于界面之间,而是在软金属Ni3Al-Ni3V中进行,所以,磨损表面损伤和磨损都很高 [12]。
5. 结论
1) 固溶时效处理的Ni3Al-Ni3V合金由软的Ni3Al相和硬的Ni3Al + Ni3V复合相组成。渗碳Ni3Al-Ni3V合金表面生成厚约4 μm的碳化物层和约6 μm的富Ni相过渡层,碳化物层由短棒状V2C相和镶嵌在块状Al4C3相中的短棒状V2C相组成,组织致密,与基体结合良好。
2) Ni3Al-Ni3V合金和渗碳Ni3Al-Ni3V合金的摩擦系数和磨损率随滑动速率的增加而降低,渗碳Ni3Al-Ni3V合金的表面碳化物层具有较高的硬度和弹性模量,提高了合金的摩擦磨损性能。
3) Ni3Al-Ni3V合金对环境中水汽敏感,磨损过程中易与水汽反应产生环境脆性,Al的临界含量为5.53 at.%。随着载荷和滑动速度的增加,合金的磨损机制由磨粒磨损和环境脆性转变为粘着磨损,渗碳Ni3Al-Ni3V合金的碳化物层和富Ni相过渡层逐渐被磨掉后,也发生了环境脆性。
基金项目
本文研究工作得到了“国家自然科学基金项目(51101055)”、“湖南省自然科学基金项目(2020JJ4312)”提供的资助。
NOTES
*通讯作者。