1. 引言
充填接顶工艺是每个使用充填采矿法的矿山普遍关注的技术难题。充填采场的接顶好坏是关系到采场及区域地压稳定及二步骤采场安全回采的重要因素,如果充填接顶不好,会使采场顶板暴露面积过大,容易造成矿岩冒落,危及采矿安全 [1]。目前国内外充填矿山虽然采取了分段充填接顶、施工充填钻孔接顶等方法,但均不能有效对充填接顶过程予以控制,很难达到二步骤回采需要的接顶效果 [2]。
2. 某矿山充填接顶技术现状分析
2.1. 现有充填接顶技术简介
目前某矿山的充填接顶工艺主要有两种,一种是反充,即采场充填进入接顶阶段,在封闭采场进口前,将充填管安装在采场顶板最高点,封闭采场进口后,根据估算采场剩余空间,进行一次性充填,由于充填料浆的不稳定性,充填过程中无法观察到空区剩余体积,无法预测充填量,充填过程无法精度控制浆量,容易造成堵管或存在充填料浆过多造成井下跑浆等环保问题 [3]。
另一种接顶工艺一般是在充填水平之上施工充填钻孔到采空区 [4] [5],共施工两个孔,一个下料孔,一个观察孔,进入接顶阶段,将采空区进路口全封闭后进行一次性充填接顶。这类接顶方法一方面增加了大量巷道和钻孔工程,另一方面只在钻孔周围接顶较好,但较远处会因钻孔提前被堵住而造成接顶效果差。
2.2. 现有充填接顶工艺不足分析
由于矿山大部分采场充填时,顶板高出充填进路,或顶板无法施工充填钻孔及观测孔,无法对剩余空间予以准确估计或进行过程观测 [6],造成空间充填不满,无法有效的实现充填接顶。或充填料过多,容易造成堵管或剩余充填料排至采空区外,从而造成井下环境污染。
3. 影响充填接顶因素分析及对策
3.1. 影响充填接顶的因素
(1) 采场的顶板形状凹凸不平,充填管及排气管没有架设在采场顶板的最高点。
(2) 充填料浆在固化过程中会产生沉降,即使采空区被完全充满,仍无法实现全部接顶。
(3) 采用自流输送充填方式,料浆在充填过程中会发生沉降,从充填管出料口到采场边缘会形成坡度,由于该自流坡度的影响,导致采场边缘不能完全接顶。
(4) 充填料浆浓度越低,充填体离析现象越明显,充填接顶效果越差;同时料浆中含有的大量水,不仅占据空间,阻碍接顶,同时越到接顶顶部,滤水速度越慢,直接影响接顶效果。
(5) 充填完毕后,需要对充填管道进行冲洗,冲洗管道的水进入接顶空间后,会直接影响接顶效果。
3.2. 提高充填接顶率的对策
(1) 采场顶板在控顶过程中,必须按设计要求控制断面形状,严格按光面爆破要求进行控顶,对局部顶板结构较差的部位需要根据情况进行支护,确保顶板相对平整 [7];充填接顶前将充填管道及排气管道安装在顶板最高点位置。
(2) 充填接顶料浆严格按规程要求执行,料浆浓度必须达到77%以上。
(3) 充填挡墙外的充填管道安装三通 [8],充填接顶完成后,冲洗管道时,关闭充填阀,打开泄水阀,严禁将冲洗管道的水引至采场。
(4) 对顶板凹凸不平的采场,根据情况进行分段接顶 [9]。
(5) 提高脱水质量,增大脱水管表面积,增强脱水管的脱水能力 [10]。
4. 一种可观测的采场充填接顶方法
某矿山在综合现有充填接顶工艺的基础上,克服了现有技术中的缺点,提供了一种采场充填的接顶方法,通过对充填管道及脱水管道的布置,有效对充填接顶过程予以观测、控制,提高充填采场的接顶率。其安装立面图及平面布置图如图1及图2所示。其具体施工过程及相关技术要求如下:
(1) 接顶前的准备工作:对采场空区顶板及边帮用空区扫描仪进行有效测量,技术人员根据测量结果进行成图,此项工作的目的除基于日常的生产管理外,其采场上部窿型的精确测量是最后的充填接顶控制的关键因素。按正常充填至采场进路或联络道上方适当位置处,具体高度以确保作业人员能方便进出采场作业为准,一般为充填面至进路顶板1.5 m左右。对剩余空区进行简易测量,主要是测定接顶前的充填面标高及确定剩余空间最高点位置,然后通过实测的窿型计算出剩余的空区体积,该项工作中最高点位置的确定及剩余空区体积大致估计对接顶率至关重要。
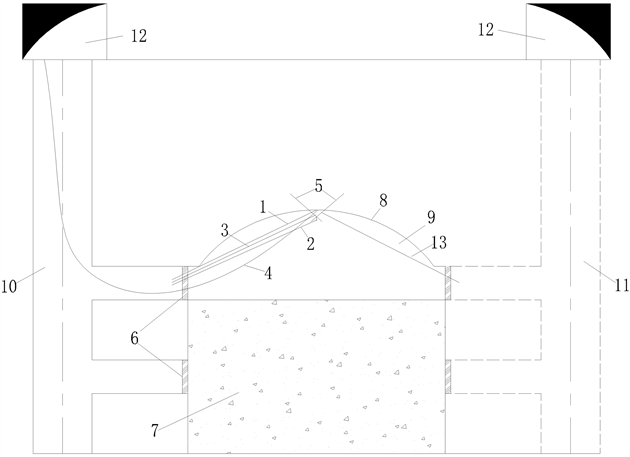
Figure 1. Elevation view of filling pipe installation
图1. 充填接顶管路安装立面图
1—脱水管①;2—脱水管②;3—脱水管③;4—充填管;5—吊装锚杆;6—充填挡墙;7—充填体;8—采场顶板;9—采场剩余空间;10—西天井;11—东天井;12—天井硐室;13—脱水管;14—天井联道;15—采场窿形。
Figure 2. The installation plan of the filling pipe
图2. 充填接顶管路安装平面图
(2) 在空区最高点施工吊装锚杆,将充填管吊装于空区最高点。用YT28钻机施工∅38 mm钻孔两个,孔距30 cm,成交叉状,交叉角度约45度;孔深1.2 m,冲∅42 mm的空心锚杆,出露60 cm于孔外,成交叉状;将∅114 mm PVC充填管置于交叉锚杆中间,用铁线等物固定,管壁尽量贴住顶板。
(3) 单独安装脱水管①至空区顶板最高点位置,用铁线等固定脱水管①,脱水管为∅90 mm的硬质波纹塑料管,管身开有泄水孔或泄水缝,管身包有铁丝网,规格为铁丝直径2 mm,网度规格1.2 cm * 1.2 cm,钢丝网外包有滤布,滤布网度为30目;后经改进的脱水管用铁丝网弯成圆形,用铁线固定成型后在外包有滤布;脱水管尾端布置在进路立模处外,避免存在水平段,脱水管头端封滤布。
(4) 单独安装脱水管②作为胶面定位管至空区顶板最高点下方,安置高度为采场顶板最高点下方60 cm,管口不封充填滤布。
(5) 单独安装脱水管③作为观测管至顶板空区顶板最高点下方,安置高度为采场顶板最高点下方10~20 cm,管口不封滤布;按正常施工要求对进路口予以封堵,需要确保3条脱水管尾端出露挡墙并确保其完整。
(6) 按设计要求配比充填料浆进行充填,当充填至胶面高度定位管即脱水管②跑浆时,立即用约∅70 mm的木塞包充填滤布进行堵塞封堵,并通知地表充填搅拌站停机洗管,其冲洗管道的水通过设置在挡墙附近的三通泄至设有挡浆墙的区域,经充填滤布过滤后排至充填水收集系统。
(7) 最后,要求充填站存足够尾砂及水泥对采场剩余空间进行接顶充填,料浆配比按矿山胶面质量技术要求,一般为灰砂比1:4,料浆浓度77%以上,并要求连续充填至采场结束;当观察管即脱水管③跑浆时,立即对其进行封堵,并通知地表充填搅拌站停机洗管,完成采场充填。
5. 该充填接顶方法应用效果及评价
(1) 该充填接顶方法有效的解决了采空区接顶问题,后续回采二步骤采场或顶底柱采场时,揭露发现采场接顶率保持在95%以上。
(2) 该充填接顶方法利用充填脱水管的有效布置,加强了对接顶空间的有效观测、控制,保证充填料浆尽量充满采空区,提高了充填采空区的接顶率,保证了采场顶板稳定及二步骤采场的回采安全。
(3) 通过对充填过程的有效观测及严格控制,可以有效的控制充填料浆量,从而有效的解决充填料浆过多带来的堵管及造成充填料浆溢出带来的环保等风险。