1. 引言
高强度钢广泛应用于航空航天特别是军事工业等领域,属于难加工材料。在传统切削加工工艺中,切削加工总量的1/3约是孔加工,钻削是孔加工工艺中最经济和高效的方法,可以提高加工效率降低加工成本,对机械制造业的发展和国民经济稳定增长有着十分重要的意义 [1]。钻削加工中关键的问题是如何合理的选择钻削工艺参数,通过控制切削力来保证钻削工件的质量寿命及加工效率。因此,对于钻削加工的切削力的研究成为国内外学者的研究热点。王凯旋 [2] 等人利用DEFORM软件对钛合金微孔加工的钻削力建立了一种能够精确预测钻头所受钻削力的切削力模型。马未未 [3] 等人利用DEFORM软件对于高速钢钻削进行了仿真分析,得到不同进给量下的轴向力、转矩及温度的仿真结果。许明三 [4] 等人从切削参数和刀具角度方面对难加工材料的切削性能进行研究。于凤云 [5] 等人通过对高强度钢的切削加工试验得出群钻可以使切削力和扭矩减小。冯光 [6] 利用ABAQUS对碳纤维复合材料进行钻削建模,并通过试验验证,钻削速度、进给速度、钻头直径对钻削力的影响。D. Mai [7] 利用3D CAD建立了一种钻削力模型,可以应用于CFRP的加工。Xiaoye Yan [8] 提出一种CFRP钻削加工的力学模型,总结出了切削深度、刀具角度、纤维趋向等因素之间的关系。Stephenson和Agapiou [9] 研究了钻削灰铸铁时,通过参数化方法结合切削试验的经验切削力模型,得到扭矩和轴向力的计算结果。Hiroyuki Kodama [10] 等人通过改变进给量、转速和进给速度,测量推力和切削温度,研究了切削条件对不锈钢小直径深孔钻进性能的影响,得到每刃进给量和进给速度相结合可以降低钻削过程中的轴向力和钻削时间。
尽管国内外的学者对不同种材料的钻削切削力进行了多方面的研究和分析,取得了一些研究成果。但对于高强度钢钻削加工的切削力研究还相对较少。为此,本文以钻削加工高强度钢的仿真分析和试验验证为基础,研究切削速度、进给量以及钻头直径这三个工艺参数对切削力及扭矩的影响规律,为提高工件的质量寿命及加工效率提供理论基础。
2. 钻削切削力仿真
2.1. 有限元仿真模型的建立
金属切削过程是刀具与工件相互运动,相互作用的过程,其中刀具和切削层会产生推挤,剪切及摩擦等作用,两者发生热-弹-塑性变形,伴随大应变和高温状态下的大塑性变形而发生断裂达到去除的效果。有限元法不但能计算塑性加工过程中的力能消耗,还能计算变形的应力和应变分布,客观地反映出切削区域切屑形态,刀具磨损等问题。有效地节约了试验时间,降低试验耗费。本文基于AdvantEdge有限元软件建立了钻削加工仿真模型,工件材料选用34CrNi3MoV高强度钢,刀具为硬质合金麻花钻头。由于材料的高温变形反应不明显,同时又存在高应变断裂,变形的情况,所以根据材料的应力曲线 [11] 定义该材料本构模型为P-L模型,刀具及工件的网格划分选择四面体网格,建立麻花钻头模型,进而仿真钻削加工的切削过程。
2.2. 单因素仿真试验
本试验选择单因素控制变量法,在保证其它两个切削参数不变的情况下,准确分析当前工艺参数对切削力和扭矩的影响,钻削仿真工艺参数及刀具几何参数如表1所示。
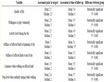
Table 1. Drilling simulation process parameter and tool geometry parameter table
表1. 钻削仿真工艺参数及刀具几何参数表
钻削仿真的三向切削力和扭矩的后处理结果,如图1所示。钻削加工中,三个方向的切削分力中轴向力最能反映钻削加工过程的实质,因此对仿真模型进行计算分析后,得出不同工艺参数下的轴向力和转矩。
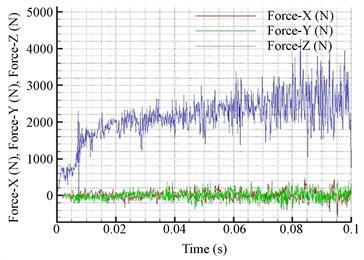
Figure 1. Three-dimensional cutting force and torque simulation results
图1. 三向切削力和扭矩仿真结果
当D = 10 mm,f = 0.2 mm/r时,得出不同切削速度下的轴向力和扭矩;当D = 10 mm,v = 55 m/min时得出不同进给量下的轴向力和扭矩;当v = 55 m/min,f = 0.2 mm/r时,得出不同刀具直径下的轴向力和扭矩,具体数据如表2所示。
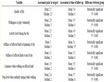
Table 2. Single factor test data table
表2. 单因素试验数据表
3. 钻削切削力试验
3.1. 正交试验
钻削加工切削力和扭矩试验选用的机床设备为VMC850E立式加工中心,试验工件材料为高强高硬34CrNi3MoV合金钢,其尺寸规格为:长180 mm,宽120 mm,高70 mm。刀具采用GD系列的外冷型整体硬质合金麻花钻。应用正交试验法 [12] 进行钻削高强度钢切削试验,采用L9 (34)标准正交表正交试验表,如表3所示,分别考虑切削速度v、进给量f以及钻头直径D工艺参数对切削力和扭矩的影响规律。采用瑞士Kistler公司生产的9257B三向动态压电式平板测力仪和5070A型多通道电荷放大器作为信号放大装置,采样频率2000 Hz、测量范围0~5000 N,对钻削的切削力和扭矩进行检测,最后通过DynoWare软件分析得到需要的相关数据,试验中设置外冷切削液。
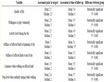
Table 3. Orthogonal test table
表3. 正交试验表(L9 (34))
3.2. 试验结果
在DynoWare软件中对各个试验参数下采集到的切削力和扭矩进行截断,去漂移等相关操作,得到如图2所示的钻削轴向力和扭矩的信号图(切削条件为D = 10 mm,v = 55 m/min,f = 0.20 mm/r)。从图2中可以看出当钻头与工件接触后切削力迅速上升,达到稳态切削后在稳定值处波动,当刀具退出切削时,切削力迅速下降到初始值。同理得扭矩的信号变化图。采用极差分析的方法对钻削切削力正交试验结果进行分析,用切削速度v、进给量f以及钻头直径D这三个工艺参数,将轴向力和扭矩的各个钻削参数的主次顺序用极差大小顺序排列出来,其结果如表4所示。
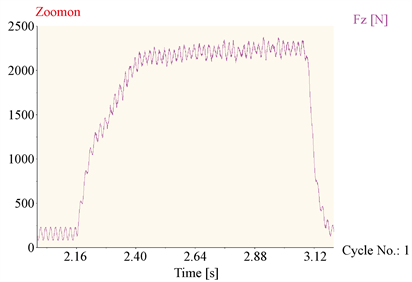
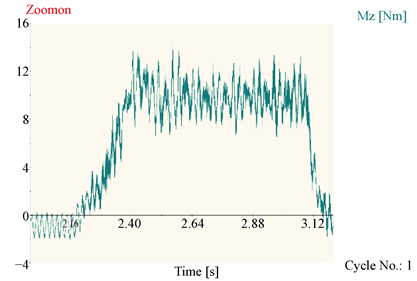
Figure 2. Signal diagram of axial force and torque
图2. 轴向力和扭矩的信号图
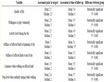
Table 4. Analysis table of extreme difference of drilling and cutting force test results
表4. 钻削切削力试验结果极差分析表
对采集到的数据进行极差分析后,得到切削参数对切削力的影响因素的主次顺序,影响切削力主要因素为钻头直径,其次为进给量和切削速度。从表4中得到最优参数组合为钻头直径D = 4 mm,进给量f = 0.25 mm/r,切削速度v = 70 m/min。
4. 仿真和试验结果对比分析
4.1. 切削速度v对切削力及扭矩的影响
图3所示为不同转切削速度下钻削轴向力和扭矩的仿真和试验对比结果。从试验数据可以看出,切削力随切削速度的增加而增加,当切削速度达到55 m/min后,缓慢上升趋于平稳。仿真分析结果在切削速度达到55 m/min后,切削力随切削速度的增加而下降。误差产生的主要原因是在钻削加工过程中,机床运动稳定性、刀具振动、刀具磨损以及切屑堵塞等因素都会对切削力带来影响。其它数据误差在允许接受范围内约为3%~7%。扭矩则随切削速度的增大而减小,验证了仿真模型的准确性,能够合理的预测实际加工过程中切削力和扭矩的变化。
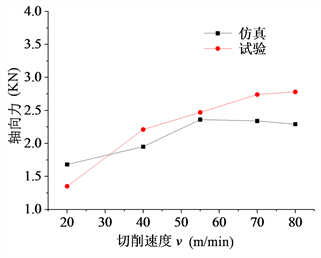
Figure 3. Drilling axial force and torque at different cutting speeds
图3. 不同切削速度下的钻削轴向力和扭矩
4.2. 进给量f对切削力及扭矩的影响
图4所示为不同进给量下钻削轴向力和扭矩的仿真和试验对比结果图。从对比数据可以看出,进给量f越大,轴向力越大,扭矩越大,主要原因为进给量增大切削厚度成比例增大,切削面积增大,刀具和切屑以及刀具和工件之间的摩擦力变大,故切削力和扭矩随之增大,钻削加工试验和仿真分析结果一致。

Figure 4. Axial force and torque at different feed rates
图4. 不同进给量下轴向力和扭矩
4.3. 钻头直径D对切削力及扭矩的影响
图5所示为不同钻头直径下钻削轴向力和扭矩的仿真和试验对比结果。从对比数据可以看出钻头直径越大,轴向力越大,扭矩越大,其主要原因是,钻头直径增大,切削宽度增大,每刃切削层公称横截面积增大导致刀具与工件、切屑与刀具的接触面积越大,摩擦力越大,同时切削刃长度增加导致扭矩也相应增大,因此轴向力和扭转均随直径的增大而增大,钻削仿真分析和钻削加工试验结果一致。
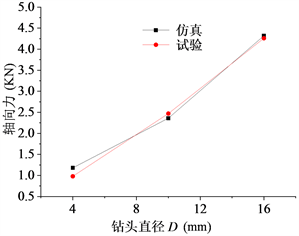
Figure 5. Axial force and torque under different drill diameters
图5. 不同钻头直径下轴向力和扭矩
5. 结论
通过钻削高强度钢仿真和试验数据的对比和分析,验证了钻削仿真模型的准确性。对于提高钻削加工工件的质量、寿命和加工效率来说,影响钻削切削力及扭矩的因素由主到次顺序依次为:钻头直径、进给量和切削速度。
钻削切削力随切削速度的增大而增大,扭矩随切削速度的增大而减小;切削力和扭矩都随进给量的增大而增大;切削力和扭矩都随钻头直径的增大而增大,适当提高切削速度或增加进给量可以提高钻削加工工件的质量寿命及加工效率。
NOTES
*第一作者。
#通讯作者。