1. 引言
在过去的几十年里,航空航天领域材料发展的一个重要目标是改善结构材料的裂纹扩展特性 [1],并对高性能、轻型结构的材料需求不断增加。人们一直在寻找能够在航空结构中替代传统材料的轻质材料 [2]。先进的铝合金和纤维增强复合材料等竞争性材料有可能满足这种结构的需求。这些材料仍有其优缺点,如铝合金的疲劳强度差,碳纤维增强复合材料的耐冲击和剩余强度性能差。为了优化结构设计,需要一种新材料,这种材料有高强度、低密度和高弹性模量,并能改善结构的韧性、耐腐蚀性和疲劳性能。七十年代末,利用先进的铝合金和纤维增强复合材料形成混合复合结构材料以克服两种材料的大部分缺点 [3]。混合复合结构材料几乎涵盖了所有要求。与金属合金相比,混合复合结构材料使得结构设计的重量大大减轻。并有许多优点,特别是在高强度和刚度重量比方面。此外,它们在应用中提供了优异的疲劳性能和耐腐蚀性 [4]。凭借所有这些优势,混合复合材料结构在航空航天工业中得到广泛应用 [5]。
混合复合材料结构是由薄金属和纤维增强复合材料由粘合剂交织而形成的纤维金属层压板(FMLs) [6]。纤维/金属复合材料技术结合了金属材料和纤维增强复合材料的优点。例如,金属是各向同性的,具有高的承载强度和抗冲击性,并且易于修复,而复合材料具有优异的疲劳特性、高强度和刚度。金属的疲劳和腐蚀特性以及复合材料的低承载强度、抗冲击性和可修复性可以通过两种材料的组合来克服 [7]。最常见的纤维金属层压板是芳纶增强铝合金层板、基于高强度玻璃纤维钢层板和碳纤维增强铝合金层板。
1978年,荷兰代尔夫特理工大学航空航天工程学院开展了对提高铝合金疲劳性能的研究。通过在粘合层中引入高强度芳族聚酰胺纤维(ARALL),获得了层压板材料疲劳性能的改善 [8]。后来又研究了一种由碳纤维组成的更硬碳纤维增强铝合金层板材料(CARALL) [9]。最近的研究表明,CARALL层压板在高应力水平下的飞行模拟疲劳试验中会发生纤维失效,从而导致疲劳性能下降。碳纤维的有限失效应变(0.5%~2.0%)也是一个缺点。CARALL对带有缺口的部位应力集中。另外碳纤维铝板在潮湿环境中的电偶腐蚀问题,需要进行更多的研究。
1990年,为了改进ARALL层压板性能和克服CARALL的确定,开发了玻璃纤维增强预浸料和高强度铝合金板交替层组成的材料。称为GLARE。AKZO和ALCOA于1991年开始合作生产GLARE并将其商业化 [4]。最后,SLC公司于1992年推出了纤维金属层压板的新概念——拼接层压板(FMLs),与ARALL相比,GLARE有更能抵抗压缩载荷。因此,在疲劳载荷期间很少观察到玻璃纤维中的纤维失效。另外GLARE有更高的拉伸和压缩强度、更好的冲击性能和更好的剩余强度。这些特性似乎使GLARE具有更广泛的潜在应用 [1]。
目前为止,国内外研究人员结合实验和数值计算方面对金属复合材料层板的性能进行了大量研究。由于金属层板和复合材料的本构关系不同,金属和复合材料层板在进行拉伸实验时应力–应变响应相互影响。许多学者也从实验方面对纤维金属层板的刚度和强度进行了研究。ALDERLIESTEN [10] 在已知荷载工况和选定材料的情况下,提出一种结合纤维金属层板的强度、疲劳和损伤容限的基本理论的方法,该方法可近似预测纤维金属层板性能并且有较高的精度。SUN研究 [11] 考虑不同的金属板厚度、金属体积分数和纤维取向的11种不同类型的碳纤维钛合金层板(TI-CF-FMLs)在准静态载荷下的拉伸性能。探讨了试件的拉伸破坏机理,并在理论上使用混合物规则的体积分数法进行的理论预测与所测得的TI-CF FMLs的力学性能非常吻合。SISAN [12] 对不同铺层的玻璃纤维金属层板进行落锤低速冲击和拉伸强度实验。并在实验以后,使用光学显微镜从试件不同侧面进行受损检查。得到Kevlar纤维、芳纶纤维和玻璃纤维金属层板的拉伸强度和破坏强度。ZHANG J [13] 通过对缺口GLARE板进行拉伸实验,以评估其破坏机理与缺口尺寸关系,并结合有限元模型对GLARE板的力学响应进行了精确的预测,特别是对其损伤机理进行了分析。RAMYA [14] 通过对层合板选择合适的纤维取向和不同铺层,使得层合板的性能得到改善。在不同的载荷条件下,如拉伸、弯曲和冲击,对制备的层压板进行了测试。并结合扫描电镜分析了断裂试样表面形貌的缺陷。得出该层合板的拉伸性能大于弯曲和冲击性能的结论。OSTAPIUK研究 [15] 了玻璃纤维金属层合板和碳纤维金属层合板在三点弯曲作用下的开裂破坏机理,介绍了基体和纤维的失效以及不同金属层厚度对被测层合板的影响。金属在压/拉应力下的弯曲过程中可减缓层合板的失效。谢波涛 [16] 基于热模压成型工艺制备GLARE层板,结合实验和有限元仿真两种方法对含圆孔、方孔GLARE层板的拉伸性能和层板各组分失效模式进行研究。基于修正后点应力准则,对含圆孔GLARE层板剩余强度进行理论预报,结果表明该预报模型与实验数据较为吻合。
金属复合材料层板常用的无损探伤检测方法可以检测层板的裂纹扩展和损伤情况 [17]。SEM电子显微镜扫描可检测GLARE层板在载荷作用表层的变形、纤维层损伤和层间分层等。只能通层板厚度切割等方法将关注部位切开。该方法无法检测层板内部损伤情况。C超声波扫描是检测GLARE层板损伤常用的方法。C扫描可检测到各铺层分层和纤维损伤面积的叠加。但金属层会而阻碍超声波对中间各层的检测检测效果不明显。GLARE层板检测也可以通过红外热成像技术实现。通过记录温度来分辨内部损伤情况,该方法可检测到金属–纤维层合板中金属层和纤维层内部的属性。
以上无损检测方法都是离线、静态、被动的材料及结构损伤检测,但是对GLARE层板服役过程中没有有效检测方法。本文利用碳纳米纸传感器(buckypaper)结构健康监测方法,完成对GLARE层板的力学状态进行监测。利用粘贴在GLARE层板结构表面和预埋在GLARE层板结构内部的碳纳米纸传感器监测GLARE层板自身状态的变化,具有实时、动态、在线的特点。采用健康监测技术可以保证结构的安全性和可靠性,GLARE层板的应用与维修提供了重要依据,避免发生灾难性故障,保障使用人员的生命安全,降低维护成本 [18]。
2. 实验
2.1. 碳纳米纸传感器的制备
碳纳米纸传感器的制备方法主要有研磨、搅拌、超声、离心、抽滤五部分,制作的传感器如下图1。具体步骤如下:
研磨:将称取100 mg单壁碳纳米管、100 mg多壁碳纳米管以及15 ml表面活性剂放入研钵进行研磨,直至碳纳米管和表面活性剂与充分混合。
搅拌:将研磨完成的碳纳米管与表面活性剂放入搅拌器中,并加入1500 ml蒸馏水,然后搅拌1小时。
超声:将搅拌好的碳纳米管溶液放入超声仪,进行超声处理1 h。
离心:使用离心机以5000 r/min运行10分钟分离碳纳米管溶液上层清液。
抽滤:最后将碳纳米管溶液上层清液进行抽滤,得到碳纳米纸薄膜传感器。
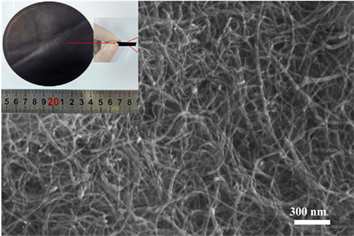
Figure 1. Pristine sample of buckypaper and SEM image of pristine buckypaper
图1. 碳纳米纸传感器样品与SEM图像
2.2. GLARE板的制备
本文中使用的试样尺寸大小为30 mm × 250 mm,为了验证碳纳米纸传感器对GLARE板的全面监测,实验准备的试样一共有三种:玻璃纤维试件、铝合金试件、GLARE板试件。并准备了若干直径为8mm的圆形的碳纳米纸传感器。
1) 铝合金试件:然后将3M460树脂使用丙酮稀释,将稀释的3M460树脂粘接圆形传感器到金属试件表面,最后放入烘箱在90℃温度下固化2小时。
2) 玻璃纤维试件:本文制作的玻璃纤维层板是使用玻璃纤维/环氧树脂单向预浸料固化制作,预浸料的型号为GFB17500。首先将预浸料裁剪10层大小30 mm × 250 mm矩形,然后按铺层方向为90°铺设。铺设完成后,将圆形传感器布置在10层单向预浸料表面。然后使用模压机以2 MPa与120℃的环境下固化3小时。使碳纳米纸传感器与玻璃纤维层板一体固化。
3) GLARE板试件:按照玻璃纤维试件制作方式铺设10层90˚方向的预浸料试件板,将一个圆形传感器布置在预浸料试件板表面,又将两个圆形传感器布置在预浸料试件板表面另一边。然后将粘有两个圆形传感器预浸料试件表面与铝合金粘接到一起,粘接完成后,将试件板放入模压机。然后使用模压机以2 MPa与120℃的环境下固化3小时。使传感器布置到玻璃纤维–铝合金界面与玻璃纤维表面。固化完成后,按照铝合金试件板制作方式粘接碳纳米纸传感器到铝合金表面,GLARE板制作方法如下图2所示,制作的三组试件如下图3所示。
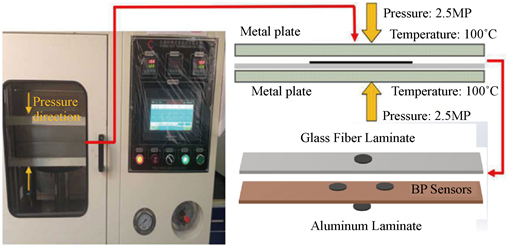
Figure 2. Fabricating process of specimen laminates
图2. 试件层板制作示意图
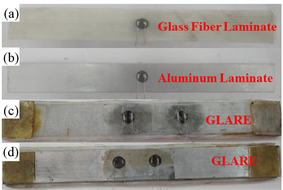
Figure 3. Specimen laminates of (a) glass fiber laminate; (b) aluminum laminate; (c) (d) GLARE
图3. 试件层板(a) 玻璃纤维试件、(b) 铝合金试件、(c)、(d) GLARE板试件
2.3. 拉伸实验
使用GOTECH AL-7000-LA20万能试验机进行拉伸实验。对玻璃纤维板进行拉伸测试,以0.5 mm/min进行拉伸实验,设置最大拉伸载荷为12 KN。首先对未粘贴传感器的铝合金板进行拉伸测试,得到铝合金板的位移-载荷关系。然后对粘接传感器的铝合金板以0.5 mm/min进行拉伸实验,由于铝合金板在较小的载荷中也出现明显塑性变形,所以铝合金板设置最大拉伸载荷为10 KN。对GLARE板拉伸实验中发现GLARE板在一定的载荷下进行两次以上拉伸以后力学性能才能达到稳定。所以以0.5 mm/min的速率将试件分别加载至3、6、9、12、15和18 KN,每个载荷重复3次。使用FLUKE实时记录传感器的电阻变化,分别拟合不同最大载荷下,传感器电阻的曲线,以评估传感器不用载荷作用下传感器响应特性。
2.4. 传感器机理与应变关系
树脂基体浸入碳纳米纸传感器固化成型后形成复合材料。采用Kaiser的异类丝状理论解释传感器的应变传感机理。碳纳米纸传感器的电阻分为两种,一是碳纳米管本征电阻R1,二是碳纳米管之间接触节点的接触电阻R2。试件受到外力作用时引起形变,导致传感器中碳纳米管之间的相对位置发生改变,其内部接触电阻R2发生明显变化,而本征电阻R1的变化忽略不计。碳纳米纸传感器中的碳纳米管通过两种方式接触,其接触电阻为
(1)
树脂与传感器薄膜固化成型以后复合材料的电阻R可以表示为:
(2)
其中,nEP为传感器中有效传导路径数目,nEN为每条有效传导路径有效碳纳米管连接,f为每条有传导路径中,类型II接触方式的有效碳纳米管连接含量。
碳纳米管接触节的接触电阻
(i = I, II)具体表达式可通过Simmons提出的电荷遂穿效应给出:
(3)
其中,ai为碳纳米管之间的接触面积,e为单元电荷量,h为普朗克常数,m为电子质量,
为潜在的屏障高度,
为碳纳米管薄膜的管间基体厚度。
有效的接触电阻
(i = I, II)与应变
关系式:
(4)
从理论模型中可知,试件在加载时,碳纳米纸传感器发行变形产生应变
,传感器的电阻随之增大,通过传感器电阻变化与应变的关系可实现对GLARE板受载情况进行监测。
3. 结果与讨论
在对GLARE板进行测试以前,先将传感器布置在铝合金表面和玻璃纤维板表面,分别进行拉伸测试,分别验证传感器可以完成对两种试件监测的可行性。对于第一组玻璃纤维板试件,将传感器植入玻璃纤维层表面,拉伸实验加载速率为0.5 mm/min,最大载荷为12 KN,实验结果如下图4(a)所示。第二组铝合金板试件,将传感器使用3M460树脂粘接在铝合金板表面,拉伸实验加载速率为0.5 mm/min,最大载荷为10 KN,实验结果如下图4(b)所示。图4中蓝色曲线表示设备采集的传感器电阻变化。红色曲线表示拉伸机引伸计所得到的位移–载荷变化。黄色曲线表示对传感器电阻变化的拟合曲线。传感器电阻变化的拟合曲线几乎和位移–载荷曲线完全重合。实验结果证明将传感器可以实现对复合材料的监测,可以准确的反映出玻璃纤维复合板的受载状况。
通过上面拉伸实验证明传感器可以实现对玻璃纤维板和铝合金板的受载状况监测。最后一组实验试件由铝合金板和玻璃纤维共固化形成的GLARE板结构。以最大载荷分别为3、6、9、12、15和18 KN进行三次拉伸实验。因为对于GLARE试件,当最大拉伸载荷为6 KN、15 KN或其他载荷时,在三次拉伸实验可以看到第一次拉伸的位移–载荷曲线和第二次、第三次拉伸的位移–载荷曲线明显不重合,如下图5所示。而第二次和第三次拉伸曲线几乎完全重合。第一次拉伸实验出现了明显的塑性变形,而第二次和第三次实验的位移–载荷曲线由两部分弹性变形组成。
(a)
(b)
Figure 4. Resistance response of sensor mount on (a) glass fiber laminate; (b) aluminum laminate
图4. 粘贴到(a)玻璃纤维;(b)铝合金表面的传感器电阻响应
(a)
(b)
Figure 5. Resistance response of sensor mount on (a) glass fiber laminate, (b) aluminum laminate
图5. 粘贴到(a)玻璃纤维(b)铝合金表面的传感器电阻响应
试件在第三次拉伸时力学性质稳定,下文取第三次拉伸实验的数据进行讨论。并规定编号x-y表示不同最大载荷x在第y此拉伸测试。例如3-3表示以最大载荷为3 KN的第3次拉伸试验。并且用1号以及2号传感器分别表示位贴在铝合金表面以及玻璃纤维表面的传感器。3号传感器和4号传感器表示贴在铝合金板和玻璃纤维板界面的传感器。由图4可知,传感器粘贴在不同材料表面虽然都有比较好的传感特性,但是传感器的初始电阻却不同。此时为了更直观的表示传感器的传感特性,用电阻变化率表示传感器响应特性。R0表示传感器初始电阻,R表示传感器受载时候的实时电阻,ΔR = R − R0传感器的电阻变化率。
图6为最大载荷分别为3、6、9、12、15和18 KN进行第三次拉伸实验时传感器的电阻响应。图中黑色曲线表示拉伸时GLARE板的位移–载荷曲线;红色曲线表示布置在玻璃纤维表面的1号传感器的
电阻响应。蓝色曲线表示布置在铝合金表面的2号传感器的电阻响应。粉色和绿色曲线布置在GLARE板界面的3号和4号传感器的电阻响应。在第三次拉伸实验时,贴在铝合金以及玻璃纤维表面的1号和2号传感器电阻均随着载荷的增加而逐渐增加。而界面的3号和4号传感器却没有出现随载荷的增加而出现类似于三角函数上下波动的趋势。并且3号和4号传感器在拉伸过程中出现了电阻变化率为负的情况。
从图中还可以看出布置在铝合金表面的2号传感器电阻变化率大于布置在玻璃纤维表面的1号传感器电阻变化率。布置界面的3号和4号传感器电阻变化率大小几乎相同,也有几乎相同的变化规律。当最大拉伸载荷不超过9 KN时,两个传感器电阻变化率有正负值。当最大拉伸载荷超过9 KN时,两个传感器电阻变化率只有正值。并且当最大拉伸载荷为18 KN时,布置在铝合金板表面的传感器发生了失效。
所有4条曲线都是波浪形变化。这是由于铝合金为弹塑性材料,玻璃纤维为弹性材料。并且玻璃铺层的方向全为90˚方向,而载荷作用方向为0˚方向。随着载荷的增加,玻璃纤维为组要受载结构,当载荷增加到一定程度时,可能由于玻璃纤维板的基体损伤,纤维板的应力释放,曲线下降,当载荷继续增加时,玻璃纤维结构继续承载,曲线上升。载荷持续增加,该过程重复出现。导致了所有传感器响应曲线都为波浪形变化。
最后将所有贴在铝合金表面、玻璃纤维表面、铝合金板和玻璃纤维板界面的传感器响应曲线分别在三幅图中表示,如图7所示。可以得出结论:当拉伸试验的最大载荷增加时,传感器电阻响应曲线的初始电阻同样在增加,传感器的灵敏度并未发生变化,从而可以通过传感器初始电阻判断其结构历史最大受载。实现对GLARE板的受载监测。
(a)
(b)
(c)
Figure 7. Resistance response of sensor embedded in GLARE with different maximum load
图7. 嵌入到GLARE板中的传感器在不同最大载荷下的电阻响应
4. 结论
本文对基于碳纳米纸传感器的GLARE板进行了研究,并将传感器分别布置于铝合金板、玻璃纤维板和GLARE板三组试件表面或界面中。通过对比三组试件在拉伸测试时的力学性能与传感器电阻响应规律,得到以下结论:
1) 先将传感器布置在铝合金表面和玻璃纤维板表面,将传感器植入玻璃纤维层表面,拉伸实验加载速率为0.5 mm/min,最大载荷为12 KN。将传感器使用3M460树脂粘接在铝合金板表面,拉伸实验加载速率为0.5 mm/min,最大载荷为10 KN。传感器电阻变化的拟合曲线几乎和位移–载荷曲线完全重合。实验结果证明传感器可以实现对复合材料的监测,可以准确地反映出玻璃纤维复合板的受载状况。
2) 对于GLARE试件进行拉伸实验,最大拉伸载荷设置为6 KN、15 KN或其他载荷。从三次拉伸实验的结果中可以看到,第一次拉伸的位移–载荷曲线和第二次、第三次拉伸的位移–载荷曲线明显不重合。而第二次和第三次拉伸曲线几乎完全重合。第一次拉伸实验出现了明显的塑性变形,而第二次和第三次实验的位移–载荷曲线由两部分弹性变形组成。
3) GLARE板第三次拉伸实验力学性能稳定时,贴在铝合金以及玻璃纤维表面的1号和2号传感器电阻均随着载荷的增加而逐渐增加。而界面的3、4号传感器却没有出现随载荷的增加而出现类似于三角函数上下波动的趋势。并且3、4号传感器在拉伸过程中出现电阻变化率为负的情况。
4) 布置在铝合金表面的2号传感器电阻变化率大于布置在玻璃纤维表面的1号传感器电阻变化率。布置界面的3、4号传感器电阻变化率大小几乎相同,也有几乎相同的变化规律。当最大拉伸载荷不超过9 KN时,两个传感器电阻变化率有正负值。当最大拉伸载荷超过9 KN时,两个传感器电阻变化率只有正值。
5) 当拉伸试验的最大载荷增加时,传感器电阻响应曲线的初始电阻同样在增加,传感器的灵敏度并未发生变化,从而可以通过传感器初始电阻判断其结构历史最大受载,实现对GLARE板的受载监测。