1. 引言
我国建筑的主要结构形式为框架结构,遵循“强柱弱梁,强剪弱弯,强节点弱构件”的设计理念,从而实现“小震不坏,中震可修,大震不倒”的抗震设防目标。为了使结构在地震作用下达到自行复位,减缓结构损伤发展进程的设计目标,自复位结构应运而生。
在过去的十几年中,国内外众多学者针对自复位结构进行了系列研究。2002年,Christopoilous [1] 等对部分应力预制混凝土连接结构进行了试验研究,结果表明:当加载至层间侧移角达到4%时,主要受力构件梁柱仍未出现大面积损伤,且连接具备较好的自复位功效。2011年,Chou [2] 等对梁上设置加强型摩擦板的两跨单层PT-MRF进行了试验,结果显示:当层间侧移处在3.9%~7.2%时,残余变形不到0.01%,自复位功效较好。2012年,蔡小宁,孟少平 [3] 等提出设置预应力筋实现结构自行复位的预应力预制框架结构,其中通过在框架节点处设置顶底角钢实现耗散地震能的设计目标,研究结果证实:当荷载加载至层间侧移角达到4%时,卸载后结构残余转角较小,表明节点具备较优自复位功效。2014年,方有珍,赵凯 [4] 等提出在梁柱节点处设置摩擦耗能T形件进行耗能能力和利用预拉螺杆提供预紧力实现自复位功效的节点连接,研究结果表明:卷边PEC柱布置方式改变刚度匹配,影响结构损伤耗能发展的规律,通过摩擦耗能T形件实现了摩擦滑移耗能能力,预拉螺杆预应力的大小对自复位效果影响明显,且卸载后结构残余变形小于小震侧移角0.01 rad,具有较优自复位功效。
本文基于新型PEC柱–钢梁通长预拉杆摩擦耗能自复位中间层子结构试验试件为基本试件,考虑T形件翼缘对穿螺栓布置、摩擦长圆孔尺寸和预拉杆预应力大小等设计参数,设计5个试件进行抗震模拟研究,用以揭示设计参数的影响规律。
2. 摩擦耗能型部分自复位连接设计
2.1. 设计思路
自复位摩擦耗能型梁柱组合框架是遵循抗震性能化设计而提出的一种新型框架结构,设计思路依据参考文献 [5] 和图1节点弯矩–转角曲线。
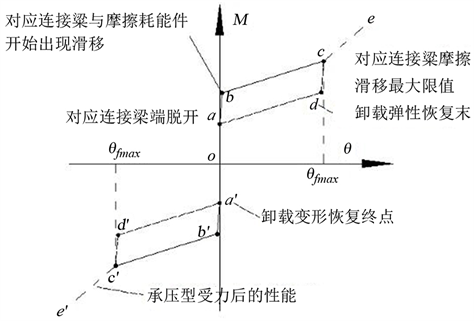
Figure 1. M-θ curves of moment-rotation
图1. 弯矩M-转角θ曲线
2.2. 试验试件设计
本文以框架结构中间层作为研究对象,按1:2缩尺比例设计了1榀中间层子结构试件(见试件设计图2)。为实现更好实现自复位效果,自复位连接设计参照文献 [6] 对梁端连接脱开弯矩Ma采与梁端开始滑移弯矩Mb按0.4~0.7范围内取值。
设计结果如下:摩擦耗能T形件与卷边PEC柱采用Q235B钢材;钢梁采用Q345工字型钢;盖板采用I
25a
剖分;混凝土选用C25。T形件翼缘和PEC柱接触面以及T形件腹板与盖板和钢梁接触面分别通过D20高强对穿螺栓和D18高强螺栓固定。
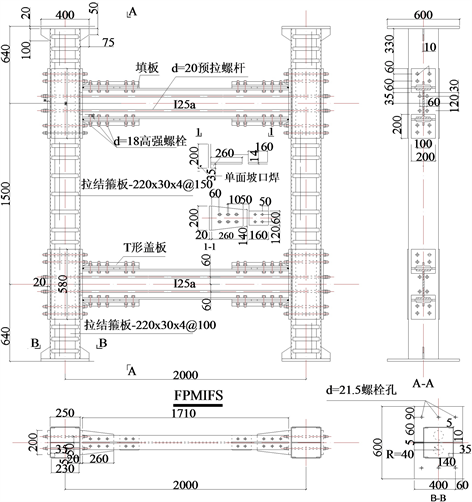
Figure 2. Design details of the test specimen
图2. 试件设计详图
3. 有限元模型建立
3.1. 模拟试件设计
按照节点连PEC柱连接的接摩擦T形件翼缘对穿螺栓布置差异分为I型和II型,其中I型试件为试验缩尺原因而仅在摩擦T形件外翼缘设置两排对穿螺栓的试验试件,II型试件为实际工程中应用的摩擦T形件内外翼缘均布置对穿螺栓连接试件。基于预拉杆控制自复位效果和摩擦耗能件提供耗能能力的基本思想,通过控制梁端脱开弯矩和初始滑移弯矩的比值设计了5个试验模型,具体参数见表1。
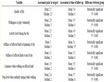
Table 1. Concrete parameters of the specimens
表1. 试件具体参数
3.1.1. 边界条件
参照试验试件设计,PEC柱顶底连接平面铰支座转轴均为对应层PEC柱反弯点处,相应在模拟模型中将柱顶底板耦合至对应铰支座转轴处(距顶板中心110 mm),且设定相应边界条件:柱顶耦合点存在框架平面内平动和转动自由度;柱底耦合点仅存在框架平面内转动自由度。
3.1.2. 单元选择与划分
为了实现模拟精确、运行时间和收敛性需求,预拉高强螺杆主要承担轴向拉力,则采用两结点线性三维桁架单元模拟,其余原件均选用八节点六面体减缩积分实体单元。由于减缩积分单元可能引起积分点数目降低导致出现刚度为零的“沙漏模式”,故对关键节点处各部件网格,组成节点的关键部件钢梁,T形件以及高强螺栓网格划分进行了相应细化。同时在T型件摩擦孔壁处网格设置必要的单元数量以改善模拟的收敛性。模拟试件见图3。
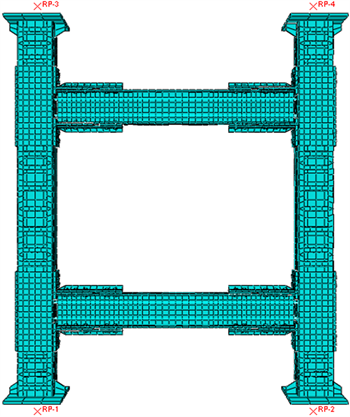
Figure 3. The geometrical model of the specimens
图3. 几何模型及单元划分
3.2. 材料本构
3.2.1. 钢材
本文模型钢材为匀质和各向同性体,采用理想弹塑性模型,见公式(2),且采用Von Mises屈服准则和等向强化与关联流动法则以考虑循环荷载作用下本构。
(2)
式中:εy为钢材屈服应变;σy为钢材屈服应力;Est为强化模量。
3.2.2. 混凝土
由于大量试验研究证实PEC钢柱和拉结板条对混凝土存在较强约束作用,使得混凝土在整个加载过程中压溃酥松脱落不明显,为此混凝土采用单轴受压的应力–应变曲线基础上,参考文献 [7] 对混凝土的骨架曲线、卸载曲线,抗压强度代表值和峰值压应变等参数作适当修正。
3.2.3. 接触面处理
本文模拟模型中钢–钢接触面和混凝土-钢接触面切向采用库伦摩擦模型(对应摩擦系数分别定义为0.3和0.33),法向选用默认的“硬接触”。高强螺栓螺杆与混凝土接触面积较小,不考虑摩擦力的影响而定义法向作用“硬接触”。由于预拉高强螺杆采用线单元模拟,而PEC柱采用实体单元,为了避免出现“刚度矩阵奇异”的错误,两者之间采用MPC多点约束。此外,所有接触面处理中的主、从面定义均基于刚度分布和网格划分。
3.2.4. 模拟加载方案
模拟加载分为三步:① 首先根据相应分析步,选择螺栓螺杆中间面施加5 kN的初始预紧力,建立高强螺栓与构件平稳接触面关系,再对d20和d18高强螺栓分别施加10 kN和50 kN的预紧力;② 其次根据不同试件预拉螺杆预紧力大小需求对其进行降温法施加预应力。③ 最后在柱顶设置耦合点后,参照试验设计加载方案进行全位移加载,以15 mm为一个加载级逐渐递增,对框架施加水平循环往复荷载,加载至150 mm结束。
4. 模拟结果分析
4.1. 试件整体与层间侧移曲线
通过对模拟结果数据处理,整理得到了各试件的整体与层间荷载—侧移曲线,见图4。
对图4试件I-SMJ1分析可得,在试件位移加载至侧移角0.025 rad前,主体构件均处于弹性阶段,试件卸载呈现良好的自复位效果;随着荷载的继续加大,盖板首先出现屈服,试件卸载存在微小残余侧移;当水平位移加载至105 mm时(第7个加载级),梁少部分进入屈服耗能,且摩擦T形件内翼缘受拉弹性面外翘曲变形导致摩擦螺栓杆未与孔壁接触承压,但试件卸载后残余侧移角仍未超过0.005 rad,自复位效果表现良好;对比试件I-SMJ1和II-SMJ2,试件II-SMJ2的承载力显著提高,原因在于试件II-SMJ2摩擦T形件与PEC柱连接采用内外翼缘均布置螺栓方式,消除了试件I-SMJ1中的T形件面外翘曲,使试件摩擦高强螺栓与T形件孔壁接触转化为承压型受力模式;对比II-SMJ2和II-SM4,在位移加载至侧移角达到0.035 rad时,II-SMJ4自复位效果较差,表明摩擦长圆孔长度减小,摩擦耗能较小,梁端受压区域较早进入塑性阶段,整体和层间残余变形较大;对比试件II-SMJ1,II-SMJ2,II-SMJ3,当Ma/Mb的值在从0.4增大到0.7时,滞回曲线捏缩现象愈加明显,主要由于预拉杆预应力的增大导致自复位效果改善,且所有试件加载至105 mm时(第7个加载级)卸载,整体残余转角均未超过小震侧移角限值0.005 rad,表现出优越的自复位功效。对比各试件层间和整体侧移曲线,两曲线几乎重合,即层间与整体受力变形基本趋于一致,即表明PEC柱–摩擦耗能性自复位框架整体性良好,抗震性能优越。
4.2. 连接弯曲–转角曲线
由于框架结构整体性能取决于梁柱连接性能,为此本文对梁柱节点连接弯矩–转角曲线进行了整理,见图5。
通过图5分析发现,试件I-SMJ1连接弯矩达到13.845 kN·m前,高强预拉杆预紧力引起的梁端压力尚未消除,T形件与钢梁端部紧密接触。当加载进一步增大,高强预拉杆预紧力引起的梁端压力尚消除,T形件未设置对穿螺栓的翼缘部分出现撬拔面外变形而与PEC柱间产生脱开,节点处转动刚度存在下降趋势;当加载逐渐增大至滑移弯矩达到25.33 kN·m时,T形件与梁连接接触面出现滑动摩擦耗能,节点处转动刚度进一步下降;当位移加载至90 mm (第6个加载级)时,由于T形件自身变形过大,T形件下翼缘撬拔与PEC柱脱开明显,摩擦螺栓与螺栓孔壁仍未接触而转化为承压型受力模式;当位移加载至105 mm (第7个加载级)时,此时节点侧移转角达到0.035 rad,钢梁仅翼缘少部分区域进入塑性阶段耗能,且在卸载过程中,由于预拉杆预拉力的作用,仍较好实现自复位功效。
实际工程应用的II型试件相比试验缩尺设计的I型试件,由于在摩擦耗能T形件内翼缘增设了一排对穿螺栓,明显减小了T形件的撬拔变形,T形件翼缘与PEC柱接触面接触紧密。试件I-SMJ1和II-SMJ2相比,加载初期,试件II-SMJ2中T形件与梁端脱开弯矩有所提高,梁与T形件产生相对滑动时对应连接转角显著减小;当位移加载至90 mm (第6个加载级)时,摩擦高强螺栓与对应长螺孔壁接触挤压,试件连接转化为承压型受力模式,承载力显著提升,节点刚度明显增强;当位移加载至105 mm (第7个加载级)时,T形件上下翼缘处受到对穿螺栓的限制故变形较小,梁端进入屈服耗能,自复位效果与试件I-SMJ1相比弱化。试件II-SMJ4相对试件II-SMJ2仅改小了摩擦孔的长度,故梁端脱开弯矩与滑动到最大位移时对应弯矩基本相同,但由于摩擦孔的减小,导致II-SMJ4在位移加载至0.02 rad时便进入承压型受力模式,试件耗能主要由梁承担,故梁屈服较早,试件自复位效果随之减弱;对比试件II-SMJ1,II-SMJ2,II-SMJ3,随着Ma/Mb的值在从0.4增大到0.7,梁端脱开弯矩与滑动到最大位移时对应弯矩逐渐提高,卸载后残余转角均小于0.005 rad,均表现出优越的自复位功效。
4.3. 连接耗能
本文通过滞回环面积表征试件的绝对耗能能力,反映试件的损伤耗能进程,见图6。
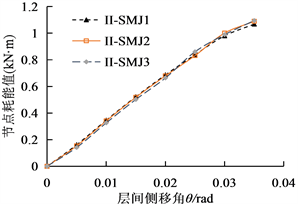
对穿螺栓布置方式和摩擦孔长度 预紧力大小
Figure 6. Hysteretic energy-dissipation of the specimens
图6. 试件滞回耗能变化规律
对比试件I-SMJ1和II-SMJ2,位移加载至75 mm (第5个加载级)前,II-SMJ2的耗能能力明显优于I-SMJ1,主要原因在于T形件内翼缘增设一排对穿螺栓相应减小了T形件撬拔面外变形,且摩擦滑移耗能相对加快。当位移加载至第5个加载级时,试件I-SMJ1和II-SMJ2的摩擦耗能T形件滑动距离基本一致,两试件耗能基本相同。当位移加载超过75 mm (第5个加载级)时,试件I-SMJ1中T形件由于下翼缘撬拔面外变形较大,且处于弹性阶段,而试件II-SMJ2中T形件撬拔面外变形较小,承载力较高,且梁端屈服耗能发展较快,耗能高于I-SMJ1;对比试件II-SMJ2和II-SMJ4,位移加载至60 mm (第4个加载级)前,耗能基本趋于一致;当位移加载至105 mm (第7个加载级)时,II-SMJ4由于长圆孔尺寸小而进入承压型受力模式早,其耗能大于试件II-SMJ2;对比试件II-SMJ1,II-SMJ2和II-SMJ3,随着预拉杆预应力的增大,相应梁与T形件的滑动摩擦滞后,延缓了T形件摩擦滑移耗能作用的发挥。
4.4. 残余变形
本文通过节点和整体残余转角分析试件损伤程度和自复位功效。基于模拟数据整理得到各试件相应的残余转角曲线,见图7。
预紧力大小 对穿螺栓布置方式和长圆孔尺寸
(a) 整体残余侧移角
预紧力大小 对穿螺栓布置方式和长圆孔尺寸
(b) 节点残余转角
Figure 7. Patterns of residual rotation
图7. 残余转角发展规律
通过图8对比分析,在位移加载之初,各试件表现出基本一致的自复位功效,在预拉杆预应力的作用下,结构实现完全自复位,试件节点和整体残余转角十分微小;当加载位移逐渐增大,节点连接处产生摩擦滑动耗能,卸载后试件在预拉杆预应力作用下实现完全自复位,整体侧移转角和节点残余转角均很小;当位移加载至90 mm时(第6个加载级),摩擦螺栓与摩擦孔壁挤压接触,试件连接转化为承压型模式,整体残余侧移转角和节点处残余转角明显增大;对比试件II-SMJ1,II-SMJ2和II-SMJ3,随着预应力的逐渐增大,整体侧移转角和节点残余转角会小幅度的降低;从图8(a)和图8(b)可以得到,试件II-SMJ2整体和节点残余转角均大于试件I-SMJ1,主要源于实践工程中T形件内外翼缘对称布置螺栓做法导致节点受拉处T形件面外撬拔作用减小,梁端塑性发展较快,整体和节点残余转角较大;在最后4级加载级中,II-SMJ4整体残余侧移转角和节点处残余转角均大于II-SMJ2,这是由于试件II-SMJ4的T形件耗能件摩擦孔长度的减小导致其连接较早转化为承压型受力模式,梁提前进入屈服耗能,残余转角相应增大。当位移加载至105 mm时(第7个加载级),所有试件卸载后整体残余侧移转角和节点处残余转角均小于0.005 rad,表明实际工程采用T形件翼缘对称布置对穿螺栓的自复位连接试件具有更优越的自复位功效。
4.5. 自复位连接受力变形模式
为了研究两种T形件对穿螺栓布置的试件受力机理,本文针对试件I-SMJ1和试件II-SMJ2左上节点进行变形受力分析,应力云图见图8。
从图8(a)应力云图中可得,在试件加载过程中,试件I-SMJ1和试件I-SMJ2受力模式基本趋于一致;由图8(b)对比看出当位移加载至90 mm (第6个加载级)时,试件I-SMJ1节点处T形件下翼缘由于撬拔作用,其与PEC柱表面脱开距离较大,摩擦高强螺栓与T形件螺栓孔接触进行承压型受力模式滞后。试件II-SMJ2节点处采用在T形件下翼缘处布置一排对穿螺栓的布置方式,保证了在加载过程中T形件与PEC柱接触紧密,当位移加载至90 mm (第6个加载级)时,节点受拉端摩擦高强螺栓与摩擦孔壁接触转化为承压型受力模式,试件承载力河刚度显著增大。从图8(c)应力云图中可得,在试件卸载完成后,试件I-SMJ1和试件II-SMJ2残余应力分布区域大致相同,残余转角均未超过0.005 rad,表明试件具有优越的自复位效果。
5. 主要结论与建议
通过对5个新型卷边钢板组合PEC柱–钢梁摩擦耗能型部分自复位连接试件的抗震性能数值模拟研究,得出以下结论与建议:
1) 试件试验加载过程中基本实现了自复位结构性态设计目标:即在位移加载至层间侧移角0.02 rad (设计地震框架结构层间侧移角限值),试件耗能主要为摩擦T形件摩擦滑动耗能,主体受力构件基本处在弹性状态;在位移加载加入旱遇地震对应侧移阶段,自复位连接转化为承压型模式,主体构件梁受力性能进一步发挥,以致进入屈服耗能。
2) 采用在耗能T形件内翼缘增设一排对穿螺栓的实际工程做法使得在位移加载至90 mm (第6个加载级)时,摩擦高强螺栓与孔壁接触挤压转化为承压型传力模式,进一步提高承载能力以及转动刚度。
3) 减小摩擦孔长度,相应降低了试件摩擦滑移耗能,加快了梁的屈服耗能进程,梁端较早进入塑性阶段而降低了自复位效果。
4) 在整体侧移角达到0.035 rad后卸载,各试件卸载后残余转角均小于小震侧移角限值0.005 rad,表明试件具有优越的自复位功效。
5) 实际工程中采用T形件翼缘对称布置对穿螺栓的自复位连接试件具有更优越的自复位功效和更理想的损伤耗能进程。
基金项目
国家自然科学基金(51478286);江苏省教育厅重大科研项目(18KJA56000);江苏省“六大人才高峰”高层次人才项目(JZ-033)。